Instrumentation engineering root cause analysis of mechanical temperature indicators (MTI) problems and solutions.
Article Type: | Root Cause Analysis (RCA) |
Category: | Instrumentation |
Equipment Type: | Sensors |
Author: | S. Raghava Chari |
Note: This root cause analysis (RCA) is from real-time scenarios that happened in industries during the tenure of two or three decades ago. These articles will help you to improve your troubleshooting skills and knowledge.
Mechanical Temperature Indicators (MTI) Problem
Mechanical Temperature Indicators (MTIs) – filled system, bi-metallic, capillary type, etc. posed the below-listed problems:
- Generally short lives; even few days only in vibrating reciprocating compressor piping
- Repair difficulties
- Calibration difficulties; need for heating systems, oil baths, reference thermometers etc. All are cumbersome to handle, even unsafe and results are often unsatisfactory Local readings only,
- Consequently possibilities of faked readings to avoid walking long distances, climbs to different elevations and descends
- Recurring high costs
- In fact the problems were so severe that one day the plant supdt threatened shutting down the plant as machines nearly 70% defective MTIsÂ
Relenting to the author’s appeal he did not shutdown the plant giving two days to resolve the issue. Nightlong thinking showed a way out.
The author gave the operators a trolley-mounted rush-bought moving coil temperature indicator connected to high temp insulation Iron Constantan extension lead (EL). He crimp jointed the wire’s other end.
He named it Extension Lead Thermocouple (ELTC). Operators inserted the ELTC in each TW and read the temperatures. This temperature arrangement mollified the plant superintendent temporarily.
Author Final solution
Seeing the satisfied operators, the author decided discarding all MTIs and to provide Thermocouples connected via selector switch Potentiometric Temperature Indicator for all temperature measurements.
He called these Temperature Monitoring Stations (TMS fig 2). Two below given constraints threatened the implementation:
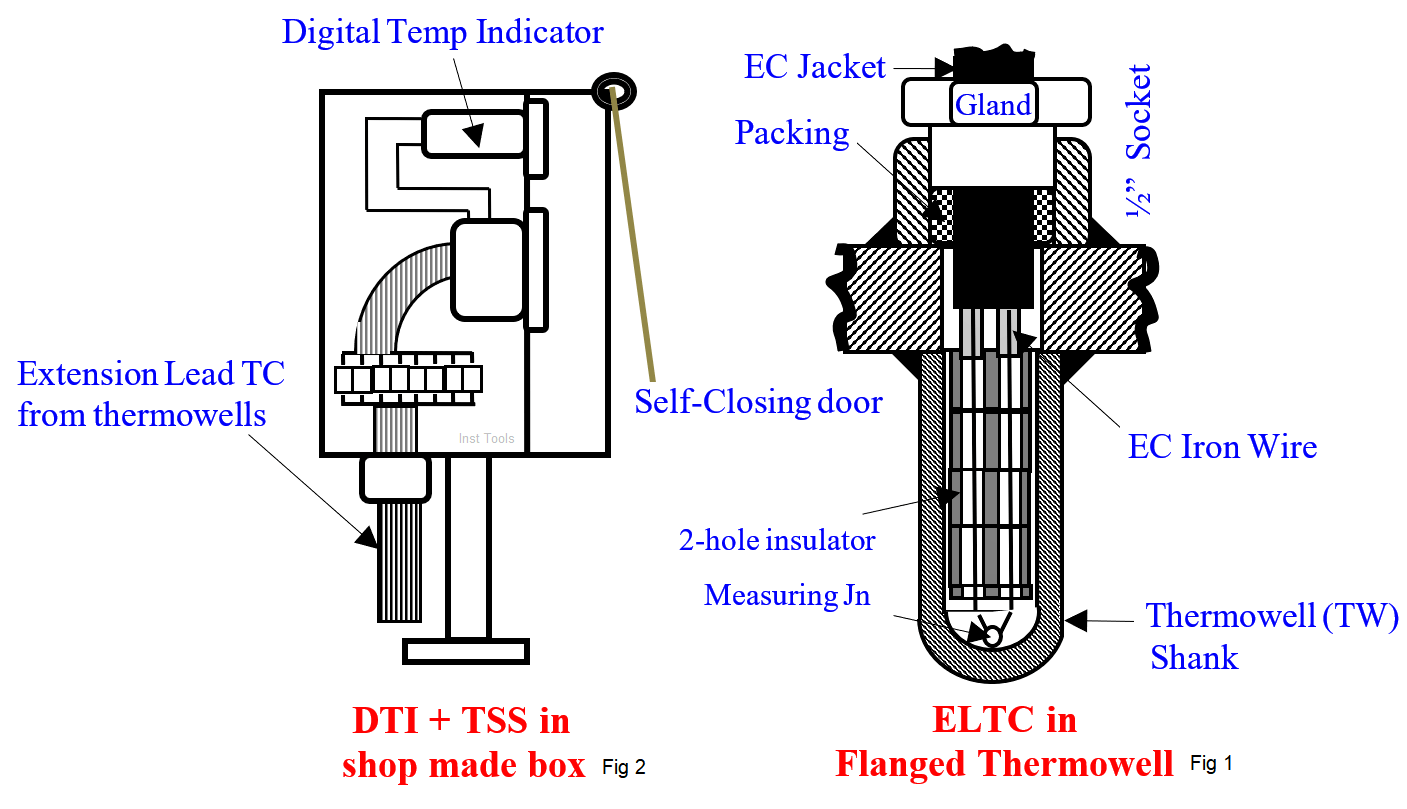
Constraint 1
Thermocouple (TC) Selector Switches (TSs) > 6 months delivery; The author resolved this thus: He rush-procured 2‑pole 2-throw telephone switches in 15 days.
The shop made the pedestal-mounted box as per his sketch within the time, Instrument crew under his guidance assembled and wired the telephone switches in a week. Thus constraint 1 vanished
Constraint 2
Thermocouple Assemblies long delivery times:Â The author resolved this thus: He developed a homemade Extension Lead Thermocouple (ELTC).
Instrument crew made these thus:
- Run single pair EL from each thermowell (TW) to the TMS box installed TS on existing cable trays or on new ones where necessary
- Strip each core PVC insulation to suit the immersion length (IL)
- Pass the bare wires through two‑hole insulators (fig 1)
- Make the MJ thus: insert the wire ends in a brass eyelet and crimp with a crimping tool. ELTC is ready
- Insert the MJ end ELTC – author given nomenclature – into the TW via grommet into the TW (fig 1)  Â
- Connect the ELTC free end to the TMS terminal strip
- Connect TS to terminal strip with EL wires
- Connect TS output to the TI terminals
CO2 and NH3 piston compressors’ TMSs were in service within 3 weeks of the project concept.
Impressed by the TMS offered convenience, uninterrupted availabilities, and savings all plant superintendents clamored for it.
The author and the instrument crew met the challenge and pleased all by commissioning the 9 more strategically located TMSs.
Extension Lead Thermocouple Advantages
Extension Lead Thermocouples (ELTCs) advantages are:Â
- Enabled immediate project completion soonest despite several constraints and prevented long plant shutdowns
- 100% reliable and 100% available TMSs enabled reliable, safe and uninterrupted plant runs
- Operators thanked the author for saved long distance walks, multiple steps ascends and descends to log temperature readings
- Saves recurring yearly over Rs 2 million expenditure on MTIs
- Lot cheaper ELTCs than purchased thermocouple assemblies using the non-moving and non-salable surplus stock EL makes the project cost almost zero.
- Prevents wrong extension lead connections at the head and thus loose connections and wrong connection reverse polarity problems pain in the neck problems
- The author replaced the somewhat maintenance prone 70s installed potentiometric temp indicators with near equal cost but high readability and no moving parts and hence no maintenance Digital Temperature Indicators that became indigenously available in the 75s.
Benefits Realized
Benefits Realized are:
- Vanished MTI posed production limiting and expensive nuisances
- Never failing, no maintenance requiring reliable temperature indications smoothed the operations and improved product qualities
- Vanished arguments on parallax error read different readings.
Author: S. Raghava Chari
Do you face any similar issues? Share with us through the below comments section.
If you liked this article, then please subscribe to our YouTube Channel for Instrumentation, Electrical, PLC, and SCADA video tutorials.
You can also follow us on Facebook and Twitter to receive daily updates.
Read Next:
- Actuator Diaphragm Bursts
- Control Valves Leak Tightness
- Thermocouple Extension Leads
- Control Valve Gland Leaks
- Pitot-tube Replaced with Orifice