Root Cause Analysis (RCA): K-602 Process Air Compressor too frequent & too lengthy overhauls Eliminated.
Article Type: | Root Cause Analysis (RCA) |
Category: | Mechanical |
Equipment Type: | High Speed, Hi KW Major Rotating Machines |
Author: | S. Raghava Chari |
Note: This root cause analysis (RCA) is from real-time scenarios that happened in industries during the tenure of one or two decades ago. These articles will help you to improve your troubleshooting skills and knowledge.
Process Air Compressor
The K-602 is a 2 case horizontally split 8000 RPM steam turbine driven centrifugal compressor (here air compressor tag is K-602). LP case contains built-in Iso Coolers to cool each wheel-delivered air to maximize compression efficiency.
It delivers the air at 8‑bars 45o C. HP case delivers the air at 150o C 36 bars to the process.
Problem
Too high first and second-case delivery temperatures, throughput loss, and excessive turbine steam consumption necessitated 6-monthly overhauls.
This was a major cause for the 750 T/d ammonia plant averaging 650 T/d.
The overhauling crew found:
- Both cases all labys severely eroded – the low throughput, turbine excessive steam consumption and high discharge temperature root cause
- Labys do not just fit with proper clearances as in other compressors; laborious trial and error 6-8 days bores hand-scrapping to realize proper clearances delays the plant start up
- The plant lived with the problem for several years.
Author Root Cause Analysis
Below given is the author who had become the Maintenance Manager
Root Cause Analysis:
Here Q is the RCA query and A is the RCA answer.
Q: Did you compare K-602 laby hardness with other compressors?
A: The rotating m/c engineer (RME) sheepishly said, “This did not strike all these years; I will get back to you after tests”.
Q: Now, the next problem! Why too long overhaul times?
A: RME,” Iso-Coolers removal for laby changes, fixing back and after start seen few gaskets leaks fixing take time
Q: Did you try Iso Coolers in-situ?
A: “No Sir, at the first overhaul, the US lead person removed them, and we follow it then on
Q: OK; let us get back to the question, why too long laby fit up times?
A: RME, “new laby bores foul with rotor shaft; hence trial and error bores hand scrapping and blue testing are necessary.” The many rotor lifts and placing on the bearings halves scares me! An accidental fall could damage the rotor and new expensive rotor purchase may be necessary! We, living with these 9 yearlong problems take it a way of life!
Poor laby lives problems solved
The RME reported that K-602 Labyrinths’ hardness was 30‑35 BHN only, but others’ »80‑BHN.
The manufacturer accepting his warehouse mix up caused error supplied two Avional (80 BHN hardness aluminum alloy) Labyrinth sets free of charge.
The avional Labyrinths in K-602 service lasted > 4-years like other compressors.
Iso-coolers caused delays eliminated: The author told the RME to call him day or night before Iso-cooler unbolting.
During the overhaul, he removed a laby and fitted it back iso-cooler in-situ! The crew grudgingly admitted the past vain removals and changed the labys 3-days sooner. No after start gasket leak fixing, 1-day saving is a bonus i.e. total 4-days.
Laby scrapping during TA
The author urged all to think intensively to find out the reason the laby’s not fitting with proper clearances as in other compressors including this company made HP case and way to ready the labys before the TA to fit with proper clearances.
His several thinking days found no answers to these problems. It occurred to him too late while writing this article.
Below given is his root cause analysis and solution.
Q: Why the Labyrinth bores foul with the shaft?
A: (after long thought), maybe Labyrinth bores CL is offset to shaft CL
Q: Why offset in K-602 LP case only and not in other machines including this machine’s HP case? How to pre-machine the Labyrinths before shutdown (SD) to design clearances with offsets
A: The flashed answer, “the built in iso coolers increase K 602 LP case halves’ lengths, widths and heights 2 to 2½ times of external intercoolers machines. Perhaps machining errors creep in while machining such large casing halves. Below given method would enable pre-machining the labys to fit with correct clearances as in other machines and save 6 TA days overhaul time.
Labyrinth Pre-machining Method
- Band eroded laby-1 top and bottom halves; machine the assembly bore dia smooth till grooves disappear and 3 mm larger than shaft sleeve dia
- Likewise machine an entire laby set; the author calls these smooth bore labys as laby gauges!
- Label with a center punch the upper Laby Gauge halves UGT1, UGT2 …. And lower halves Laby Gauge Bottom LGB1, LGB2 etc. (fig‑2)
- Fit up all the machined LGBs and LGTs on the casing halves at their proper locations.
- Cello-tape 25x10x10 mm ‘tin piece top’ (TPT 1) to UGT 1 and ‘tin piece bottom’ (TPB 1) to LGB 1 (fig 2).
- Similarly fit all UGs and LGs tin pieces tapped
- Place the rotor on oiled bearing bottom halves.
- Bolt the casing halves together with 25% bolts evenly distributed
- Unbolt and lift casing top half and lift the rotor.
- Measure and record TP thicknesses (Table 1)
- Save the table as a permanent record. Slide out and save LGBs and LBTs in the compressor toolbox for future use
- SS band a new Labyrinth set halves and bore machine for the recorded offsets taking care of the signs and clearances.
- These labys would have correct clearances at the machine with no custom scrapping, saving around 6‑6½ TA days
- Complete the compressor assy and handover for production
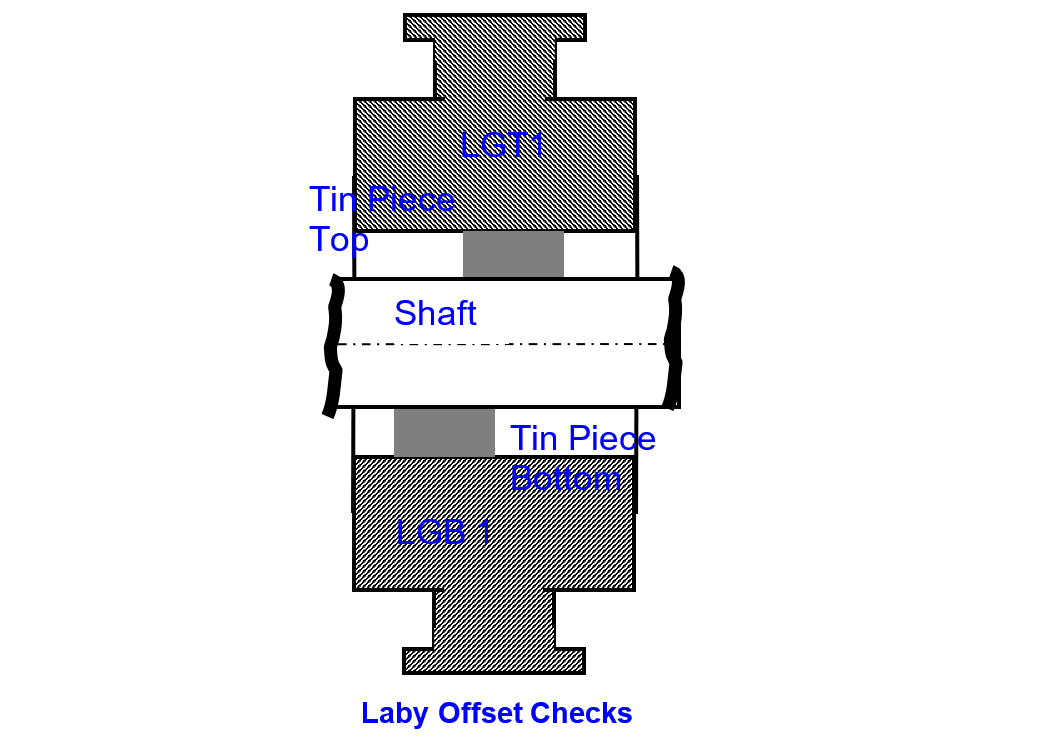
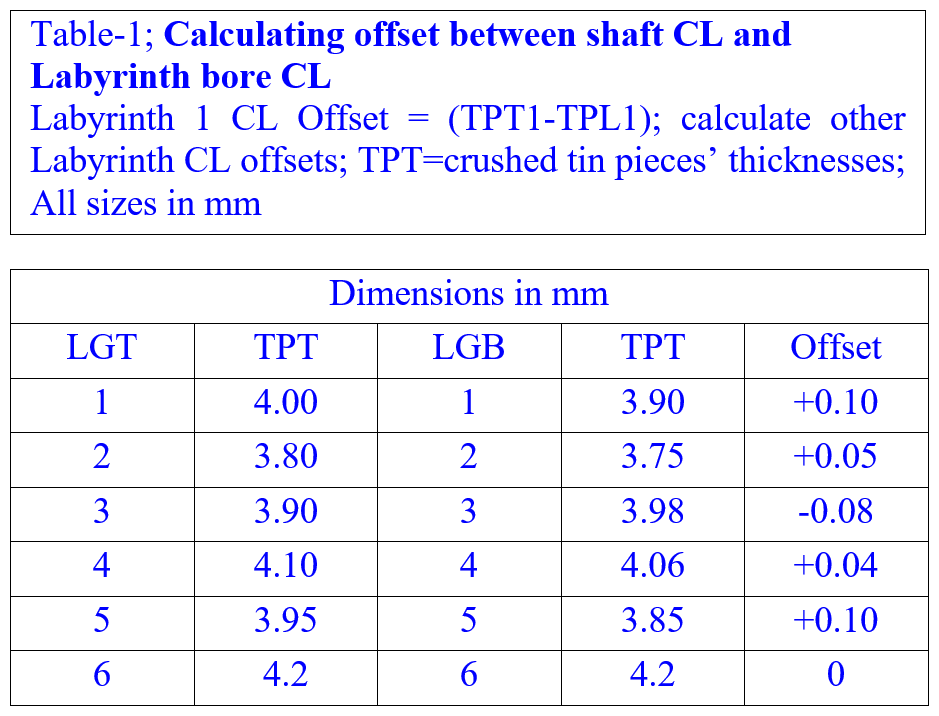
The author now not employed is unable to try out this. He requests Iso-cooler machine users to try this out and point out problems if any. On invitation, he will gladly help.
RCA solution benefits
- Avional labys last 4-or more years as other compressors labys i.e. 10% on stream days increase
- Iso-coolers in-situ laby changes saves K‑602 overhaul 4‑days
- The author is certain that
- His suggested Laby set pre-TA machining would cut down K‑602 overhaul times by further 6-days at each overhauls.
- It would avoid the too many rotor lifts and placements for laby scrapping and the associated fall damage risks
- He requests Iso-cooler machine users to try and feedback. He will gladly help
Author: S. Raghava Chari
Do you face any similar issues? Share with us through the below comments section.
If you liked this article, then please subscribe to our YouTube Channel for Instrumentation, Electrical, PLC, and SCADA video tutorials.
You can also follow us on Facebook and Twitter to receive daily updates.
Read Next: