After several years of service the urea reactor top bolted plug developed leaks. This root cause analysis solved the problem.
Article Type: | Root Cause Analysis (RCA) |
Category: | Mechanical |
Equipment Type: | Pipelines and Miscellaneous Problems |
Author: | S. Raghava Chari |
Note: This root cause analysis (RCA) is from real-time scenarios that happened in industries during the tenure of two or three decades ago. These articles will help you to improve your troubleshooting skills and knowledge.
Urea Reactor Top Bolted Plug Leaks
After several years of service the urea reactor 400 mm, dia x 280 mm thick top bolted plug (fig A) developed leaks.
Tightening the studs loads the 30o included angle plug (fig B) and the 20o included angle reactor body opening conical portion line contact resulting in leak tight joint.
Crew usually repair such leaks by lapping the plug cone and reactor opening cone with a cast iron lap paste smeared lap block.
Usually the task takes several shutdown days. Since, the minor leak posed neither serious safety nor environment hazard; the plant lived with the leak awaiting a suitable repair opportunity.
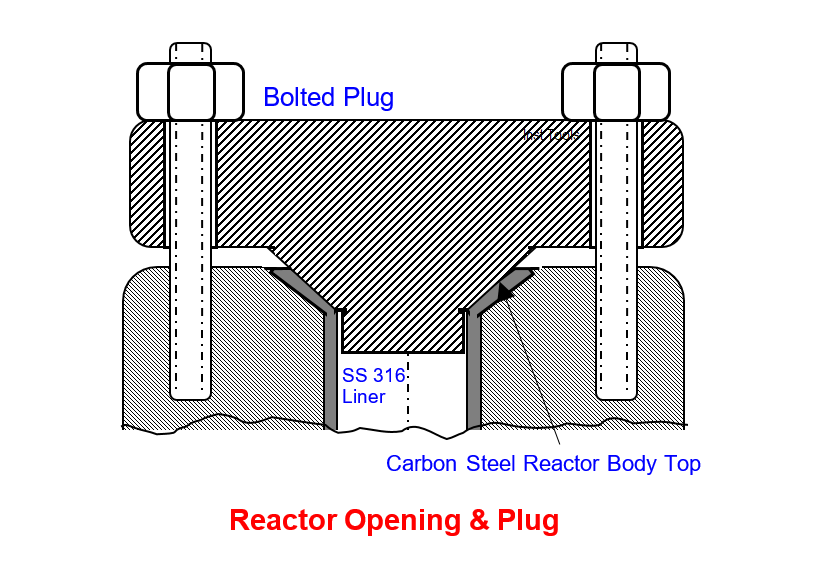
Crew’s leak stop attempt
Crew leader showed the CI lapping block showing only cone to lap the reactor 20o included angle opening using the reactor drawing given information (fig B), and another lap block for lapping the 30o plug sketch. Â
The author appreciated the crew leader sketch. In addition, he suggested cutting the plug cone-lapping portion also on the same block to save costs. The lapping block was ready in few days.
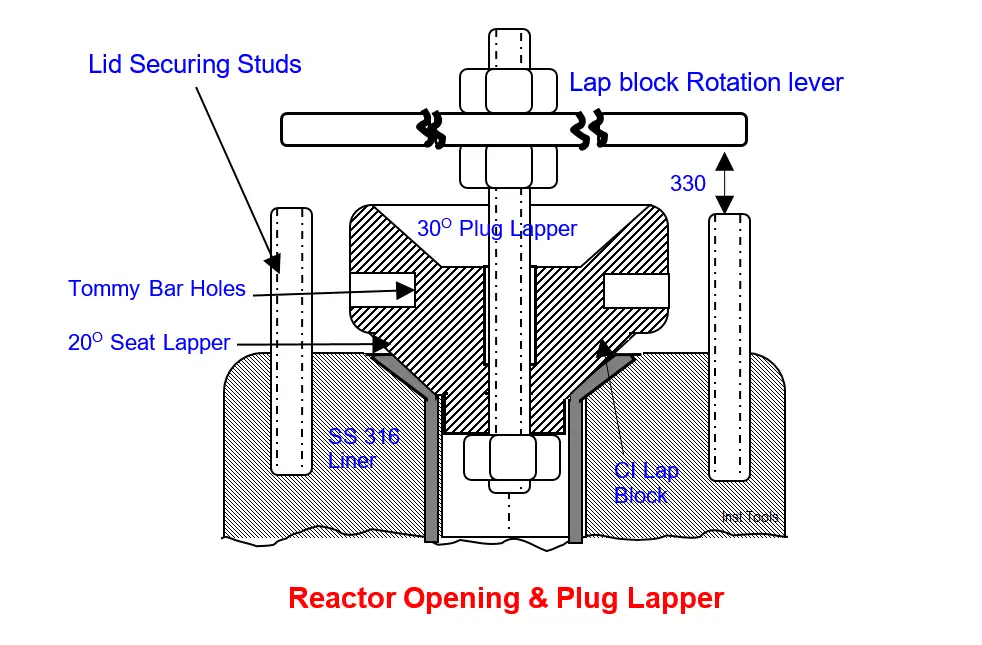
Repair Attempts
Severe draught forced an indefinite plant shutdown. The crew started the task. The leader reported two days later that two nos. cover studs defy unscrewing from the reactor body even with violent efforts. It would prevent Tommy bar Clockwise (CW) and CCW lap block rotation. Hence, lapping has not yet started.
The author chided himself for overlooking this possibility when he reviewed the lap block sketch.
He educated the crew to avoid unscrewing studs from vessels and valves as this could damage the body threads. Their repair is lengthy and time taking and often beyond field crew’s resources.
Site visit and few minutes thinking flashed him an idea: just drill a hole in the lapping block center and tighten a long stem to accept the Tommy bar well above the studs (fig B). Often site visits will generate ideas, which sometimes don’t occur on the office table drawing studies.
The crew lapped the reactor seat with the tall stem fitted lap block. They removed the stem, inverted the lap block and lapped the plug also. The entire task was over in a week working general shift hours only.
Operation crew 300 bars hydro-tested reactor with chlorides free condensate using the air operated piston pump that came with the plant. No leaks cheered all.
In addition, the crew learned the evils of violently unscrewing studs from vessel and valve bodies.
Author: S. Raghava Chari
Do you face any similar issues? Share with us through the below comments section.
If you liked this article, then please subscribe to our YouTube Channel for Instrumentation, Electrical, PLC, and SCADA video tutorials.
You can also follow us on Facebook and Twitter to receive daily updates.
Read Next:
- Gas Cooler Re-tubing
- Rotary Granulator Drive
- Problems with Demister Pads
- Steam Letdown Station Problems
- Bucket elevators Chain Problems