Root Cause Analysis (RCA): A pipe elbow sudden pipe burst fatalities and wrecked panel instrumentation.
Article Type: | Root Cause Analysis (RCA) |
Category: | Mechanical |
Equipment Type: | Pipelines and Miscellaneous Problems |
Author: | S. Raghava Chari |
Note: This root cause analysis (RCA) is from real-time scenarios that happened in industries during the tenure of two or three decades ago. These articles will help you to improve your troubleshooting skills and knowledge.
Pipe Elbow Sudden Burst Problem
The author’s (instrument engineer then returned home from two days outstation trip. His son informed about the previous night’s frantic plant phone call: “an accident has happened; report soonest.”
Reporting within an hour by 10 AM, he learned the following sad news:
- The CO2 absorber to CO2 stripper letdown PCV downstream elbow burst spill flashed vapors shattered the control room front glass panes, and killed 8-ammonia plant operators
- It wrecked the control room panel instruments
- The boss took him out and told, “For morale build up and minimizing, the accident effects on people, starting back the plant soonest by hook or crook is vital; therefore, instruments restoring is the crying need; do all what you can do. All will work with you to the best of our abilities.”
System description, accident root cause, and recurrence prevention remedial steps follow and the instrument restoration details under instrumentation problems.
Complete Article: Wrecked Control Panel Problem
Burst Elbow Root Cause
The Night Superintendent (NS) responding to the emergency siren rushed to the ammonia plant. Noticed the spill from the burst.
He, using the two shift electricians, shift mechanics and 2 lab technicians wearing gas masks got the persons moved to a safe place. Called the local fire brigade and an ambulance from the general hospital.
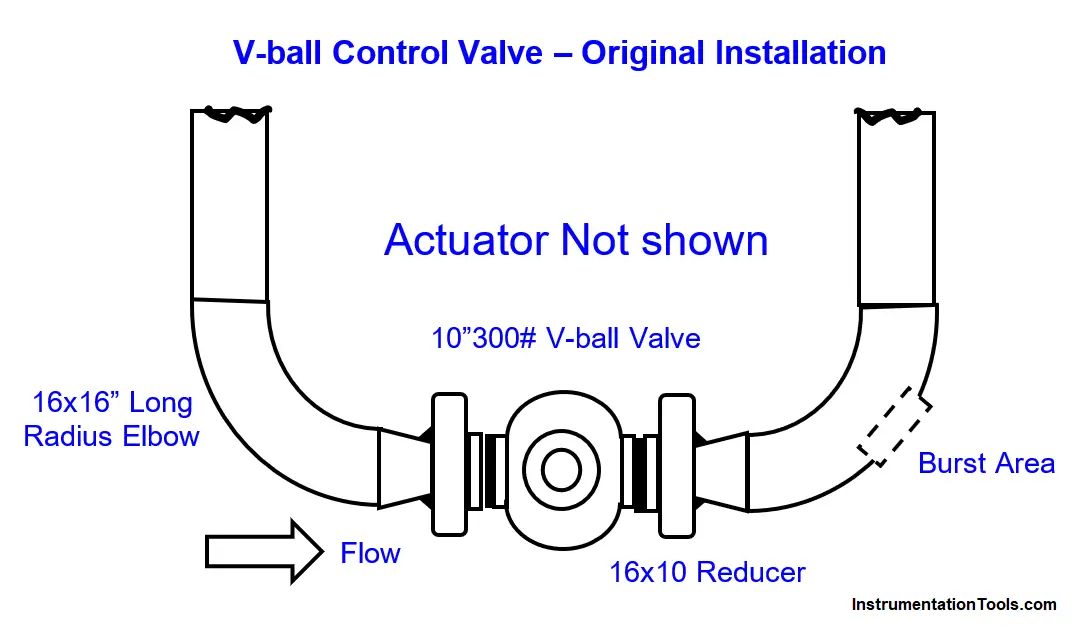
Then he, he shut down and secured the plant using the same persons. Since, the control room instruments have become inoperable, and his helpers ignorant of various valves locations, he took them there and showed how to take CV on hand jack and mode and got the valves closed / opened as needed and secured the plant.
Using them, he performed other tasks and restored some order and the others who reached on his call took over.
Thanks to these heroic efforts, the author and his team entered the cleaned-up control room and started instruments restoration discussed details under instrumentation problems.
More details
After restoring order, an inspecting engineer inspected and found a gaping 200×150 elliptical burst opening in the 10” V-ball valve (above figure) immediately downstream 16” elbow outer wall.
Suddenly jetting 35-bars, 120 deg C, high velocity, and enormous volume liquid spill flashing into vapors shattered the control room front glass panels, filled the control room, and caused the above-described sad events. The inspection engineer’s failure analysis report follows:
Failure Analysis Report
The turbulent high-velocity liquid exiting the 10”x300# rated V-ball type control valve (CV) constantly hit the elbow outer wall and caused the accident thus:
- Eroded the elbow outer wall and thinned it
- Prevented the added corrosion inhibitor forming the passivating film; consequent combined corrosion and erosion thinned the metal faster
- Unfortunately, none foresaw the above
- Eventually the wall’s thinned portion gave way; gushing liquids and flashed vapors through the large opening caused the sad accident
Accident Prevention Recommendations
The below given are the Accident Prevention Recommendations:
- Never bolt CVs between elbows even long radius
- Provide min 3-D (D-pipe dia) CV upstream straight pipe run (SPR) and 5-D downstream
- Check all CV locations and correct to comply with the recommendations
- Thickness check few high letdown pressure CVs upstream and downstream 10-D lengths to verify the recommended corrective measures adequacy
The plant re-located all control valves (above figure) in the vertical (Right leg in this case) leg with necessary upstream and downstream straight lengths and followed the other recommendations too.
The crew provided the working platform and cat ladder approach for operator access for easy hand-jack operation. Subsequent inspections confirmed the recommended corrective steps adequacy.
Pipe or pipefittings never burst thereafter.
Author: S. Raghava Chari
Do you face any similar issues? Share with us through the below comments section.
If you liked this article, then please subscribe to our YouTube Channel for Instrumentation, Electrical, PLC, and SCADA video tutorials.
You can also follow us on Facebook and Twitter to receive daily updates.
Read Next:
- Dozing System Problems
- Pump Low throughput Eliminated
- Fan Motor Journal Bearing Failures
- Turbine to Gearbox Alignment Drifts
- Storage Tanks Ammonia Gas Venting Issue