In this post, we will learn why 24V DC supply is used in all major industrial automation and control systems.
We have seen that a majority of sensors, instruments, and other control devices use a 24V DC power supply. Times have also advanced nowadays in such a way that some motors use 24V DC for energizing.
Why 24 Volts DC Power Supply?
What is it that DC supply is preferred over AC supply is powering the instruments?
We will have a look at some of the general advantages of DC supply and try to correlate it with AC supply.
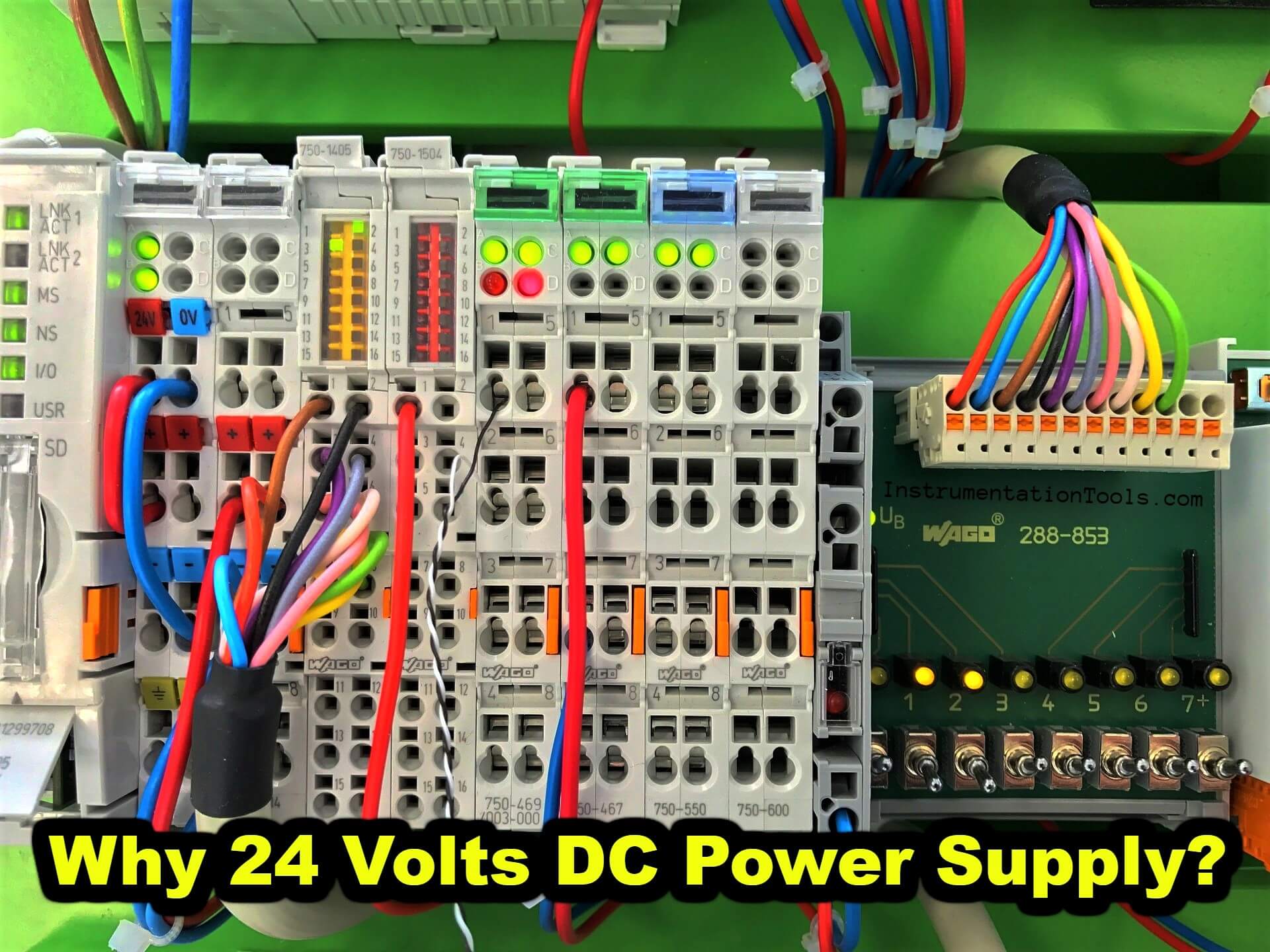
One main advantage of a 24V DC supply is less arc generation. AC supply of 120V or 230V is highly risky considering that it produces a good amount of electric sparks and arc; which can be dangerous for surrounding personnel or the environment.
This risk factor is very less in 24V DC supply as it produces less or even sometimes the negligible amount of arc and electric spark. Also, due to such a low voltage, there are hardly any chances of a person getting an electric shock when touching it.
The current carrying capacity of DC supply is limited. This does not mean that it cannot drive an instrument. The current is enough for it to power the device and when a short circuit occurs, it simply cuts off the supply to the instrument due to its limitation.
Though this may sound like fuses are not required for DC supply then, it is used in many applications depending on the requirement of the user; for additional protection to the device.
Otherwise, a fuse is not required for DC supply as compared to AC supply, where a fuse is required in general for protection to the device.
Due to the general behavior pattern of DC supply, it is possible to reduce the size of the instrument or power supply. This reduces the cost and complexity to a great extent.
Bulky and oversized devices employing AC supply are not easy to handle and occupy a large space.
Heat dissipation is also more in such devices and nowadays, in times where semiconductors function at nano-size levels, reduced DC supply size is also helpful in increasing the reliability, decreasing the cost, and increasing the efficiency of the instrument.
If you see the output of DC voltage as compared to AC voltage, it is much constant and less prone to fluctuations. This makes the instruments get fixed voltage at a much higher percentage rate and if fluctuations are less, then the performance will too be higher. A higher rate of fluctuations or short spikes in voltage at the upper level can damage the circuitry.
In a 24V DC supply, the instruments can drive 500-600 ohms of load resistance, which is enough for even a valve positioner; which is heavy in operation. So, the load-carrying capacity of DC supply is also on par with AC supply.
DC supply is more noise redundant as compared to AC supply.
UPS or batteries use a DC power supply as electricity can be stored in a DC supply.
Disadvantages of 24 volts DC Supply
Although DC supply has many advantages, it has some demerits too.
Let us have a look at some of them.
- One main disadvantage of DC supply is that it cannot be used for longer distances. There is reduction in signal capacity at long distances.
- 24V DC supply cannot be used to drive high current loads.
These are the general demerits of a 24 Volts DC power supply; but overall, it is best suitable for most of the instruments and devices as compared to 230V AC supply.
If you liked this article, then please subscribe to our YouTube Channel for Electrical, Electronics, Instrumentation, PLC, and SCADA video tutorials.
You can also follow us on Facebook and Twitter to receive daily updates.
Read Next:
- Why 24 Volts DC Power Supply?
- Factory Acceptance Test of PLC
- Control Two Motors in Sequence
- MODBUS Communication Protocol
- High-end Programmable Logic Controller