PLC is a crucial and basic component of the automation system of any industrial process, using a PLC in your process will help increase productivity, reliability, and performance of your process. But these benefits can only be achieved if an adequate selection of the PLC was made. Choosing the PLC that best fits your application will help your process reach its designed targets.
In this article, we will talk about how to select a PLC for your application.
Contents:
- What is a PLC?
- Why PLC is important in automation?
- How to select the best PLC for your application?
- Examples of PLC selection.
- When is a PLC no longer suitable for your application?
- What would be the alternative to the PLC?
- Examples where a PLC may not be the best choice.
- Conclusion
What is a PLC?
PLCs are control devices used to automate and control machines and industrial processes. They are used in various industries such as manufacturing, chemical processing, and transportation to control and monitor industrial processes.
PLCs can be programmed using ladder logic or other programming languages via many programming software and platforms depending on the PLC brand you use. PLCs are designed to withstand harsh environments and operate reliably for long periods of time.
Why PLC is important in automation?
PLCs are an important component of automation because they provide a reliable and efficient way to control industrial processes and machines.
Some of the benefits a PLC provides are:
- PLCs are designed to operate in harsh industrial environments and can withstand high levels of vibration, shock, and temperature fluctuations, making them ideal for use in industrial automation.
- PLCs are programmable devices, which means that they can be easily reprogrammed to adapt to changing production requirements, making them versatile and flexible.
- PLCs are a cost-effective solution for automating industrial processes when compared to other types of automation systems.
- PLCs operate in real-time, which means that they can respond quickly to changes in the process or environment, ensuring accurate and precise control.
- PLCs are easy to integrate with other automation components such as HMIs, SCADA systems, and other industrial devices.
These benefits and many more are why PLC is very important for automation.
How to Select the Best PLC for Your Application?
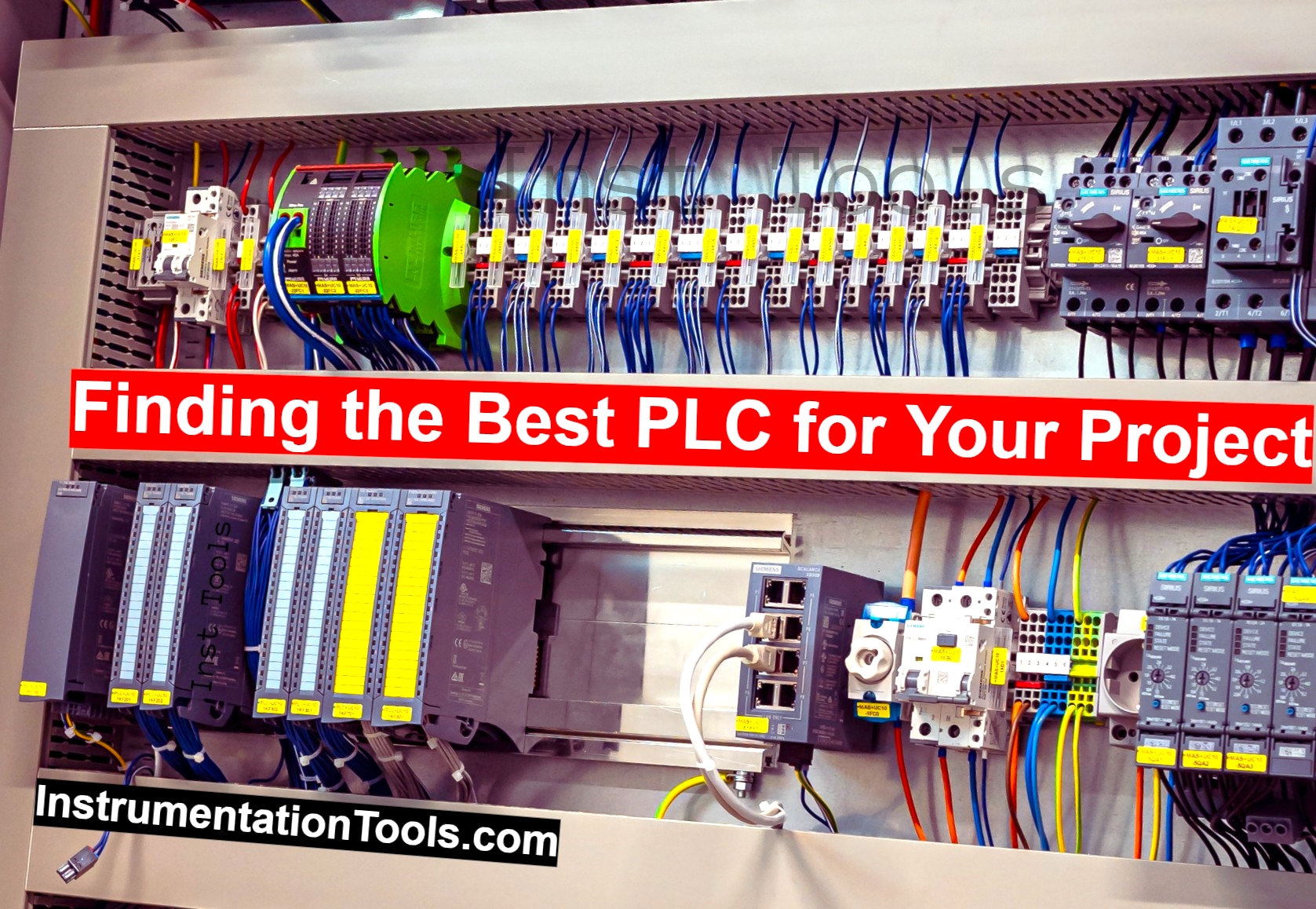
As we said before, all the benefits and advantages of using PLCs in your automation system will only be achieved if a suitable PLC was chosen for the application.
Failing to choose the PLC that best fits your process requirements will not only cause the loss of some of these benefits but also might be a cause for hindering your whole process.
The Factors for Choosing the Right PLC
There are many factors that should be considered when choosing a PLC for your system, some of these factors are:
Define Your Application Requirements
For example, if you want to control a conveyor system, you may need a PLC with a high number of I/O points to handle the many sensors and actuators used.
You may also need a PLC that supports high-speed counting to monitor the conveyor’s speed accurately.
Determine the Required Processing Power
If you are controlling a complex process with multiple steps, you may need a PLC with a higher processing power to execute the program efficiently.
However, if your process is relatively simple, you may be able to use a PLC with less processing power.
Choose the Appropriate I/O Modules
For example, if you are controlling a process that requires temperature monitoring, you may need analog I/O modules to handle the temperature sensors.
If you are controlling a process that requires motion control, you may need I/O modules that support pulse width modulation (PWM) to control the speed of the motors.
Select a Suitable Communication
Your process will most likely have many components that need to communicate with each other; most likely your PLC will need to communicate with most if not all of them.
You need to make sure that the PLC can communicate with the needed partners in your process.
Consider the Environment
If your PLC will operate in an environment with high levels of dust or moisture, you may need a PLC with a higher protection rating, such as IP67 or NEMA 4X.
If your PLC will operate in an environment with high temperatures, you may need a PLC with a built-in fan or a larger heatsink.
Compare Different PLC Models and Vendors
You may compare different models from vendors such as Siemens, Allen-Bradley, or Mitsubishi Electric (or other brands, in this article we will talk about these 3 PLC brands). You may also consider factors such as the availability of spare parts and accessories, the cost of the PLC, and the level of support provided by the vendor.
These are just some factors that you can consider, depending on your application some of these points can be very critical for your or none at all, also other factors might be of interest.
Examples of PLC Selection for Your Project
Here we will discuss two PLC-based projects for easy understanding of the concept with 3 PLC manufacturers.
PLC Example 1
Suppose that you need to control a process that involves mixing and heating chemicals in a laboratory.
You have the following requirements:
- 20 analog input channels to monitor the temperature and pressure of the process
- 10 digital input channels to monitor the status of valves and switches
- 15 analog output channels to control the heating elements and pumps
- 5 digital output channels to control the valves and switches
- Support for Ethernet communication with a PC for data logging and remote monitoring
- High processing power to execute the control algorithm in real-time
- Compact size to fit in a small control panel
- Ability to operate in a laboratory environment with moderate temperature and humidity levels
Based on these requirements, you could consider several PLC models from different vendors, such as:
Siemens S7-1200
The Siemens S7-1200 PLC supports several channels of analog inputs and analog outputs, as well as Ethernet communication and high-speed pulse outputs.
Siemens S7-1200 has a compact size and a built-in web server for remote access. It is suitable for small to medium-sized applications and has a moderate cost.
Allen-Bradley CompactLogix 5370
The Allen-Bradley CompactLogix 5370 PLC supports also several analog inputs and analog outputs channels, as well as Ethernet communication and high-speed pulse outputs.
CompactLogix 5370 has a compact size and a modular design for easy expansion. It is suitable for medium to large-sized applications but has a higher cost.
Mitsubishi Electric FX5U
The Mitsubishi Electric FX5U PLC can support needed analog inputs and analog outputs, as well as Ethernet communication and high-speed pulse outputs.
Mitsubishi Electric FX5U has a compact size and a built-in web server for remote access. It is suitable for small to medium-sized applications and has a lower cost.
Those 3 PLCs can be used with your application; it is up to you to choose which one will be more suitable. Of course, this is just an example, many more models from these brands and other vendors can be used with this application.
PLC Example 2
Let’s consider another example. Suppose that you need to control a large-scale manufacturing process that involves multiple machines and systems.
You have the following requirements:
- 500 digital input channels to monitor various sensors and switches
- 250 digital output channels to control valves, motors, and other actuators
- Support for multiple communication protocols, including Ethernet/IP, Modbus TCP, and Profibus.
- High processing power to execute complex control algorithms and handle large amounts of data
- Redundancy and fault tolerance features to ensure reliable operation
- Scalability and expandability to accommodate future growth and changes
- Ability to operate in an industrial environment with high levels of dust and vibration
Based on these requirements, you could consider several PLC models from different vendors, such as:
Siemens S7-400H
The Siemens S7-400H PLC supports up to 2,048 I/O points and has high processing power, redundancy features, and support for multiple communication protocols. It is suitable for large-scale applications and has a high cost.
Allen-Bradley ControlLogix 5570
The ControlLogix 5570 PLC supports up to 32,000 I/O points and has high processing power, redundancy features, and support for multiple communication protocols.
The ControlLogix 5570 has a modular design for easy expansion and is suitable for large-scale applications. It has a high cost.
Mitsubishi Electric iQ-R
The Mitsubishi Electric iQ-R PLC supports up to 4,096 I/O points and has high processing power, redundancy features, and support for multiple communication protocols.
Mitsubishi Electric iQ-R has a modular design for easy expansion and is suitable for large-scale applications. It has a moderate cost.
When is a PLC no longer suitable for your application?
Look, even with this many advantages of the PLCs, sometimes a PLC will not be the best choice for your application, here are some examples of when a PLC is no longer suitable for your application:
The Complexity of the Application
If your application has become too complex for the PLC to handle, you may need to consider other solutions.
For example, if you need to control a complex robotic system with multiple axes of motion and vision-based sensing, a PLC may not be the best choice.
Scalability and Expandability
If your application is likely to grow and change over time, you may need to consider other solutions that can be easily scaled and expanded.
A PLC may not be the best choice if you need to add a large number of I/O points or support additional communication protocols.
Specialized Functionality
If your application requires special functionality that is not available in a PLC, you may need to consider other solutions.
For example, if you need to perform advanced motion control or high-speed data acquisition, a dedicated motion controller or data acquisition system may be a better choice.
Cost
Cost is always a consideration. If a PLC is too expensive for your application, you may need to consider other solutions that are more affordable.
What would be the alternative to the PLC?
The alternative to a PLC depends on the specific requirements of your application. Here are a few examples of alternative solutions:
PC-based Control Systems
A PC-based control system can provide a high level of processing power, advanced graphics capabilities, and support for multiple communication protocols.
These systems use software to perform control functions and typically require specialized I/O modules or interface cards to interface with sensors and actuators.
Distributed Control Systems
A distributed control system (DCS) consists of multiple controllers that communicate with each other over a network.
Each controller is responsible for a specific portion of the application, and the system as a whole can provide a high level of redundancy and fault tolerance.
Programmable Automation Controllers
A programmable automation controller (PAC) combines the features of a PLC and a PC-based control system.
These controllers provide advanced programming capabilities, support for multiple communication protocols, and a high level of processing power.
Dedicated Motion Controllers
If your application involves advanced motion control, a dedicated motion controller may be a better choice than a PLC.
These controllers provide advanced functionality for controlling servo and stepper motors and are designed for high-speed, high-precision motion control applications.
In summary, there are several alternative solutions to a PLC, and the best choice depends on the specific requirements of your application.
Examples where a PLC may not be the best choice
Let’s say you are developing a high-speed packaging machine for a food processing plant. The machine needs to handle multiple packaging formats and materials, and it requires high-speed motion control and precision positioning of the packaging components. In addition, the machine needs to collect data from various sensors and cameras to ensure quality control and traceability.
In this case, a PLC may not be the best choice because it may not be able to handle the high-speed motion control requirements and the advanced vision-based sensing needed for quality control. A dedicated motion controller and a PC-based control system may be better suited for this application, as they can provide the necessary processing power and advanced functionality.
Also, if the machine needs to be integrated with other plant systems, such as an enterprise resource planning (ERP) system or a manufacturing execution system (MES), a PLC may not be the best choice. In this case, a distributed control system (DCS) or a programmable automation controller (PAC) may be a better choice, as they can provide the necessary connectivity and data management capabilities.
Conclusion
- PLCs are very critical components of industrial processes and automation.
- PLCs provide many advantages to your processes, including high reliability, better performance, and lower cost.
- Only by choosing the PLC that fits your application can you get these mentioned benefits and advantages.
- Many factors should be considered when choosing the PLC for your application.
- Sometimes a PLC is not suitable for your application, in this case, other solutions should be considered just as DCS, PACs, or dedicated motion control systems should be considered.
If you liked this article, then please subscribe to our YouTube Channel for Instrumentation, Electrical, PLC, and SCADA video tutorials.
You can also follow us on Facebook and Twitter to receive daily updates.
Read Next:
- Types of SCADA System Architecture
- PLC Cold Standby and Hot Standby
- Compare Motion Controller & PLC
- Normally Closed for Stop Buttons
- Timers in Siemens PLC Programming