In this article, you will learn how to choose a PLC for the new project and important factors for the selection of PLC, and their criteria.
You are working on an industrial automation project and you will surely require a PLC for that. Many times, we get confused as to what is the right PLC that needs to be chosen for an application.
Because there are many factors involved and ignoring even any one of them will surely cause a hurdle in the performance.
How to Choose a PLC?
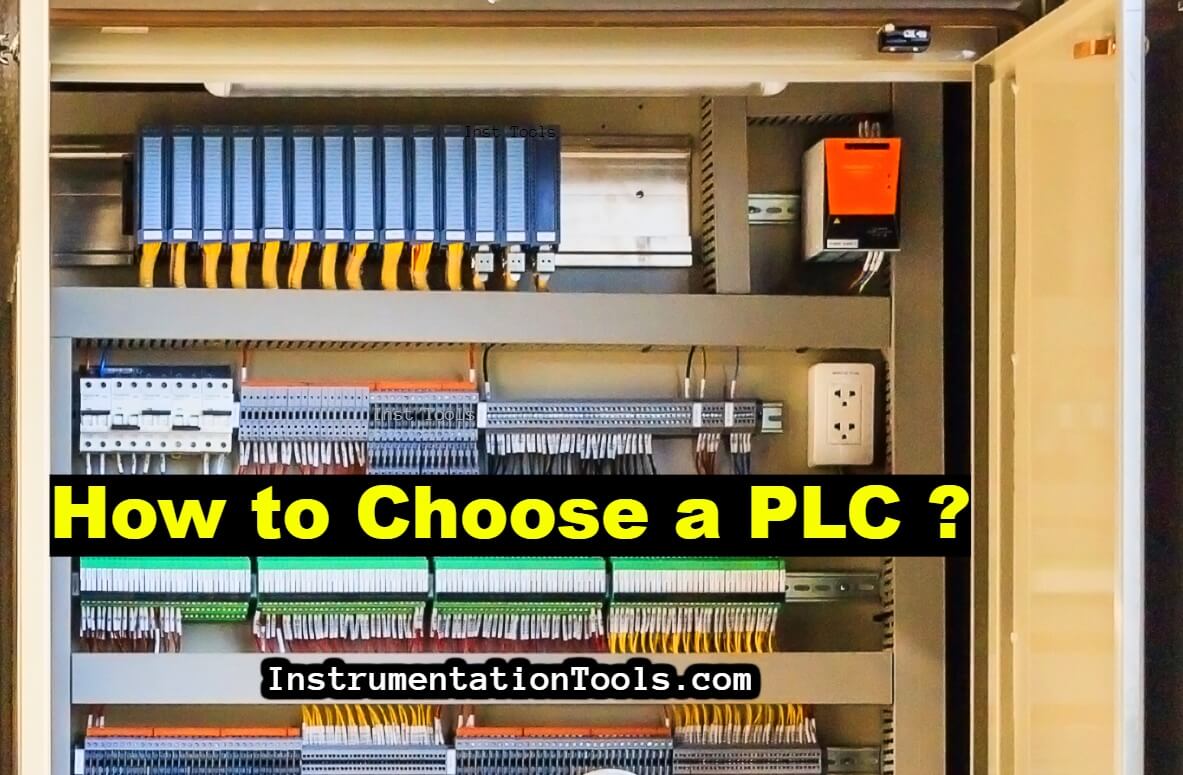
You have set your machine mechanically and electrically; but if you have chosen the wrong PLC for the same, then the design is of no use.
So, it is important to select the right PLC for the application, and for that, it is necessary to understand the various criteria involved in it.
Criteria for Selection of PLC
Let us have a look at the important factors involved in selecting a PLC.
Power Supply
PLC supply can be 24V DC, 24V AC, or 230V AC. Mostly, an electrical panel will have SMPS for the field instrument power supply.
So, depending on the power consumption and SMPS size, you can either use a PLC which requires a 24V DC power supply or a PLC which requires 230V AC.
If you are using a transformer instead which provides 24V AC output, you can choose that PLC which requires a 24 V AC supply. But, just a PLC power supply is not enough.
As discussed, there are field instruments too in the electrical panel; so choose that PLC through which can power it up and also power the instruments according to the voltage required.
Like, if the field devices require DC supply for power, but there is no provision in the PLC IOs for DC supply; then there is no use in selecting a PLC which has the provision of getting only AC input and output for itself and the IO’s.
So, the power supply is an important factor, and choose the PLC seeing all the angles; not the PLC power supply only.
The number of Inputs and Outputs
Depending on the number of inputs and outputs that you have in the system, choose the PLC accordingly which will support that number.
If even the expansion modules are not enough to fulfill the number, then choose that PLC which supports a higher number of IOs by supporting a higher number of expansion modules.
Nowadays, due to the usage of remote IO PLC, where only IO’s can be connected and no program can be written; more flexibility is provided to the user in choosing the PLC and it also gives him the confidence to go with more numbers of IO’s.
Communication Protocol
Along with PLC, you also have other devices in the panel like a field device that communicates on soft protocol rather than hard protocol (digital IO or analog IO), HMI, SCADA, VFD, and some other type of graphical device.
These devices require networking for communication like Ethernet, Modbus RTU, Device Net, Profibus, Profinet, CAN Open, Modbus ASCII, etc.
So, depending on the device that you are using and the protocol that is used in it, you have to choose the PLC accordingly which will support that protocol.
Environment Specifications
Mostly, PLCs are used in ambient temperature and humidity ranges. But, sometimes, the location can be rugged and there can be chances of extreme temperature or humidity.
So, the PLC used must withstand such changes.
Every PLC comes with operating ranges in its specifications, and it also shows the maximum tolerable ranges that it can withstand.
Motion Requirement / Speed of CPU
High-speed applications require high-speed counters/inputs and high-speed outputs (pulse train type) in PLCs. So, choose the PLC accordingly.
Also, check the processing speed of the CPU (scan time). If it is high, then only it can support such types of fast applications.
Also, motion automation requires customized and special types of software libraries for application; so see whether the PLC chosen has such types of libraries or not.
Application Requirements of PLC
If the application demands some special type of programming and the PLC has dedicated libraries for that, then choose that one.
This will make programming easier, as well as cater to your specific demands in running the machine.
Operator Interface
If the machine operator requires the graphical displays to be operated from the PLC itself, rather than going somewhere long near the HMI for critical operation; then choose the PLC which has an inbuilt display in it.
Although you cannot show every minute graphic representation in that, the operator can at least ensure basic operation of the machine from that; like start, stop or reset buttons.
Automation Vendor Support
The PLC that you are using must be ensured that its manufacturer has a large customer support base, proper pricing, and a strong technical team to support the challenges.
These are the general criteria for selecting a PLC. In this way, we saw some standards which must be taken care of before choosing a PLC.
If you liked this article, then please subscribe to our YouTube Channel for Instrumentation, Electrical, PLC, and SCADA video tutorials.
You can also follow us on Facebook and Twitter to receive daily updates.
Read Next: