Root Cause Analysis (RCA): Fired boiler-induced draft fan (IDF) failures upset all plants operations.
Article Type: | Root Cause Analysis (RCA) |
Category: | Mechanical |
Equipment Type: | Miscellaneous Rotating Machine Problems |
Author: | S. Raghava Chari |
Note: This root cause analysis (RCA) is from real-time scenarios that happened in industries during the tenure of two or three decades ago. These articles will help you to improve your troubleshooting skills and knowledge.
Fired Boiler Induced Draft Fan (IDF) Failures
The fired boiler induced draft fan (IDF) failures posed 10-yearlong problems are:
- The Non-Drive End antifriction bearing failed frequently.
- Even with full open guide vanes furnace pressure is above atmospheric and flames shoot out
Root Cause Analysis Solution
Problem 1 Root Cause Analysis Queries (Q) and Answers (A) are:
Q: Why too low AFB lives?
A: The Antifriction bearings (AFB) situates in the hot flue gas path (below figure); maybe excessive temp fails the AFB.
Q: Why excessive AFB temp; surely the makers would have taken care for it to work in the high temp environs
A: Our guessed reasons are
- The bearing housing cooling water lines corrode away quickly, hence water cooling is mostly absent
- The shop is unable to balance the fabricated rotor well; consequent excessive vibrations shorten the AFB lives
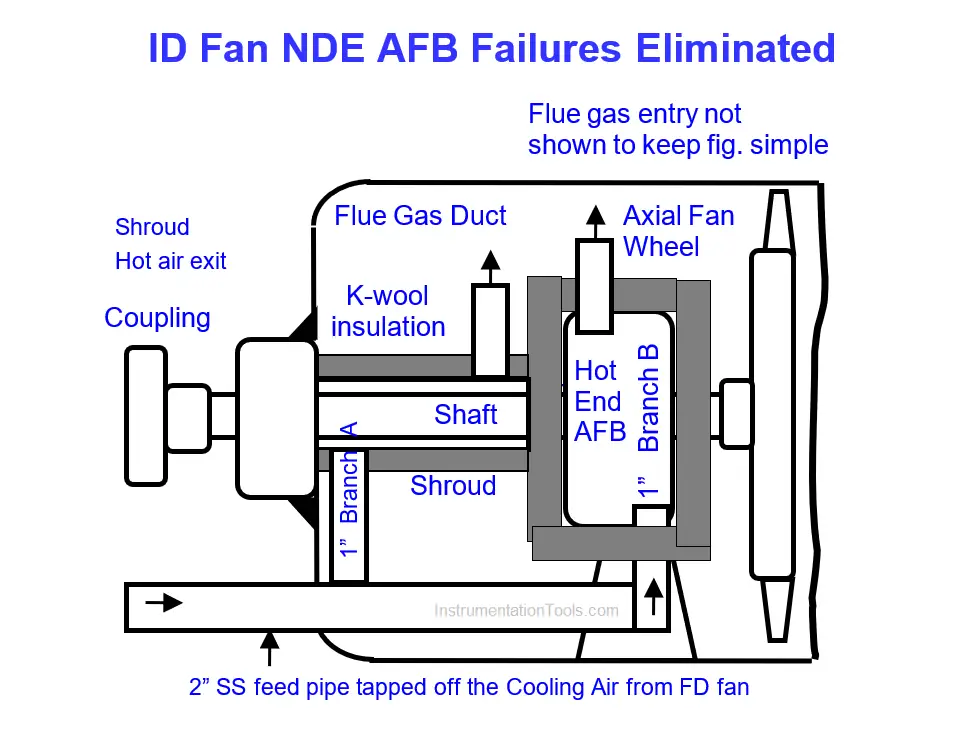
Problem 1 Root Cause Analyzed Solution:
Mulling this information 2-days, the author developed the below-given solutions:
- Insulate the pipe shrouding the shaft and bearing housing with 20 mm thick K-wool – a recently developed low thermal conductivity super insulating material – and SS clade to last long (above figure).
- Cool the AFB with air tapped off the nearby surplus capacity FD fan’ The 2” SS air pipe entering the duct to branch off into 1” branches A and B; branch A fed large cool air quantities to cool the shaft passing through the shroud to reduce hot shaft transmitted heat to the AFB and Branch B fed air to cool the AFB house. Both air shall escape into the duct and reach the environs with the flue gases
Run ¼” SS pipe from AFB grease port extending 150‑mm out of duct wall to pump grease and another for the exiting old grease. Monthly pump in new grease till all old grease is out. Leave the exit grease pipe partially open to let the hot grease out when the fan runs.
Problem 2 RCA queries and answers:
Q: Why poor furnace pressure control?
A: We don’t know Sir”.
The author guessed possible errors in the shop-made fan labeled vendor part No. F 1250. The measured dia was 1210 mm only. Possibly the shop duplicating it from an old rotor committed the error.
The author found a local vendor – he fabricates the rotor for the fan manufacturer – furnished correct size and balanced to standards rotors on his ‘hard suspension’ balancing machines exhausted rated flue gas quantities. Now the furnace pressure is near 0 mm WC with 75% guide vanes open.
Both problems vanished
RCA solution Benefits
RCA solution Benefits are:
- Controlled to zero furnace pressures eliminated flame come outs out of viewing windows and potential operators’ injuries – an essential safety requirement
- due to Reliable and lasting hot end AFB cooling, consequent long AFB lives, 100%, IDF availabilities, smooth uninterrupted boiler runs offered steam production resulted in smooth and uninterrupted NH3 and Urea Plant runs and 10% increased production.
- Gone are the standby motor driven ID fan failing either due to its own poor reliability or power failure while restoring the failed steam driven ID fan threats are gone
- Gone are the often done extremely difficult blinding the fan duct for personnel entry, back-breaking hazardous atmosphere several shifts long failed fan restoration tasks
- Gone are the shop made poor rotors due to locating a reliable vendor capable of supplying dimensionally accurate and well-balanced rotors
- No ID fan work between turnarounds delighted operators and millwrights immensely and boosted their morale though they lost enormous overtime wages
- 20% saved maintenance costs
Author: S. Raghava Chari
Do you face any similar issues? Share with us through the below comments section.
If you liked this article, then please subscribe to our YouTube Channel for Instrumentation, Electrical, PLC, and SCADA video tutorials.
You can also follow us on Facebook and Twitter to receive daily updates.
Read Next:
- Dozing System Problems
- Pump Low throughput Eliminated
- Fan Motor Journal Bearing Failures
- Turbine to Gearbox Alignment Drifts
- Storage Tanks Ammonia Gas Venting Issue