Loop diagrams are very important Instrumentation design deliverable. Mainly for construction contractor who will install and wire all the loops. It helps them to track each and every tag correctly and easily while keeping log of the activities.
Loop drawing are mostly drawn on drafting software like AutoCad but nowadays they can be generated automatically by intelligent design data base softwares.
Purpose of this particular Instrumentation design deliverable is but not limited to :
1) Showing how the control system is getting Instruments data and how it controlling output device. The complete wiring of the loop is shown for particular tag whether that tag is open loop or close loop.
2) Indicating the accessories associated with that loop for example some loops will have loop power indicator or some instruments will have extra displays.
3) Specifying all the point to point connection with cable details and their termination locations.
Loop Diagram
In below picture a sample loop drawing is shown
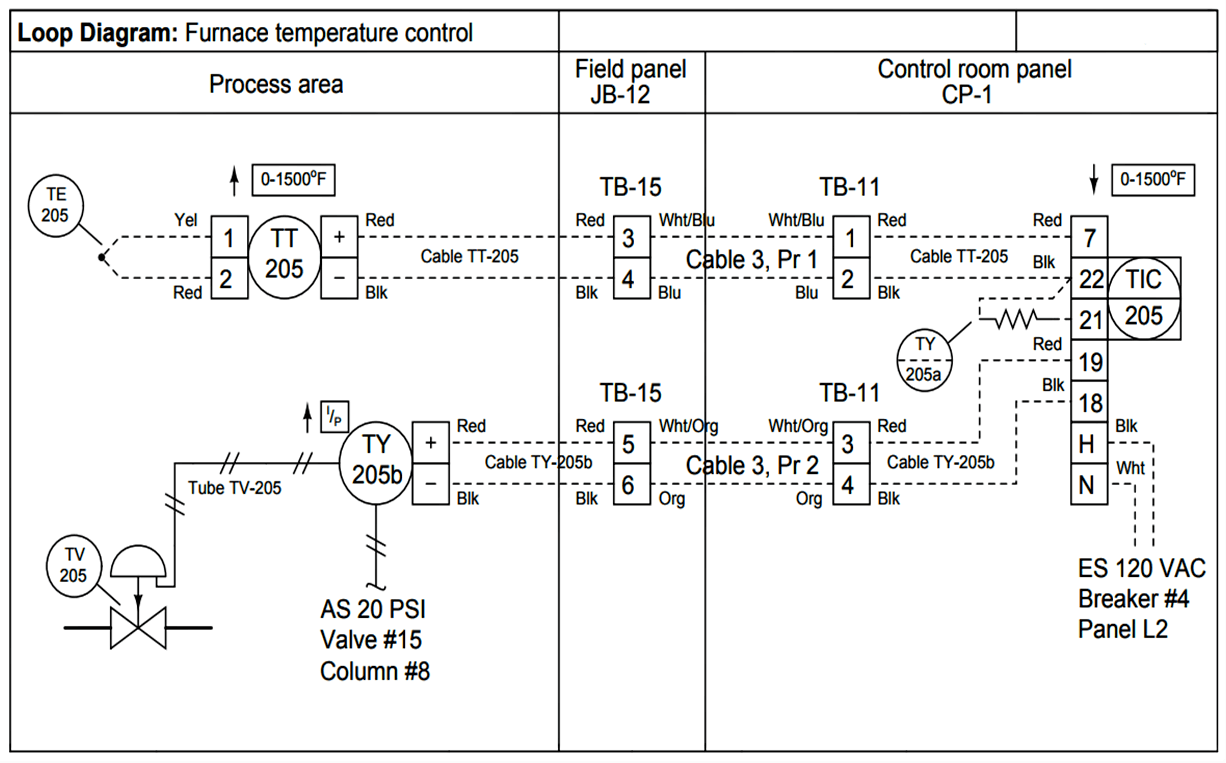
Decoding the Information
ISA 5.4 clearly states minimum and optional information that should be in Loop Diagram but let’s try to understand that using above loop diagram as an example.
At first glance we can see that whole diagram is divided into 3 main location wise parts viz Process area, Field Panel junction box and control room.
This is general format but due to complexity of the loops every case is different for example if remote I/Os are used format would be different but remember we have to show whole routing of the cable from the instrument to the very last terminal of the control panel.
Also note just like P&ID here we also indicate if it is electrical line or pneumatic via standard method.
In above loop diagram temperature element wiring to its transmitter is also shown with transmitter’s terminal numbers and colours of the cables.
But Instrument range is also indicated above the transmitter, which is not compulsory or something should be mentioned in each loop diagram. Every loop diagram’s format would be different in some capacity.
Fundamental details like terminal numbers, cable tags, cable colours, location of each and every termination are main features of this deliverable. In above example we can clearly see termination are clearly mentioned with numbers also colour and tags of the cables are clearly indicated.
One very important factor is how that Instrument is powered up; here we can see it is loop powered instrument so no need to show additional power wiring but some instruments require separate power sources. In such cases power wiring indication is important, remember our aim is to explain the whole geography and architecture of the loop.
If there are any interlocks are acting on this loop that also needs to be shown properly and interlock description should also be added to notes if applicable.
Also for actuators it is very important to show fail safe position as per ISA-5.1(Instrumentation Symbols and Identification).
There are optional information that can be represented in loop drawing as and when needed like model and manufacturer details of equipments, reference to other deliverable and cross reference between loops where they use one device such as recorder.
Reference
- ISA 5.4 – INSTRUMENT LOOP DIAGRAM
Author: Kalpit Patel
Read Next
- Loop Diagram Question
- Intrinsic Safe Calculation
- Engineering Logic Diagrams
- Electrical Schematics
- Junction Box Schedule
A loop diagram for an instrumentation technician or engineer is very useful and important as a maintenance tool. It can be used to follow the connection line of an instrument in the field, hence easily locate the error or the malfunction.
You will know through which cabinet and JBs the instrument is connected prior to enter the PLC or the DCS marshalling panel. Without the loop diagram it will be very difficult to have complete knowledge about the complete connection drawing.