Industrial automation systems involve various use of machinery and equipment. Operators operate a machine and do the required production activities. Because of automated actions, operators require less of their intervention in it. All the processes will be properly controlled and maintained by automation systems.
Due to this, there are many occasions where an operator sometimes gets relaxed and overlooks some issues, hoping that they will be solved automatically. This working style can prove dangerous sometimes, because if the issue is very grave, then it can prove life-threatening too. So, safety when working in automation systems needs very serious attention.
Safety in Automation Systems
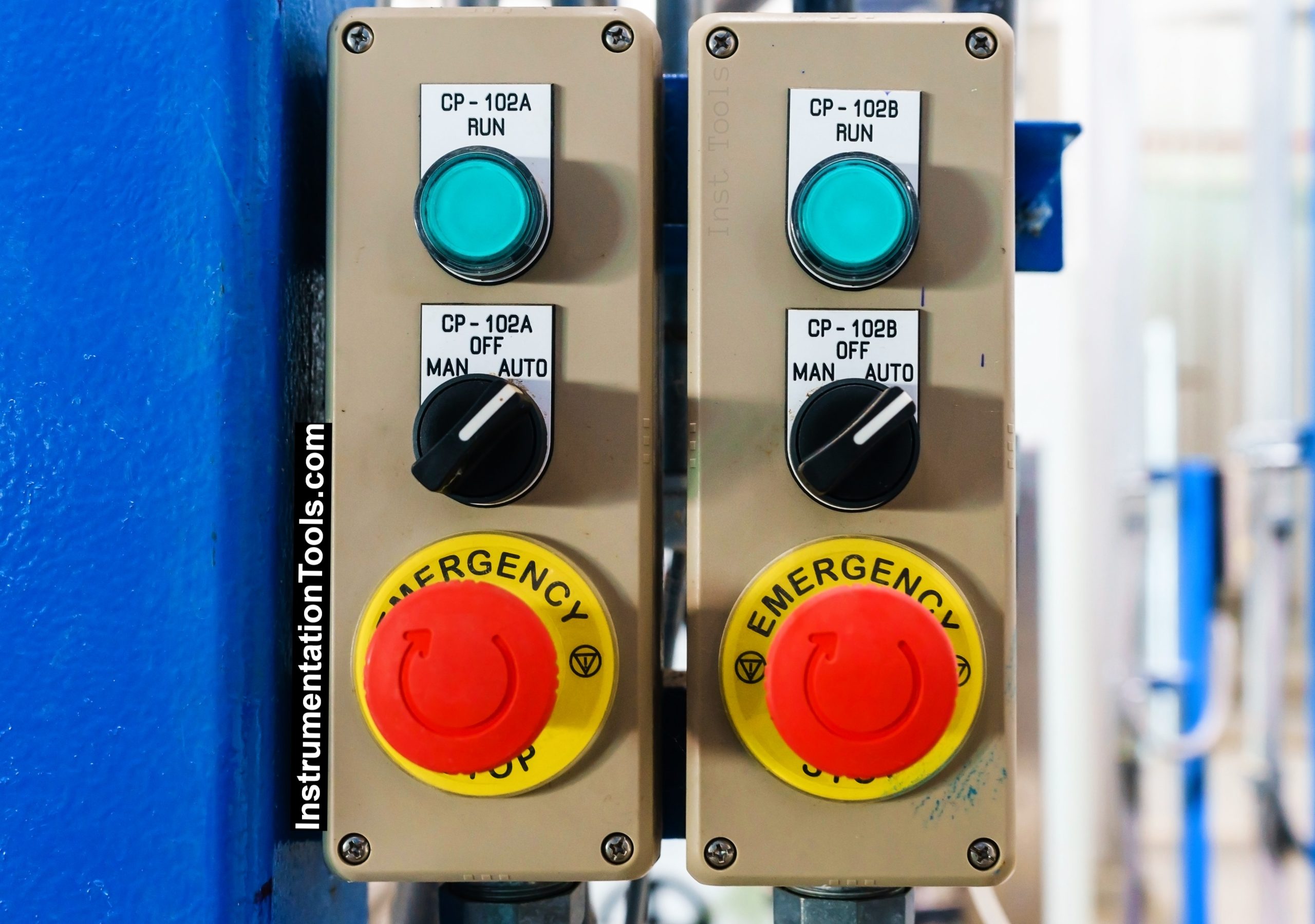
Also, efforts must be done to safely bring down a system, complete the task and exit the zone. There are typical applications associated with high risk, e.g. presses, saws, tooling machines, robots, conveying and packing systems, chemical processes, high-pressure operations, off-shore technology, fire and gas sensing, burners, cable cars, etc. which need special care and technology; thus bringing safety considerations into the picture.
This mindset of working ensures a very safe operation for the personnel as well as the nearby environment. In this post, we will see the various types of safety in automation systems.
Emergency Stop
This is the most common and generally used safety action in automation systems. When there is a PLC system, its digital input is considered (in the NC way). The program is written in such a way that when this input is not received, then all the PLC outputs will stop immediately and the process will pause.
When there is no PLC used in the system, it’s wiring in the control panel is done in such a way that it will break the circuit of all outputs immediately. The operator will press the button when he finds any abnormal situation happening in a process. When everything becomes normal again, then he will release the button and start the process again from where it was paused.
Light Curtains
As the name implies, invisible light is continuously present around a hazardous operating machine. The purpose of a light curtain is to sense any object or person present near the machine, and then stop the machine immediately.
When the light beam is obstructed by the presence of a person, then all the outputs turn off. When the operator has moved away, he can then press the reset function in it and start the system again. Light curtains are required where no presence is necessary in front of the machine, as any nearby presence can prove harmful or life-threatening to the person.
Area Scanners
This can be termed as an extension of the light curtain. A continuous laser beam is rotated and emitted by the scanner. The beam intensity can be varied according to your requirement.
When the beam detects any person or object in this range, then all the outputs will stop immediately. When the operator has moved away, he can then press the reset function in it and start the system again.
Safety Mats
Safety mats are pressure-sensitive machine-safeguarding products for the industrial marketplace. Safety mats are designed to detect the presence of workers or passers-by on the mat surface area around hazardous machines.
These safety mats are flexible, impact resilient, functional after punctures, extremely durable, and will not rust. This functions the same as discussed earlier; detecting the presence and stopping the system.
Robot safety measures
Robots are extremely useful and help in reducing the task to a great extent. But, it is also to be noted that moving around robots is dangerous, especially if the machine is also critical. If any untoward incident happens in the robot, then it can be life-threatening for the nearby workers.
So, robots must always be operated in a zone, marked by some highlighting colors. This prevents the workers and operators from roaming around them. Also, limit switches and sensors are present in a robot, to detect any presence and stop the machine.
Safety PLC
The last but not the least solution used nowadays is a safety PLC. It is different from a standard PLC, in the sense that it has safety functions in it according to various SIL categories. They are specially designed to be rugged and durable, able to withstand the industrial environment.
Safety PLCs have redundancy designed in them for wiring practices and IO monitoring. This helps to function and switch to a standby IO in case of primary IO failure. Another key factor of a safety module is that they are dual-channeled with testing. Input signals are not only received on a terminal but a pulsing test node is also wired to very device integrity.