Instrumentation engineering root cause analysis (RCA) of wrecked electrical control panel instruments that threaten indefinite plant shutdown.
Article Type: | Root Cause Analysis (RCA) |
Category: | Instrumentation |
Equipment Type: | Transmitters |
Author: | S. Raghava Chari |
Note: This root cause analysis (RCA) is from real-time scenarios that happened in industries during the tenure of two or three decades ago. These articles will help you to improve your troubleshooting skills and knowledge.
Control Panel Instruments Problem
The pipe elbow burst problem discussed under Mechanical Problems wrecked the NH3 plant control panel instruments also entirely.
The general manager (GM) requested the author Instrument Engineer then to restore the instrumentation by hook or crook to under-platy the situation gravity and for morale-boosting.
Restoration details follow:
Panel instruments Restoration
The below-listed constraints made the task Difficult, Unattainable, and Despairing Problem (DDUDP).
- Potassium carbonate solution drenched and crusted all panel instruments
- No spares and manpower help from the panel and instruments supply and erection contractor
- Extensively damaged panel rear signal tube bundles
- And many more minor items
Yet the author and his team trusting in God and other teams’ whole-hearted cooperation started the job after a vigorous prayer and completed it.
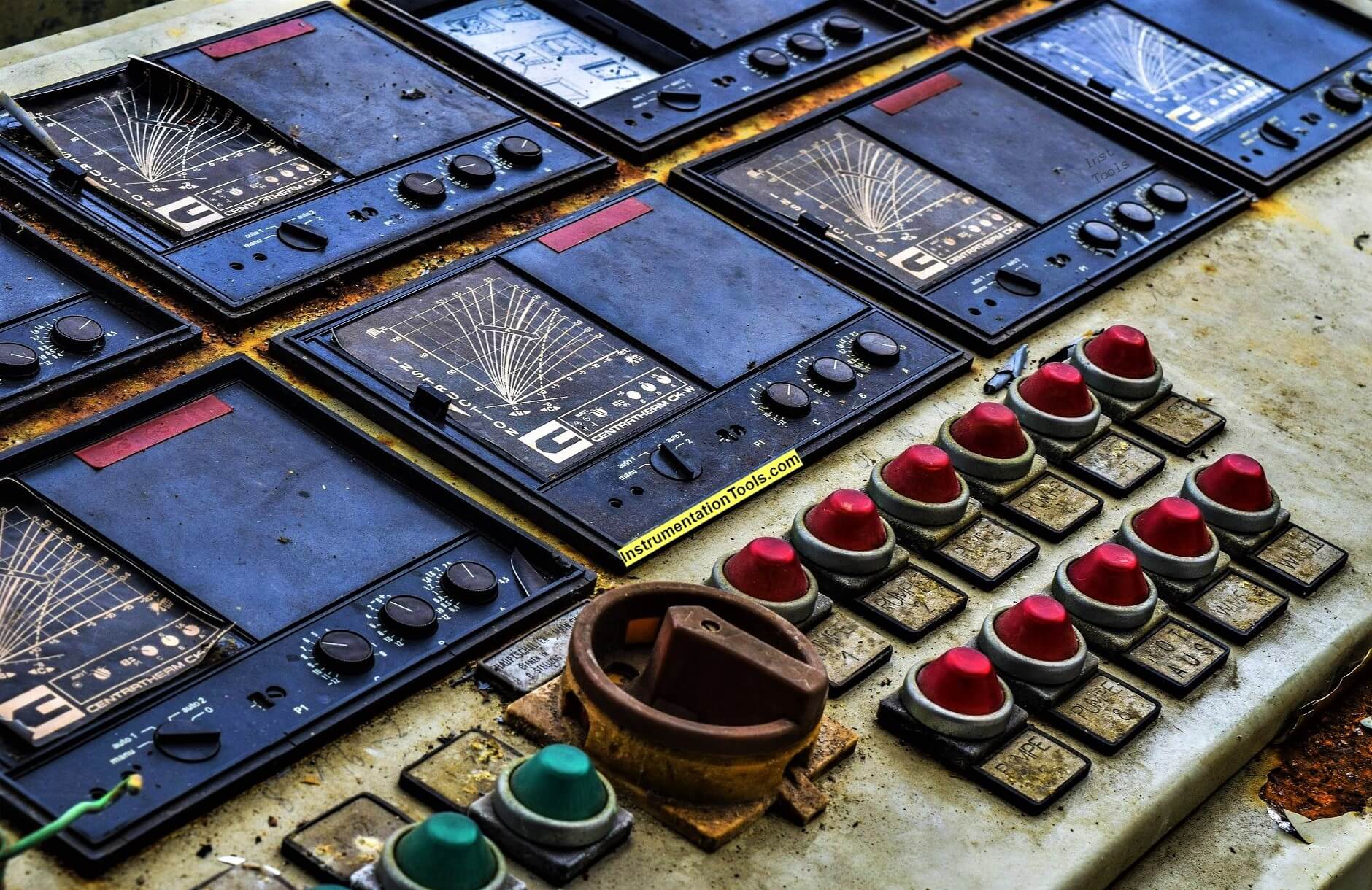
Description follows:
Panel Pneumatic Receivers Restoration
Panel Pneumatic Receivers Restoration proceeded thus:
- Crew took out the ‘chassis’ from ten random panel pneumatic receivers and one from undamaged urea plant panel receiver.
- All the 2-6 mm small bores interconnecting tubes were found melted. The crew pulled a set out of the urea plant good receiver chassis
- A purchase assistant and an instrument mechanic scouted the market and returned with tubes as closely matching the samples – first not feasible problem solved
- During this time plant crew detergent washed the ten soiled chassis and casings in a tub, water washed these in another and dried them in the 70oC set armature drying oven for 3 hours – trial found .
- Fortunately, the washed chassis and all components though discolored seemed functional
- The crew connected the components using the bought-out tubes.
- Lo & Behold! The receiver – chassis and casing assembly – calibrated fine.
- Fortunately, panel rear casing plugged controllers did not suffer much damage. Wet cloth wipe was enough to clean them
The assurance that all pneumatic receivers and controllers are restorable boosted the morale so high that they took other jobs too enthusiastically.
Panel Electronic Instruments Restoration
An instrument tech and an electrician took out all the panel electronic instruments – temperature recorders and selector switches – and sent them to a firm who helped us with electronic instrument problems.
Damaged Air Signal Tubes Restoration
While the pneumatic and electronic instruments restorations were progressing, the author formed an Instrument Technician and an operator, an Electrician, and an operator team.
The operator closed all field transmitters and valve positioners’ air supplies. He opened e.g. PT 101 air supply.
The instrument technician in the control room would immerse the damaged tube ends in a beaker of water one by one, identified, and tagged as PT 101 the tube that bubbles.
The operator – Electrician team identified and tagged the from the receiver PRESSURE 101 damaged tube end likewise. This laborious process was necessary, as the site assembled tube bundle had no individual tubes identifying number.
They araldite coated the identified tube ends and inserted in a tight-fitting PVC tube for reliable and pull out free joints. Then they confirmed PT 101 connects to PRESSURE 101.
The twine-tied the jointed tubes and wrapped 25 mm wide tightly gripping electrical insulation tape to prevent mechanical damages. Thus, the damaged air signal tubes bundles were ready in 8‑days.
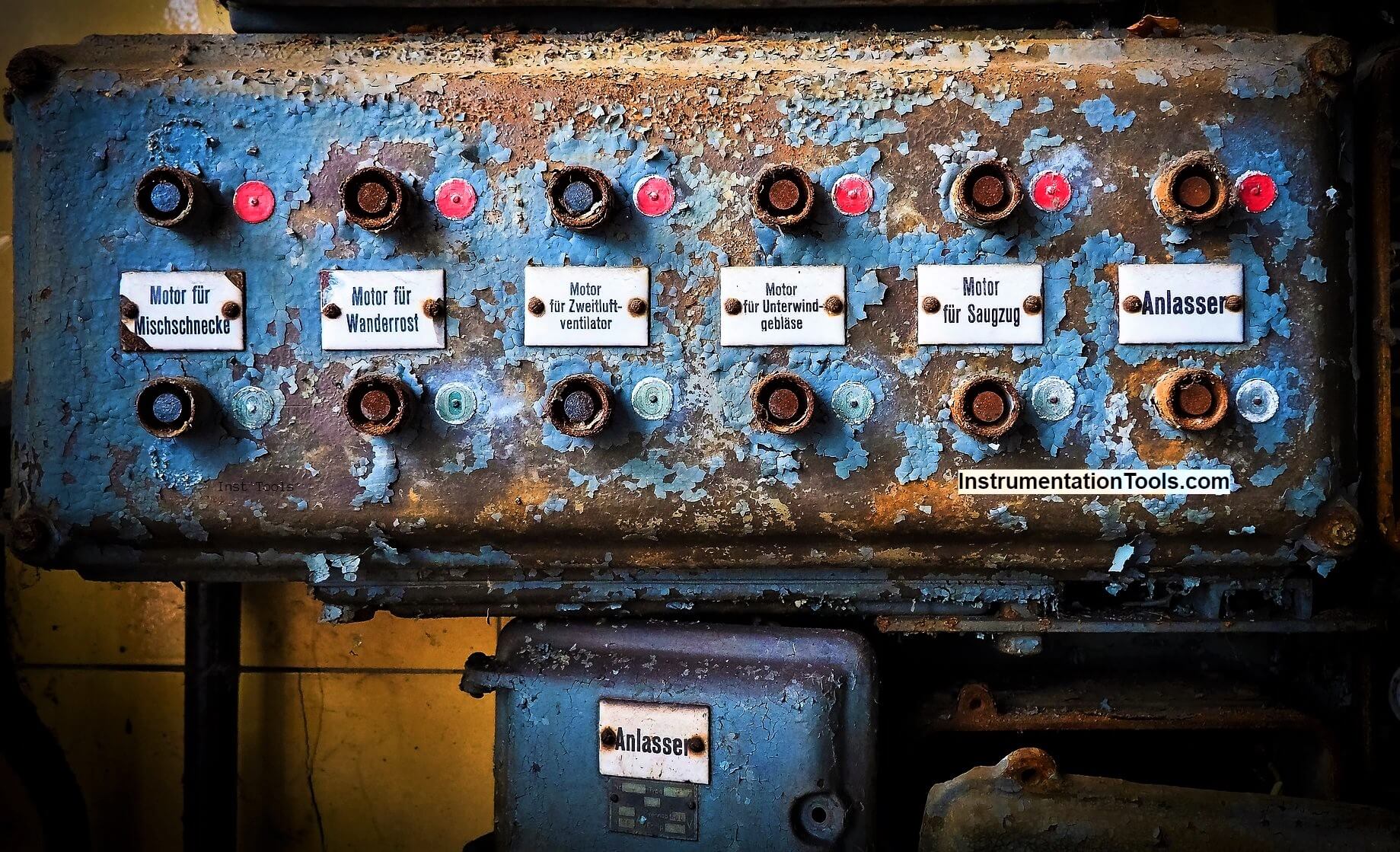
Trip Panels Restoration
Two nos. two electricians team crew removed the terminals wires connections preserving their original geometry, from the home wired contactor trip panels, took those out, water washed, oven-dried, discarded the existing contactors, positioned new bought out contactors, and connected the wires.
The trip panels were ready in two days.
Electronics Instruments Restoration
The electronics expert delivered the electronic temperature recorders, indicators, and selector switches in 8 days. He declined to share his special know-how!
Faced Constraints overcome
Faced Constraints and overcoming details follow:
- Hot K2CO3 distorted receiver panel doors: The instruments manufacturing licensee declared only his principal could supply the plastic doors and delivery time 6 M. As the reasonably clean room housed panel instruments can stand it, the author postponed the job
- Receiver Pens: The licensee said the same for pens too. The author got these made by the electrical section cable jointer nick named pen maker (PM) thus:
Make red pen bucket duplicating a store held spare; the PM folded 0.3 mm thick brass sheet as a rectangular bucket as the original and soldered the seams.
He recovered the tubes only from the bought-out syringes discarding the rest, bent like the original, and soldered to the bucket.
In addition, soldered cut portions from discarded steel measuring tapes as pen holders for inserting into receiver arm socket. The red pen is ready.
Likewise, he made green and blue pens also. Required quantities all types of pens were ready in two days
Panel Painting and Control Room face-lifting
- A very cooperative painter from the painting contractor detergent solution mopped the instruments taken out portions followed by water mop and dried the portions using a hair dryer, easy emery cleaned and sprayed two paint coats. Similarly, he painted the panel rear too
- Another contactor rough emery cleaned the brick walls and distemper painted
- Another contractor installed steel panes in place of the glass panes. He pre-fitted from automobile windshields cut shatter‑proof 150×150 viewing windows on the steel panels.
The plant took these face-lift steps to prevent past gruesome incident reminders and assuring maximum possible safety.
The DDUDP instrumentation restoration was ready in a record 10-days. The plant started with a puja and prasad distribution smoothly.
The share-holding US partner sent the former US citizen General Manager to make sure of necessary plant changes to prevent the accident recurrence. He remarked, “Chari, you and your team have re-built a truck run-over egg; hats off to you and your team.”
Author: S. Raghava Chari
Do you face any similar issues? Share with us through the below comments section.
If you liked this article, then please subscribe to our YouTube Channel for Instrumentation, Electrical, PLC, and SCADA video tutorials.
You can also follow us on Facebook and Twitter to receive daily updates.
Read Next:
- Actuator Diaphragm Bursts
- Control Valves Leak Tightness
- Over-Capacity Control Valve
- Control Valve Gland Leaks
- Transmitter Pressure Correction