In this post, we will understand the various communication protocols used in PLC (programmable logic controller).
Communication is an important role player in PLC. Apart from traditional hardware IO’s, communication protocols provide more diversity and flexibility to exchange data with various means.
Communication Protocols in PLC
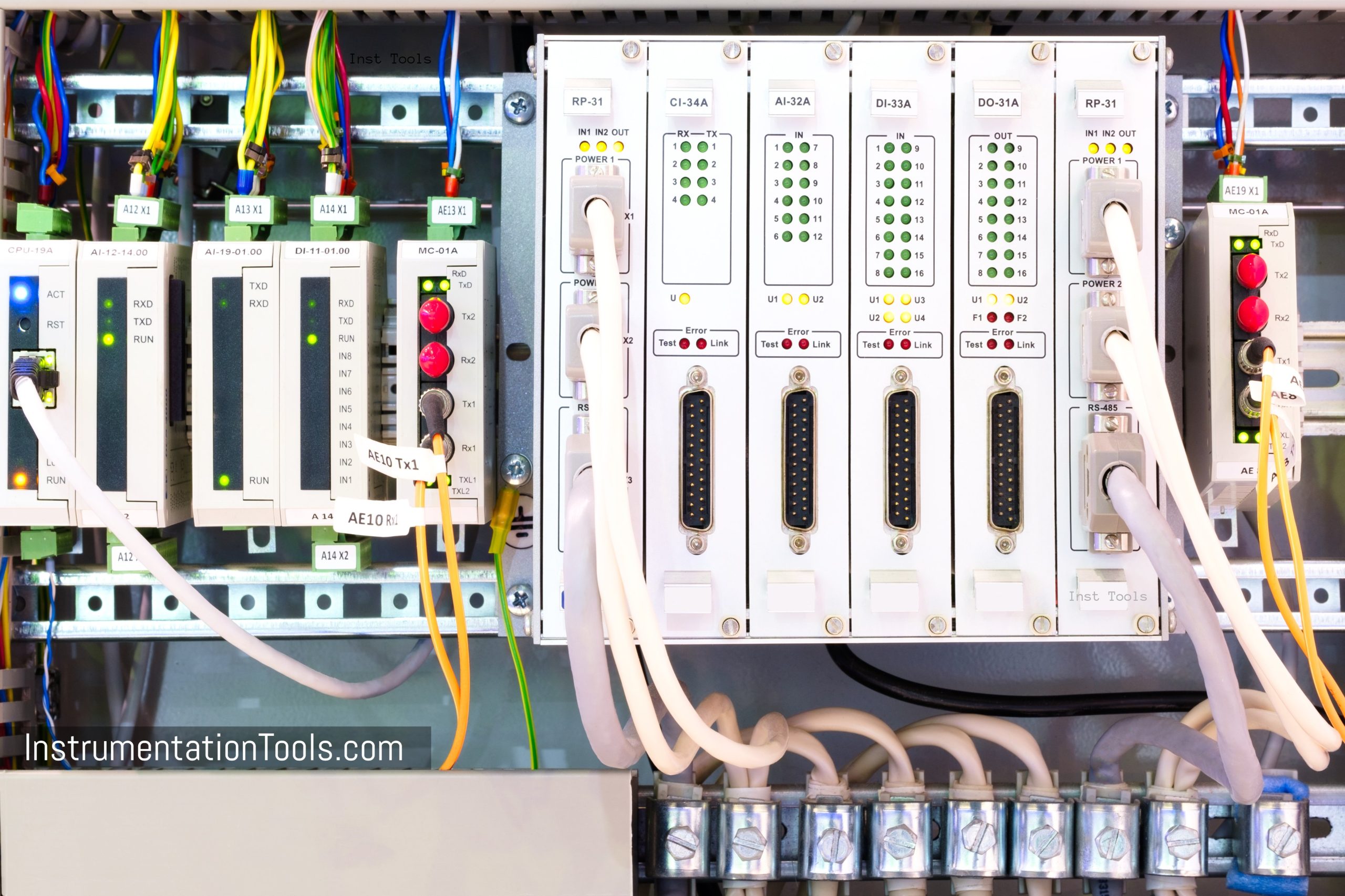
You must be familiar with OSI layers and different types of communication hardware ports used in PLC, to understand the whole cycle of communication in a better way.
We will here see the various communication methods used in a PLC:
Ethernet/IP
It is a protocol that works under Common Industrial Protocol (CIP), which is an open application layer protocol. It is an advanced version of standard Ethernet, which is useful only for in-home and commercial purposes; but not for industrial applications.
It defines all the devices on a network as a series of objects and binds all of them to work on the same standard. This protocol was developed by Rockwell Automation.
Similar protocols with these standards are Profinet, ControlNet, DeviceNet and RAPIEnet. They are different in it’s OSI layers and have their individual functions which differentiate themselves from each other. They have been manufactured by different vendors.
Modbus
Modbus is a protocol that is used for transmitting information over a serial lines or Ethernet, based on master-slave technology. Â
Here we have two types of devices in this communication. The devices which request information are called Modbus Master and the devices which provide the information are called Modbus Slaves.
It is further categorized into Modbus RTU, Modbus ASCII, and Modbus TCPIP. This protocol was developed by Modicon (now Schneider Electric).
Profibus
It is similar to Modbus RTU, which also works on serial line communication. The only difference is that it is owned by Siemens Automation.
Optomux
It is a serial network protocol that works on RS-232/RS-485 and works on ASCII standard. It was developed by Opto22.
Similar protocols with these standards are Interbus and DirectNet.
DF-1
It is an asynchronous byte-oriented protocol that is used to communicate with only Rockwell devices based on RS-232.
Interbus
It is a serial network protocol which works on RS-232/RS-485 and works on RTU standard.
It was developed by Phoenix Contact.
HostLink
It is a serial network protocol that works on RS-232/RS-485 and works on RTU standard.
It works only on Omron PLCs. It was developed by Omron.
Data Highway (DH+)
It is a protocol developed by Rockwell Automation and uses transformer-coupled differential signals; meaning that the transmitter and receiver stations need not be at the same ground potential.
It works with the differential signaling concept. It uses two wires for data transfer and the data is represented with voltage differences in the two wires. Here the data is carried with differential voltages, the noise will be easily removed in the two wires.
It uses half-duplex transmission for communication. It is a very old protocol and is used only in Rockwell PLCs. Nowadays, it has become obsolete and rarely used.
It works on token-passing protocol and uses trunk lines with drops.
Point to Point (PP)
As the name suggests, it is a communication protocol which is used to communicate between only two connected devices.
It is byte-oriented and is full duplex.
Actual Sensor Interface (ASI)
It is a protocol that is used to connect all the sensors and actuators in a field with a single two-conductor cable.
It reduces the wiring and manpower done to connect the field equipment to the PLC. It works in master-slave technology.
Open Smart Grid Protocol
This protocol has been developed to connect all the electrical devices in a power grid through communication and make it a smart grid system.
The devices are meters, direct load control modules, solar panels, gateways, and other smart grid devices.
Due to use of communication, all the information is transmitted in a safe and efficient way; to make the whole power grid system a better way to operate.
CAN (Controller Area Network) Open
This protocol is an application layer protocol that communicates with various devices using peer messaging. It is a multi-master slave communication system and has an object dictionary that contains all the functions of a device.
This is an actual communication mean and has standard communication objects for real-time data (PDO’s), configuration data (SDO’s), timestamp, sync message, emergency message, boot-up message, NMT message, and error control message, and other data.
In a hardware configuration, one point to remember is that it requires termination at the end device to establish the whole link communication.
HART (Highway Addressable Remote Transducer)
HART is a protocol in which digital data is superimposed on the traditional analog signal of 4-20 mA; so that the user gets both the analog information as well as digital information.
HART-enabled field transmitters and actuators are of great use in industrial automation; as the user gets all the information and calibration settings sitting at one corner in the office.
Conclusion
These are the general communication protocols used in PLC. Apart from these, many more are available depending on different manufacturers.
Did we miss any communication protocol? Share with us through below comments section.
If you liked this article, then please subscribe to our YouTube Channel for Instrumentation, Electrical, PLC, and SCADA video tutorials.
You can also follow us on Facebook and Twitter to receive daily updates.
Read Next:
ASi- Actuator Sensor Interface not Actual sensor interface