Electrical engineering root cause analysis (RCA) related to miscellaneous electrical tasks in industries.
Article Type: | Root Cause Analysis (RCA) |
Category: | Electrical |
Equipment Type: | Miscellaneous |
Author: | S. Raghava Chari |
Note: This root cause analysis (RCA) is from real-time scenarios that happened in industries during the tenure of two or three decades ago. These articles will help you to improve your troubleshooting skills and knowledge.
Repaired Reformer Tubes Weld Stress Relief
The electrical crew handles Central Air Conditioning and window Air Conditioners Maintenance, and welded joints and thinned vessels weld builds Stress Relieving. Stress relieving tasks pose serious challenges.
The plant had to weld repair the entire 240 Nos. 13 long 150 mm dia primary reformer catalysts tubes every Turnaround (See Mechanical Problem).
Each weld joint needs pre and post-weld stress-relieving – a challenging task to complete within the available one week to avoid turnaround (TA) lengthening. The author thought out a reusable furnace (below figure) speeded up the task so fast that the electrical crew had to wait for to-weld and welded tubes’ arrival.
Initially, the electricians wrapped beaded heating elements over each tube weld, tack welded beaded Chromel–Alumel thermocouples (TC), and thermally insulated all over – a time consuming and tedious task indeed.
Post stress relief heating elements dissemble too was labor and time-intensive. Both lengthened the turnaround (TA). Most of the used material becoming non-reusable added to the woes and costs.
Stress Relieving Simplified
The author-guided crew built a novel, re-usable & easy-mount split portable furnace (SPF; below-figure) solved all the problems.
SPS each half consists of 400 mm long 10” Sch 10 pipe half (273 mm OD x 4.2 mm WT) bore lined with formed non-ceramic fiberboard.
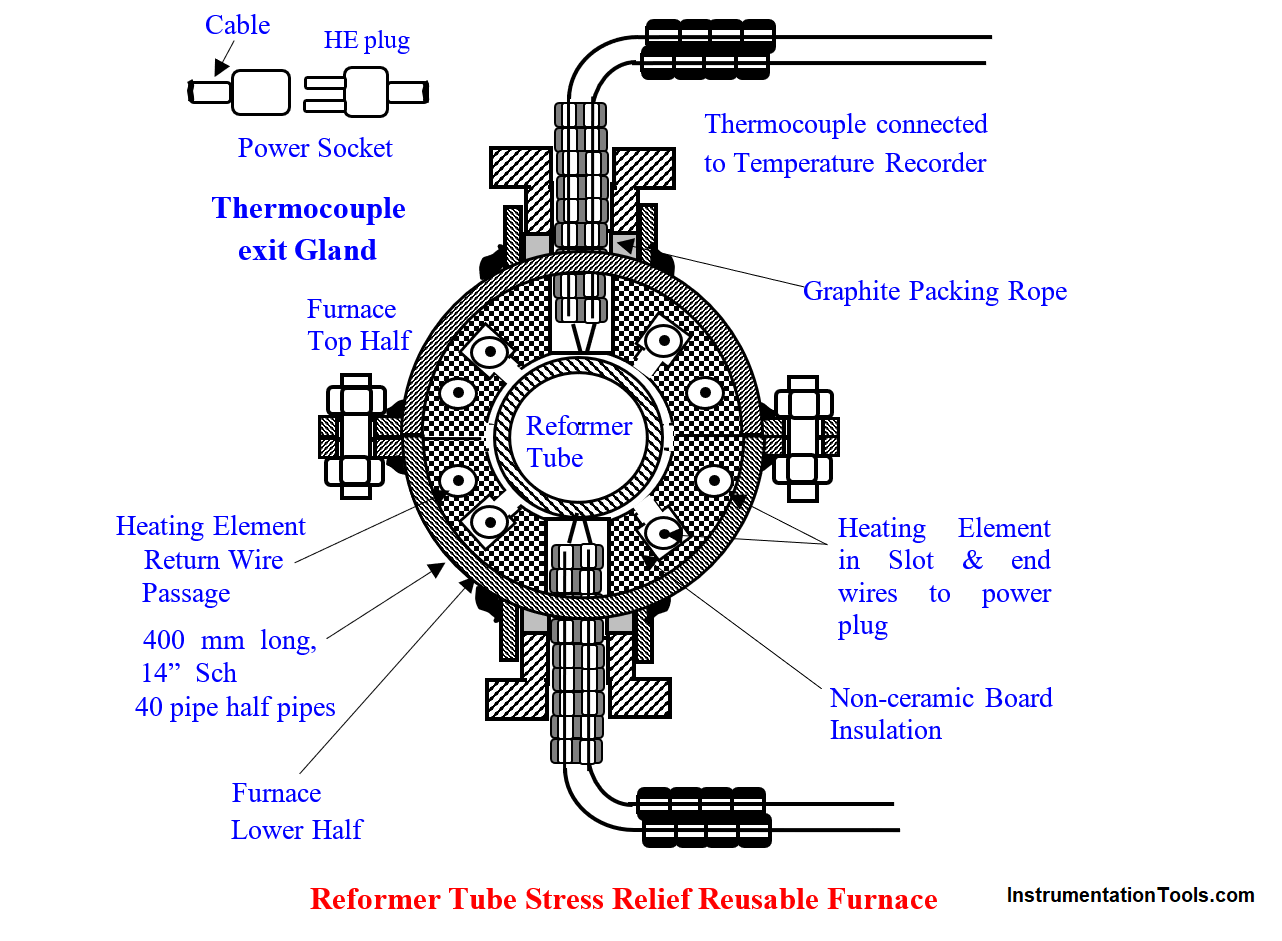
Two slots cut in each fiberboard half house a heating element each and a 6 mm dia hole – both along the length – the heating element end lengthy wire.
Electricians wire the heating system and terminate into a plug for inserting into the power socket fed by a contactor-controlled welding machine power source.
The crew just bolts the furnace halves over the weld, plugs heating elements into the power socket. Slot openings along the length (fig) maximize heat input to the welds and minimize radiation to atmosphere heat losses, A TC at each half connects to a nearby table carried temperature recorder (TR).
TR built-in switch cuts off the heating power at a set temperature and cuts in 20o below set temperature. After the specified hot soak, the crew shuts off the power and slow cools the heated area with the furnace still in position, but electricity switched off.
The furnace insulation slow cools the welds. Thus, the semi-automated system stress relieves the welds rapidly and accurately. Hence, the stress-relieving became a non-critical path TA task.
SPF Benefits
SPF Benefits are:
- Forty % shortened stress relief time because the crew just bolts the furnace halves to the RT, plugs the heating element into the power supply socket and the plugs thermocouple to the recorder socket instead of waiting for an electrician building the furnace over the tubes each time and connecting to the power supply and the TC to the recorder
- Simplifies the task considerably, saves costs, efforts and materials as a previous paragraph discusses.
Other miscellaneous electrical tasks: Providing a sufficient number of welding machines to weld build up the thinned wall of a 10‑m dia x 25-m tall high-pressure vessel from 32 to 50-mm, and after stress relieving build-up were other major challenging tasks successfully completed by the electrical crew in past turnarounds.
Author: S. Raghava Chari
Do you face any similar issues? Share with us through the below comments section.
If you liked this article, then please subscribe to our YouTube Channel for Instrumentation, Electrical, PLC, and SCADA video tutorials.
You can also follow us on Facebook and Twitter to receive daily updates.
Read Next:
- Welding Machine Problems
- HT Motor Direction of Rotation
- Inability to Test Repaired HT Motors
- Street Light Poles Corrosion Problems
- Cement Plant Rotary Kiln Electrical Drive