Instrumentation engineering root cause analysis of seal level differential pressure transmitter problems and displacer level transmitters.
Article Type: | Root Cause Analysis (RCA) |
Category: | Instrumentation |
Equipment Type: | Sensors |
Author: | S. Raghava Chari |
Note: This root cause analysis (RCA) is from real-time scenarios that happened in industries during the tenure of two or three decades ago. These articles will help you to improve your troubleshooting skills and knowledge.
Seal Level Differential Pressure Transmitter Problems
Urea Plant’s various vessels seal Differential Pressure Transmitters (DPLTs, fig 1) were the worst of all seal instruments, because these, costing several times more than the seal pressure transmitters too failed as frequently.
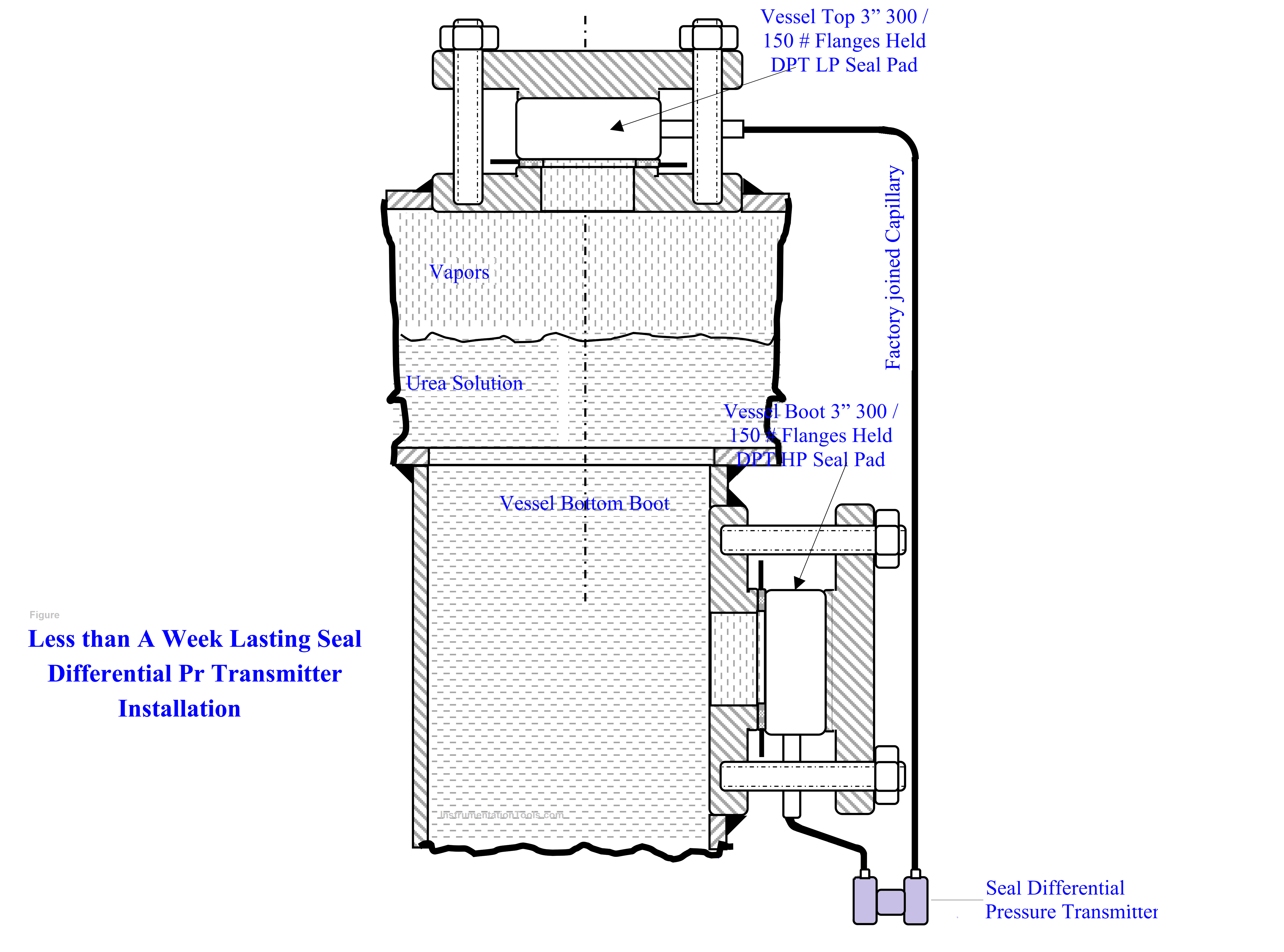
Author Solution
The author after yearlong unsuccessful previously described efforts to make the DPLTs work, gave up and selected Displacer Level Transmitters (DLTs Fig 1).
The below given formidable constraints almost aborted the first displacer level transmitter (DLT) trial; the author thought out, shown under each constraint effective, economical, and easily implementable solutions – shown in italics – won the first DLT trial approval:
- The mechanical crew declined welding steam jacketed 2” taps for bolting the jacketed displacer chamber because of the severe welding code stress relieving requirements
The author proposed bolting the DLTs to the existing 3” vessel top flange itself involving no welding on the vessel
- Other heating tasks small bore steam lines leaks plagued operation and maintenance team vehemently opposed adding 10 steam jacketed displacer chambers jacket heating. Vessel top flange bolted DLTs require no heating steam
- Saturated steam, – the best for heating – non-availability requires using the available superheated steam – a compromise from the best practice
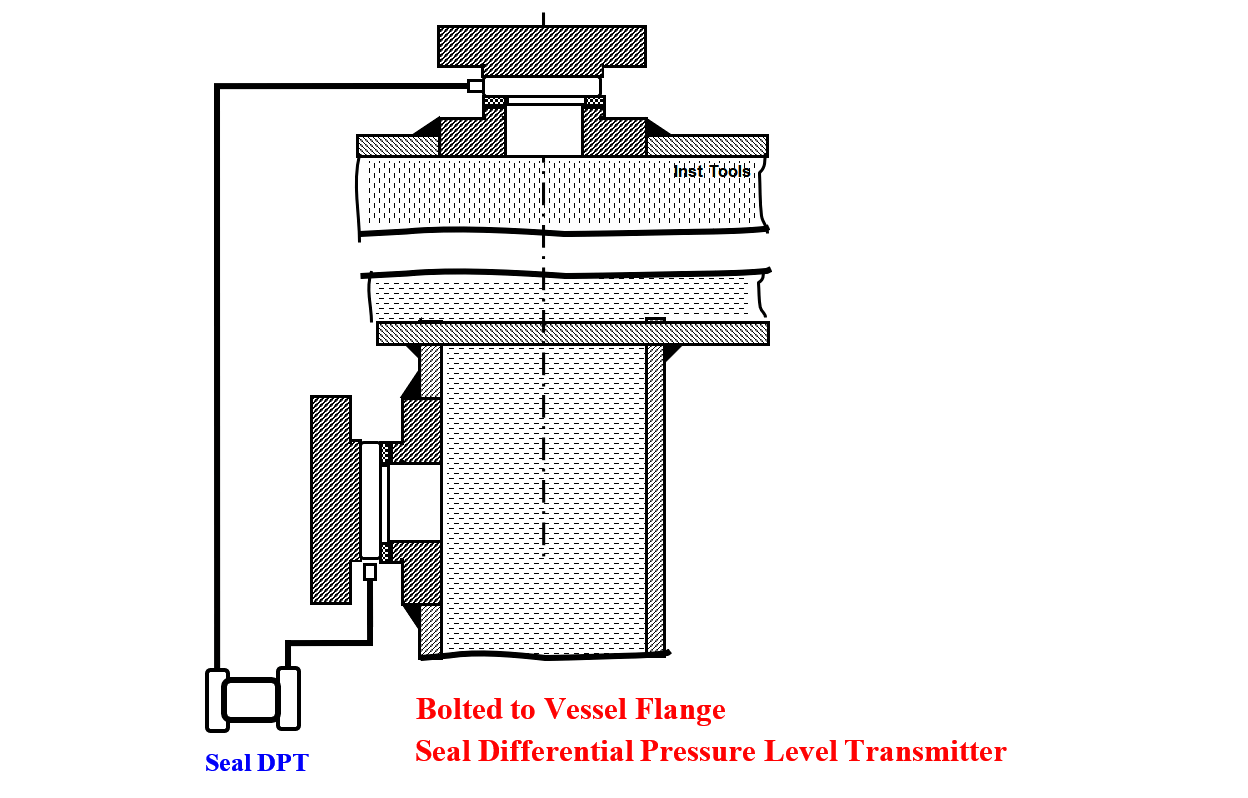
Vessel top flange bolted DLTs require no heating steam
- The author feared, the severe vessel turbulence would unhook the vessel top flange bolted DLT’s torque tube suspended displacer (fig 1) within start up few minutes and fail the DLTs.
The author’s solution: suspend the displacer inside stilling well (SW); SW is a 2” Sch-40 top collar, bottom cover welded and numerous 3‑mm dia fill holes drilled along the SS-316 pipe length. SW prevents not only the vessel turbulent contents unhooking the displacer, but also the consequent lost level readings and the unhooked displacer entering the pump and wrecking it.
- The author feared, bolting the vendor’s standard 2” flanged DLTs on the existing 3” vessel flange may require some innovation
Thanks to the author pointing out the possibilities of 10 Nos. of DLTs order the vendor relented and accepted supplying 3” 300#/150# flanged DLTs – a deviation from his standard. This overcame the mounting problem
Trial Displacer Level Transmitter installed
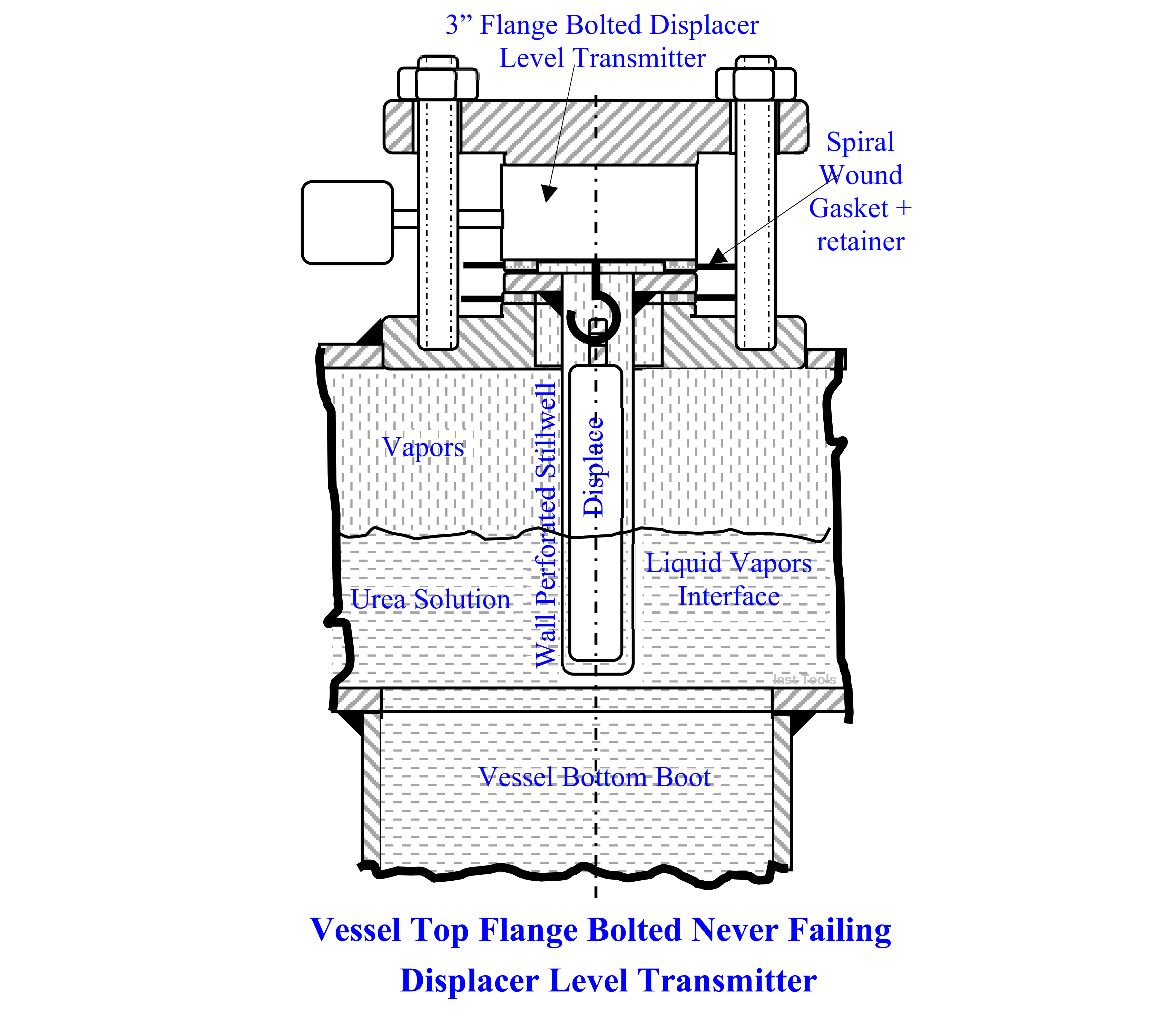
Thanks to the above solutions overcoming all the constraints, the plant approved the first displacer level transmitter (DLT) trial (figure 3). The trial succeeded beyond expectations.
The displacer level transmitter (DLT) worked well even with experimentally closed torque tube condensate flushing – an abundant caution measure – pipe tap valve.
The initially reluctant, but now highly delighted urea superintendent and general manager chased the author to provide the remaining 9 Nos.
Displacer Level Transmitter (DLT) Benefits
Displacer level transmitter (DLT) benefits are:
- The DLTs offered 100% reliable level readings and hence controls, HI & Lo level alarms, Hi-Hi and Lo-Lo level trips provided the so far unavailable vessels and persons safety, smoothed the plant operations, and boosted operator morale.
- The everlasting fit and forget DLTs cost just $700 ea. against a week only lasting and costing $2000 ea. – 80s figures – DPLTs
- They work fine even without the originally proposed torque tube flushing condensate. Hence, not provided for the balance 9 nos. DLTs – an extra cost saver
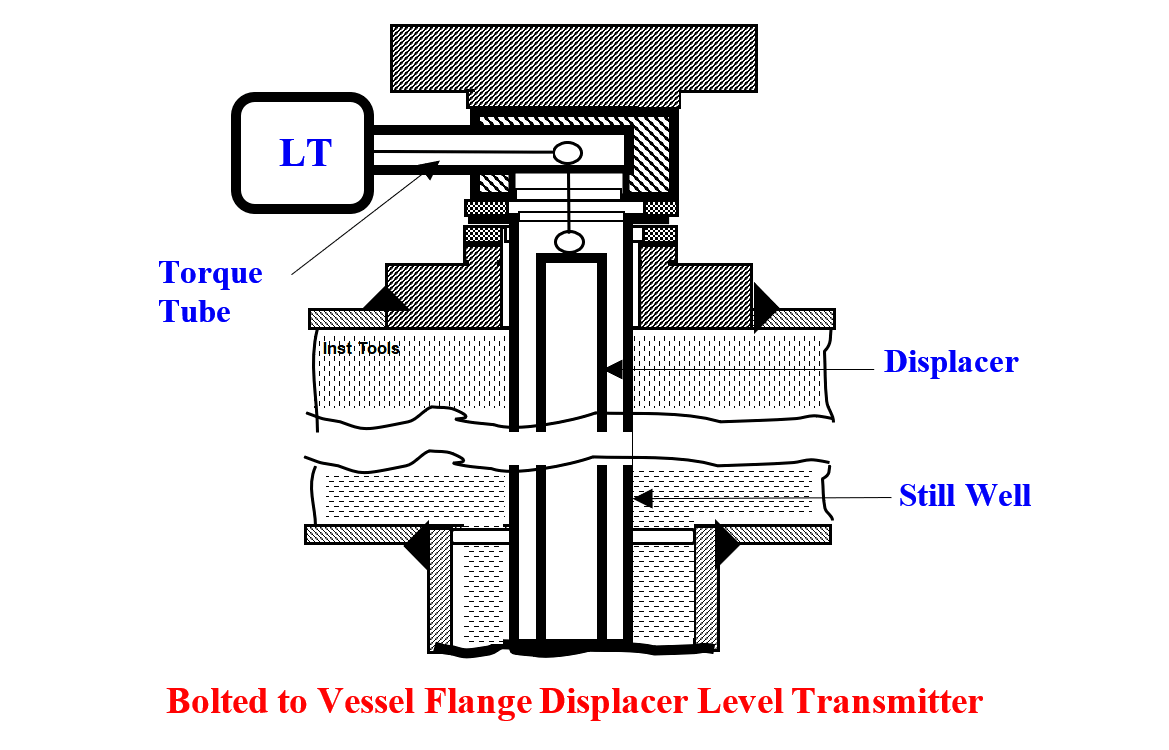
Modification Benefits
High plant safety from reliably restored LI/LC/LA – Hi-Hi and Lo-Lo – enhanced plant safety and boosted operator morale.
The everlasting fit and forget DLTs costed just $700 ea. against $2000 each of a week only lasting DPLTs
- The DLTs bolt to the existing vessel top-flanges; hence, avoids 2” displacer chamber taps and valves buying and welding them to the vessel’s costs. In addition, many wary of welding taps to several vessels confirming to stringent welding codes, perennial jacket heating steam costs and adding to the present prolific steam leaks heaved a relief sigh
- The found solution eliminated superheated steam use for heating – a compromise from best solution
- Added, small-bore heating steam lines leaks problem and steam costs gone
- Costing $ 700 everlasting 10 DLTs replacing 10 Nos. a week only serving and costing $ 2000 each 10 Nos. DPLTs recurring yearly savings run into stupendous several hundred thousand rupees savings
- DLTs offered increased safety, smooth operation, freedom from futile repetitive tasks, and crews’ morale boost are invaluable in terms of money
Author: S. Raghava Chari
Do you face any similar issues? Share with us through the below comments section.
If you liked this article, then please subscribe to our YouTube Channel for Instrumentation, Electrical, PLC, and SCADA video tutorials.
You can also follow us on Facebook and Twitter to receive daily updates.
Read Next:
- Thermocouple Extension Leads
- Pitot-tube Replaced with Orifice
- Mechanical Temperature Indicator
- Pressure Transmitter Stopped Working
- Seal Pressure Instruments Problems