Instrumentation engineering root cause analysis of level instruments of ammonia flash vessel stopped working.
Article Type: | Root Cause Analysis (RCA) |
Category: | Instrumentation |
Equipment Type: | Sensors |
Author: | S. Raghava Chari |
Note: This root cause analysis (RCA) is from real-time scenarios that happened in industries during the tenure of two or three decades ago. These articles will help you to improve your troubleshooting skills and knowledge.
Layout Description
A Differential Level Transmitter (DLT), a Hi-Level (LG), a Lo-Level (LG), a Hi LS, a Hi-HI LS, a Lo LS, and a Lo-Lo LS – Seven level instruments – bolt to the 3” Sch 120 pipe connecting the vessel top nozzle (below figure; TN) to the bottom nozzle (BN).
The figure shows just two instruments to avoid clutter. Such instruments mounting avoids multiple taps welding on the 40‑bars operating pressure ammonia, N2, and H2 rich synthesis gas wetted vessel subjected to stringent weld codes.
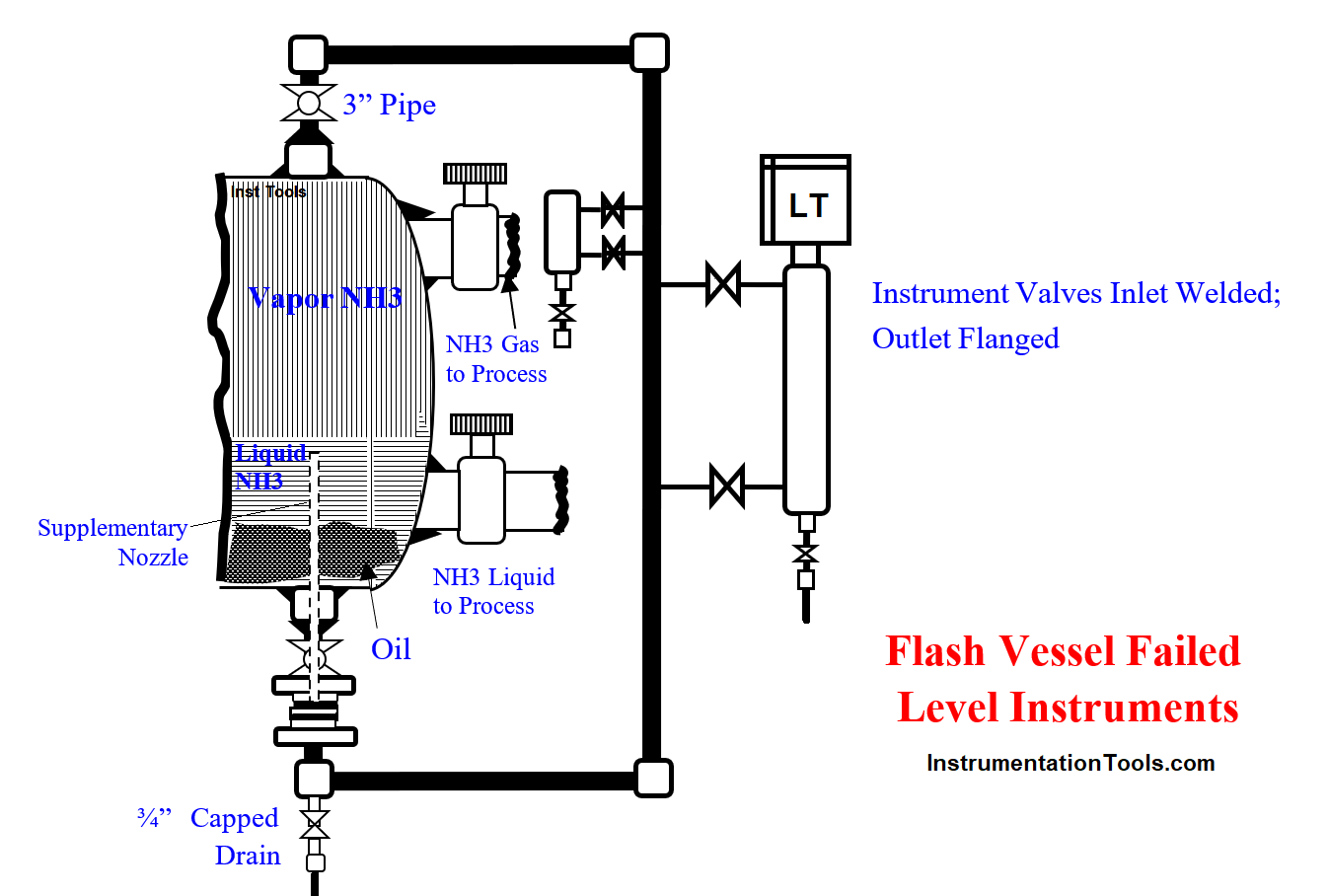
Flash Vessel Level Instruments Stopped Working
All the level instruments behaved erratic three months after commissioning. Simultaneous erratic so many instruments behavior points blocked signals. Draining the line and steam cleaning if necessary seemed the answer.
All ridiculed the Author’s diagnosis, “how can liquid ammonia as clear as distilled water choke especially 3” pipe column feeding the instruments?”
The author patiently explained, “Friends, I also don’t know the oil source; but oil draining only we can do. Let us do it and hope for the best. The 0.8 Sp Gr oil settles at the tank bottom below the 0.64 Sp Gr liquid NH3.
I guess this oil emulsified and choked the 3” pipe in 3 months. Hence, let us try oil draining. Though half-convinced, the crew were reluctant to drain fearing the extreme pungency of ammonia escaping to the atmosphere. Even PPM levels of ammonia are highly irritating.
Immediate Solution
The author guided the operation engineer to get the oil drained safely as under:
- Insert a hose clamped to the ¾” drain into an empty oil drum small dia hole and build a clay dam at the entry to avoid vapor leaks
- Screw in a 3 m long 1½” pipe to the large dia hole
- Close the bottom and top 3” block valves and open the ¾” drain valve and crack open the bottom 3” valve
- 40-bars gas pressure pushed tank bottom collected oil drains into the tank and the carried over and flashed gases escaping via the large 1½” pipe to the atmosphere well above the ground and winds carry these away
- After 15 minutes draining, close the ¾” drain valve, remove the hose clamped to the drain, crack open the ¾” drain valve; if oil drain continues clamp back the hose and continue draining few times as above till no oil comes out
Crew drained nearly ¾ drum of oil. Then they put the instruments back on service. Finally working all instruments cheered all.
The plant continued till the 18-months later turnaround by draining the oil two monthly.
Problem Solved Forever
The author got done below listed activities solved the problem forever:
- He got a supplementary nozzle made before the plant turnaround (TA). It is a 1.2 m long ¾” pipe welded to a 10 mm thick x dia = 3” 300 # RF flange dia
- Replaced the both sides welded 3” bottom valve with inlet welded and outlet flanged 3” gate valve.
- Inserted the supplementary nozzle into the tank and bolted back the 3” line
Thanks to the supplementary nozzle, oil did not reach the 3” pipe, and the instruments performed flawlessly between the two yearly TAs.
Operators conveniently drained the oil from the depressured tank easily and were extremely safe.
Intermediate & Final Solution Benefits
Intermediate & final Solution Benefits are:
- The intermediate solution enabled safe oil draining averted plant shutdowns for two monthly oil drains
- The final solution of inserting the supplementary nozzle eliminated the cumbersome and risky draining between turnarounds
- The level instruments perform will with conveniently draining the oil at a TA when the vessel is free of NH3 – very safe and easy task
- Always available reliable level readings smoothens plant operations and boosts safety.
Author: S. Raghava Chari
Do you face any similar issues? Share with us through the below comments section.
If you liked this article, then please subscribe to our YouTube Channel for Instrumentation, Electrical, PLC, and SCADA video tutorials.
You can also follow us on Facebook and Twitter to receive daily updates.
Read Next:
- Level Transmitters Zero Drifts
- Pitot-tube Replaced with Orifice
- Mechanical Temperature Indicator
- Pressure Transmitter Stopped Working
- Seal Pressure Instruments Problems