Control loops are the building blocks of control systems and come in various configurations, depending on the number of variables being controlled, the type of control, and other factors.
Comparison of Control Loops
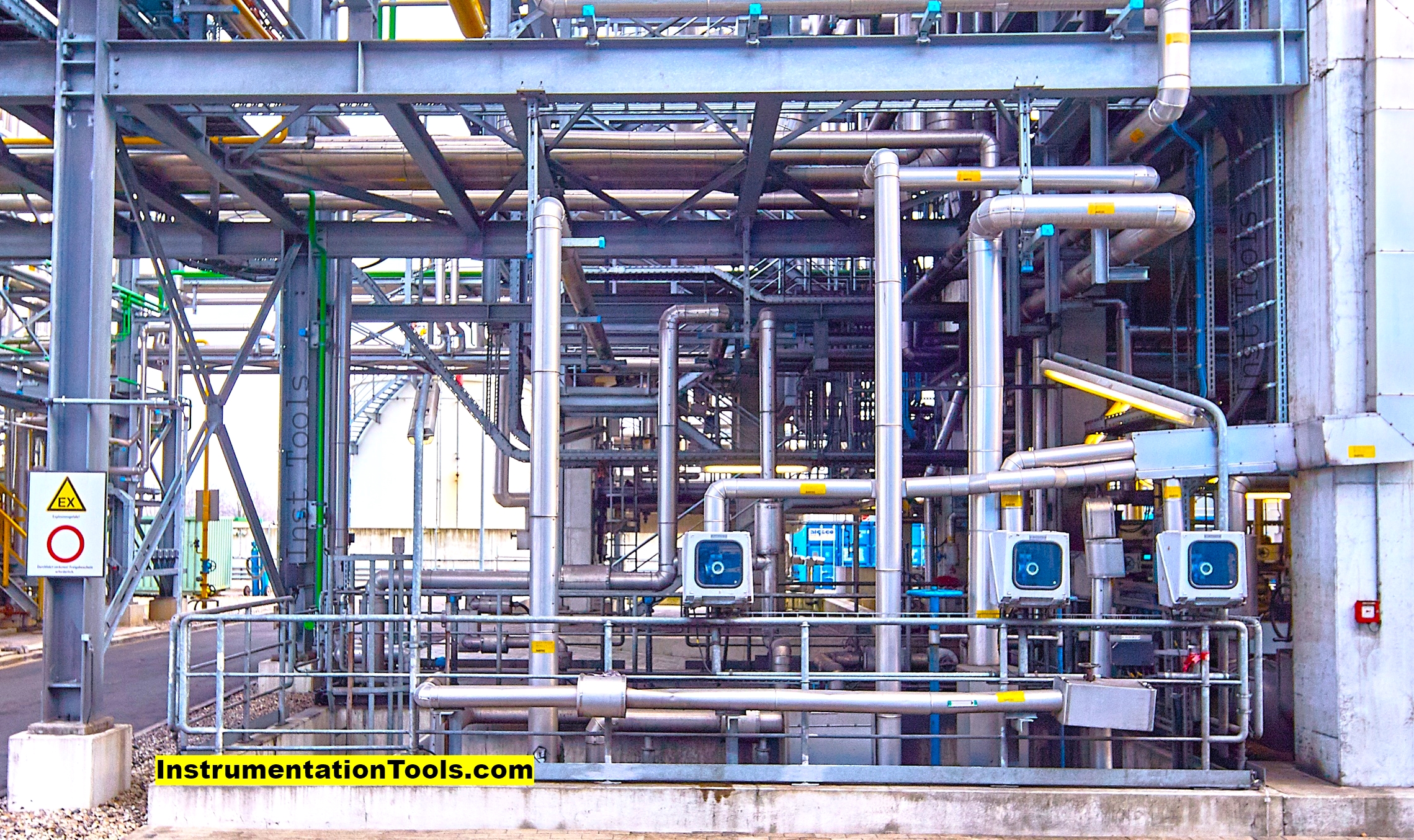
Below is a comparison table that outlines the key features of commonly used types of control loops such as open, closed, cascade, feedforward, ratio, and split range loops.
Parameter | Open Loop | Closed Loop | Cascade Loop | Feedforward Loop | Ratio Control Loop | Split Range Loop |
---|---|---|---|---|---|---|
Principle of Operation | No feedback is used. Output is neither measured nor adjusted to achieve a desired result. | Uses feedback to adjust the control action based on the output. | Two control loops where the output of one serves as the set point for another. | Anticipates disturbances and proactively adjusts the system. | Maintains the ratio between two variables. | Uses multiple control devices to handle different ranges of a process variable. |
Theory | A predetermined input directly controls the action, irrespective of the output. | Measures output, compares to a set point, and adjusts accordingly. | Main loop controls a process variable, secondary loop controls another variable. | Identifies disturbances and proactively makes adjustments before they affect output. | Measures two variables, adjusts one to maintain a set ratio with the other. | The controller splits its output to different control elements based on setpoints. |
Advantages | Simple design. Generally less expensive and less complex. | Higher accuracy due to feedback. Adaptable to system changes. | Better disturbance rejection. Enhanced control accuracy. | Preemptively deals with disturbances. Enhances output quality. | Ensures consistent ratios. Useful for processes like blending or mixing. | Efficiently manages processes with a wide operation range. |
Disadvantages | No correction for disturbances. Potential inaccuracy. | More complex design. Potential for instability. | More complex setup. Needs tuning of two controllers. | Requires knowledge and model of the disturbance. Complexity increases. | Requires accurate measurement. If one variable falters, the ratio is affected. | Potential for overlap or dead zones. Needs careful tuning. |
Response to Disturbances | Poor | Good | Good | Good | Good | Variable |
Accuracy | Low | High | High | Moderate to High | High | Moderate to High |
Stability | Variable | Generally stable | Generally stable | Can improve stability | Generally stable | Generally stable |
Complexity | Simple | Moderate | Complex | Moderate to Complex | Complex | Moderate to Complex |
Cost | Low | Moderate to High | High | Moderate to High | High | Moderate to High |
Control Action | Pre-determined | Dynamic | Multiple, Dynamic | Dynamic | Dynamic | Dynamic |
Tuning Required | No | Yes | Yes | Sometimes | Yes | Yes |
Application Examples | Timers, Basic motors | HVAC, Industrial processes | Complex systems with interacting variables | Systems with measurable disturbances | Mixing, Blending processes | Heating and cooling systems |
Feedback Required | No | Yes | Yes | Yes | Optional | Optional |
Brief explanation:
- Principle of Operation: The fundamental principle that the control loop operates on.
- Response to Disturbances: How well the loop can handle changes in the system or environment.
- Accuracy: How precisely the loop can control the process variable.
- Stability: The loop’s ability to maintain control without oscillating.
- Complexity: The difficulty level in understanding, implementing, and maintaining the loop.
- Cost: The relative financial expense of implementing and maintaining the loop.
- Control Action: Describes the method of control action undertaken by the loop.
- Tuning Required: Whether the control parameters need to be tuned for optimal performance.
- Application Examples: Examples of real-world applications where each type of control loop is used.
- Feedback Required: Whether the loop needs feedback from the process variable.
If you liked this article, then please subscribe to our YouTube Channel for Instrumentation, Electrical, PLC, and SCADA video tutorials.
You can also follow us on Facebook and Twitter to receive daily updates.
Read Next:
- PLC Data Files and Program Files
- Testing Modbus Communication
- S7-1500 S7-1200 S7-400 S7-300
- Static and Temp Variables in PLC
- Power Supply Sizing for Systems