The components of a PID controller – Proportional (P), Integral (I), and Derivative (D) each have distinct characteristics and applications. These controllers can also be used independently or in combinations like PI, PD, etc.
Comparison of Proportional Integral Derivative Controllers
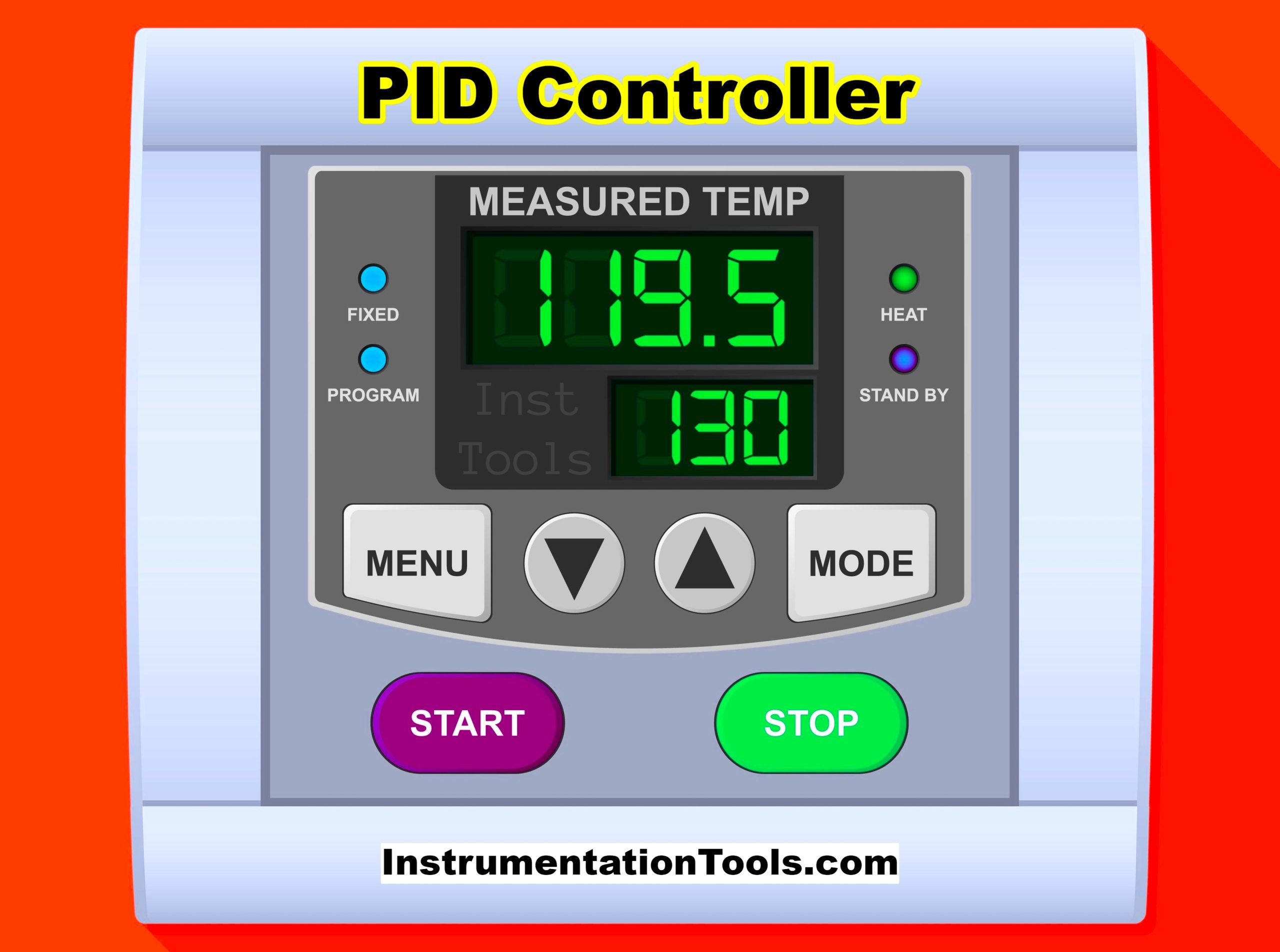
The following table shows the differences between the P, I, and D controller functions.
Parameter | P Controller | I Controller | D Controller |
---|---|---|---|
Principle of Operation | Proportional to error | Integral of error | Derivative of error |
Error Elimination | Steady-state error | Eliminates steady-state error | Does not eliminate any error |
Stability | Moderate | May reduce stability | Increases stability |
Overshoot | Moderate | High | Low |
Response Time | Fast | Slow | Fast |
System Type Suitability | First order systems | Systems with steady-state errors | Systems requiring damping |
Implementation Complexity | Low | Moderate | Moderate |
Cost | Low | Moderate | Moderate |
Application Examples | Level control, temperature control | Cruise control, HVAC | Damping control, robotics |
Tuning Complexity | Low | Moderate | Moderate |
Control Action | Proportional to present error | Based on accumulated past errors | Predictive, based on rate of error change |
Explanation of the terms:
- Principle of Operation: The mathematical relationship that dictates how each controller type reacts to the error signal.
- Error Elimination: How effective the controller is at eliminating system error.
- Stability: How the controller affects the system’s stability.
- Overshoot: The extent to which the system exceeds its setpoint.
- Response Time: How quickly the controller reacts to an error.
- System Type Suitability: Types of systems where each controller is most effective.
- Implementation Complexity: The complexity involved in implementing each type of control.
- Cost: The relative cost of implementing each control type.
- Application Examples: Common applications where each type of control is often used.
- Tuning Complexity: How difficult it is to tune the parameters for optimal performance.
- Control Action: Describes what aspect of the error signal the controller acts upon.
If you liked this article, then please subscribe to our YouTube Channel for Instrumentation, Electrical, PLC, and SCADA video tutorials.
You can also follow us on Facebook and Twitter to receive daily updates.
Read Next:
- Compare Hardwired I/O and Serial I/O
- Difference Between PNP and NPN Sensor
- Light Tower in Industrial Automation
- Learn about PLC, DCS, RTU, SCADA
- Programming and Tuning PID Controller