Root Cause Analysis (RCA) related to primary reformer RFG main hot spots threaten indefinite outage eliminated.
Article Type: | Root Cause Analysis (RCA) |
Category: | Mechanical |
Equipment Type: | Pipelines and Miscellaneous Problems |
Author: | S. Raghava Chari |
Note: This root cause analysis (RCA) is from real-time scenarios that happened in industries during the tenure of two or three decades ago. These articles will help you to improve your troubleshooting skills and knowledge.
Problem
Reformed Gas (RFG) collecting main hot spots: gas collecting main conveying the reformer produced 800o C and 35 bars pressure RFG to the secondary reformer developed hot spots threatening the indefinite shutdown.
Primary Reformer RFG main Hot Spots Problem
The below figure shows the gas collecting main details. RFG passes through loose couplers joined 6 m long x 150 mm dia x 3 mm wall thickness (WT) Incoloy pipes concentric to 300 mm dia x 25 mm WT welded all over CS pipes. Cast refractory fills the annular space.
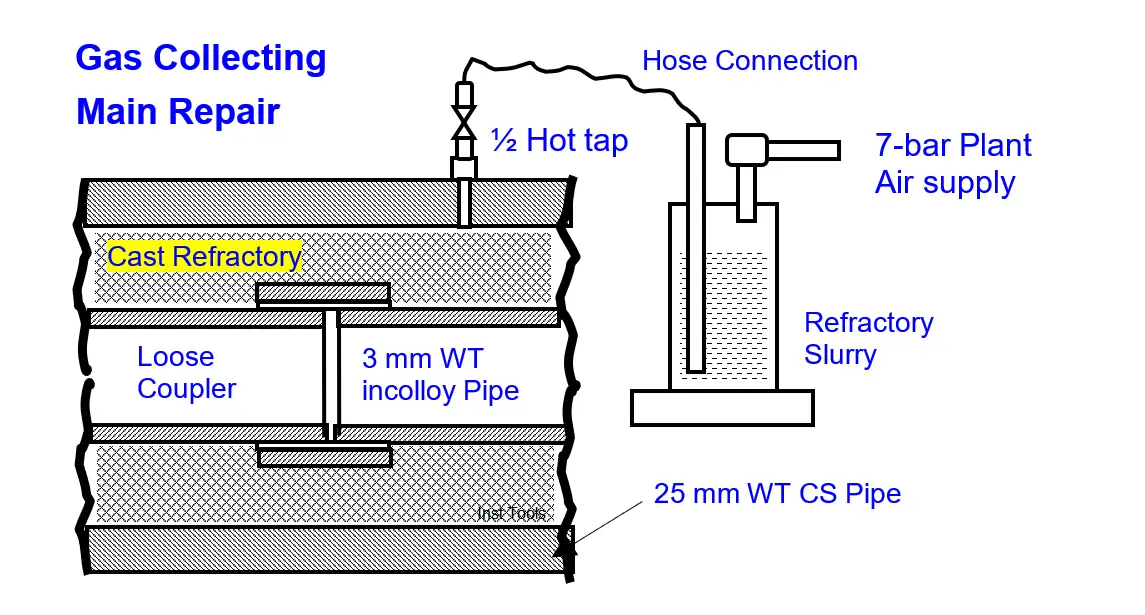
The hot gases’ small leaks percolating into the refractory eventually cool down as continuous large quantities of gas flow paths are absent. Thus, 800 deg C and H2 rich RFG wets the expensive suitable Incoloy and not the CS jacket, incompatible to the hot RFG.
In addition, the gas leaking out of the coupler joints pressures the annulus to near 35-bars; hence, the incolloy pipes handle zero differential pressure only.
Hence, the very small 3 mm thickness suffices. Such a design minimizes expensive incolloy use and reduces the system costs by 60 to 70%.
To summarize, inexpensive thick walled CS pipes handle the pressure at low temperatures, and expensive thin walled incolloy pipes the high temp and H2 attack; CS is incompatible to both.
Root Cause Analysis
Why hot spots? Probably excessive refractory cracks at different locations allow unacceptable quantities of 800o C RFG to circulate around.
Repair Options
The first suggested option was:
- Shut down the reformer and cool it down –– several days of dreaded task
- Flame cut the 30o hot spot CS pipe segment sufficient length.
- Steam pressure the reformer tubes to 1 bar
- Identify refractory leaks and repair The author thanked the proposer and invited all to come out with easier, safer, shorter SD and surer solution as soon as possible as living with the hot spots is unsafe.
Final Solution
After 3-thinking days, the author implemented below described steps to solve the problem:
- Crew welded 20 Nos. ¾” 6000 PSI sockets with welded gate valves distributed around the hot spot area
- During a 1 shift shut down, under 1-bar steam pressure, a crew at one end and another at the other end drilled 10 mm dia holes on the pipe. A stopper prevented drilling deep into the refractory
- injected a specialist company provided refractory slurry for 5 minutes, at each of the taps (fig 42), stopped and closed the valve
- After injection at all the taps they waited for 10 minutes and repeated the injection and hoped for the best
- The crew plugged all closed valves outlets.
Success
Operators started the reformer feeds and firing. No leaks at plugged valve ends and no hot spot delighted everyone.
Crew seal welded the plugs 4-hours later for extra caution against leaks. The great success attempt averted threatened indefinite total plant shutdown.
Author: S. Raghava Chari
Do you face any similar issues? Share with us through the below comments section.
If you liked this article, then please subscribe to our YouTube Channel for Instrumentation, Electrical, PLC, and SCADA video tutorials.
You can also follow us on Facebook and Twitter to receive daily updates.
Read Next:
- Plug Valves Leaks
- Rupture Discs bursts
- Trip Throttle Valve RCA
- Repeat Safety Valve Popping
- Steam Letdown Station Problems
.