The junction box is one of the safest elements of the automation system which we think will not face any issues. The components like terminal blocks, cards, etc. installed in the junction box will not face any problems because of the surrounding atmospheric conditions. But for this, there are certain things that need to be done in the junction box.
Today in this article we will discuss one incident in which the cables inside a junction box were found damaged.
Junction Box Internal Corrosion Problems
Let us see the incident in detail.
Fuse blowing in the solenoid valve’s power supply loop is a common problem. This occurs due to several reasons like aging of the fuse or blowing of the fuse due to heating. But in the case which we are going to discuss, some on-off valve’s fuse used to get a blow. The frequency of this kept increasing.
After a few days, the instrument team noticed that only 14 valve fuses were blowing frequently. All other valves fuse are okay. So, the instrument team decided to check this incident in detail. On checking they found that all these valve’s solenoid supply was going through a single junction box.
On opening the junction box, the instrument team found moisture as well as minor corrosion on the internal surface of the junction box. Also, one major observation was that several cables’ insulation was in damaged condition. Because of the damaged cable’s insulation, the current was getting short circuit path and the fuses were blowing frequently.
Immediate action was taken by the instrument team and all the fuse TB in the marshaling cabinet for these solenoids were opened. Then the cable whose insulation were damaged were cut in the junction box, and the cables were pulled inside the junction box after cutting the damaged cable.
Learnings About this Incident
After investigation, it was observed that many things went wrong and this led to this incident. Let us have a look at these learnings which will be very useful for us as an instrument as well as an electrical engineer.
- On the very first observation, it was seen that the monsoon protection done was good. The silastic sealant was used on the surfaces of the junction box.
- The cable entry in the junction box was from the downside. When the bottom of the junction box was seen, it was observed that one hole for cable entry was not properly closed. Aluminum tape was used to cover that hole for cable entry. The aluminum tape was also in damaged condition. So, there is a high possibility that the moisture might have entered the junction box from this location.
- Also, the junction box was located near the area where acid dosing was taking place. Because of this, fumes of acid might have entered the junction box and damaged the cable’s insulation.
Junction Box Solutions
Learning points from this incident.
Always use the proper amount of Silastic to protect the junction box from moisture and rain.
Cover all the cable entry holes with bling plugs and apply proper silastic on them to eliminate the chances of moisture entering the junction box.
In junction boxes where cards or electronics are installed, use a vortex cooler to give proper cooling to the components as well as maintain a positive pressure inside the junction box to eliminate the possibility of moisture accumulation. Also, always give instrument air as inlet air to the vortex cooler.
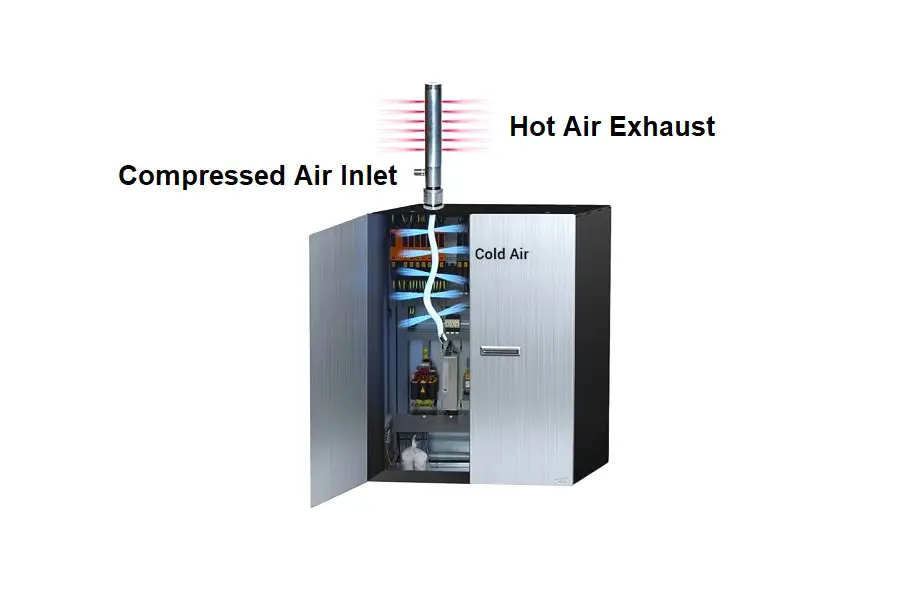
Try installing the junction boxes away from wet areas having high moisture content, areas where acid fumes are present, areas where temperature can increase due to sunlight, and other such areas where the atmospheric conditions can damage the junction box or its internal components.
Try not to open the junction boxes in the rainy season when the humidity in the air is high. If any such condition arises when there is a need to open the junction box in the rainy season, then ensure to blow instrument air or hot air using a blower inside the junction box so that the moisture evaporates and there is no chance of damage inside the junction box.
Always place Zerust capsule (as per my experience) or silica gel packets inside the junction box.
The last one but the most important one, cover all the junction box in the PM list (maintenance) or in LLF in which internal inspection as well as cleaning of the junction box is done on a regular basis.
If you liked this article, then please subscribe to our YouTube Channel for Instrumentation, Electrical, PLC, and SCADA video tutorials.
You can also follow us on Facebook and Twitter to receive daily updates.
Read Next:
- Process Air Compressor Overhauls
- Root Cause Analysis for Plant Trip
- Malfunctioning Inlet Check Valves
- Refrigeration Compressor Turbine
- BP Refinery Explosion at Texas City