In this article, we will discuss the commissioning and testing procedure of PLC (Programmable Logic Controller).
Various first-time programmers of industrial automation face a question on what to do when they are asked to test a PLC and its logic properly.
Well, it is obvious because every new task requires some set of rules and steps to follow for proper execution. So, commissioning a PLC is also a tedious task for a new programmer.
PLC Commissioning
In this post, we will see some general guidelines regarding the commissioning of a PLC. Using these, any new programmer can easily test a PLC and its logic afterward.
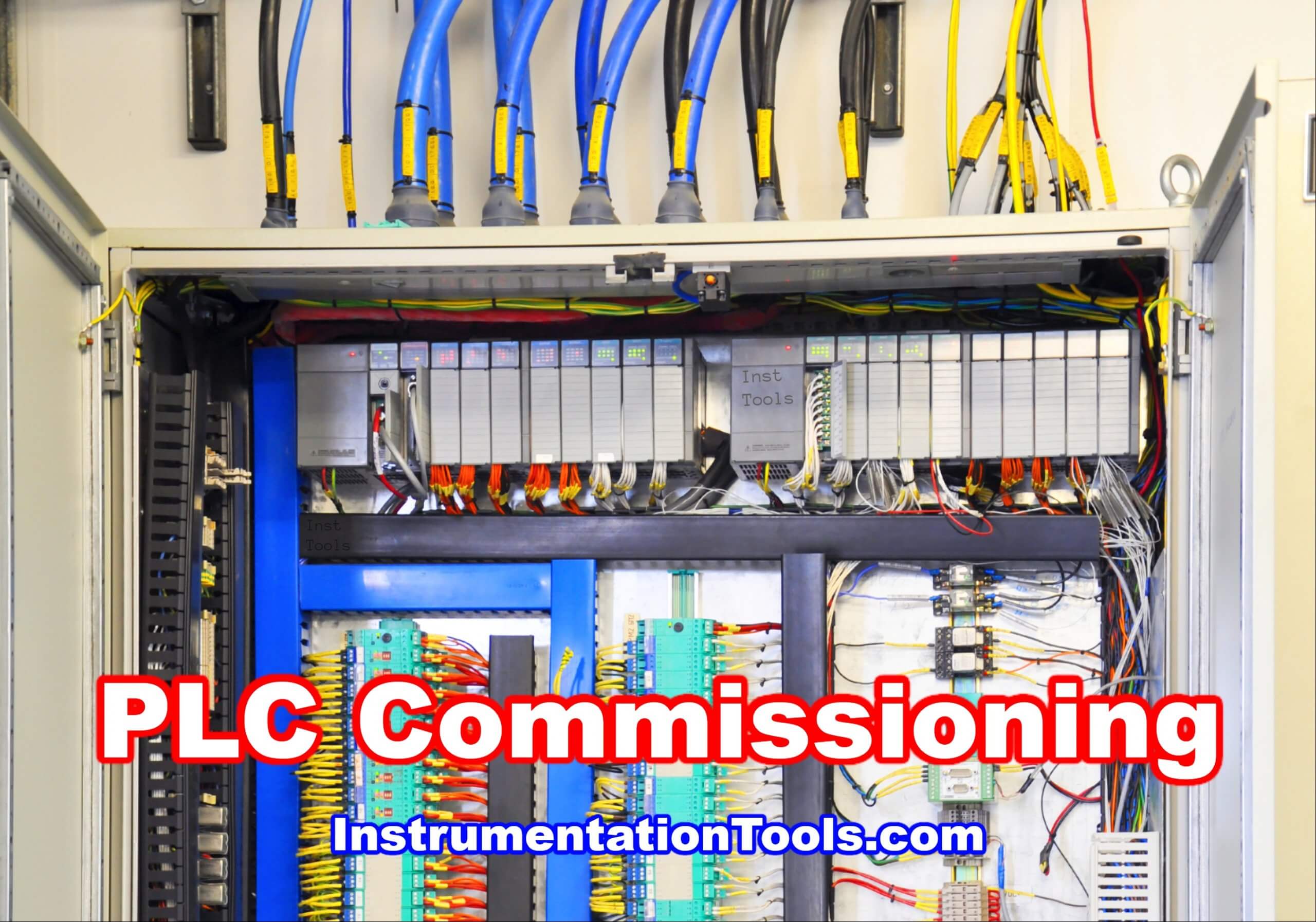
Let us have a look at the below steps.
Every PLC has its own software. You are given a PLC and just by starting it, you will not be able to identify what type of software to use.
So, when given a PLC, first check its software version and firmware version on the internet. When you get the latest one, download it to your PC / laptop and install it. The software will also by default install communication drivers along with it, or you will need to manually install it.
Once downloaded, install the software and its communication drivers. When the software is installed, you will be able to select the PLC model number that you have. If the model number is shown correctly, that means the software you have installed is correct.
Once confirmed, you have to start building your PLC program in it. Also, configure the hardware of PLC in the program inside.
After building, compile the program and check for any errors. The program will not be downloaded in PLC if there are compilation errors.
Now, you have to check the wiring of inputs, outputs, and communication ports.
Open the PLC hardware catalog for reference.
Determine whether the PLC inputs are sink or source;
PLC outputs are triac, transistor, or relay type, analog inputs are 4-20 mA or 0-10 V, and analog inputs are 4-20 mA or 0-10 V. Once confirmed, do the necessary wiring in the PLC.
Now that your program is ready and wiring has also been done, take the PLC and power it up according to the supply it requires.
Make sure you also provide proper earthing to the PLC panel.
After powering up, you have to connect the communication cable to it according to the medium you have set in the backup for downloading.
For example, you have set the medium as USB, connect a USB cable to it and see whether its driver is showing the proper name in the computer driver sheet or not. If it is not showing properly or not installed, then you have to reinstall the driver and look for any other updated driver on the internet and use it.
If your connection has been established successfully, go online in the PLC through it now.
First, download the latest firmware in the PLC. After the firmware has been downloaded, power reboot the PLC and then, download your final program in it.
After downloading, put the PLC in run mode.
Now that your PLC is loaded with the program, you now have to check the inputs, outputs, and communication ports.
According to the PLC wiring that you have done, check digital inputs first.
On giving the input, the corresponding PLC input address in the program must be turned on.
Then, check the digital outputs. According to the PLC output address that you have turned on, the physical PLC output must also turn on. When it is ON, check the output voltage across it.
Then, check the analog inputs. On giving the input, the corresponding PLC input address in the program must be shown analog counts accordingly.
Then, check the analog outputs. According to the PLC output address that you have given counts, the physical PLC output must also give the corresponding counts.
After the IO’s have been checked, check the communication ports configured in PLC. See whether they are communicating or not.
Now, check the program that you have developed and see whether it is functioning according to the IO’s configured. If done, your PLC is commissioned now.
In this way, we saw how to commission a PLC.
If you liked this article, then please subscribe to our YouTube Channel for Instrumentation, Electrical, PLC, and SCADA video tutorials.
You can also follow us on Facebook and Twitter to receive daily updates.
Read Next:
- Errors in Siemens PLC
- DCS Commissioning
- Learn SCADA System
- Electrical Wiring Diagram
- Yokogawa DCS Tutorials
Good