For non-contacting radar level measurement there are two main modulation techniques,
- Pulse radar technique
- FMCW (Frequency Modulated Continuous Wave) radar technique
Basic principle
Non-contacting pulse radar sends out a microwave signal that bounces off the product surface and returns to the sensor. The transmitter measures the time delay between the transmitted and received echo signal and the on-board microprocessor calculates the distance to the liquid surface using the formula:
Distance = (Speed of light x time delay) / 2
Once the transmitter is programmed with the tank reference height of the application – usually the bottom of the tank or chamber – the liquid level is calculated by the microprocessor.
Level = Tank Height – Distance
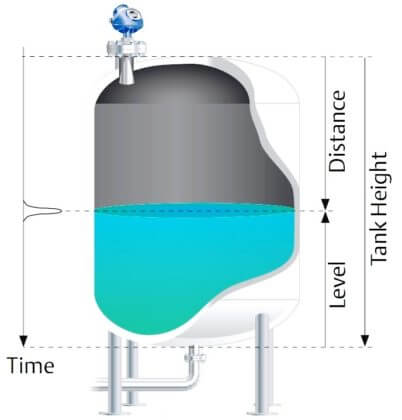
The FMCW radar also transmits microwaves towards the product surface, but the transmitted signal is of continuously varying frequency. When the signal has travelled down to the liquid surface and back to the antenna, it is mixed with the signal that is being transmitted at that time. The difference in frequency between the received and transmitted signal is directly proportional to the distance to the liquid with high precision.
Because it is non-contacting, the Sensor’s susceptibility to corrosion is limited and it is an ideal choice for viscous, sticky, and abrasive fluids.
Non-contacting radar can frequently be used in vessels with agitators. High frequency devices can be completely isolated from the process with PTFE seals and can be used with valves.
The frequency of the non-contacting radar can impact its performance. A lower frequency reduces sensitivity to vapor, foam, and contamination of the antenna, whereas a higher frequency keeps the radar beam narrow in order to minimize influence from nozzles, walls, and disturbing objects. Beam width is inversely proportional to antenna size. The beam width of a given frequency will decrease as the antenna size increases.
Advantages
- Non-contacting radar provides a top-down, direct measurement as it measures the distance to the surface.
- It can be used with liquids, sludges, slurries, and some solids.
- A key advantage of radar is that no compensation is necessary for changes in density, dielectric, or conductivity of the fluid.
- Changes in pressure, temperature, and most vapor space conditions have no impact on the accuracy of radar measurements.
- In addition, radar devices have no moving parts
- so maintenance is minimal.
- Non- contacting radar devices can be isolated from the process by using barriers such as PTFE seals or valves.
- Since it is not in contact with the measured media it is also good for corrosive and dirty application.
Limitations
- For non-contacting radar, good installation is the key to success. The sensor needs a clear view of the surface with a smooth, unobstructed, unrestricted mounting nozzle.
- Obstructions in the tank, such as pipes, strengthening bars and agitators can cause false echoes, but most transmitters have sophisticated software algorithms to allow masking or ignoring of these echoes.
- Non-contacting radar can handle agitation, but their success will depend on a combination of the fluid properties and the amount of turbulence. Dielectric constant (DK) of the medium and the surface conditions will impact the measurement. The measurement may be influenced by the presence of foam. Energy tends to not be reflected by light and airy foam while a dense and heavy foam typically reflects the energy.
- With low dielectric process fluids, much of the radiated energy is lost to the fluid, leaving very little energy to be reflected back to the sensor. Water and most chemical solutions have a high DK; fuel oil, lube oil and some solids, such as lime, have a low DK.
- If the surface is turbulent, whether from agitation, product blending, or splashing, more of the signal is lost. So a combination of a low dielectric fluid and turbulence can limit the return signal to a non- contacting radar. To get around this, bypass pipes or stilling wells can be used to isolate the surface from the turbulence.
Types of Radar Level Transmitter Antennas
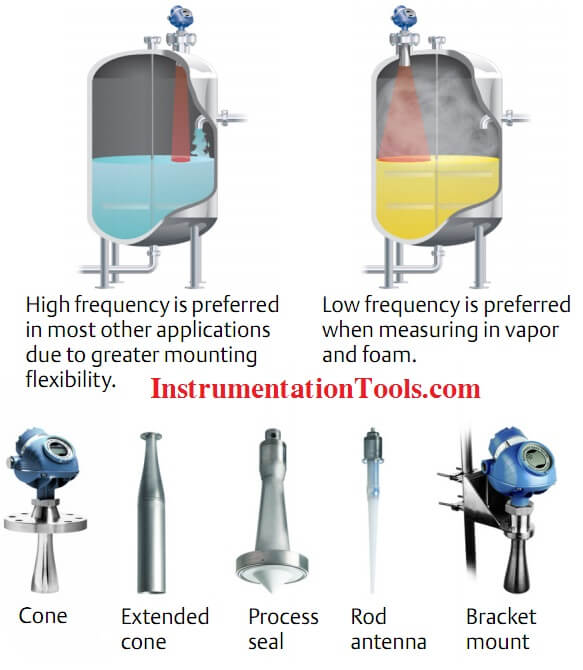
thank u!
Instrument technician full courses
The radar levels TX have some problems when measure oil or lube, due the the low DK of the liquid, and when the level liquid is low, on those cases the Echo profile will show two peaks, one weak, which is the reflect of the liquid, and one more strong, which is from the floor, but because a delay of the back signal the measure is higher than really should be, some devices come with a software which suppresses or cut the strong back of the signal in low measuring levels. The guide wave radars have better performance and are capable to measuring liquid phases, but are a little expensive.