Calibration of Measuring Instruments – Significance, Costs & Risks for Your Business.
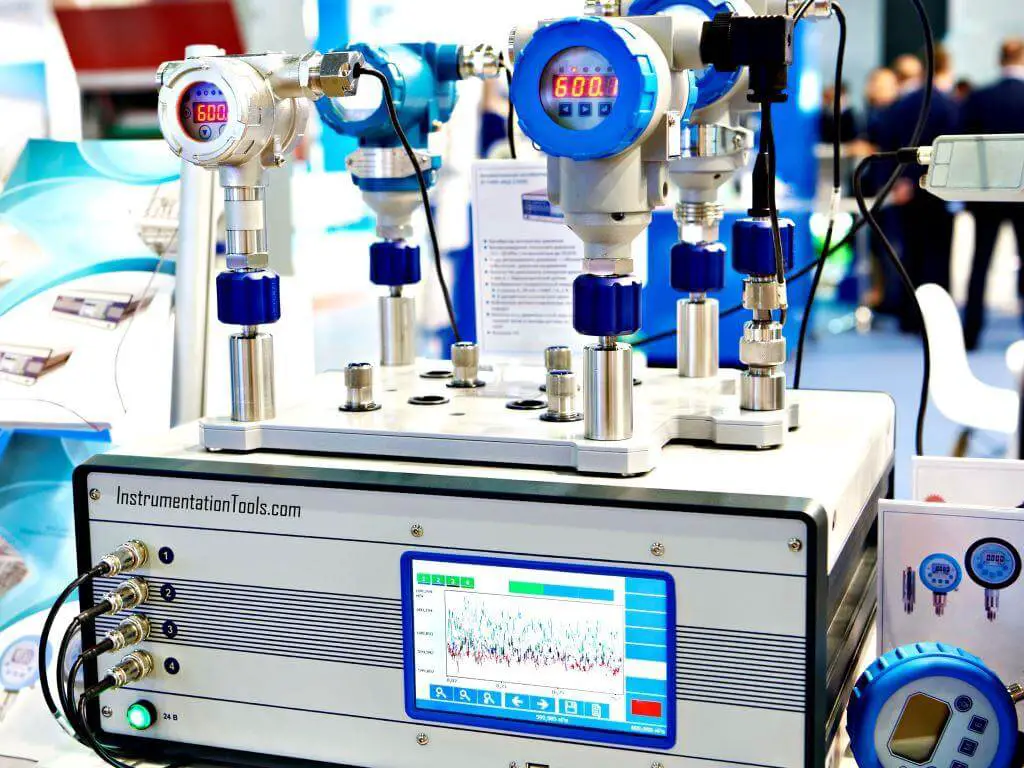
Calibration is a comparison of two instruments against each other, one being the standard (the calibrator). This process is essential to document the error of the instrument being calibrated and to increase its accuracy.
All instruments have errors and decreasing accuracies after a certain amount of time. Calibration helps address these issues.
Why should you Calibrate your Instruments?
The biggest reason behind performing periodic calibration of instruments is to test and ensure that they make correct and accurate measurements.
Regular calibration establishes efficient instrument performance, safety during operations, long term sustainability, and high instrument quality.
Timely action against drift
All electric and electronic instruments drift over time with continuous usage. Environmental conditions such as extreme temperature fluctuations, changing weather, excess or lack of humidity can affect an instrument’s drift too. In most instruments, greater usage means greater drift.
In instruments requiring extreme accuracy and precision, drift can be highly critical. Drift beyond the specified tolerance also poses a safety hazard. To avoid these inaccuracies, it is important to perform periodic instrument calibration.
Calibration helps identify the amount of drift, which helps analyze instrument stability and measurement consistency.
Early detection of defects & damage
Apart from drift, instruments are also prone to damage and defects due to loose connections or faulty components. This damage can be detected at an earlier stage with the help of calibration, and a total breakdown of the instrument can be safely prevented.
Once the defects are identified, the error propagation can be minimized, reducing costs and resources of handling serious damages.
Proactive Safety
In industries such as oil and gas, petrochemical, chemical, energy, power, electric, and electronic, there is a high risk of explosions, fires, and leakages. The measurement equipment used in these industries must be calibrated regularly and properly to avoid safety hazards and ensure employee safety and infrastructure safety.
In other industries such as pharmaceutical, food, and beverage, the calibration of instruments is necessary for consumer/customer safety.
Reputation of Quality
Calibration is also important for social corporate responsibility, environmental and financial reasons. Most companies and their customers have a quality system that needs to be adhered to. Governments and regulatory bodies also lay down conditions that need to be met to certify the company’s quality system, such as emission monitoring and equipment testing.
Measurement instruments used for these purposes should be highly accurate which is why they need to be calibrated from time to time using calibration techniques and equipment accredited to relevant ISO standards.
Labs and test equipment companies that adhere to updated standards like ISO/IEC17025:2017 establish their competence in quality management, improved lab testing environments, better customer satisfaction, an international reputation, & systematic processes.
What are the Costs and Risks of not Calibrating your Instruments?
While calibration may seem like an additional cost, it must not be neglected. Calibration has long-term benefits. Not calibrating your instruments regularly can lead to undesirable results, including:
False passes or failures
- The manufacturing industry often faces the issue of false passes or false failures. False passes may result in inferior and low-quality products being manufactured and sold, reducing the credibility of the production factory.
- False failures unnecessarily increase the manufacturing or reworking costs and may end up discarding high quality and fully functioning products.
Inaccuracies or errors in measurement
- A lot of electric and electronic industries and laboratories require high precision measurements with very small acceptable errors.
- Not calibrating your measurement instruments can leave these errors unnoticed and unattended, and can distort your final measurements and give highly inaccurate results.
- Errors in measurements can deviate the final output from the globally agreed standards. This means the entire process of testing and measurement will need to be repeated with new or repaired measurement instruments, making the process both time-consuming and expensive.
Penalties
- Regulatory bodies and agencies establish certain standards, guidelines, and regulations for instrument calibration. Not complying with these regulations can result in fines or penalties, seizure of the company’s license, and shutting down the business or plant.
Safety Hazards
- Failure to calibrate or incorrect calibration of instruments can pose significant risks to both the employees and the plant.
- Unidentified product failure can be a threat to consumer safety and can result in loss of credibility and reputation, increased manufacturing costs, and economic losses.
Benefits of Calibration
Some of the benefits of calibration are:
- Long term cost-effectiveness, high return on investment
- High instrument accuracy and precision
- Reduction of costly errors
- Longer instrument life
- Compliance with regulatory standards and certification of equipment
- Elimination of safety risks
- Less downtime for repair and maintenance of equipment
- High customer satisfaction
Types of Instrument Calibration
Some of the common types of instrument calibration are:
Humidity and Temperature Calibration
It is used for businesses that use thermal cameras, thermometers, humidity generators, weather stations, and other instruments with their primary input as temperature and humidity.
This type of calibration is carried out in closed environments to eliminate disturbances from the surroundings and atmosphere.
Pressure Calibration
It is used for instruments such as transmitters, test gauges, and barometers. In pressure calibration, the spectrum of hydraulic and gas pressure is measured.
Mechanical Calibration
It is used for equipment such as torque wrenches, micrometers, scales, and balances. Mechanical calibration calibrates for factors like force, mass, vibration, or torque to ensure instrument accuracy.
Electrical Calibration
It is used for testing instruments such as clamp meters, data loggers, and insulation testers. Equipment that measures frequency, voltage, or resistance should undergo electrical calibration.
How often should Instruments be Calibrated?
While there is no specific single to call attention to this need, there are some ways to determine how often you should calibrate your instruments. The simplest thing to do is to follow the equipment manufacturer’s recommendation. Manufacturers often provide specifications about a device’s calibration and calibration period.
Another important factor to consider is the measurement location criticality and accuracy requirements. Some measurements require greater accuracy compared to others. The more critical locations should be calibrated frequently, while the less critical locations can be calibrated in longer intervals.
If an instrument is used often and is subjected to high workload and extreme or harsh operating conditions, it is good practice to calibrate often. The stability history of an instrument should also be factored in. If the instrument has a demonstrated history of being stable, it can be calibrated less frequently. On the other hand, if it has been shown to drift quickly, it should be calibrated more often.
Conclusion
Calibration is essential to every instrument used across industries and laboratories and should not be avoided or neglected. The type of calibration will differ depending on the type of instrument. Instruments performing critical operations should be calibrated more frequently.
Calibration can help reduce costs, prevent safety hazards and reduce risks, increasing an instrument’s life and performance, and ensure your business delivers on precision and customer satisfaction.