Safety instrumented systems (SIS) are the most flexible and one of the most common engineered safeguards used in process plants today. The design of SIS, in accordance with current practice, is a risk-based process where the selected equipment and associated maintenance and testing procedures are tailored to the specific requirements of an application. This risk-based approach yields superior designs that provide the required risk reduction while minimizing cost.
SIS design has become a more complex process due to the need to understand more than traditional instrumentation and control engineering. In addition to basic concepts, SIS design requires expertise in analyzing the risks of the process under control (which necessarily requires an understanding of the process) in order to establish design targets, and also expertise in reliability engineering to ensure that the selected targets have been met.
The purpose of this book is to provide a brief overview of the Safety Lifecycle that is used to design SIS, along with general information to assist in performing the tasks that are defined in the safety lifecycle. This includes tables of data, lists of definitions and acronyms, equations, and explanations for using these resources.
Safety Instrumented System
The Safety Instrumented System is an instrumentation and control system that detects out-of-control process conditions, and automatically returns the process to a safe state. It is the last line – or near the last line – of defense against a chemical process hazard, and it is not part of the Basic Process Control System. The last line of defense is what differentiates a Safety Instrumented System from the Basic Process Control System, which is used for normal regulatory process control.
The below figure demonstrates how Safety Instrumented Systems are different from Basic Process Control Systems, or the BPCS. In this example, pressure is a potential hazard. Pressure is normally controlled by a regulatory control loop, shown as the Basic Process Control System, which modulates a pressure control valve.
An independent high-pressure shutdown function is implemented in a Safety Instrumented System. It is independent in as much as the components used in the BPCS and the SIS are separate, physically and functionally.
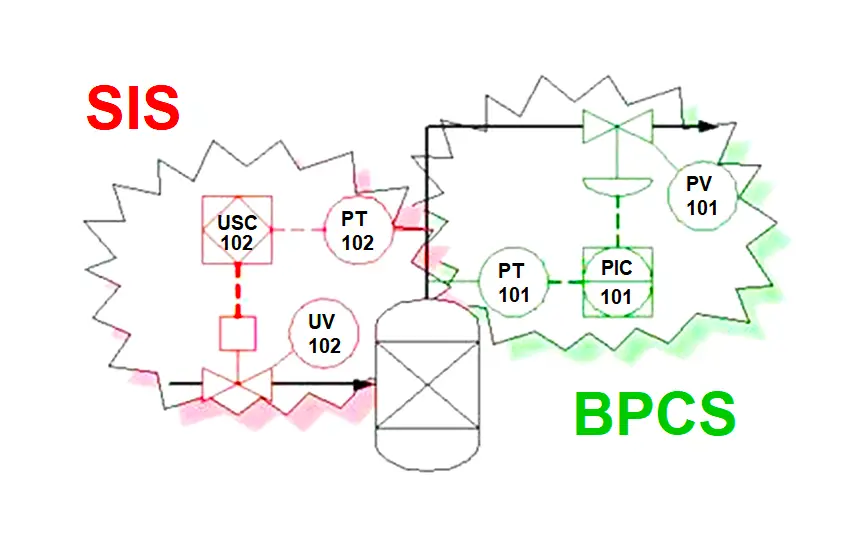
This includes the sensor components, the logic solver, as well as the final control elements. SIS are generally independent, both physically and functionally, from the BPCS in order to ensure that any condition, that might result in an out-of-control process parameter in the BPCS, is safeguarded by the SIS, regardless of the function of the BPCS.
The SIS will include three types of components including sensor components, a logic solver component, and final control elements. Together these components make up the Safety Instrumented System, which detects out-of-control process conditions, and automatically returns the process to a safe condition, regardless of the functioning of the Basic Process Control System. In this case, the SIS could include a programmable system or a non-programmable system.
Read more about the SIS. Download the document from the below table.
Title: | Safety Instrumented System Handbook |
Author: | Kenexis |
Format: | |
Size: | 1.69 MB |
Pages: | 67 |
Download: | Click Here |
If you liked this article, then please subscribe to our YouTube Channel for PLC and SCADA video tutorials.
You can also follow us on Facebook and Twitter to receive daily updates.
Read Next:
- Pyrometers Handbook
- Electrical Enclosure eBook
- Valve Basics and Sizing Book
- Industrial Control System Guide
- Instrumentation Books Download