Root Cause Analysis (RCA) provides a solution to Reformer Fan Bearing Change Times cut by 90%.
Article Type: | Root Cause Analysis (RCA) |
Category: | Mechanical |
Equipment Type: | Miscellaneous Rotating Machine Problems |
Author: | S. Raghava Chari |
Note: This root cause analysis (RCA) is from real-time scenarios that happened in industries during the tenure of two or three decades ago. These articles will help you to improve your troubleshooting skills and knowledge.
Fan Bearing Change Times cut by 90%
Unbolt the over 250 Nos. 10 mm dia casing bolts
Position a crane suitably before plant shutdown (SD), after SD lift the casing upper half (above figure), place it nearby; lift the rotor 20 mm using a chain pulley block suspended from crane hook for Antifriction bearings (AFB) pull out; change the failed AFB, assemble back, etc.
Author Solution
Though the crew assured the instruction manual offered no easier bearing changing method, the author felt designers would have envisaged an easier bearing changing method:
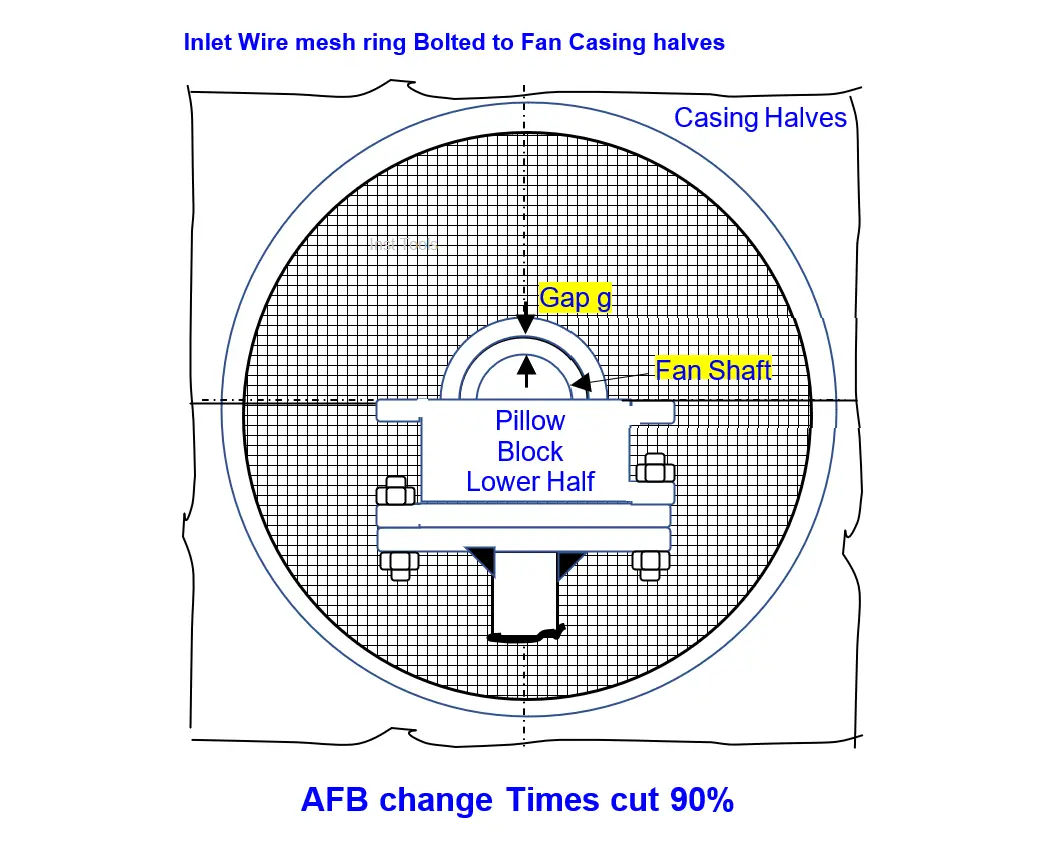
He carefully viewed the fan 10 minutes and suggested to replace the AFBs thus:
- Arrange bearing pullers and electric bearing heaters close by before fan SD.
- Unbolt both side Pillow Block’s upper halves
- Unbolt both sides the top ½ ring bolted to the fan entry filter
- Lift the fan rotor with a crane carefully and slowly till it contacts the casing top; the rotor tip to case bore distance is usually sufficiently large and bearing OD will be clear the pillow block step
- With the crane holding the rotor, replace both the bearings.
- Lower the rotor carefully and guide both end AFBs into the pillow block seat
- Mallet tap the shaft and seat the both end AFBs in the pillow block
- Tighten Pillow Block top halves. The fan is ready for use! Just 2 hours task- not 2 shifts i.e., 16 hours.
The study-based solution Benefits
The plant resumed full capacity production within 3 hours and with just a few easy maintenance efforts and needless 13 hours ½ capacity runs.
Author: S. Raghava Chari
Do you face any similar issues? Share with us through the below comments section.
If you liked this article, then please subscribe to our YouTube Channel for Instrumentation, Electrical, PLC, and SCADA video tutorials.
You can also follow us on Facebook and Twitter to receive daily updates.
Read Next:
- Dozing System Problems
- Pump Low throughput Eliminated
- Fan Motor Journal Bearing Failures
- Turbine to Gearbox Alignment Drifts
- Storage Tanks Ammonia Gas Venting Issue