These problems developed during commissioning and during the author’s 17 years’ service in a South Indian Ammonia, Urea, and NPK complex fertilizers plant. The author and his team resolved these problems forever mostly online or involving shortest shutdowns.
That plant’s success ushered many still higher capacities plants in India wary of high-speed centrifugal compressors-based fertilizers technology.
He, a mechanical engineering graduate joined that plant after serving the Steel Authority of India (SAIL) for 13 years as Instrument Engineer.
During his first five yearlong South Indian Fertilizer Plant services, he successfully solved many instruments commissioning problems.
In addition, he offered solutions to many mechanical and electrical problems repeatedly discussed in the problems solving meetings.
During the next 4 years’ tenure as Instrument Electrical and Workshop Engineer, he continued solving more problems.
How he got into handling all given up crippling electrical problems appears in the Electrical Problems Introduction.
During the 8 years tenure as Maintenance Manager, he solved this booklet discussed mechanical problems. Just two months as General Manager, he joined a Saudi Arabian Fertilizer Plant.
During his 5 years Saudi tenure he solved few problems that enabled the debuting co to establish its image as a reputable NH3 supplier initially and as high-quality urea and complex fertilizer supplier after the plant added those facilities.
After the return from Saudi, he took 3½ years of training assignment with Reliance Petroleum Ltd Jamnagar, and several lecture assignments, a one-year assignment with Reliance Navi Mumbai, and a six-month assignment with Chambal Fertilizers Ltd.
Root Cause Analysis (RCA)
The author attributes his problems solving success to the following:
- Every one’s cooperation
- Root Cause Analysis supported by input from the problems-sufferers, instruction manual studies, comparing design and actual operating data, gathering knowhow from relevant literature, tech journals articles and advertisements especially on new products
- In short ‘avoiding the popular industry joke, “When all else fail read the instruction books”
- Consider input from anyone. – no matter his/her qualification and hierarchical rank – thankfully and credit his / her contribution
- The author learnt mere experience does not suffice, as mostly many have one-year experience repeated so many years by not solving problems by root cause analysis and living with it; it makes most persons complacent, leads to take the problems as a way of life and live with them, and prevents finding root cause analysis solutions. Experience combined with adequate job knowledge-based root cause analysis only can solve problems; not years and years of experience alone.
Good Luck to all plant problems solving troubleshooters. The free plant personnel from the drudgery of annoying repeat low-tech tasks, midnight, off days, and during vacation calls and the associated ill effects e.g. the inconvenience and family wrath from missed family times and functions.
Mechanical Engineering Plant Problems
This root cause analysis (RCA) is from real-time scenarios that happened in industries during the tenure of two or three decades ago. These articles will help you to improve your troubleshooting skills and knowledge.
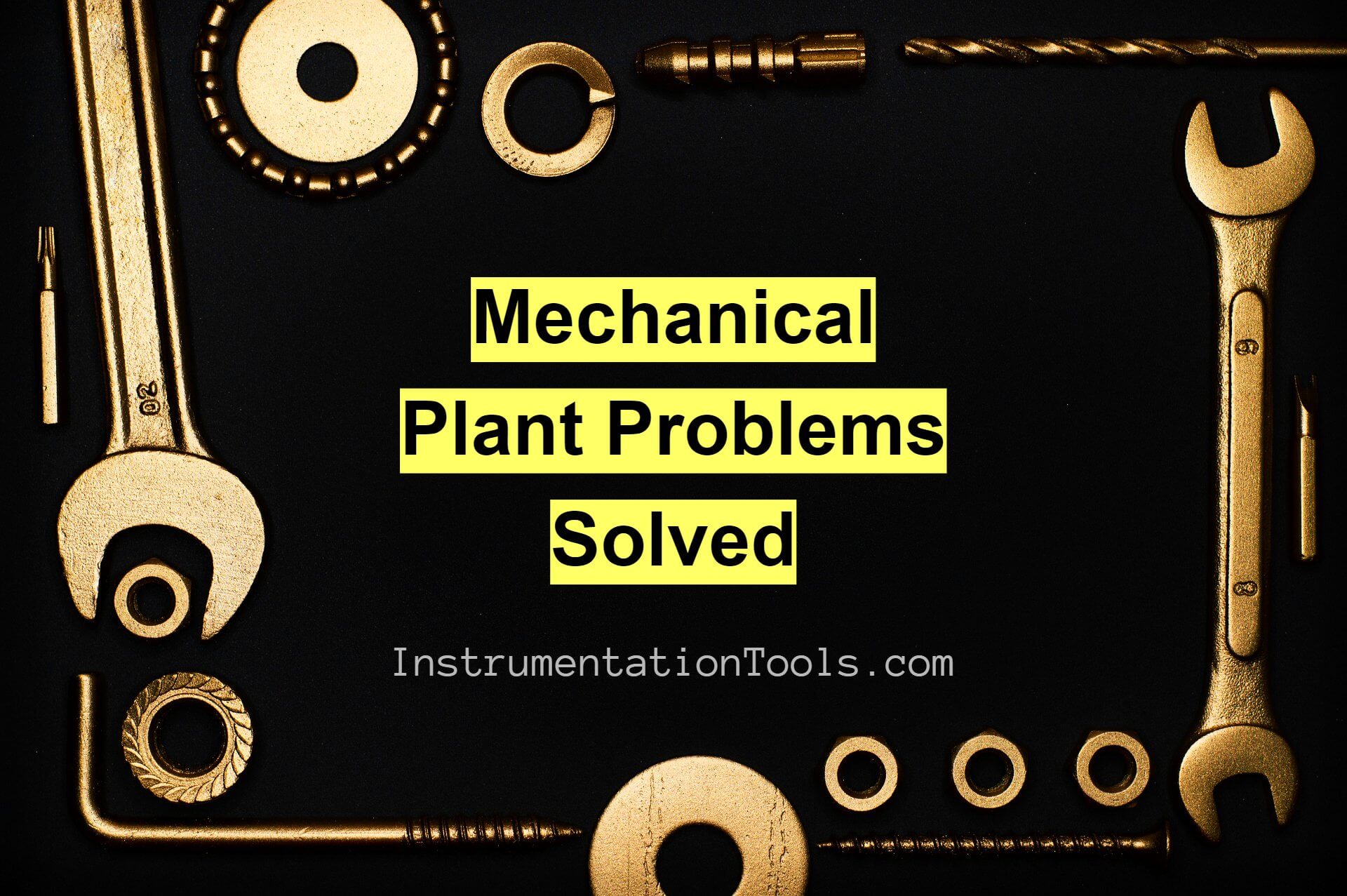
The below is the list of mechanical solved problems.
S.No. | Mechanical Problems and Solutions | Article |
---|---|---|
1 | Steam turbine HP case three monthly Discharge Head (DH) leaks 10-days plant outages cut to 1½ days using negligible resources than the past | Click Here |
2 | The above 3-year persisting K-601 Discharge Head 3-monthly leaks eliminated | Click Here |
3 | Steam turbine (K-601) IP case six monthly 2 days shutdowns eliminated | Click Here |
4 | Process Air Compressor (K-602) too frequent & too lengthy overhauls | Click Here |
5 | Refrigeration Compressor Not-tripping Trip Throttle threatened potential compressor wrecks eliminated | Click Here |
6 | Malfunctioning inlet check valves caused 5-yearlong chaos at each compressor stop/trip eliminated | Click Here |
7 | K-603 near ½-RPM frequency high magnitude shaft vibrations eliminated | Click Here |
8 | Steam turbine surge caused near-miss K-601 wreck eliminated | Click Here |
9 | 8,000-RPM, 7000 KW K-602 T injured rotor threatened yearlong total plant outage. Innovative in-house repairs put the plant on stream in 1½ days; recurrence eliminated | Click Here |
10 | 8000 – RPM K-602 cracked shaft spacers; the plant Root Cause Analyzed, made the spacers and heat-treated to lesser hardness and fitted on the spare and running rotor | Click Here |
11 | K‑601 T turning gear chamber excessive oil belch posed indefinite SD threat eliminated on stream and recurrence eliminated | Click Here |
12 | NH3 plant K-601 T Tilting Pad too high temperatures sudden entire plant indefinite shutdown threat eliminated | Click Here |
13 | An Indian Plants all turbines’ low Vacuum & Plant K-601 T only solved and recurrence eliminated | Click Here |
14 | often-found pitted shaft and coupling bore tapers repair caused excessive and length shutdowns | Click Here |
15 | Poorly engineered plant Air Compressor often failing drives made 100% reliable very economically | Click Here |
16 | Boosting <40% available Plant Air Compressors availabilities to 100% enables fulfilling “keep the plant young corporate goal”. | Click Here |
17 | NH3 Storage tanks financially crippling 12 T/d wasteful venting & pollution authorities plant closure threat eliminated | Click Here |
18 | Potassium Carbonate Pump 3-monthly Seal Leaks threaten entire plant shut down indefinitely | Click Here |
19 | Plant BFW Pump Low throughput DDUDP resolved | Click Here |
20 | CW circulating Pump Low throughput resolved & proposed Rs 20 million pump add averted | Click Here |
21 | Failed Phosphate Dozing restored | Click Here |
22 | Acid Dozing Pump weekly failures eliminated | Click Here |
23 | Eleven Cooling Tower Fan frequently failing drives made never failing | Click Here |
24 | CT fan FRP fan blades saves and saves | Click Here |
25 | Condensate Pump Frequent Wrecks eliminated | Click Here |
26 | Generally too poor AFB lives and production loss from impossible to remove AFBs and Coupling halves | Click Here |
27 | Root Cause Analysis eliminated too poor antifriction bearings lives boosts production | Click Here |
28 | Too frequent 1800 kW 8000-750 RPM Gearbox (GB) failures eliminated | Click Here |
29 | Turbine to gearbox too frequent alignment drifts eliminated | Click Here |
30 | Large motor’s too frequent Journal Bearing (JB) failures eliminated | Click Here |
31 | Fired Boiler ID fan too frequent AFB failures eliminated | Click Here |
32 | Fan Bearing Changes made easy at 10% former times | Click Here |
33 | Sudden fatal pipe burst root cause removed; wrecked panel instrumentation restored within a week and recurrence eliminated | Click Here |
34 | Sledge open/close valves replaced with one hand operable valves | Click Here |
35 | Flange Joint Errors shutdowns root cause analyzed and eliminated | Click Here |
36 | K-601 T 100-40 bar steam letdown station 3-year long flange leaks eliminated | Click Here |
37 | Seawater pipeline spools leaks threatened NH3 plant indefinite SD eliminated | Click Here |
38 | K-601 T 12” 2500 # Trip Throttle Valve stubborn cover opened | Click Here |
39 | Repeat Safety Valve Pops caused too many Urea Plant shutdowns eliminated | Click Here |
40 | Rupture Discs bursts caused too many Urea Plant shutdowns eliminated | Click Here |
41 | Urea Plant PTFE lined 6” 300# butt weld end Plug Valves leaks stopped forever | Click Here |
42 | Primary Reformer – Each Turnaround done massive and expensive Tubes Repairs eliminated | Click Here |
43 | Too often done riskily repaired roof Hot spots eliminated forever | Click Here |
44 | Primary Reformer RFG main hot spots eliminated online and indefinite outage eliminated | Click Here |
45 | 10-years persisting syn loop BFH shell flange leaks, and nuisance ammonia plant trips eliminated | Click Here |
46 | Despite senior colleagues’ diffidence & a seemingly no solution last-minute hitch, 220-bar syngas cooler successfully re-tubed | Click Here |
47 | Constraints ridden ‘impossible’ demister cleaning innovatively done and urea plant indefinite outage eliminated. | Click Here |
48 | Constraints ridden another ‘impossible’ heat exchanger leaks innovatively stopped and urea plant indefinite outage eliminated. | Click Here |
49 | Root cause analysis stops crews morale robbing many Bucket Elevators many wrecks | Click Here |
50 | Bucket elevators’ 5-year long too short chains lives eliminated | Click Here |
51 | Plant Bucket Elevators chains too short chain lives eliminated | Click Here |
52 | Too noisy & too maintenance-intensive granulator drive silenced and made maintenance-free | Click Here |
53 | Home-made Rotary Drier Shell to Split Gear drive eliminates too frequent drive failures | Click Here |
54 | Home developed motor vibrators lot better than provided vibrators boost safety and production | Click Here |
55 | Innovative in-house motor-operated valve repair enables guarantee test completion and final settlement. | Click Here |
56 | Root Cause Analysis enhances a new exchanger’s 50% heat transfer to 100% and enables a urea plant commissioning completion | Click Here |
57 | Ruined De-Min vessel internals innovative within few hours’ restorations eliminates an Ammonia plant indefinite shutdown | Click Here |
58 | A near impossible constraint overcoming enables repairing a 220-bar urea reactor top cover | Click Here |
59 | 10-yearlong every TA restored CO2 Stripper collapsed internals eliminated | Click Here |
60 | Every turnaround (TA) done CO2 Absorber corroded wall thickness weld building eliminated | Click Here |
Also Read:
Author: S. Raghava Chari
Do you face any similar issues? Share with us through the below comments section.
If you liked this article, then please subscribe to our YouTube Channel for Instrumentation, Electrical, PLC, and SCADA video tutorials.
You can also follow us on Facebook and Twitter to receive daily updates.
Thank you sir. I am not from mechanical background but some articles are good to read.