Root Cause Analysis (RCA) related to the roof hot spots repairs and their problem eliminated forever.
Article Type: | Root Cause Analysis (RCA) |
Category: | Mechanical |
Equipment Type: | Pipelines and Miscellaneous Problems |
Author: | S. Raghava Chari |
Note: This root cause analysis (RCA) is from real-time scenarios that happened in industries during the tenure of two or three decades ago. These articles will help you to improve your troubleshooting skills and knowledge.
Roof Hot Spots Problem
20 to 30% of the cast bricks thermally insulating the reformer room fell off randomly yearly, after two years of service. Hazardous emergency repairs of welding cast refractory lined box over the hot spots (HS) avoided plant shutdowns.
The hot spotted parent roof portions plus some adjacent areas disintegrated in time. The plant felt a keen need to stop the recurring, annoying, expensive, and hazard-prone emergency hot spot boxing for safety-enhancing and eliminating the repeated expensive roof metal renewal at the two-yearly turnarounds (TA).
Solution
The plant lined the revamped roof during the INÂ 529 RT change (earlier Problem) with the vendor suggested 12600C grade non-ceramic Fiber blankets (FB). More details follow:
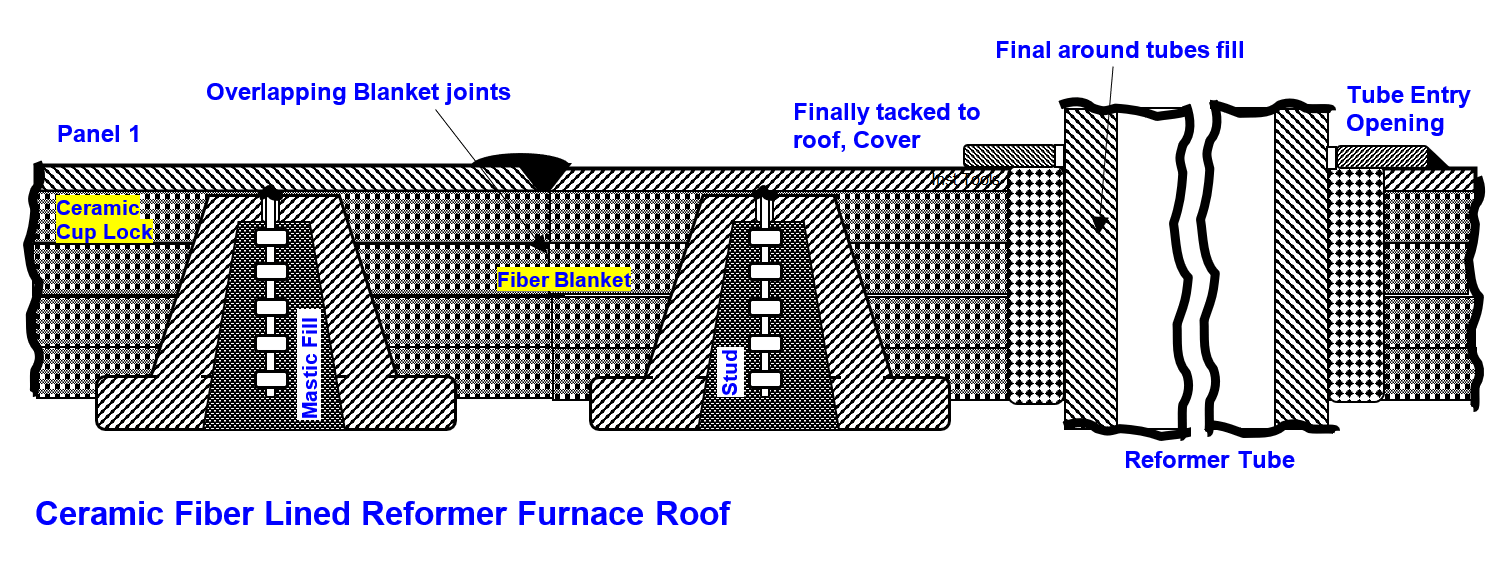
Pre-TA Activity
Below listed are pre-TA tasks:
- Technicians flame cut 3650 x 2950 x 12 mm carbon Steel Roof Plate panels, ground weld edge prepared the ends, chalk marked vendor recommended flat anchor – described later – positions, and cut 220×170 oval openings to insert the 150-mm OD reformer tubes with welded bottom outlet nozzles. The chosen panel dimensions minimizes wastage while cutting out of standard 7500x610x20 mm sized rolls.
- Crew calibrated the vendor furnished welding gun popularly called ‘Six-shooter’ thus: they clamped vendor furnished Inconel Flat Anchor (FA fig 2) to the gun plugged to a 220 V AC outlet; pressing the ‘on button’ they touched the FA to the panel at the marked location. Presto, the FA welds on to the panel instantly and so strong that the weld did not break even on hammering the studs flat with the panel
- Without disturbing the calibrated setting, they welded the flat anchors to the panel (fig 1) at specified longitudinal and lateral pitch. The welding ease and speed of 20 welds / minute surprised all.
- FA underhand shop welding to panels took 50% of the estimated field overhead welding time on the finished roof
- In, addition, saved the scaffold building and stud welding during numerous other revamp activities progress during TA. It saved 6-TA days, and enabled reformer tubes installation and catalyst loading concurrently and rapidly
- Then they spread Fiber Blankets (FB) 4‑layers (fig 2) one at a time on to the panels piercing the FAs. After spreading the 4-blanket layers they inserted the ceramic cup locks (CCL) keeping its top slot parallel to stud width all the way and on more pushing possible, they turned 90O. The CCL top locked in the stud slot and support the blanket sag free and efficiently insulate the roof from the flame and flue gases Â
- Final mastic fill prevents cup-locks accidentally unlocking, heat conduction to the roof and strengthens FB securing.
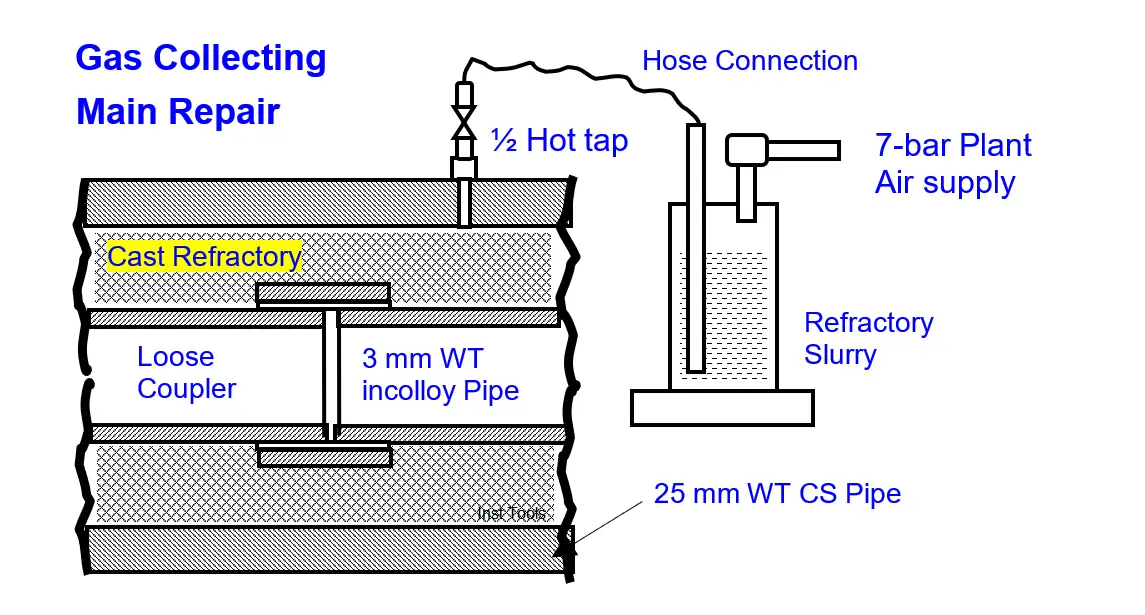
TA activities
Reformer Tubes were out of the reformer for new HK-40 RTs insertion. Technicians tore off the old roof and welded the lined panels to form the lined roof.
The 50-mm blanket protrusions beyond the panel sides butting into dense layer prevents hot flue gases wetting the roof plates at the joints assures cooler root top metal. After an area blanketed roof top completion, the crew moved to another far away area.
Other crews installed the new RTs and welded the outlet pigtails. They welded the inlet pigtails new flanges. The operation started filling catalysts in OPT welded RTs.
Roof crews packed fiber blanket pieces in the RT annuluses to prevent leaks, positioned 20 mm thick CS split cover halves, and tack welded to the roof metal.
Thus, many crews working simultaneously w/o interfering with one other in a coordinated manner completed the RT and Roof change in 14 record days.Â
FB lining an existing good roof with RTs in position though not as easy and quick as above, is practical, cheaper, lot easier and quicker than cast blocks restoration and living with the expenses and hazards of frequent hot boxing.
Benefits of fiber blanket lining
Below listed are the benefits:
- Roof revamp took just 4-TA days only, against the most tightly estimated 30 days of conventional refractory lined roof
- It permitted new RTs insertion and catalyst fill concurrently
- Zero curing time and just a day of temperature ramp time saved further 5 days, i.e. total (30+5 -4=31) on stream days gain
- The rooftop looks elegant and plain thanks to no protruding studs and nuts. No stud holes leaks is a bonus benefit.
- 500C cold-face temperature against the former 70o C, saves recurring 16% energy i.e. hundreds of thousands of rupees of fuel costs yearly and eases working on reformer top – both invaluable benefits. Though the existing structure can easily support several more FB layers, we settled for 4 layers only, as more layers’ incremental cost was higher than the energy loss savings.  Â
- The 20% lower re-roofing costs over conventional refractory roof is an additional bonus
- Estimated service life is nearly 20 years with practically negligible maintenance; on the other hand, the refractory roof initial and ownership costs are very high            Â
Sidewall Refractory
The conventional sidewall refractory was in very good condition. The crew shutdown the reformer at two-year catalyst change intervals only. Hence, it stayed.
However, a much larger 1987-built Saudi 1500T/d Ammonia Plant reformer and a near equal-sized 1998 built world’s largest petroleum refinery reformer are FB lined all over – walls and roof.
Both perform exemplarily maintenance-free even after 5-years of their 20 years life expectancy. Their much lighter structural supports save 30 to 35% steel than that of the author re-roofed reformer.
Author: S. Raghava Chari
Do you face any similar issues? Share with us through the below comments section.
If you liked this article, then please subscribe to our YouTube Channel for Instrumentation, Electrical, PLC, and SCADA video tutorials.
You can also follow us on Facebook and Twitter to receive daily updates.
Read Next:
- Plug Valves Leaks
- Rupture Discs bursts
- Trip Throttle Valve RCA
- Repeat Safety Valve Popping
- Steam Letdown Station Problems