Today in this article we will discuss the root cause analysis for a differential pressure level transmitter that was installed to measure the level of a tank filled with water.
The DP type level transmitter started showing less value after the preventive maintenance job.
Differential Pressure Level Transmitter Problem Statement
A dry leg DP type level transmitter was installed in a tank that stores water. One leg of the transmitter i.e. high-pressure side is connected to the tank bottom while the other leg i.e. low-pressure side is connected to the top of the tank.
The LP side is dry leg type. The connection is from the top of the tank because the tank receives the water and then supplies the water as per the process need.
Due to this, the tank undergoes pressure change and hence LP side of the transmitter is connected to the top of the tank for reference pressure purposes.
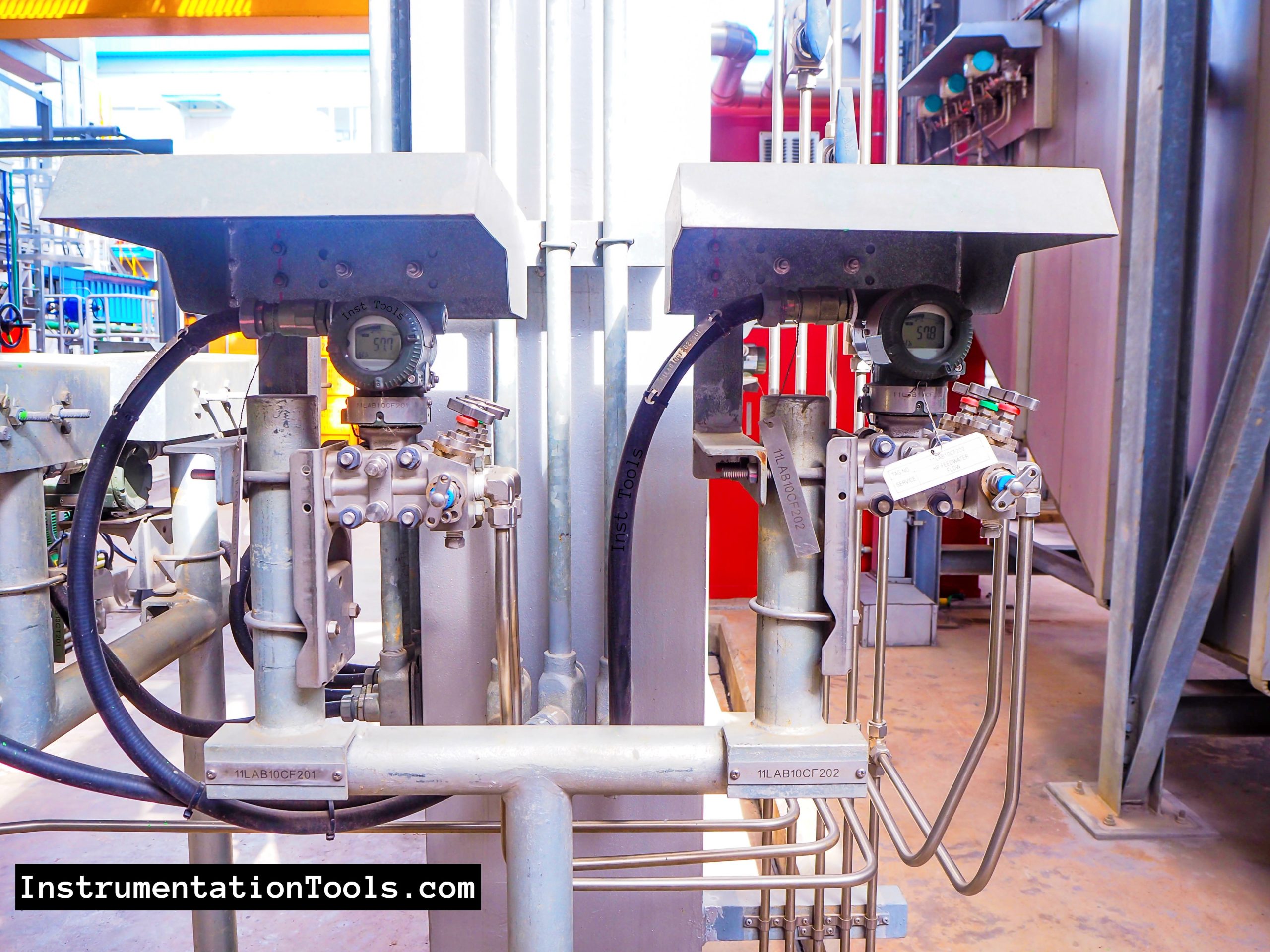
Preventive maintenance was taken for the DP type level transmitter. The level reading before the job was 92 %. The level transmitter was working perfectly. During the preventive maintenance job, the level transmitter was isolated.
The response of the level transmitter was checked. Then after the flushing job, the level transmitter was taken in line. After the preventive maintenance job, the level transmitter was showing 70 % level only. While in the level gauge, the level was 93 %.
So, on a doubt basis of the level gauge, the level gauge was taken for the maintenance job. But still, after completion of the maintenance job on the level gauge, the level was the same i.e. 93 %. But still level transmitter was showing 70 %. After the maintenance job on the level transmitter, the level transmitter was showing a 93 % level.
So what can be the probable reason for water coming out of the LP side of the level transmitter after the Preventive maintenance job?
Root Cause Analysis of Level Transmitter
Probable Problem 1: Actual level was 70 % and after the preventive maintenance job, the level transmitter started showing an ok value.
While confirming the reading with the level gauge, the level was found 93 %. Also, the level gauge was checked and found ok. So this possibility was ruled out.
Probable Problem 2: The level transmitter became faulty
During the preventive maintenance job, the level transmitter’s response was checked. The response of the level transmitter was ok.
Probable Problem 3: Problem in the root valve opening
Both the root valves were found open during checking after the problem was encountered. Both the root valves were found open.
Probable Problem 4: Issue in manifold
Manifold checked after the problem was encountered. Both the isolation valves, vent valves, and equalization valve were found in ok condition.
Probable Problem 5: Leakage in the impulse tubing of the level transmitter
Leakage was checked after the problem was encountered. No leakage was found.
Observations
Observations after taking level transmitter for maintenance job again:
- The actual level was the same.
- Level transmitter’s response checked. Found ok.
- Level transmitter’s both root valves checked. Found ok.
- Level transmitter’s manifold valve’s condition checked. Found ok.
- The level transmitter’s tube was checked for any leakages. Found no leakage.
- While opening the LP side vent plug, found water coming out of the LP leg. LP side flushed and taken inline. Level transmitter started showing 93%.
What went wrong?
As per the technician who did the job, the following activities were done. During the level transmitter preventive maintenance job, the level transmitter was isolated from the root valves.
Then the level transmitter’s response was checked using the pressure calibrator. The response was found ok. Both HP leg and LP leg were flushed and then the transmitter was taken inline.
But while filling the preventive maintenance checklist, the technician observed that he missed zero checking procedures. So he opened the equalization valve and then closed the isolation valves from the manifold.
So in this process, the water from the HP side went to the LP side. After checking zero which was found ok. Then transmitter was taken inline. Now due to the water on the LP side, the level transmitter started showing low values.
If you liked this article, then please subscribe to our YouTube Channel for Instrumentation, Electrical, PLC, and SCADA video tutorials.
You can also follow us on Facebook and Twitter to receive daily updates.
Read Next:
- Level Indicators Working Principle
- Transparent & Reflex Level Gauge
- Calculate Current 4-20 mA
- Level Gauge Design
- Types of Level Gauges
We are always facing this issue with DP type level transmitter. We flushed the high level inclined ss line so we get level proper. is there any other solution.