Root Cause Analysis (RCA): Saudi Potassium Carbonate Pump 3-monthly Seal Leaks threaten the entire plant shut down indefinitely.
Article Type: | Root Cause Analysis (RCA) |
Category: | Mechanical |
Equipment Type: | Miscellaneous Rotating Machine Problems |
Author: | S. Raghava Chari |
Note: This root cause analysis (RCA) is from real-time scenarios that happened in industries during the tenure of two or three decades ago. These articles will help you to improve your troubleshooting skills and knowledge.
Pump Seal Leaks Problem
Too short thrust bearing and mechanical seal lives: A coupled through gearbox turbine-driven 1800 RPM (in 60 Hz power Saudi Arabia), 2000 KW Pump draws Potassium Carbonate solution from a 2 bars pressure source and delivers to the absorber at 35 bars.
The motor-driven standby rarely runs and the turbine pump (TP) always, because of the below-given reasons:
- Waste heat generated steam use economy
- Freedom from unreliable power supply pump stoppages and total plant shutdowns
The 1987 commissioned pump Suction and Discharge Mechanical Seals (MS) and thrust antifriction bearing (TB) failed three monthlies after 18 months exceedingly fine run.
The crew found the failed MS elastomers hard and brittle. However, the seal vendor pointed out the original seals over 18-months of trouble-free performance and assured that the original and replacement seals elastomers materials are the same and none better available.
The author had to solve the problem.
He gleaned the below information from the difficult to understand pump instruction manual drawing and sketched fig 3:
Impellors 1 to 4 suction eyes face left. Letdown to 3‑bars CO2 rich K2CO3 solution aka lean solution reaches the CO2 stripper which strips the CO2 out of the solution for urea production. Suction eyes left facing impellors 1 to 4 boost the pressure to around 18.5-bars.
Impellor 4 diffuser delivered flow reaches impellor 5 at the pump end and finally impellor 7 adjacent to impellor 4 diffuser delivers the K2CO3 solution at 35 bars to the CO2 absorber at 35 bars. Impellors 5 to 7 suction eyes face right. This balances significantly the rotor axial thrust towards suction common in centrifugal pumps
Keyed to the shaft right end Balance piston (BP) rotates at shaft RPM in its chamber. BP annular dia clearance is 0.8 mm.
BP right pressure = I5 suction pressure 18.5 bars. Leaks across the BP to BP chamber 0.8 mm clearance reaches the BP left side. A 2” pipe of 3 times the clearance area conveys the leaks to the pump suction the balance piston
Hence the across BP ΔP = (18.5-2) = 16.5 bars. Hence, the BP exerted force of ABP*16.5 towards left balances the residual axial thrust leaving a negligible load on the thrust Antifriction Bearing.
6-bars 60o C condensate flushing prevents 115o C K2CO3 wetting both right and left end MS and prolongs their lives.
3 mm radial thick stellite – cobalt-based hard-facing alloy – hard facing increases all casing Wear Rings (WR) bores and BP OD hardness to 450 BHN.
Thus, 250-BHN hard SS impellor eyes and BP chamber bore mate with the 450 BHN hard-faced parts, providing more than the required galling prevention 50 BHN mating parts hardness differences
Both Problems Root Cause Analysis
Using the above information, observed MS brittle elastomers and intact seal faces, the author Root Cause Analyzed (RCA) thus:
Why are elastomers brittle and hard? → (→ maybe due to) 115o C K2CO3 wetted MS. Why? →failed seal flush. Why? → BP right pressure close to 18.5 bars the BP left side pressure Why? → Excessive BP clearance. Why? → No answer now; await pump disassemble and parts inspection.
Too poor Thrust Bearing (TB) lives Root Cause Analysis
Why too poor TB lives? → excessive axial load. Why? → BP not canceling the rotor axial thrust. Why? →Excessive BP clearance as explained above.
Surmised Root Cause Corroboration
A few days later, “check the 2” seal condensate pipe skin temperature,” flashed to the author. Measured 105o C pointed out, “maybe 115o C K2CO3 flows in the pipe and not the 60o C flushing condensate.
This corroborated the surmised poor seal and TB lives root cause.
Root Cause confirmed
Next seal change shutdown, crew measured 6 mm higher than instruction manual clearance BP clearance surprised all and prompted checking clearances all over.
Similar 6-mm excess clearances at all locations and 250 BHN BP periphery and WR bores hardness pointed out K2CO3 corroding away the stellite – both problems RC.
Starting the dissembled turbine-driven pump ASAP was necessary as explained before. Hence, the crew put new seals, took the author ordered BP essential dimensions, changed thrust bearing, assembled back, and started the TP.
Clearances Restoration
Shaft vibrations not increasing despite so much clearance increases all over surprised the author. Remember the pumped liquid lubed WRs serve as supplementary bearings too.
Hence, excessive WR clearances usually result in increased rotor vibrations. Hence, using no-stellite SS 316 WRs, and BP was the only solution with 0.125 mm higher than original clearances – American Petroleum Institute (API) Recommendation – to prevent galling was the only solution.
Actions Taken
The vendor’s WRs and BP delivery period and costs were excessive. In addition, the entire scrapping of the 480 mm dia x 250 SS – 316 BP and putting a new one was a shear waste.
Hence, the author got SS to wear rings made from plasma cut blanks out of 35 mm thick SS–316 plates. How to restore BP clearance still eluded solution.
A few days later he thought of sleeving the BP using a proper bore and thickness SS-316 pipe. He found a ½ m long 20” Sch 160 pipe the suitable material for the sleeve.
Accordingly, the shop readied a 480 OD x 250 long x 10 wall thick sleeve out of a bought-out 300 mm long 20” Sch160 SS pipe scrap. Making WRs also out SS 316 pipe bits would have been easier and economical, but the idea did not occur in time!
Provided API 610 specified 0.125 mm extra all-over clearances made the mating parts galling free. The author provided rotameters to monitor seal flushing condensate flow to take timely corrections.
Below listed fits-information helped to make the WRs and BP Sleeve.
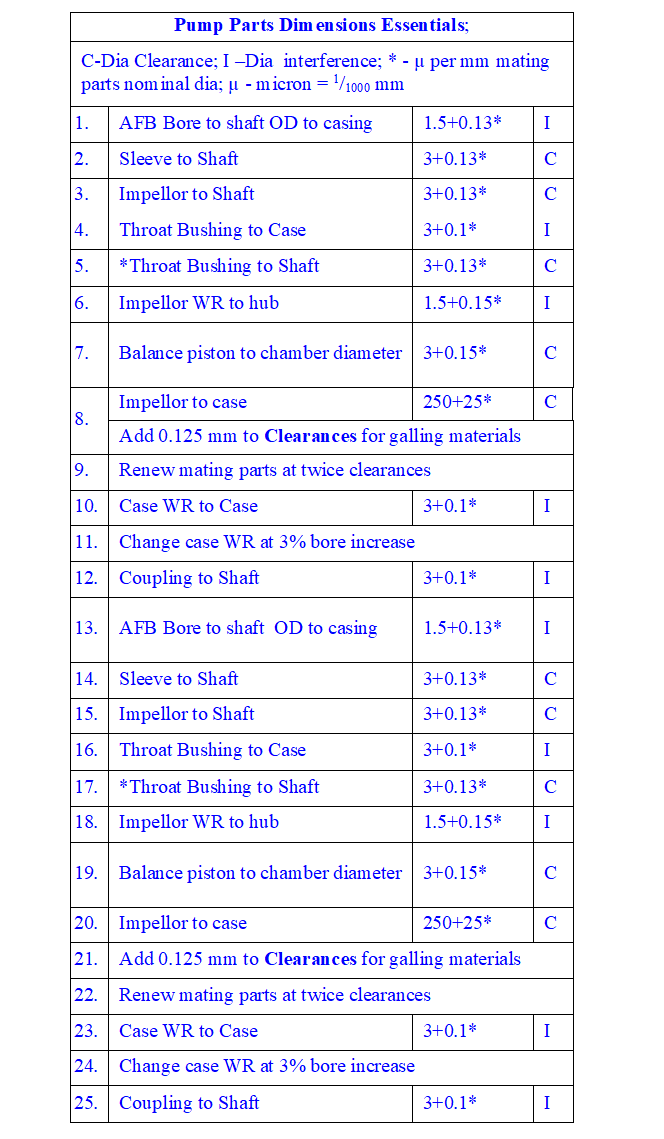
The pump problems vanished totally. Seal lives exceed 4 years and Thrust Bearing > L10 lives.
The flaw in the above RCA
The MS and Thrust Bearing short lives elimination won top management and many seminars participants’ appreciations as each seal cost nearly $9000 in 1988, and a long motor-driven pump run could shut down the entire plant.
The author reveling in the success did not look back at the RCA. However, he realized the below listed his RCA flaws now. None of the many seminar participants spotting them surprises him.
First RCA flaws
Below are the First RCA flaws:
- Fig 1 shown BP right side as new pump condition pressure would be almost 18.5 bars, as BP annulus area is 687-mm2 and TB1 annulus 82.5.
- Consequently,
- Both MS would not receive condensate flush. The hot 115o C wetted MS elastomers would harden in 3 months and seals would leak;
- In addition, the near zero across BP differential would not cancel the rotor thrust. Consequent excessively loaded thrust bearing would fail in 2 or 3 months.
- In short because of 2a and 2b the realized 18 months first good run would not have been possible
- Hence, the RCA though solved a very high cost and annoying problem is not all correct.
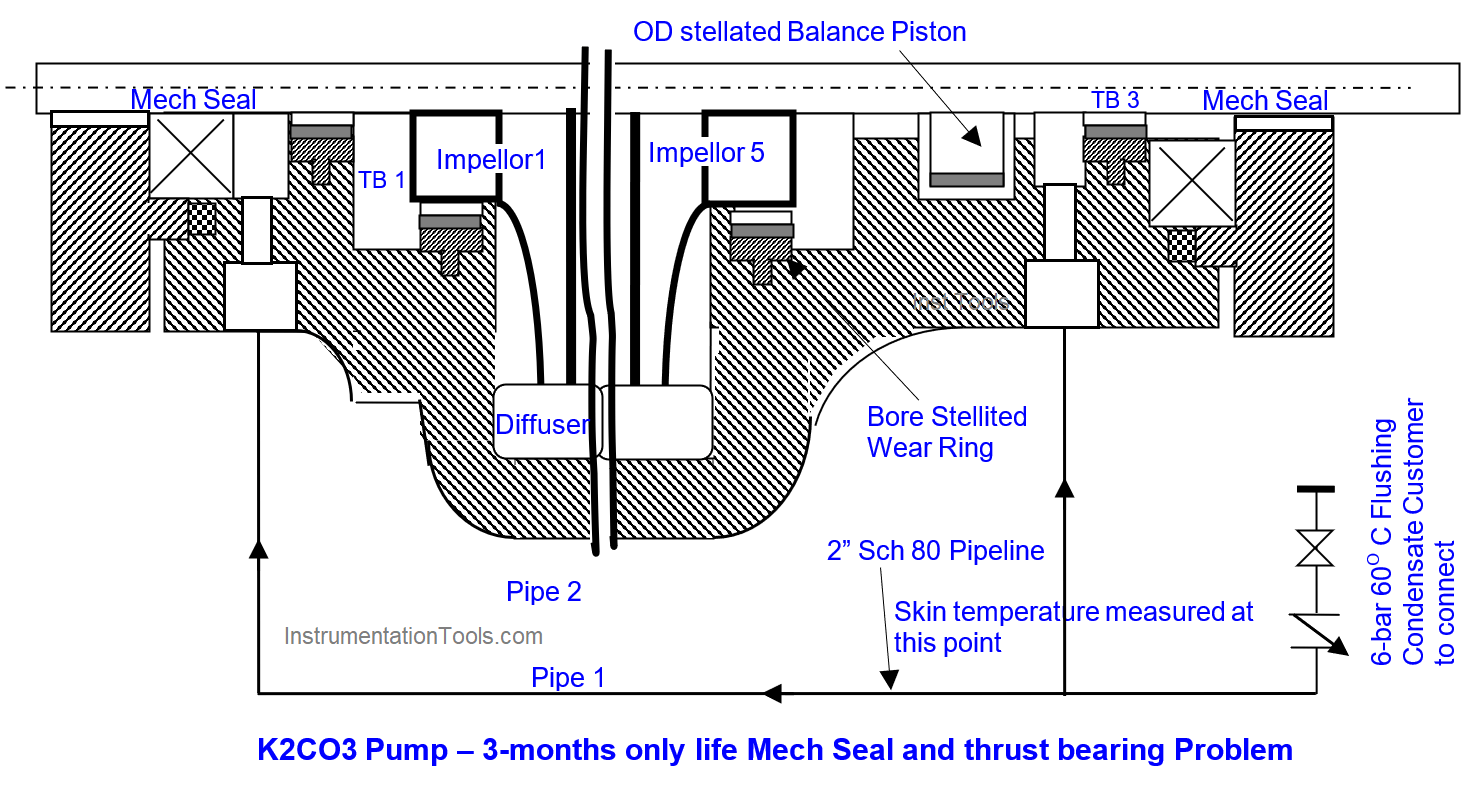
Revised Poor MS lives RCA
Hence, the author reviewed the first RCA (Click Here) and sketched the figure, which explains the solution flawlessly and satisfactorily.
Why are MS elastomers brittle and hard? → (maybe due to) 115O C K2CO3 wets the MS. Why? →failed seal flush.
Why? → At the measured > 6 mm BP clearance BP annulus area is around 4400 mm2, well above the 2” pipes 2200 mm2 → BP right pressure close to BP left 18.5 bars pressure → no right and left seals condensate flushes → within 3 months failed seals.
Poor Thrust Bearing lives RCA
What could reduce thrust bearing lives? Excessive axial load ↔ (↔ = What could cause it) ↔ BP not canceling the rotor axial thrust ↔ too low across BP ▲P ↔ too high BP clearance as explained above.
OK, explain fig 2 system adequacy in a new condition.
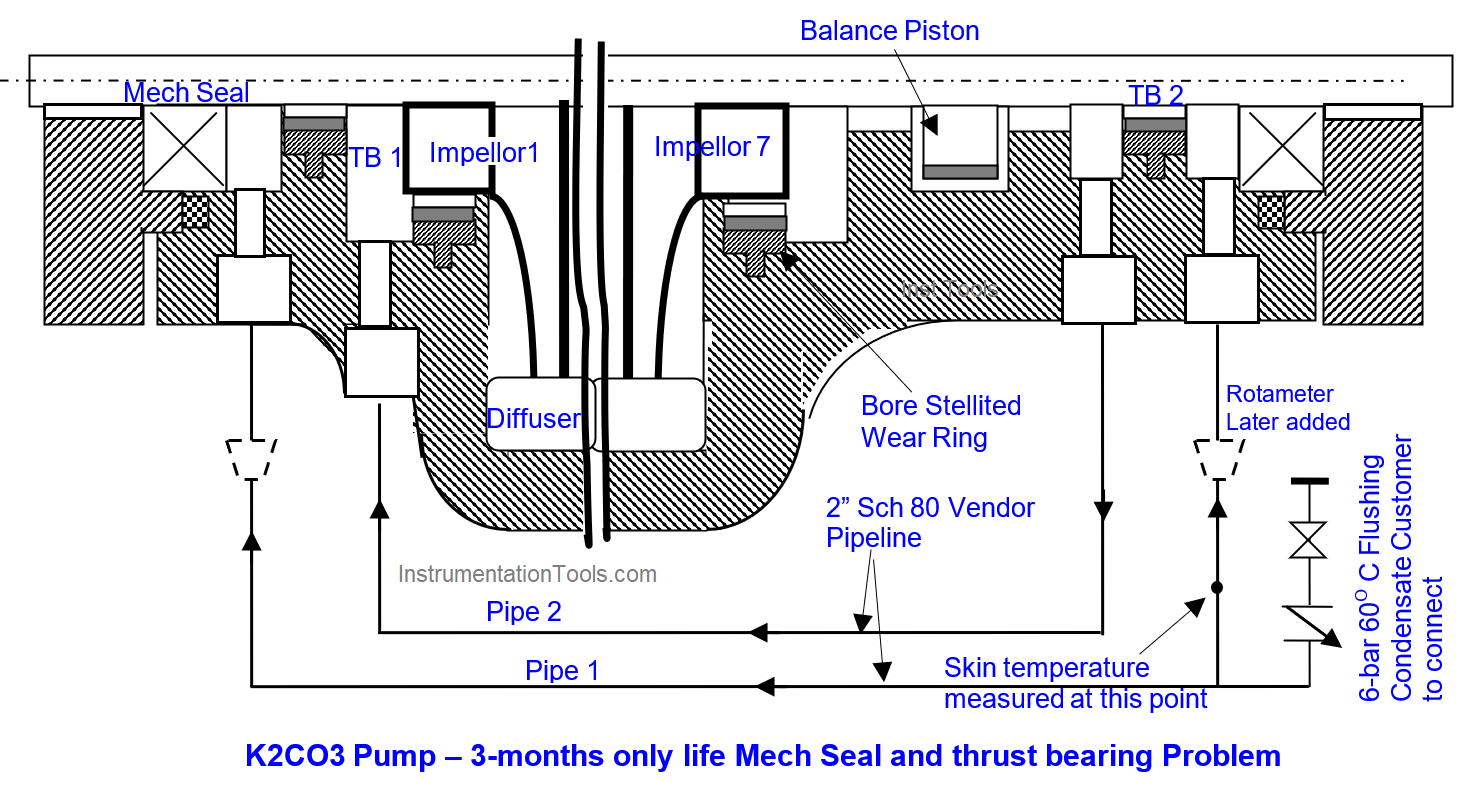
Below given is the explanation:
At as new pump conditions long MS & Thrust bearing lives
BP annulus area is 697 mm2 only and pipe 2 2200 mm2. Hence, one can easily understand from the following:
- BP right pressure is ≈ 2 bars
- As a result, condensate flushes both seals
- Hence, seals last 4 or even more years
- High BP ▲P effectively cancels rotor axial thrust. Hence, indefinite Thrust Bearing lives
Now and then, Pump Speed raise need a complaint
Responding to the author’s query, the operation engineer responded grinning sheepishly, “Sir, we did notice throughput loss now and then during the 1st 18-months run.
We just made up by increasing the turbine speed 20 RPM each time and finally settled at 1625 RPM from the initial 1550 RPM at the end of 18 months.”
The author pointed out that was his serious lapse; had they reported it sooner, the sooner would have been WR bore corrosion identification and sooner the plant saving drive turbine steam consumption.
Author: S. Raghava Chari
Do you face any similar issues? Share with us through the below comments section.
If you liked this article, then please subscribe to our YouTube Channel for Instrumentation, Electrical, PLC, and SCADA video tutorials.
You can also follow us on Facebook and Twitter to receive daily updates.
Read Next:
- Turbo-Compressor Problem
- Compressor Anti-Surge Control
- Process Air Compressor Overhauls
- NH3 Plant Turbo-compressor Problem
- Failing Plant Air Compressor Drives