Industrial boilers are very important equipment in factories. Because steam is required in many processes, boilers play an important role in such industries. So, it is necessary to maintain boilers properly for longer life. One issue that always troubles boilers is corrosion.
Corrosion is mostly caused by dissolved gases and air. So, to prevent corrosion from affecting boilers, a device called a deaerator is used. A deaerator is available where a boiler is present. In this post, we will learn the concept of a deaerator.
Deaerator System
Let us first understand why a deaerator system is required. The first purpose is the removal of non-condensable gases and air. The thermal conductivity of air and non-condensable gas is very low. If air is stuck inside for a long time, then the heat transfer efficiency of the steam system can reduce to a great extent; which can also result in the creation of a vacuum inside. Also, air for a long period of time can also reduce the temperature of steam.
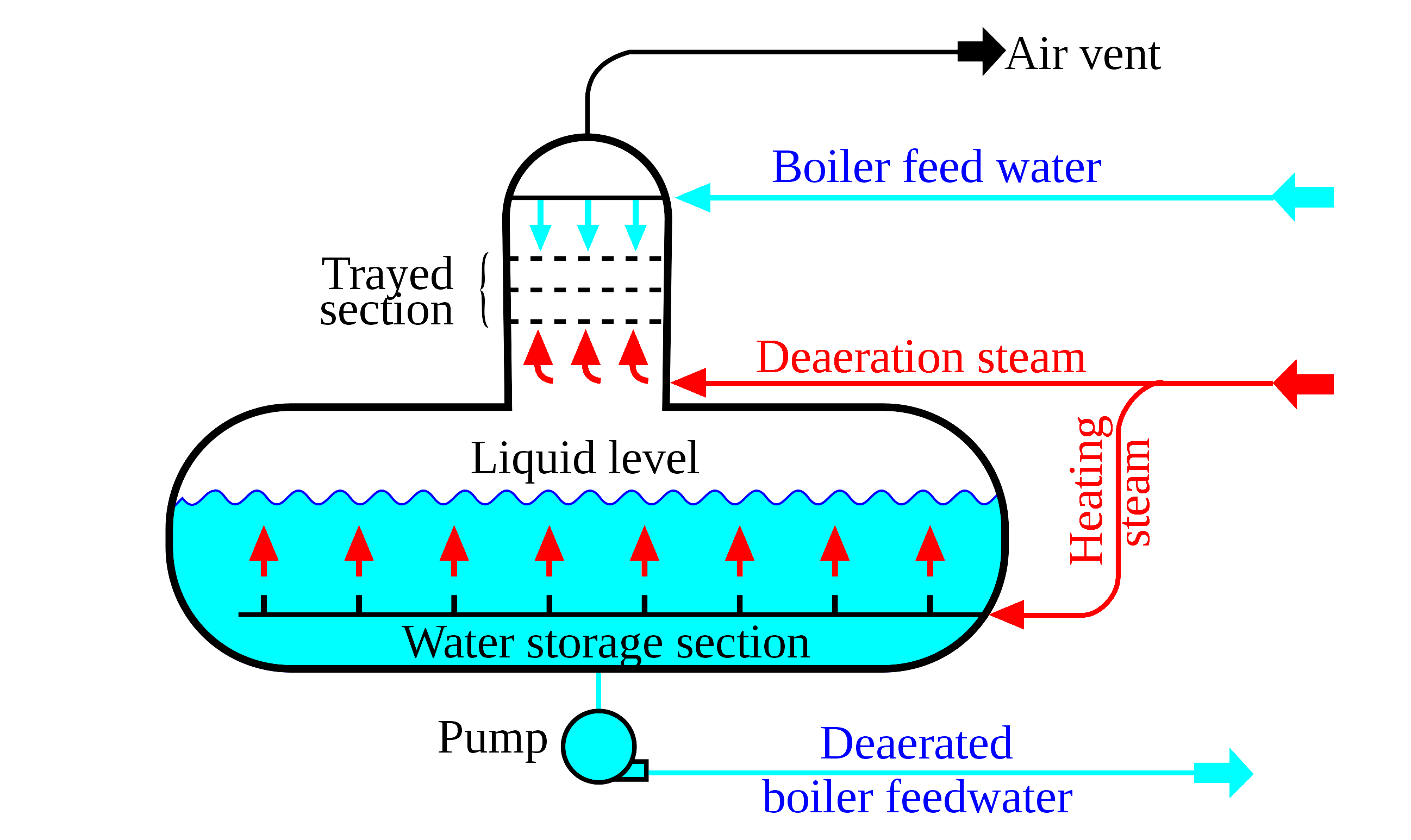
The second purpose is to increase the temperature of make-up water. Make-up water is a term related to cooling towers, which is added to increase water quality, lower fouling, and reduce the usage of chemicals in the water. Increasing its temperature can result in good evaporation factors and helps in heat transfer easily.
The third purpose is to store a certain amount of water in it which can be sent to the boiler as the demand for steam varies in a boiler. So, the deaerator plays a major role in boiler systems, to reduce corrosion and increase their life longevity.
Deaerator Working Principle
Basically, a deaerator is a pressure vessel system. The pressure and temperature inside it varies from design to design. It consists of four main inlets and outlets – a condensate inlet, a steam and gas vent, a steam inlet, and a safety relief valve.
A condensate inlet gets its input from the steam outlet of a boiler. After the steam of a boiler has condensed and released its heat, this condensate is fed here in the inlet, where its temperature is increased and fed back to the boiler.
The steam and gas vent is used to vent with the outside atmosphere and allows for the return of non-condensable gases in the outside air. Improper venting can cause damage to the boiler after a prolonged period of time by corroding it.
The steam inlet valve is used to provide steam to the deaerator, which is used to increase the temperature of the water inside. Increasing the temperature starts to reduce air and non-condensable gases inside to a massive extent.
A safety relief valve is used to open when the pressure increases and discharge the fluid until the pressure drops to an acceptable level. It is important to note that these inlet and outlet connections are arranged in the same sequence as discussed.
The process starts with a condensate inlet valve. The condensate outlet from the boiler or make-up water is fed here and inside the valve, it comes out in a spray form. The spray is used because it provides a good contact area and is able to touch many parts of the surfaces easily.
This provides good contact between water and steam and helps to increase heat transfer efficiency easily. And because heat transfer is achieved easily, the temperature too increases quickly and this starts to release air and non-condensable gases quickly. These released vapors will then travel to the vent valve and get released into the atmosphere.
Now, the remaining water from the first part will go down in the deaerator vessel and travel to the steam inlet section; where it will get heated up to increase its temperature. This water is then fed again to the boiler and the cycle continues.
Industrial Steam Deaerator
As you can see, all the theory works on steam and heat exchange majorly. So, the steam calculation is a very important factor before feeding it actually to the deaerator. One amount of steam is required to boil the water inside the deaerator; and as some amount of steam is vented with the non-condensable gases and air, it is required to consider that too. Some steam can get lost in steam traps too.
These factors need to be considered before deciding the final amount of steam to be given. But, it is to be remembered that the steam pressure must be low, as the deaerator vessel operates at lower steam pressure.
Read Next:
- Chemical Dosing System
- Reciprocating Compressors
- Design of Instrument Air System
- Blowout preventer Principle
- Compare Orifice & Restriction Orifice