Root Cause Analysis (RCA) related to the eleven numbers of Cooling Tower Fan frequently failing drives.
Article Type: | Root Cause Analysis (RCA) |
Category: | Mechanical |
Equipment Type: | Miscellaneous Rotating Machine Problems |
Author: | S. Raghava Chari |
Note: This root cause analysis (RCA) is from real-time scenarios that happened in industries during the tenure of two or three decades ago. These articles will help you to improve your troubleshooting skills and knowledge.
Cooling Tower Fans Frequently Failing RCA
The author after detailed study considered the two below given alternatives to solve his 3 predecessors gave up 10‑yearlong problem:
Shift the motor inside the CT shell and couple the motor to the Gearbox (GB) to eliminate the 3-m long tubular shaft (LTS) – the problems’ Root cause. The management already besieged with pain in the neck electrical problems instantly rejected it.
Replace LTS with universal joint shaft (UJS, below figure) – the problem vexed management approved instantly trial at two fans.
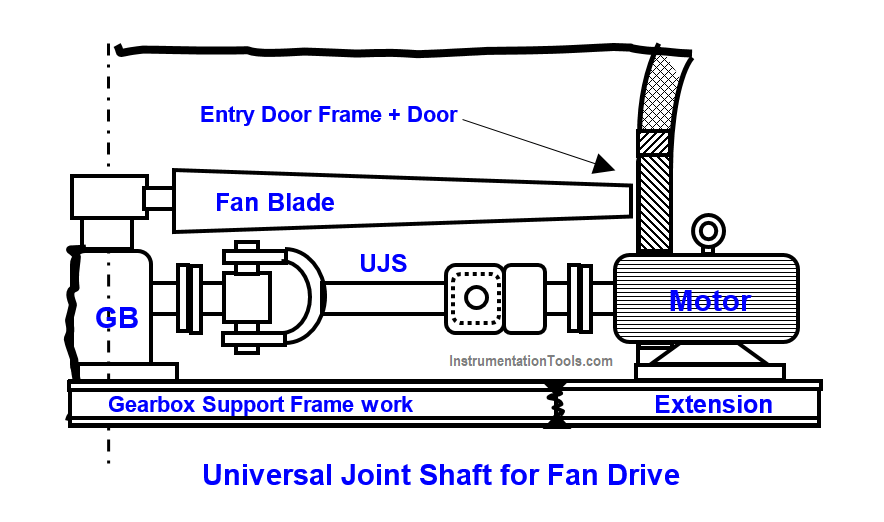
Eliminated Constraints
The author decided replacing the poor life LTSs with universal joint shafts (UJS) because, being a well-engineered, strictly quality controlled for material quality, dimensional tolerances, assembly fit ups and special-painted to withstand the dusty and wet environs the automobiles face.
The faced constraints (C) and remedies (R) follow:
C1-The torque capable longest available UJS was not long enough to couple the motor to the JB!
R1- The author got the motor pushed towards the fan; cutting a hole in the wooden door. 1/3 motor length penetrating into the fan chamber enabled coupling to the GB input shaft
C2-1500 RPM rotation centrifugal force threw the grease out of the UJS; the lubricant starved UJS would fail within weeks; in addition, the falling grease would contaminate the water and pose housekeeping problems.
R-2; Covered the UJS with UJS vendor sold low cost ‘boot,’ benzene washed the old grease, recharged new grease during the two-yearly TAs and covered the joint with new boot. Hence, the UJS lasts forever
Modifications’ Benefits
Below given are the benefits from UJS:
- Thanks to UJS cells availabilities rose to 100% and offered the below given benefits
- Thanks to always near design TCW. Hence, the former frequent NH3 and urea plants load adjustments to suit varying TCW vanished; and the total plant shutdown risks from likely operator errors during load changes too
- Hence, NH3 and Urea production rose 10%. In addition, equipment and personnelnstrains due to load changes also vanished and helped in achieving the corporate goal “keep the plant young”.
- Gone are the 4-6 hours skilled technicians’ time taking motor to gearbox LTS anyway unsatisfactory alignments – the CT cells poor availability root cause
- UJS just fits; it requires no alignment
- Wasteful shop making and balancing with poor results during missed vendor LTS deliveries gone
- The UJS are of top quality as explained before; on the CT vendor offered tubular rigid joint lacked all these.
- Thanks to smoothest vibrations free and durable UJS drives the motors’ and gearboxes’ bearings’ lives exceed the 50,000 hours (nearly 6 years) L10, lives. Associated benefits are bonus.
- Readily available UJS eliminated large inventory holding costs and eliminated the former delayed deliveries anxieties and need for in-house LTS making
Author: S. Raghava Chari
Do you face any similar issues? Share with us through the below comments section.
If you liked this article, then please subscribe to our YouTube Channel for Instrumentation, Electrical, PLC, and SCADA video tutorials.
You can also follow us on Facebook and Twitter to receive daily updates.
Read Next:
- Turbo-Compressor Problem
- Compressor Anti-Surge Control
- Plant Air Compressors Problems
- Plant Turbo-compressor Problem
- Failing Plant Air Compressor Drives