In this article, we will learn how to configure PID controllers in Siemens PLC using Tia portal programming software.
PID is a very important function block in controlling various analog parameters like temperature, flow, pressure, etc. through modulating outputs.
This modulation helps in keeping the parameters hovering around a control set-point and accurately controlling the process. PID function is available in various PLCs and also some standalone microcontrollers.
Also, there are some specific PID controllers available in the market which are designed to just handle the PID process.
Various PLCs have different types of PID configuration according to the software design. In this post, we will have a look at the PID configuration in Siemens PLC.
Configure PID in Siemens PLC
Let us see step by step how to configure a simple PID in Siemens PLC.
On opening the software, add a new object in Technology objects as shown in the figure. On clicking it, a popup window will open to add a new technology object.
In the PID window, select PID_Compact; which will add a PID controller in the software.
There are two other PID types available as shown in the figure; but here, we will see a simpler type that is widely used.
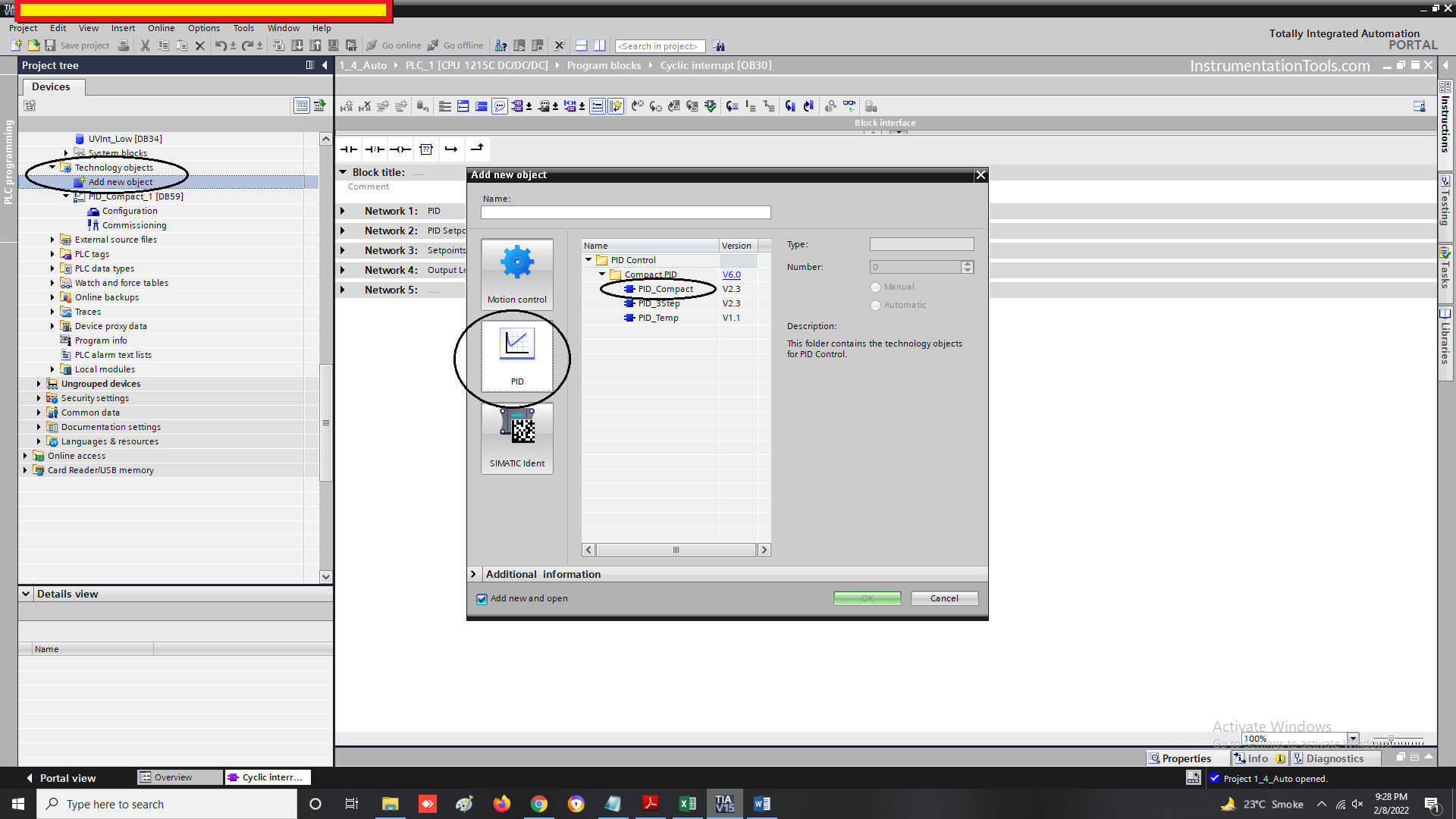
When the block is added, click the Configuration tab under the PID block added. A whole new window of configuration parameters will open.
In the next step, we will first see the series of images where basic configuration parameters need to be edited for PID working.
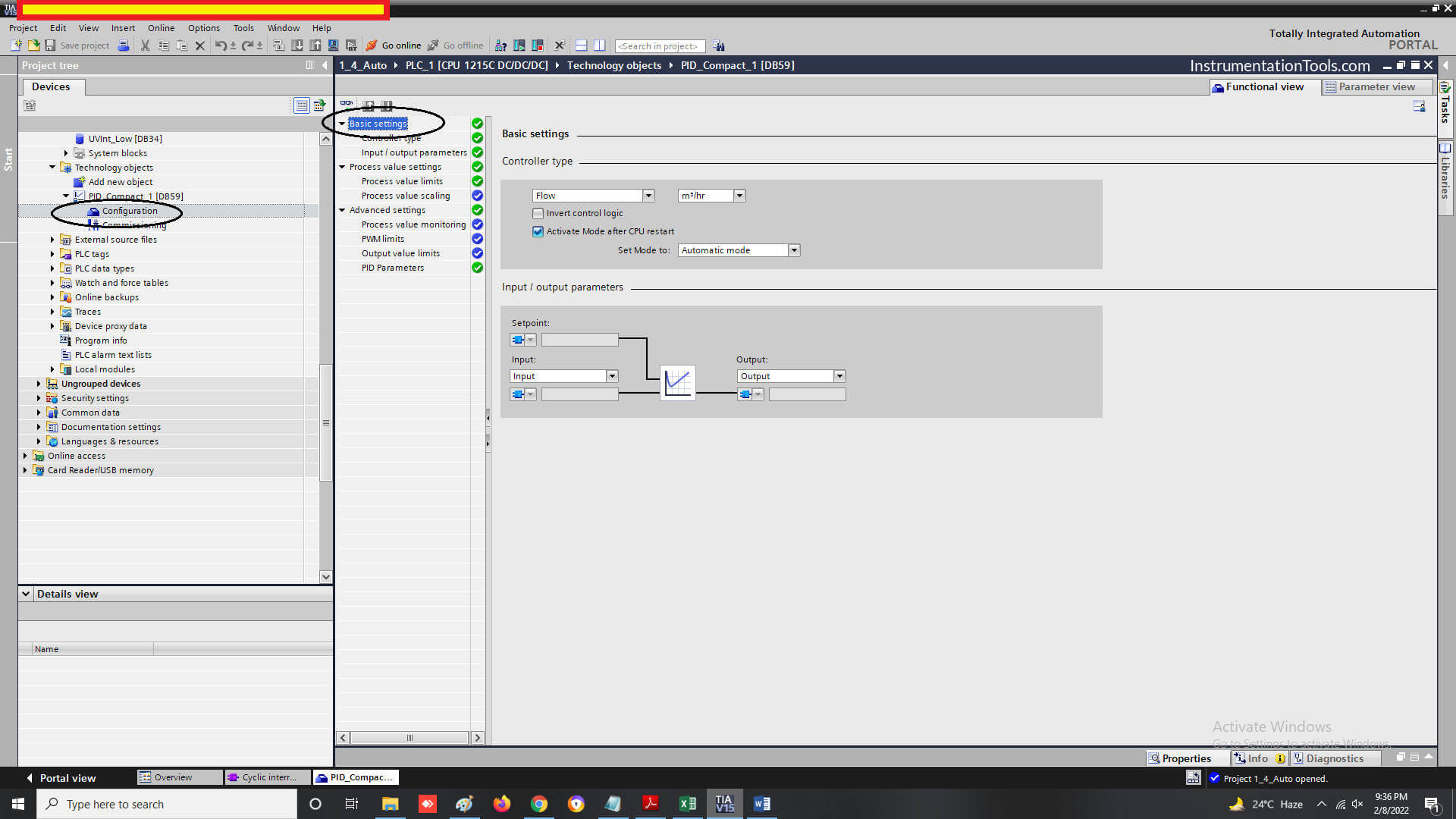
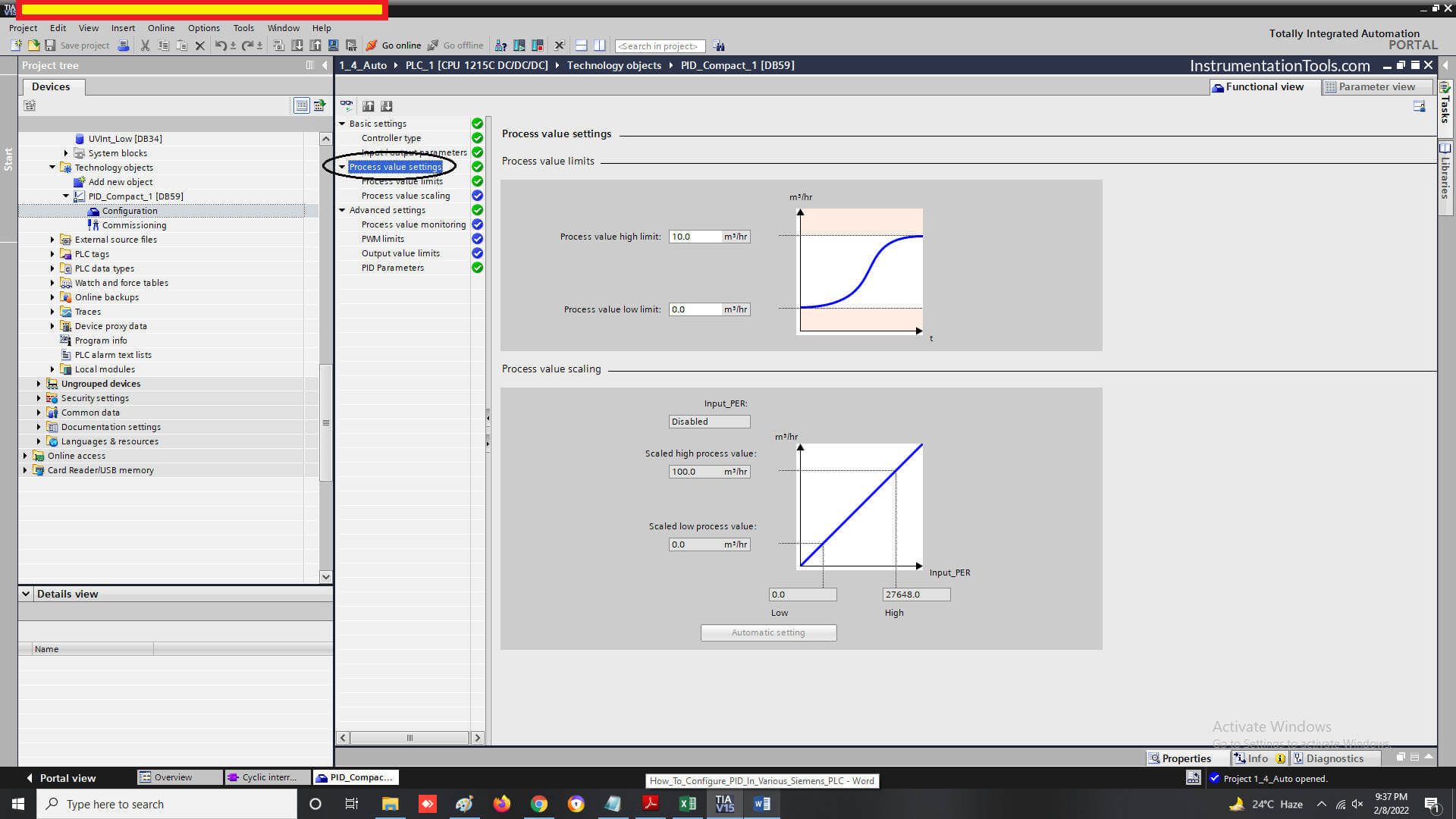
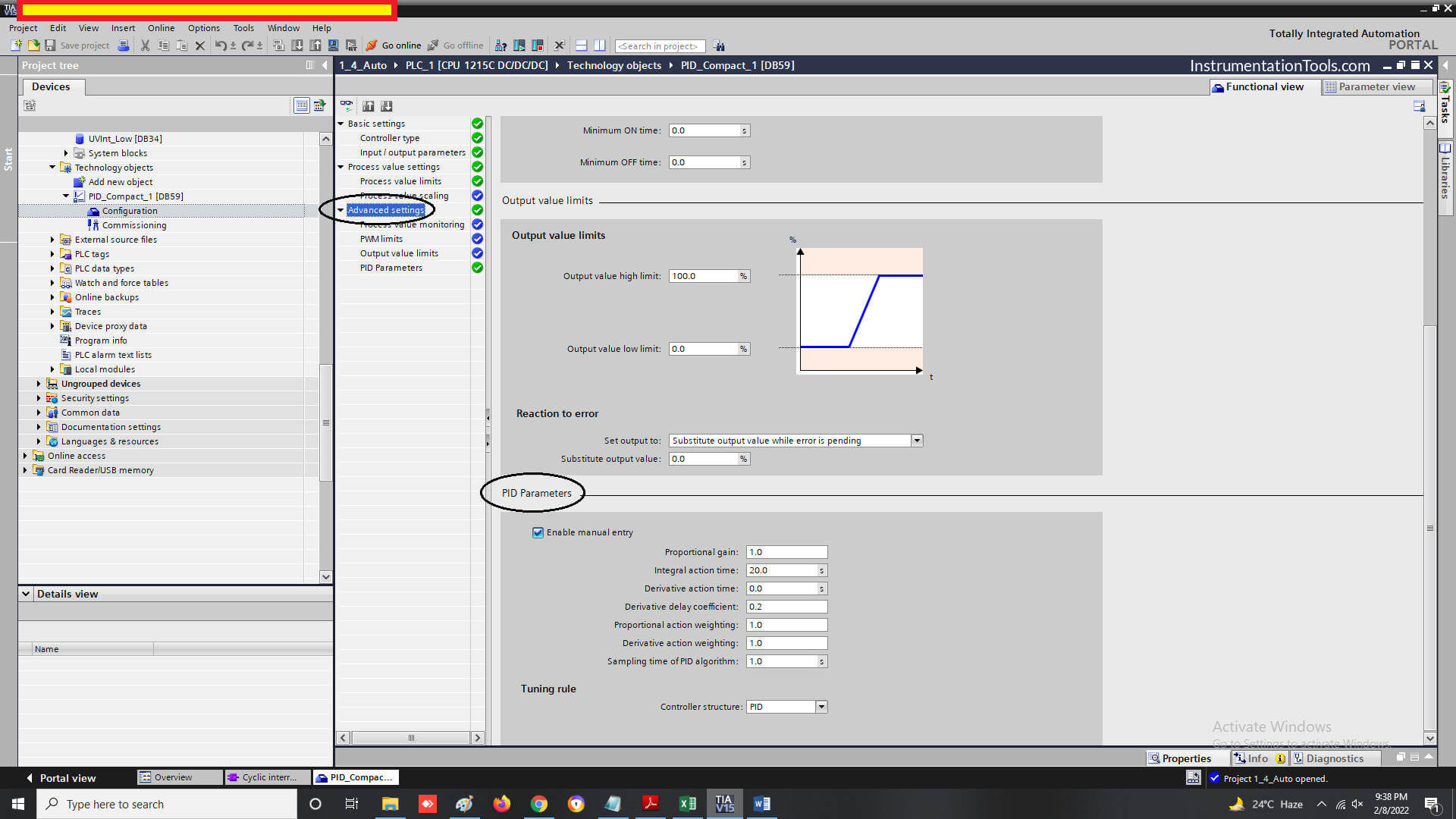
In the basic settings screen, as shown in the first image, you have to select the analog sensor type to be controlled, its unit, mode selection, its input type and output type.
In the process value settings screen, as shown in the second image, you have to select process value high limit and low limit.
In the advanced settings screen, as shown in the third image, you have to set PID values (if you are not setting PID configuration to auto-tune).
Then, you have to add an OB (Cyclic Interrupt) in the program as shown in the figure.
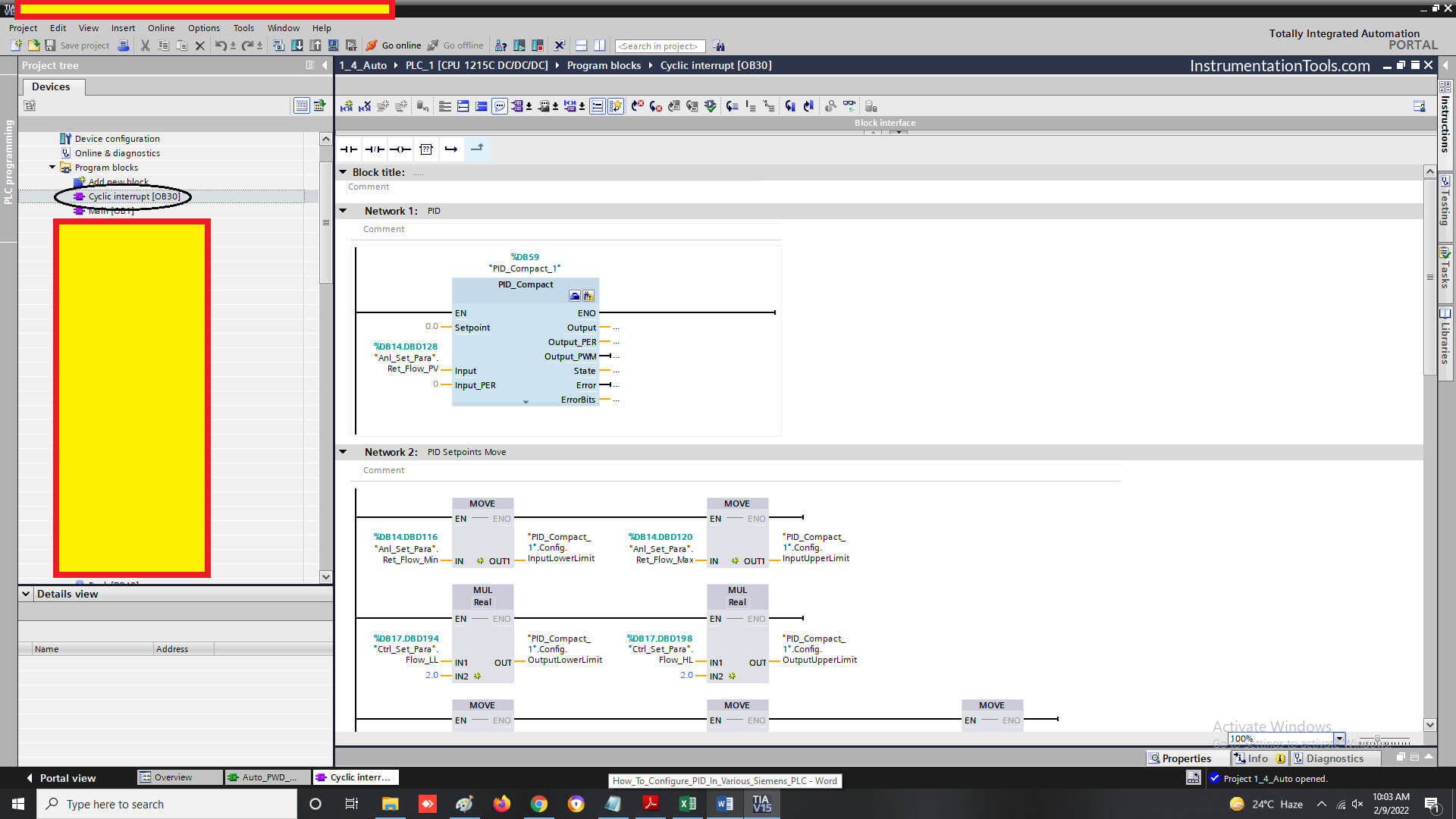
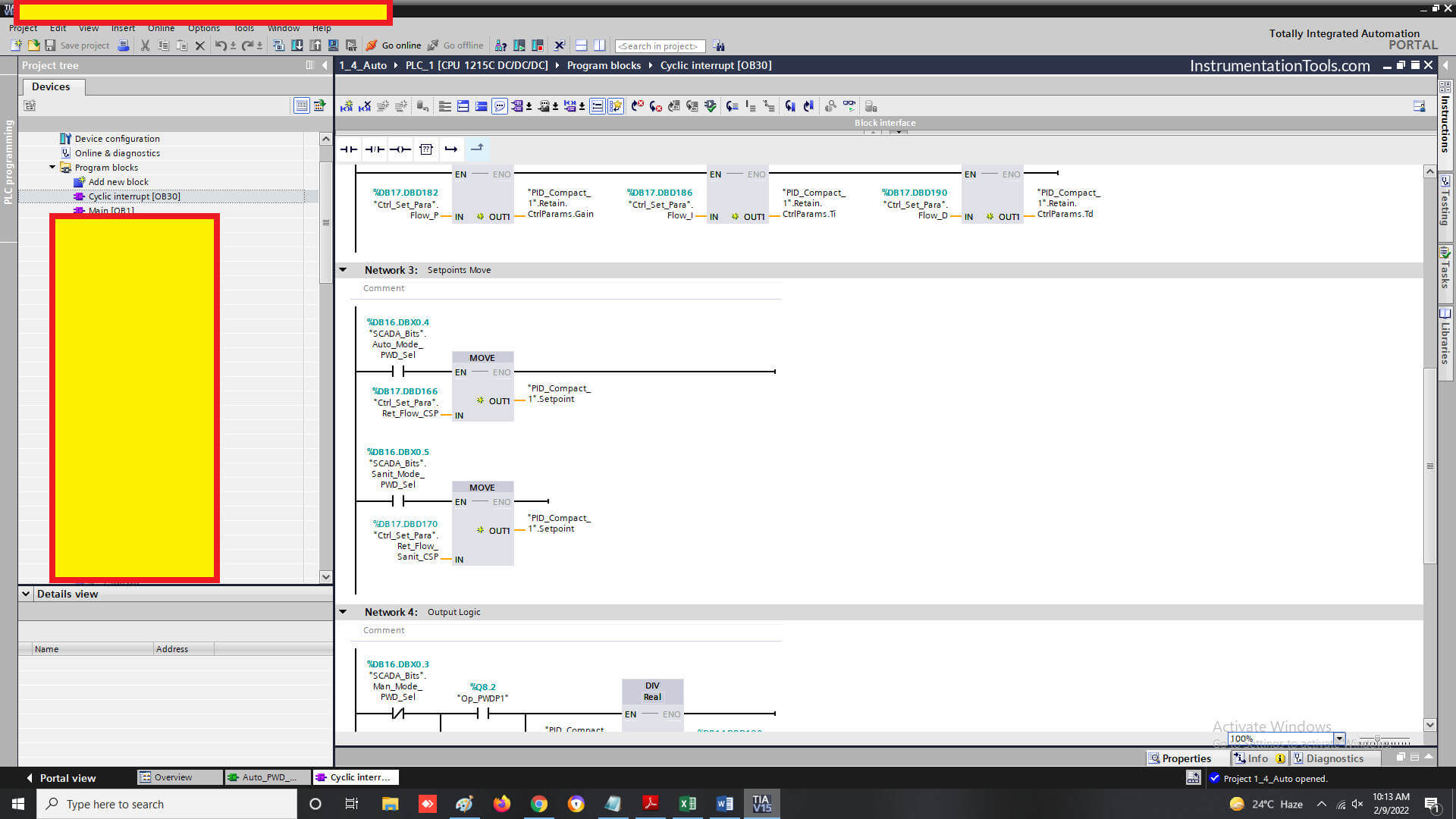
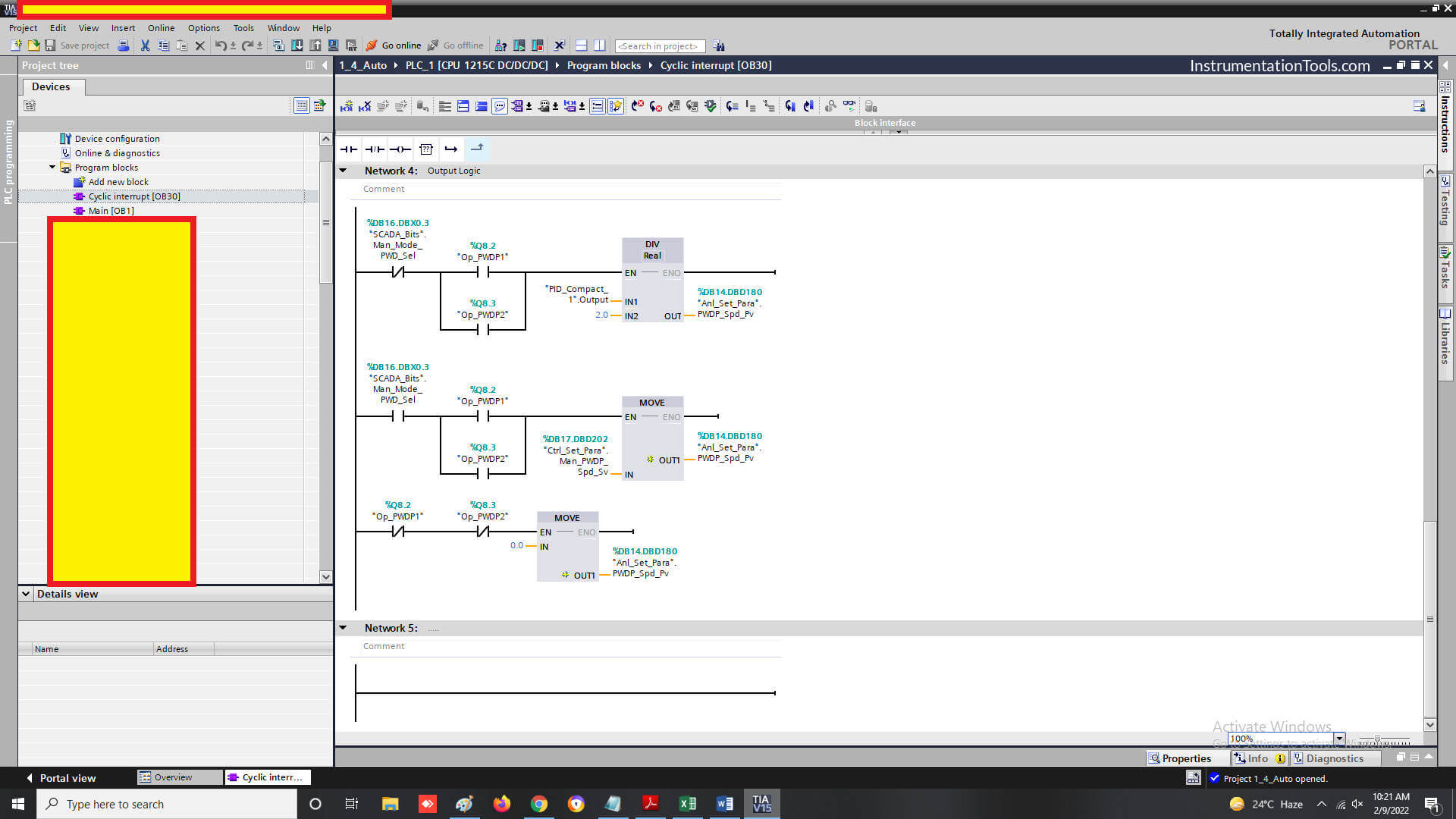
Then, as shown in the above three figures, you have to make the same sections in this OB.
Basically, you are moving set parameters from the HMI or SCADA in the PID configuration. This will overwrite the settings done in the PID configuration.
As shown, in the first image, take the PID block and map the process variable to it. Then, move the following parameters to the PID configuration – input lower and upper limits, output lower and upper limits, P, I, D, and control set-point.
In the third image, we have to only move the PID output to the physical analog output according to the logic required.
After doing all this, just download the backup in PLC, power recycle it, and check. The PID will work properly according to the parameters set.
In this way, we saw how to configure PID in Siemens PLC.
Siemens Tia PLC Course
Follow the below series of videos from Siemens PLC Tia course.
If you liked this article, then please subscribe to our YouTube Channel for Electrical, Electronics, Instrumentation, PLC, and SCADA video tutorials.
You can also follow us on Facebook and Twitter to receive daily updates.
Read Next:
- Nameplate of a Motor
- Solenoid-controlled Valve
- MODBUS ASCII Communication
- DCS Alarm Summary Dashboard
- AC Fundamentals Questions