In the realm of industrial automation, communication between various devices, such as sensors, actuators, and controllers, plays an essential role. One protocol that has been developed to facilitate this communication is known as Profibus. But what is Profibus, and why is it essential for industrial automation? Let’s dive in and explore.
What is Profibus?
Profibus (Process Field Bus) is a standard for fieldbus communication in automation technology. It was first promoted in 1989 by the German federal department for Education and Research with the intention of providing a robust, efficient, and flexible communication protocol for a wide range of industrial applications.
Understanding Fieldbus Communication
Before we go any further, it’s important to understand the concept of a fieldbus. In simple terms, a fieldbus is a system for serial data transfer in the field level of an industrial environment. It enables communication between various automation devices, reducing the need for a large amount of cabling.
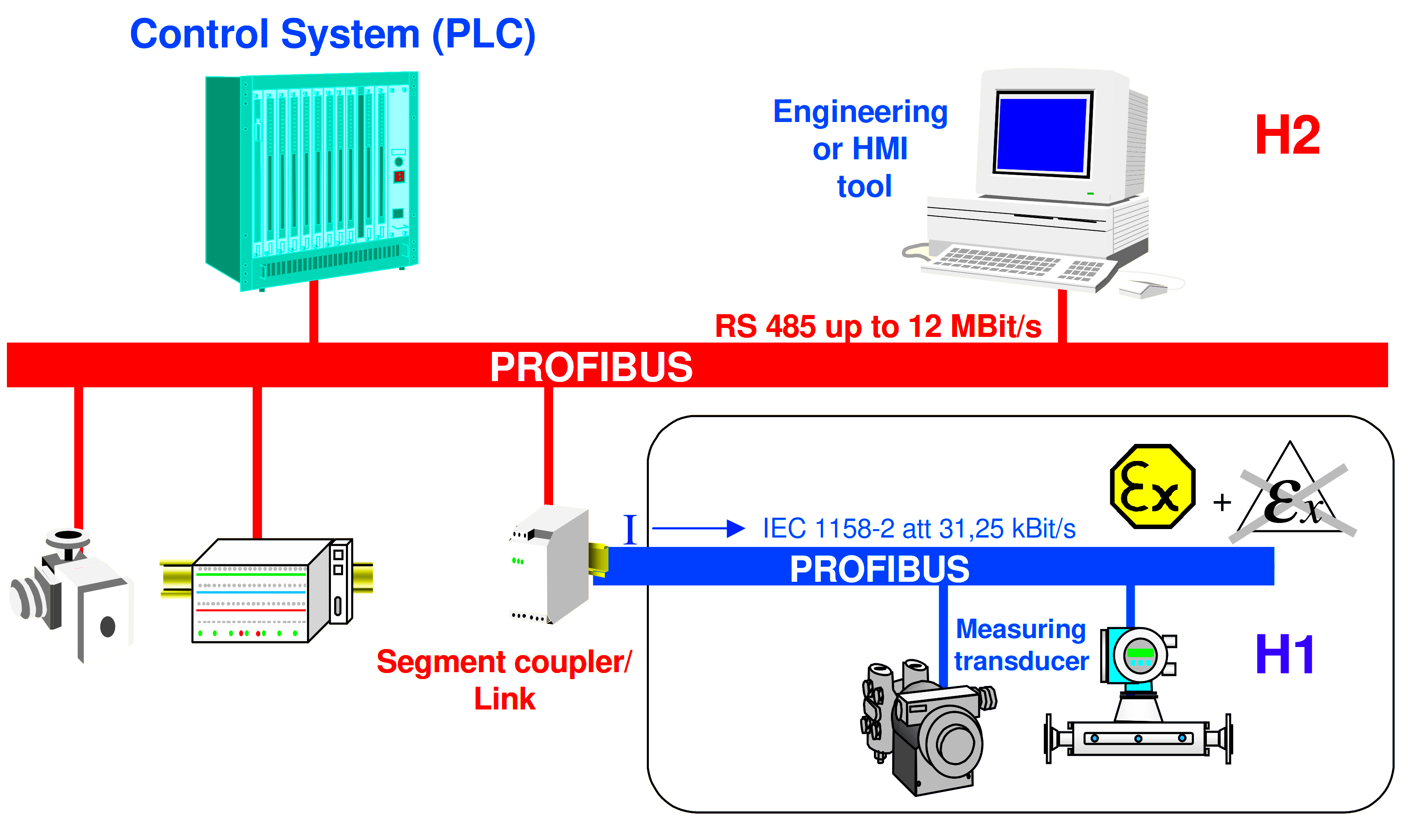
Traditional control systems used point-to-point wiring for each device, which was time-consuming, expensive, and inefficient. Fieldbus systems, on the other hand, use a single cable (the bus) that all devices connect to, significantly simplifying the setup.
How Profibus Works?
Profibus employs a Master-Slave communication architecture. In this setup, one or more devices act as masters, controlling communication on the bus, while other devices act as slaves, responding to requests from the master.
There are two versions of Profibus that utilize this Master-Slave structure:
- Profibus-DP (Decentralized Peripherals): This is the most used version and is designed for fast communication between control systems and I/O devices.
- Profibus-PA (Process Automation): This version is used for process automation applications, particularly in potentially explosive environments. It includes features for powering field devices over the bus and intrinsically safe operation.
Key Features of Profibus
Profibus is recognized for its robustness, versatility, and interoperability. Here are some of its main features:
- Speed and Efficiency: Profibus can support up to 12 Mbps data transfer rates, ensuring quick and efficient communication.
- Interoperability: Profibus enables devices from different manufacturers to communicate seamlessly, thanks to its standardized communication protocol.
- Flexibility: The protocol can be used in a variety of network topologies, including tree, star, and ring structures.
- Cost-Effective: By reducing the need for extensive cabling and allowing for easier system expansion, Profibus provides a cost-effective solution for industrial automation.
Profibus Communication – A Manufacturing Plant Example
Let’s consider a manufacturing plant that produces bottles.
Setup
In this manufacturing plant, there’s a main control room housing the Programmable Logic Controller (PLC), which serves as the Master in our Profibus network. Various devices spread throughout the plant act as the Slaves – these include sensors that measure temperature and pressure, motors that control conveyor belts, and actuators that control the bottle-filling stations.
Step 1: Master Message
Let’s start with the conveyor belt system. The PLC, acting as the Master, sends a command to a motor controller (a Slave) to start the conveyor belt. This command is sent over the Profibus network, reaching the motor controller that’s been specifically addressed by the PLC.
Step 2: Slave Response
Upon receiving the command, the motor controller starts the motor, and the conveyor belt begins to move. The motor controller then sends an acknowledgment back to the PLC, signaling that it has successfully received and executed the command. This round-trip communication occurs very rapidly, often within milliseconds.
Step 3: Next Command or Device
After successfully starting the conveyor belt, the PLC sends another command, this time to a temperature sensor (another Slave) near the bottle filling station. This is a read command, as the PLC needs to verify that the temperature at the filling station is within an acceptable range for safe and efficient operation.
Step 4: Continuous Cycle
The temperature sensor sends the requested data back to the PLC. If the temperature is within the safe range, the PLC sends a command to the actuator at the bottle filling station to begin filling the bottles. If the temperature is too high or too low, the PLC could send commands to other devices in the network to adjust the temperature accordingly. This cycle of communication continues, ensuring the smooth and efficient operation of the entire manufacturing process.
Through the Profibus network, the PLC can quickly and accurately control the many devices involved in the manufacturing process. The PLC can send and receive data, monitor device status, and respond rapidly to any issues that may arise, maintaining the safety and efficiency of the plant.
Profibus Applications
Profibus is used in many different industrial sectors. In factory automation, it’s used to connect I/O devices to controllers, such as PLCs. In process automation, Profibus provides a reliable solution for transmitting process data and control signals.
Its robust and reliable nature also makes it suitable for applications in sectors like energy, water treatment, and transportation.
Characteristics of Profibus communication
Certainly, here are the key characteristics of Profibus communication:
- Standardized Protocol: Profibus follows a standardized protocol according to IEC 61158 and EN 50170. This means that devices from different manufacturers can communicate with each other seamlessly.
- Master-Slave Architecture: Profibus employs a Master-Slave architecture, where the master initiates communication and the slaves respond. This structure ensures controlled and orderly data transmission.
- Fast Data Transfer Rates: Profibus supports data transfer rates up to 12 Mbps, which allows for efficient and rapid communication between devices.
- Flexible Network Topologies: Profibus can support several network topologies, such as line, ring, and star structures, providing flexibility in system design.
- Scalability: Profibus allows for adding or removing devices from the network without interrupting communication, which offers scalability to the system.
- Supports Up to 126 Devices: A single Profibus network can support up to 126 devices (including the master), which is more than sufficient for most industrial applications.
- Robust Communication: Profibus is designed to offer reliable and robust communication, making it suitable for harsh industrial environments.
- Supports Redundancy: Profibus supports network redundancy, which means that a backup master can take over if the primary master fails, ensuring continuous communication.
- Safety Protocol Integration: Profibus includes a safety-related protocol called PROFIsafe, designed for transmitting safety-related data.
- Multi-vendor Interoperability: Thanks to its standardized nature, Profibus allows for devices from different manufacturers to operate together, providing a wide range of choices when designing a system.
- Diagnostic Capabilities: Profibus offers diagnostic capabilities, which can help with preventive maintenance and troubleshooting, reducing downtime.
- Cost-Effective: By reducing the need for extensive wiring and allowing for easier system expansion, Profibus can provide a cost-effective solution for industrial automation.
Profibus Specifications
Here are some of the key specifications of Profibus:
- Type of Protocol: Fieldbus Protocol.
- Communication Model: Master-Slave and Peer-to-Peer.
- Transmission Speed: Speeds range from 9.6 kbps to 12 Mbps.
- Maximum Devices: Supports up to 126 devices per network segment, including the master.
- Cable Length: With a transmission rate of 12 Mbps, the maximum cable length is 100 meters, but at lower rates, this can be extended up to 1200 meters without repeaters.
- Topology: Supports several topologies, such as bus, star, and ring.
- Types of Profibus: Profibus DP (Decentralized Peripherals), used primarily for high-speed communication between control systems and I/O devices, and Profibus PA (Process Automation), designed for process automation applications.
- Media: Twisted pair and fiber optic cables.
- Conformance Testing: Certified by the PNO (Profibus Nutzerorganisation, Profibus User Organization).
- Safety Communication: Integration with PROFIsafe protocol for safety-related communication.
- Power Supply: Most Profibus devices are powered externally, but Profibus PA supports supplying power to devices over the bus.
Profibus and Industrial Safety
Profibus includes a safety-related protocol known as PROFIsafe, specifically designed for transmitting safety-related data. This ensures that devices operate safely and predictably, making Profibus suitable for applications with high safety requirements.
Advantages of Profibus Communication
- Reliability: Profibus is renowned for its reliability and robustness in industrial environments, offering consistent performance even in demanding situations.
- Real-Time Communication: Profibus supports real-time communication, which is essential for time-critical applications in automation systems.
- Simplicity: Profibus is simpler to install and configure compared to some other protocols due to its master-slave architecture.
- Mature and Widely Supported: Profibus has been around for decades and is supported by a large number of devices from many different manufacturers.
- Integration of Field Devices: Profibus allows easy integration of field devices into the control system, offering a wide range of network components for various application profiles.
- Safety Features: With the PROFIsafe profile, Profibus also supports safety-oriented communication.
Disadvantages of Profibus Communication
- Limited Speed: While Profibus is suitable for most industrial applications, its maximum speed of 12 Mbps may not be enough for some high-speed or large data volume applications.
- Master-Slave Architecture: The Master-Slave architecture used by Profibus can be a limitation in systems where peer-to-peer communication is desirable.
- Limited Cable Length: Without repeaters, the cable length of a Profibus network is limited, especially at higher transmission rates.
- Adaption to IT Systems: Unlike Profinet, Profibus does not use standard Ethernet, so it does not integrate as seamlessly with existing IT systems.
The Future of Profibus
While newer communication protocols like Profinet are becoming more prevalent in the industry, Profibus still holds a substantial market share. Its reliability, wide applicability, and established base of installed devices ensure that it will continue to be a vital part of industrial communication for years to come.
Conclusion
Profibus has undoubtedly become a cornerstone of industrial automation. By providing a robust, efficient, and interoperable means of communication, it has made the process of automation significantly easier and more effective. Whether you’re an engineer looking to implement an automation system, or simply curious about industrial communication, understanding Profibus is undoubtedly beneficial.
If you liked this article, then please subscribe to our YouTube Channel for PLC and SCADA video tutorials.
You can also follow us on Facebook and Twitter to receive daily updates.
Read Next:
- All About Fieldbus Protocols
- Basics for CAN Bus Protocol
- Industrial Automation Protocols
- Fieldbus Transmitters Calibration
- AS-interface and DeviceNet Protocol
What is the difference between Profibus and Foundation fieldbus?