Nowadays, when we talk about the manufacturing market, metal fabrication plays a role in manufacturing precision machined parts with ease. The advancement in fabrication technology has seen an increase in demand for custom parts in various industries.
Each metal fabrication begins with the appropriate methods and materials to produce each unique fabrication design. Sheet metal fabrication involves a broad range of processes that can get confused.
Custom Metal Fabrication Techniques
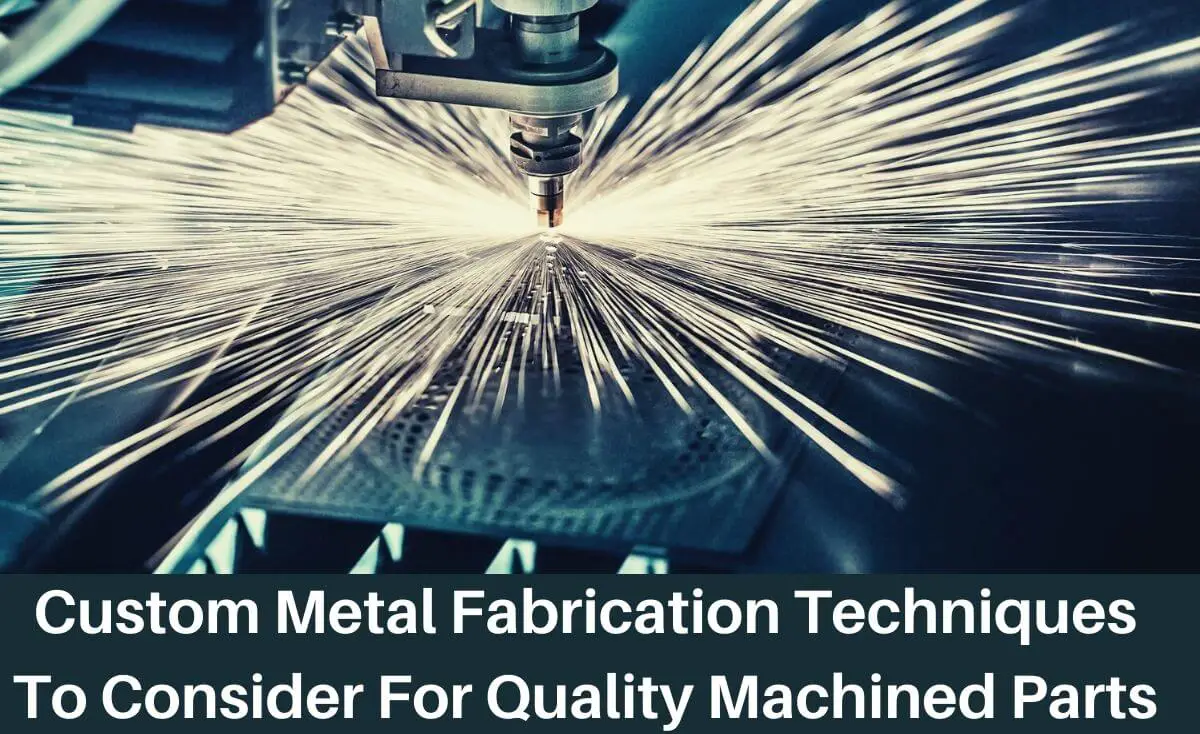
This article comprises the metal fabrication techniques that help to produce quality precision parts with ease.
#1. Make your design crisp
Your fabricator will have a better idea of what you want if you are more specific in your design. It helps to prevent mistakes from occurring as your project progresses from design to fabrication.
Your measurements and dimensions will be the first thing to specify. Ensure these are correct by double-checking them.
In your drawings, make sure to include the following information:
- Tolerance
- The flatness of the surface
- The radius of the corners
- The thickness of the material
- Height, width, and length in total
#2. Cutting the metal
The laser cutting process begins after the machine programmers have to work. Lasers follow the programmed design and cut through the material with ease and precision.
It makes them one of the most accurate methods of cutting sheet metal material.
There are various methods of cutting present in the market manual to power tools to CNC cutters.
Here are several ways to cut metal for your custom fabrication project:
Torching:
A cutting torch uses a hot flame to cut the sheet metal that gets oxidized.
Water jet:
Water jet gets used to cut the sheet metal with a high stream of water. It gets done with the help of a narrow nozzle done with high pressure.
Sawing:
Sawing helps cut metal that is too thick to be cut via other methods. Sawing is a long and intensive process, therefore needed for dense materials.
#3. Metal Bending
When it comes to putting metal together, you have a variety of welding options to select.
The type of metal, the thickness of the material, and your welding equipment all influence which method you use.
The following are some of the most common welding procedures:
- MIG welding
- TIG welding
- Laser welding
#4. Shrink the metal
Some fabrication projects require shrinking metal to smooth out dents.
There are three methods for shrinking sheet metal:
Tucking metal:
This involves pushing the sheet metal’s edges and hammering them into place with a planishing hammer and fork.
Shrink machines:
Unlike the two previous methods of shrinking sheet metal by hand, shrink machines can automate the process. Jaws on this machine grab the sheet metal and squeeze it together, shrinking it to the desired shape.
#5. Finishing Metal
The final sheet metal fabrication step is to finish your project after you’ve cut, shrank, and welded your metal.
Your metal will last longer and perform better if you apply a finish to it.
The following are three finishing techniques:
Sandblasting:
This entails spraying sand and other abrasives at high speeds against your sheet metal.
Sandblasting gives your sheet metal a matte finish and is commonly used to prepare it for coating.
Buff polishing:
This finish gets achieved by buffing the metal’s surface with a cloth wheel.
Buff polishing is likely the technique for you if you want your metal project to shine.
Metal plating:
Chemical baths get used to applying various coats to your project.
It alters the substrate and improves the corrosion resistance and durability of your sheet metal project.
Conclusion
The best way to optimize your custom metal fabrication design is to collaborate with experts. To perfect your blueprint and create a durable, high-quality, cost-effective product, combine your industry expertise with fabricators and engineers.