Today in this article we will have a look at some most commonly used technologies i.e. PLC, DCS, RTU, SCADA, and PAC which often create confusion in our minds when we want to differentiate between them.
PLC
PLC stands for Programmable Logic Controller. PLC is mainly used for performing certain functions or in other way we can say that we use a single PLC to run small to medium-sized plants. PLC has its own controller, input-output cards, and communication cards to communicate with other systems.
PLCs are used to control plants or units like compressors, nitrogen generation units, hydrogen generation units, desalination units, and other units having limited input and output which requires controlling with a high scan rate (near 100 milliseconds).
One should also note that Safety PLC is also available in the market and used in plants for taking action very quickly (10 to 100 milliseconds) and running plants smoothly. Other protection/control systems like Bentley Nevada Machine Condition Monitoring System, Woodward control system, and many more are used with PLC for achieving the desired purpose of running a compressor or other equipment.
So, in a simple language, PLC will have a program written in its processor, which will keep communicating/controlling with the inputs and outputs connected to the input and output cards and thus keep the plant running as per the logic written in the controller.
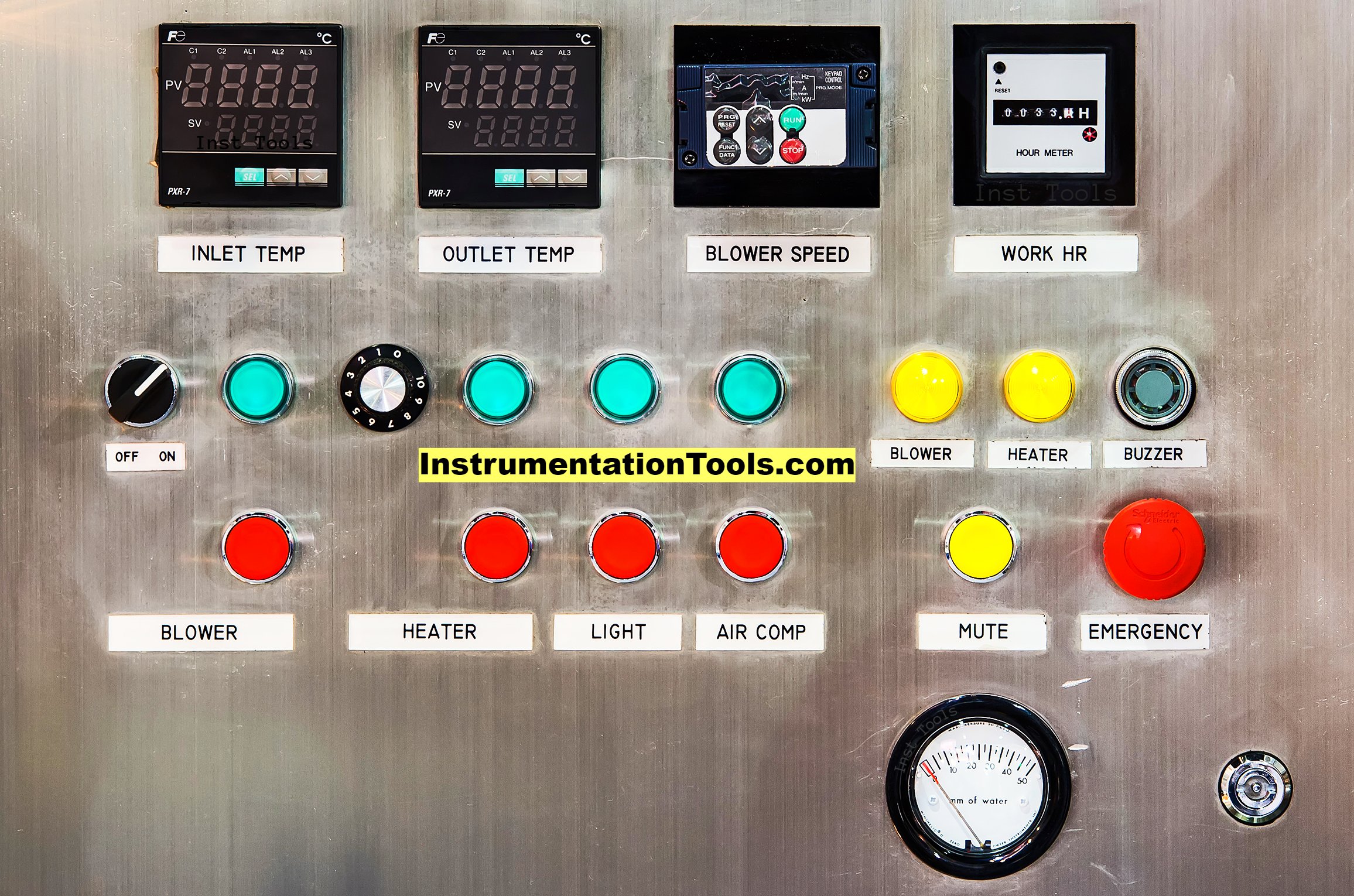
DCS
DCS stands for Distributed Control System. DCS is generally used for plants having a large number of inputs and outputs. The controlling is done by various controllers which are controlling different processes or different parts of plants.
The scan cycle of DCS is also a bit more than PLC. The typical scan cycle of DCS varies between 100 milliseconds to 2 seconds depending upon the program complexity and number of inputs and outputs.
To understand DCS, we can take an example of the plant where 4 air compressor and 2 nitrogen generation unit is running through PLC (each compressor has its own PLC, and both nitrogen generation unit have their own PLC). Now these PLCs will only control respective units. Here, generally, we use DCS to control the distribution of the air and nitrogen. Various input and output devices to control the distribution are connected and controlled by DCS.
PLC and DCS also keep communicating for the smooth functioning of the plant. Other applications of DCS are controlling small pumps and small non-critical processes. The advantage of DCS is that input output can be added easily in DCS and in many DCS, these changes can be downloaded without stopping the current process. In the case of PLC, the PLC needs to be stopped and then only we can download the program.
RTU
RTU stands for Remote Terminal Unit. RTU is also a kind of controller that helps to manage processes located at very far distances. The RTU then sends data to connected systems like DCS or SCADA which can be at large distances.
From the name itself, it is clear that RTU is used in remote conditions and hence RTUs are more rugged than PLC and can easily be used in harsh environmental conditions.
RTUs generally are used in applications like pipelines for the transfer of materials, electrical systems, and many such systems having input-output devices at large distances. RTUs also have a very simple program that controls the outputs.
SCADA
SCADA stands for Supervisor Control and Data Acquisition. The SCADA’s basic function is to collect real-time data on the processes, maintain history, generate specific reports, and generate alarms as per configuration.
SCADA works in conjunction with PLC and/or RTU. Through the use of SCADA, the operators can control the plant. The command given through the SCADA is passed on to connected systems like PLC or RTU.
Now you might think what is the difference between the SCADA and DCS then? The answer is simple, the SCADA system doesn’t have its own controller which a DCS has. SCADA only communicates with systems like PLC and RTU and helps the operator to do needed operations by giving commands to PLC and/or RTU.
On the other hand, the DCS is a stand-alone system that can control a plant, maintain history, and generate alarms and reports. Typical applications of SCADA are water treatment plants, and pipeline systems for transfer of material.
PAC
PAC stands for Programmable Automation Controller. PAC is also a kind of PLC but with much greater abilities. PAC generally has a greater memory and more number of input outputs than PLC.
PAC also has a facility to communicate with databases, OLE, and ethernet which makes it very convenient for the end user to maximize its usage. PAC systems can also be programmed with C and C++.
In simple language, PACs are a kind of higher version of PLC having more capabilities. PACs are used in large plants having a high number of inputs and outputs along with a good scan rate.
If you liked this article, then please subscribe to our YouTube Channel for Instrumentation, Electrical, PLC, and SCADA video tutorials.
You can also follow us on Facebook and Twitter to receive daily updates.
Read Next:
- PID_PWM and PID_Output Controllers
- Difference Between PNP and NPN Sensor
- Light Tower in Industrial Automation
- Micro Electro-Mechanical Systems (MEMS)
- Programming and Tuning PID Controller