Electrical engineering root cause analysis (RCA) related to Critical High KW motor winding burnout threats.
Article Type: | Root Cause Analysis (RCA) |
Category: | Electrical |
Equipment Type: | Motors |
Author: | S. Raghava Chari |
Note: This root cause analysis (RCA) is from real-time scenarios that happened in industries during the tenure of two or three decades ago. These articles will help you to improve your troubleshooting skills and knowledge.
Motor Winding Burnout Problem
A 2500 3.3. KV 300 RPM Motor coupled compressor feeds the entire urea production CO2 feed. Its winding temperature was 112oC (Max rated 115o C; trip 120o C).
It threatened reduced motor lives, even sudden burnouts and entire complex long shutdown during the long repair and difficult re-installation.
The plant lived with these 10-yearlong threats!
Author Root Cause Analysis
He noted the following from the motor cooling system study:
- Shaft driven fan circulates mostly the motor casing contained bottled air to cool the rotor and stator windings to the expected 80 deg C.
- Motor casing inside mounted 5 pass finned tubes heat exchanger’s tube circuit 34 deg C water flow cools the hot air.
- Bottled air + negligible ambient air circulation minimizes the contaminated ambient airflow into the motor and motor internals deterioration.
Technical service engineers repeatedly confirmed heat exchanger adequacy and electricians the brushed tubes’ bores and fins cleanliness.Â
Why winding temperature is high then?
The author instructed the crew to call him day or night at the next before heat exchanger cleaning. He adjourned a routine meeting and personally inspected the to-clean exchanger.
Factory shine three passes brass tubes’ bores surprised him! Concluding no water flows in those and in effect, 40% heat transfer area only functioning as the 10-yearlong problem’s root cause was easy!
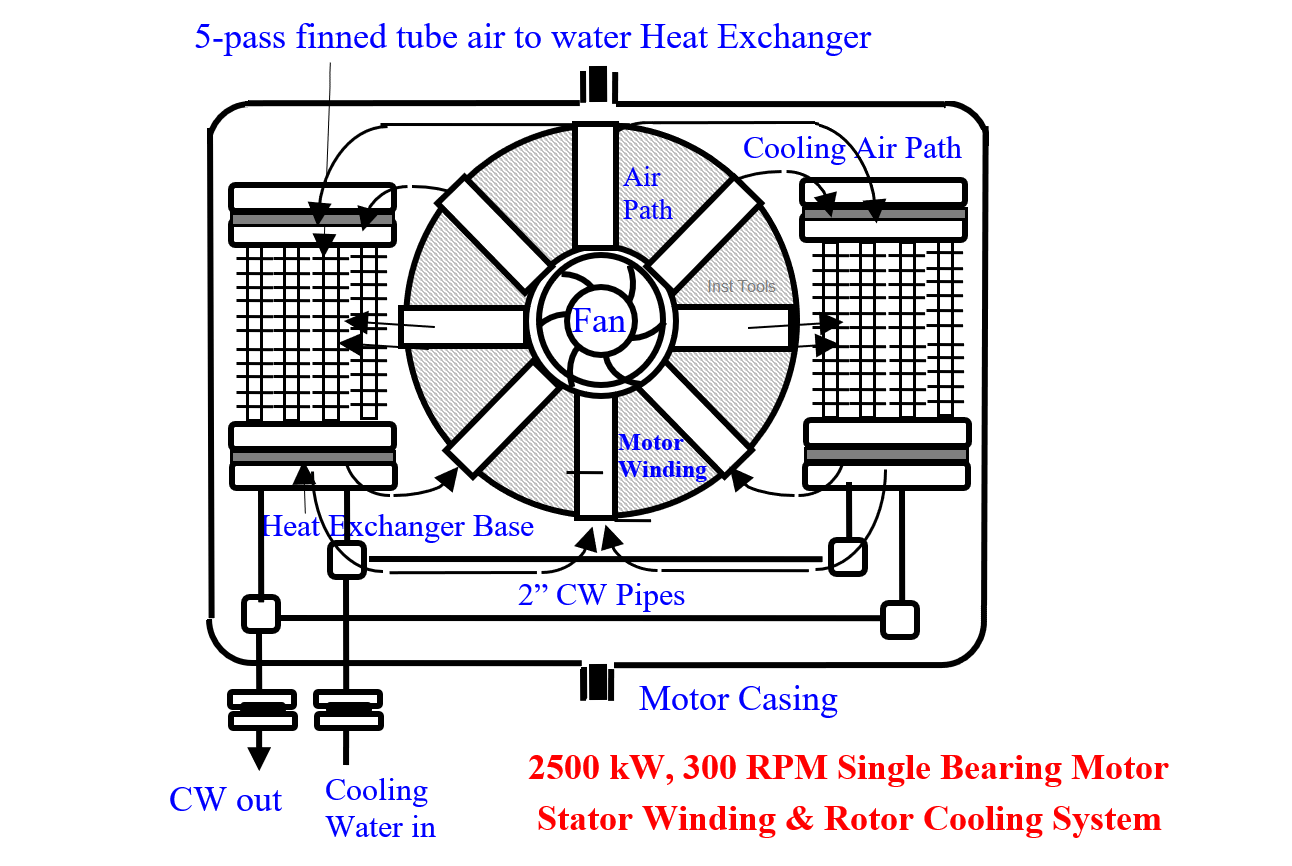
Answer to the RC query ‘why’ was, since the problem started day 1, probably the rectangular exchanger bolted with its side AB coinciding with the base’s side DC i.e., 180o mechanical out of phase!
The crew who dutifully match marked, removed the heat exchanger out of the motor body, cleaned the heat exchanger, and assembled it back exactly as it was.
Hence, the 10-year long persisting problem! The author-guided crew installed the exchanger correctly and dowelled it to avoid repeat mistakes.
The tech services engineers assigned to solve this problem felt sheepish for missing the important clue that identified the root cause.
RCA Solution Benefits
Even peak summer months <Â 800C winding temperatures pleasantly surprised everyone, freed all from the above-described anxieties and threats.
The Plant confidently produced 110% rated capacities urea even in summer. The past summers’ lower than rated capacities urea production vanished.
Author: S. Raghava Chari
Do you face any similar issues? Share with us through the below comments section.
If you liked this article, then please subscribe to our YouTube Channel for Instrumentation, Electrical, PLC, and SCADA video tutorials.
You can also follow us on Facebook and Twitter to receive daily updates.
Read Next:
- Problems with Switchgears
- Transformer Problem Solved
- Aluminum Cable Terminations
- Arc Fault Breaker Problem Solved
- Hardware Troubleshooting for PLC