In this post, we will see the concept of MES in industrial automation.
It is necessary to understand various levels of industrial automation. There are so many hardware devices, software, IT infrastructure and networking involved; that it is a must to co-relate things between them and understand what the difference between them is.Â
Suppose you are working in an office and are not aware of the level of the various employees. This will hamper your knowledge about the company working and will also not teach you what to speak with whom.
For example, an engineer cannot talk directly to a director. He has to report to his immediate next higher level of team leader.
Similarly, it is important to know what level in industrial automation can speak and co-relate things to the next level. Basically, there are five levels in industrial automation – starting from L0 to L4.
Manufacturing Execution System
In this post, we will see the fourth level (L3). This level is used for planning and operations in a plant. It is a computer management system and can monitor and control multiple SCADA systems.
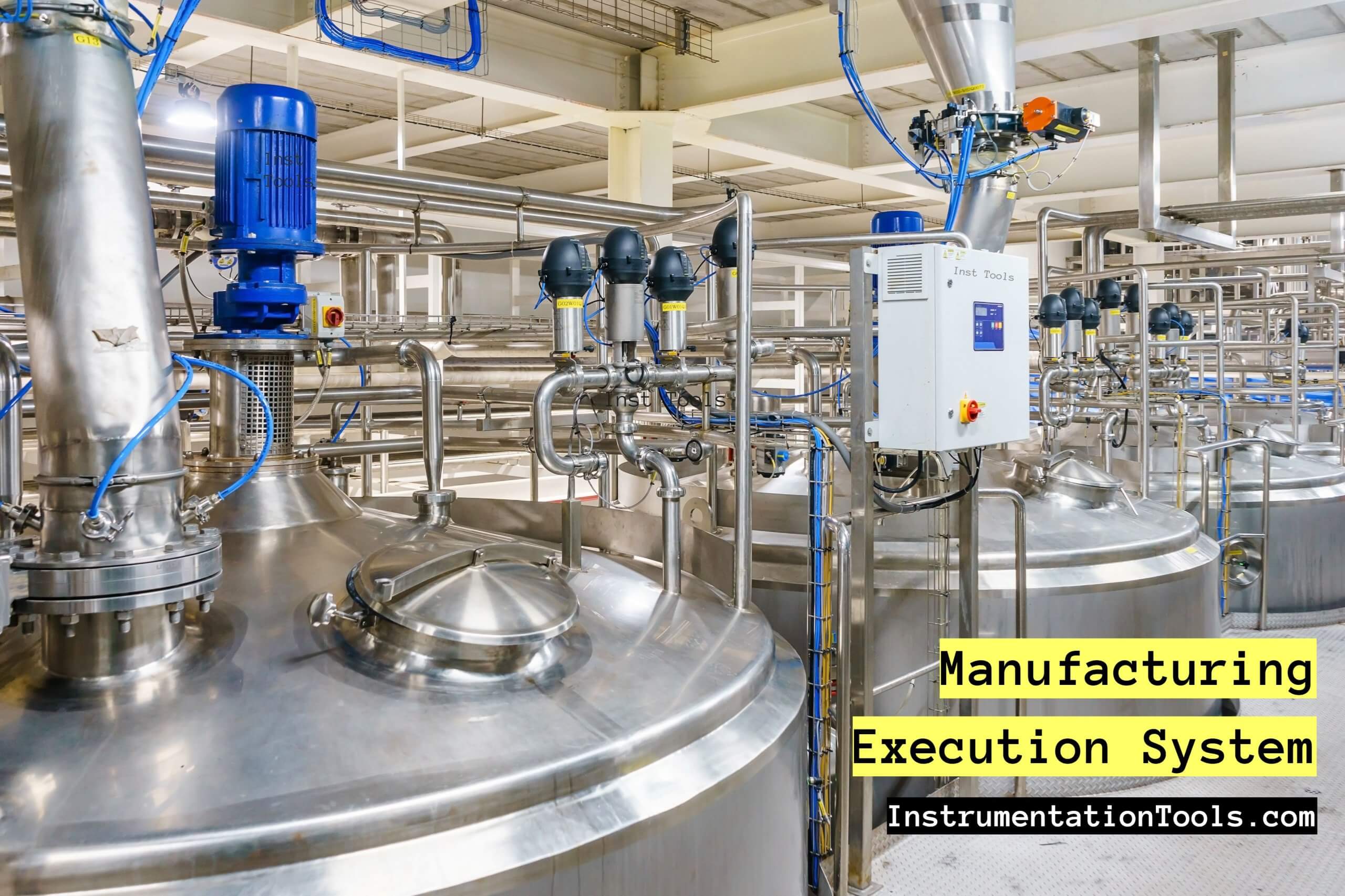
So, suppose there are multiple processes in a plant and it is required to supervise the entire manufacturing process from start to end. This can be done by MES (Manufacturing Execution System).
With this, the user can plan his activities and control manufacturing data and processes. Multiple plants (right from start to end), various vendor data information, equipment information, and planning and manufacturing daily chart can be viewed and controlled through MES.
MES basically works on a large-scale basis and covers each and every manufacturing processes of the plant. Due to this information system, real-time data of all the systems will be tracked and controlled and thus, the production output will be increased.
Core Functions of MES
The core functions of MES are listed below.
- Operation scheduling
- Production tracking
- Process management
- Maintenance management
- Document management
- Data collection and acquisition
- Staff and resource management
- Performance analysis
- Quality management.
MES in Industrial Automation
In today’s modern production world, challenges come in almost all the ways; starting from brisk consumer demands to handling their pressure, technology innovations, raw material handling, employee managing, resource planning, and the most important – short time requirement for production.
Apart from this, if the company is a pharmaceutical, food, and beverage, or biotechnology type, then strict adherence guidelines like 21CFR, GAMP-5, etc. need to be followed; otherwise, the product will not be passed for sale. So, all these challenges make MES a very reliable information software for managing the production activities of a plant.
If you see the working of MES, it’s pretty simpler to understand. The planner plans the production schedule and feeds the data into MES software. His schedule is also based on the inputs provided by the designer, who gives drawings, instructions, specifications, and programs to the software.
Accordingly, relevant information regarding manufacturing is produced. This data is given to the plant in charge or supervisor, who is overlooking the manufacturing activities.
Accordingly, he guides different operators of various machines to produce the material in a specific, sequential, and standard way. The final product manufactured is given to quality assurance and once approved, it is ready for sale; and if not, it is again fed to the production department for rectification.
All these data exchanges are continuously fed to the MES software and it thus gives real-time data of what is happening in the plant and not for manufacturing a product.
You would ask a question that the same activity could be done by SCADA. But, it becomes bulky to monitor so many processes in a single SCADA system, which will overall reduce the efficiency of production.
Yes, SCADA can be used in small-scale industries in place of MES for handling the same task. But, large-scale plants require MES for operation. It also has many advanced features in it when compared to SCADA, for reliably handling the manufacturing activities of a plant.
Advantages of MES
MES works on various inputs like machine breakdowns, employee presence, maintenance times, changing delivery dates, quality issues, availability of transport, availability of quality resources, and alternative parts list. Based on all this, the actual manufacturing process of the plant becomes very easy.
One main advantage is that it reduces a lot of paperwork between manufacturing-related departments; and thus, the planning process is improved to a very great extent due to the use of this automated software.
Popular MES Softwares
Some popular MES softwares are mentioned below.
- SAP ME (SAP)
- MES Software (Wonder ware)
- Hydra (MPDV)
- PHARIS (Unis)
- Simatic IT (Siemens)
- IDBox (CIC) and
- Proficy Plant Applications (GE)
In this way, MES plays a very important role in large-scale industrial automation and obviously, in the fourth industrial revolution (Industry 4.0).