Instrumentation engineering root cause analysis (RCA) of fire burnt ammonia converter thermocouple (TC) problem threaten entire plant shutdown.
Article Type: | Root Cause Analysis (RCA) |
Category: | Instrumentation |
Equipment Type: | Sensors |
Author: | S. Raghava Chari |
Note: This root cause analysis (RCA) is from real-time scenarios that happened in industries during the tenure of two or three decades ago. These articles will help you to improve your troubleshooting skills and knowledge.
NH3 Convertor Catalyst Beds Temperature Measuring System 750‑1500 T/d NH3 convertors are 1.2 to 1.8 m dia x 20 m tall vessels operating at 220 bars 430o C. 24 Mineral Insulated Duplex Chromel-Alumel Thermocouples (MITC) measure the 3 catalyst beds temperatures.
From now on MITC means duplex MITC for this article. Convertor external crew insert each MITC into the convertor via compression fittings – one for each MITC – welded to the 10” 2500 # RTJ thermocouple flange (TCF, fig 1) bolted to the convertor shell near top.
This avoids welding 24 thermowell taps on this 220 bars 450o C operating high pressure vessel subjected to severe welding codes.
Consider catalyst bed 3 (CB3) corner 1 top temp measurement: A 3/8” Sch 80 bottom end closed and adequately supported incolloy pipe (IP) extends from Thermocouple Flange (TCF, Fig 1) bottom level up to the CB3 top layer.
Convertor inside crew inserts it into the IP till it bottoms. Thus, the IP guards the TC as process thermowells do. IP end cut 4 Nos. 2.5 wide x 30 mm long slots allow the process gas to wet the MITC sheath for enhanced temp measurement sensitivity.
Thus 8-Nos. MITCs measure each beds’ 4‑corners top and bottom temperatures, and total 24 MITCs installed as above the 3-beds. Convertor outside crew terminates the 24 MITCs’ color-coded leads at the terminals of the Thermocouple Junction Box (TCJB) bolted to a pillar 3-m away.
Operators load the 3-beds’ catalysts after the instrument crews complete the TC installation, check, and give catalyst load clearance.
Problem
After 3 years good run, the plant professional fire fighters, trained volunteer fire fighters and others put out the huge fire noticed at the TCF. After fire quench checks identified that Synthesis Gas leaks at the TCF and CFs caused the fire.
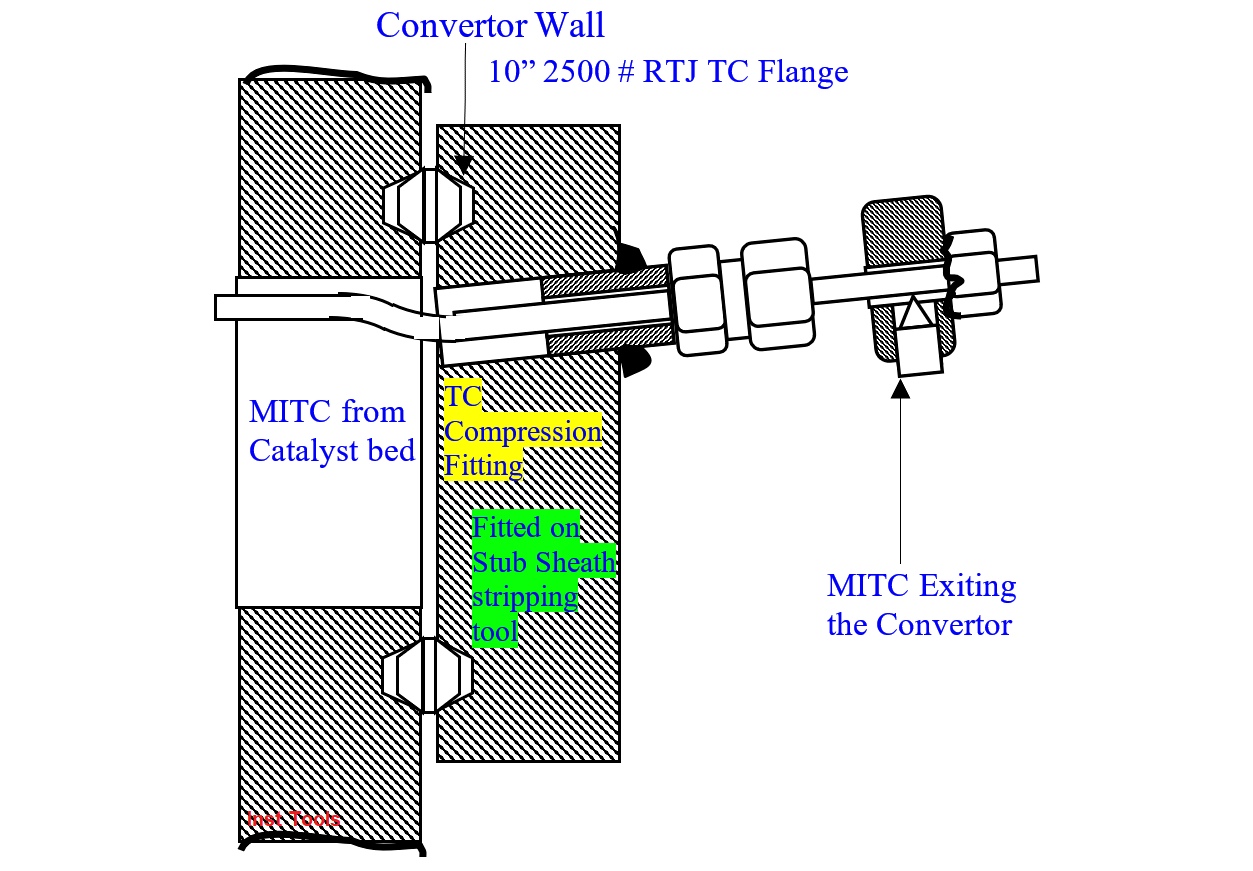
This fire burnt the 24‑Nos MITCs and left 100 to 200 mm long stubs at TCF, and 50 m of the 110 m long Extension Lead cable (ELC) connecting the MITCs to the panel Temperature Recorder (TR) and the backup Temperature Indicator (TI).
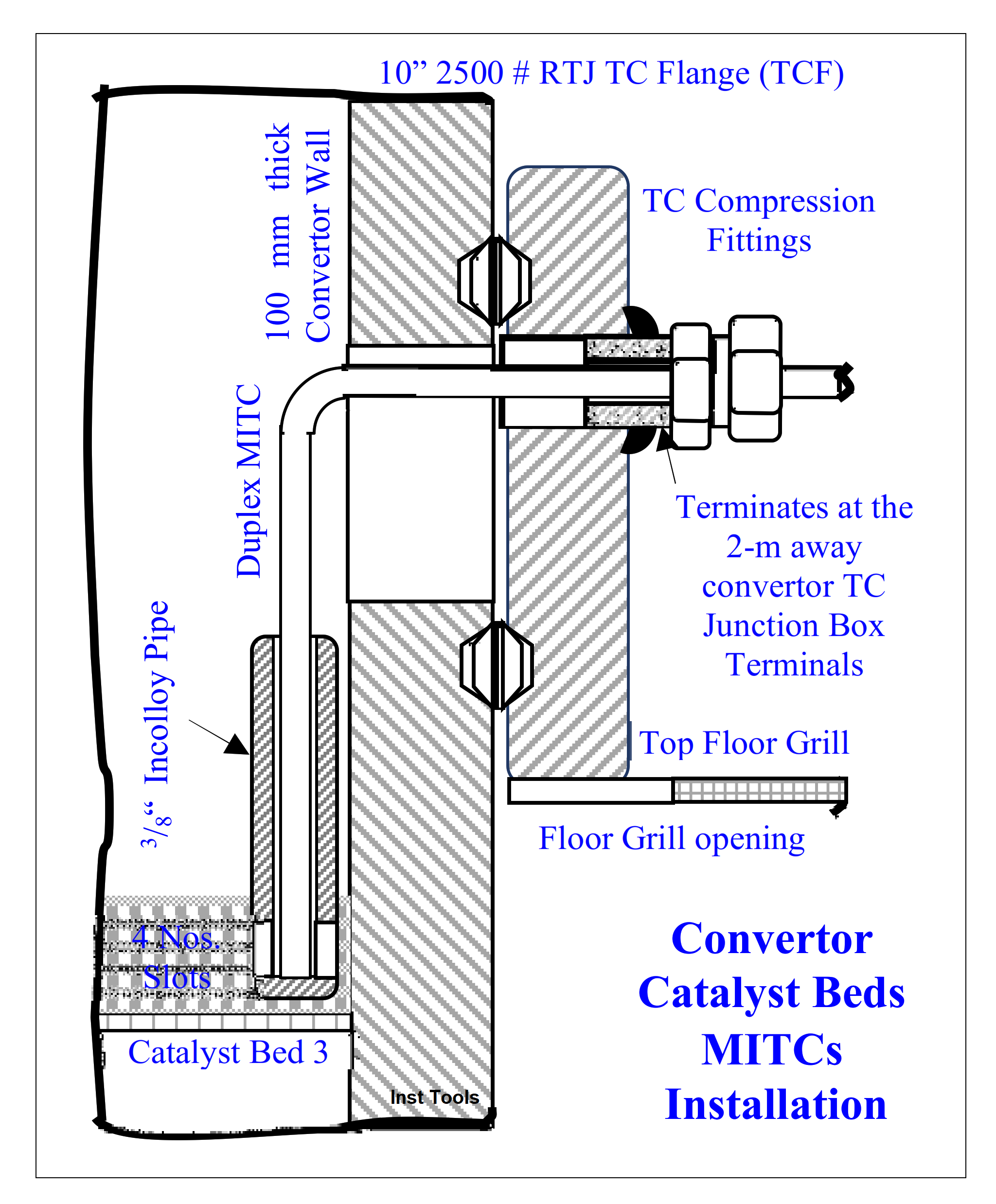
Thermocouple Basics
A German physicist Thomas Seebeck found heating a long homogeneous composition of few metals or alloys wire types generates few mV potential difference aka electromotive force (EMF) between the wire’s ends.
In fig 2, heating wire W1 right end increase its left end mV higher than the right end’s. Using this principle, thermocouple makers make e.g., a PtRh-Pt thermocouple (TC, fig 2) to measure, e.g., molten steel temp in a ladle.
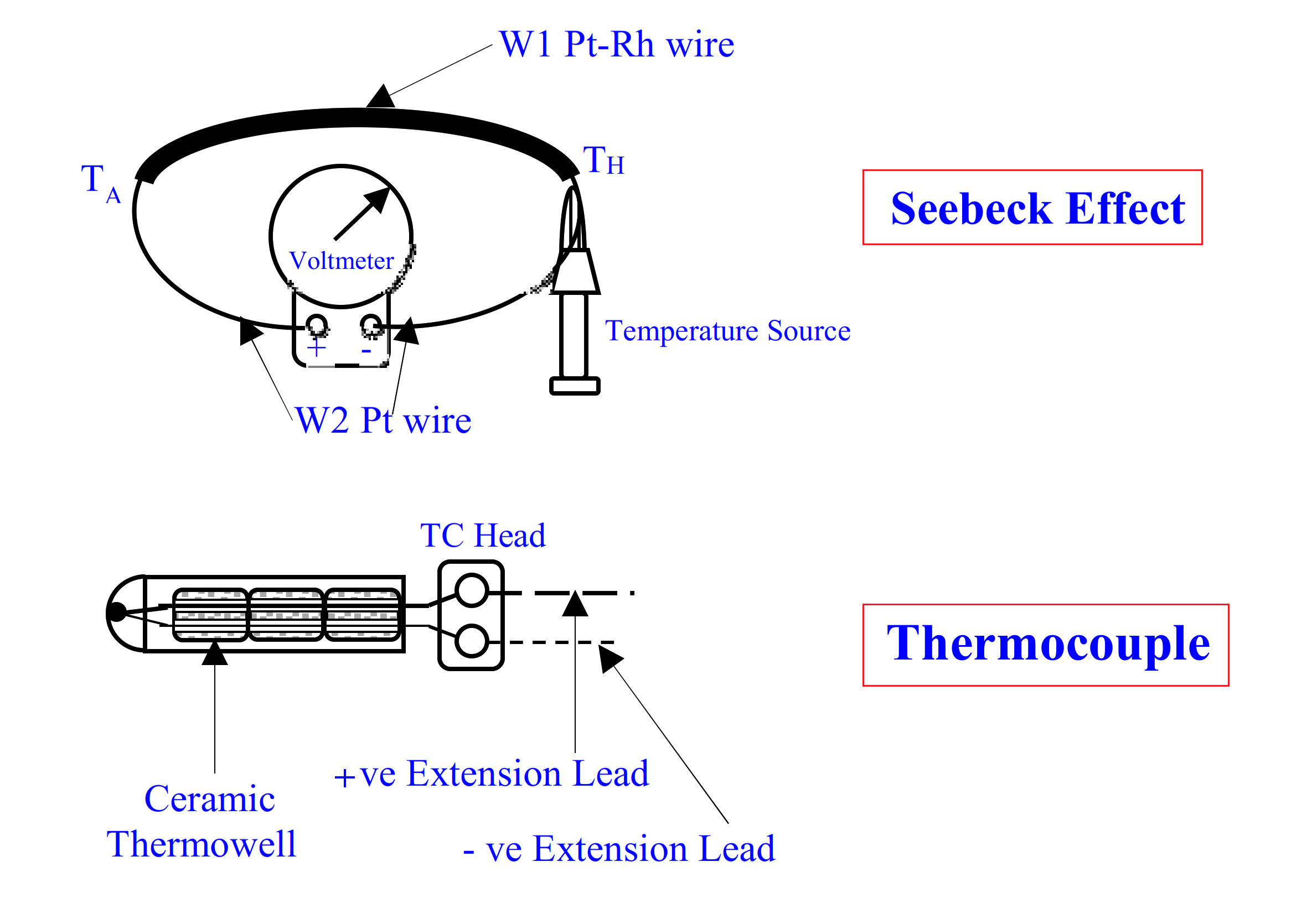
PtRh wire is the +ve thermocouple wire; it generates tabled mV at different temperatures. The negative Pt wire generating much lower mVs than the PtRh-Pt wire for a given ∆t helps connecting the +ve wire hot end to the voltmeter -ve terminal. Note both TC wires shall withstand the process temp.
The +ve wire generates max mV for the measured temp and the -ve wire the least mV to maximize the temperature measurement sensitivity. Thus, two dissimilar wires W1 and W2 combination as in fig 2 constitutes a Thermocouple (TC).
It produces an emf at the TC head (TCH) terminals depending on the temperature difference between the Measuring Junction (M) and the TCH terminals. Usually, the TCH’s all terminals would be at the same temperature – a requirement for the TCs max accuracy.
Extension Leads (EL)
If we connect the head terminals to the remote panel temp indicator (TI), by means of copper wires, industries usual wires, the TI terminals mV = k(TM – TH).
The terminals where the TC wires end e.g., TC head (fig 3). The environs and too close to the furnace/equipment wall situated TH varies considerably within a day and seasonally.
Hence, instead of the copper wires, wires called Extension Leads (EL) connect TCH to e.g., panel TI terminals. EL wires are of less expensive metals/alloys, and have the same thermoelectric properties as TC wires up to 200o C. Obviously, EL wires need not withstand the high process temperatures.
Note TC’s Law of Intermediate Materials validates different metals’ use in fig 3 and 16 TC circuits. The law says “Different metals addition to a TC circuit does not alter the TC generated EMFs, if the connected terminals have the same temperature.
In fig, the TC + and -ve wires connect to head brass terminals, (all different metal / alloys). If the head terminals and connecting wire ends temp are the same the TC generated emf remains the same at (TM‑TH).
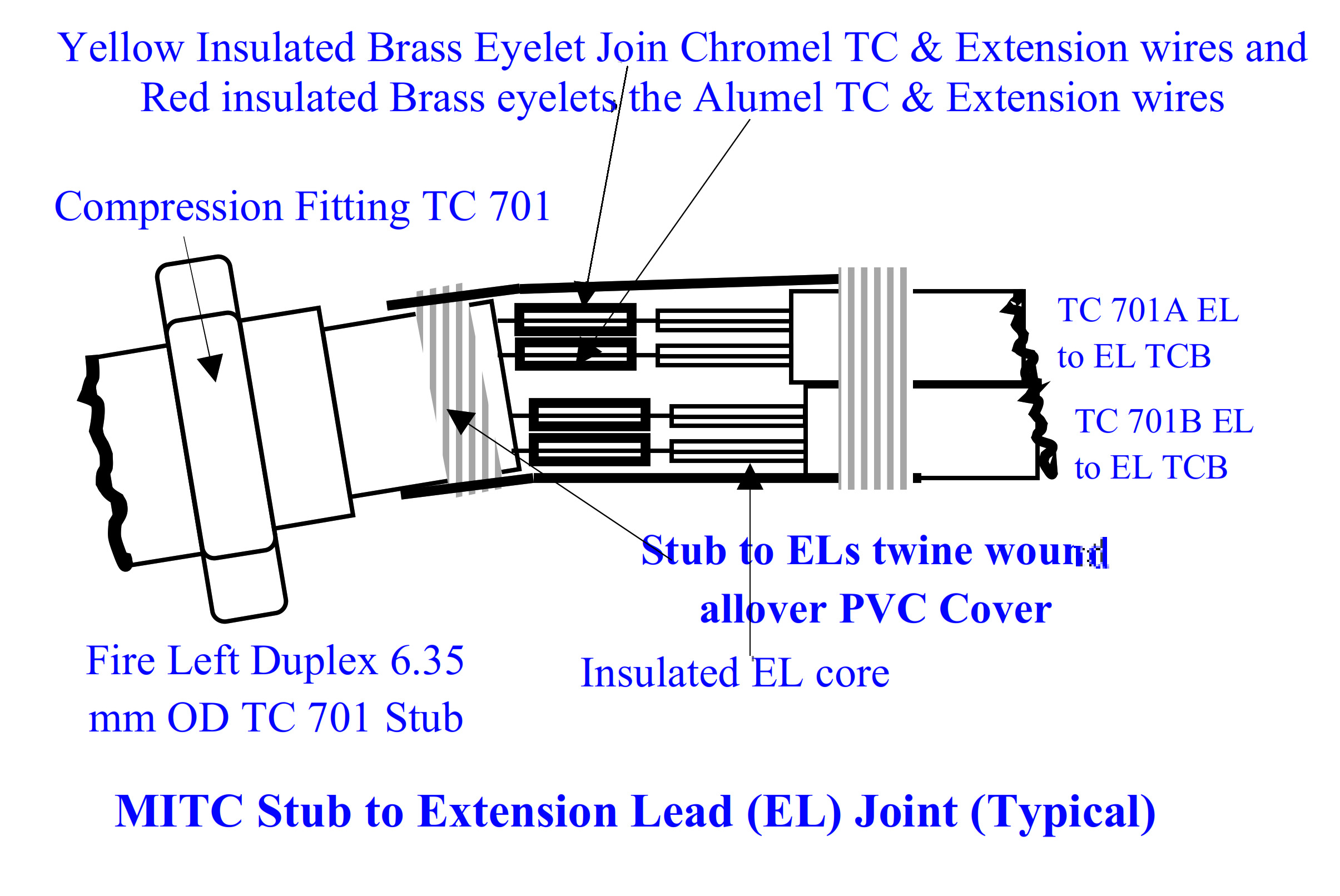
Convertor Temperature Measurement Restoration
Putting the warehouse held 24 nos. MITC set was impossible because:
- TC installation requires convertor catalyst evacuation, an uphill 5‑days shut down task after pre-shutdown several months preparation
- Evacuating oxidizes the ≈ 15 years remaining life high-cost 25 Tons catalyst into a useless product! Its disposal and new catalysts costs run into nearly two million rupees
- Items 1 and 2 threatened the entire fertilizer complex indefinite SD
Hence, the author trusting in God and his crew attempted restoring the temperature readings by joining the TCF stubs to the 3 m away TCJB hook or crook.
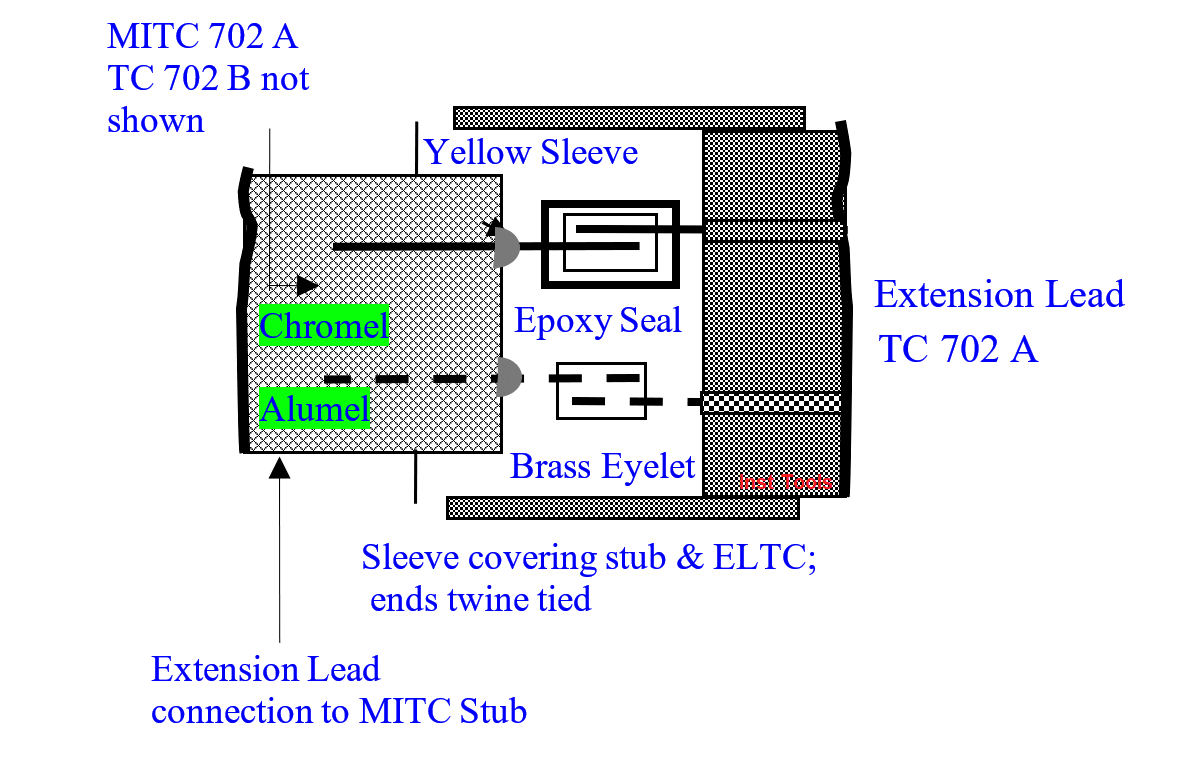
Constraints Faced
Below are the faced constraints
- The fire hardened MITC stubs sheath stripping is field never done task, hence none with the necessary skill and experience, the SS 316 stubs access high difficulties, the near impossible to strip fire hardened sheaths etc. intimidated the maiden attempt crew and the author!
- Yet the author trusting in God, and his crew moved forward – the only available choice – though none was confident and many even discouraged.
Other TC Associated Tasks
An instrument technician wiped the fire quench left water and epoxy sealed to prevent the stubs MgO insulation absorbed moisture shorting the TC wires and rendering them useless immediately after fire quench.
An instrument technician and an electrician team removed the fire burnt MITC lengths from TCF to TCJB piled them neatly for any likely uses. They ran EL lengths from the TCJB and tagged the TC No. on each extension lead cable (ELC) at the TCF end.
MITC Sheath Stripping Training
The author trained four teams – each of an electrician and an instrument technician, a team for each 8‑hrs shift and one standby in case of absence as abundant caution. This leaves enough instrument technicians for the complex’s other needs.
- An instrument technician tightly yellow sleeved 60 brass eyelets red sleeved 60
- They recovered 30-Nos. 1 m long MITC good portions from the MITC lengths pile
- They welded 75 mm long junior hacksaw blade to a 50 long ½” pipe. Called the six made Improvised Sheath Stripper (ISS). Nothing but the ISSs could strip the MITC Stubs’ sheaths at the poor access 24 stubs crowded TCF.
- During practice they deep scored the MITC sheath all around 10 mm away from an end using the ISS
- Holding the long end with a plier, – the only usable TCF crowding stubs stripping tool – and bending the 10 mm portion with another plier broke the sheath neatly
- Handheld screwdriver blade careful taps loosened and dropped the MgO insulating powder and enabled pulling out the cut sheath end without shorting the TC wires to the sheath
- Trial with tube cutters and other tools invariably shorted the TC wires to the sheath and scrapped the MITC.
Other Jobs done during MITC to EL Joining Training
A millwright tightened the TC flange studs, and an instrument technician the CFs – both soap bubble test leaks free. Too often slipped spanner falls, its recovery descends to the 20 m below floor and ascends slowed the CF tightening task ridiculously.
The author twine tying the spanner to the grill speeded up the task beyond expectations, besides preventing persons around injuries.
The convertor still under 100-bars, 200O C, syn Gas pressure enabled leak testing and tightening the TCF studs, and the CFs leak tight.
Stubs to EL Joining
A ‘graduate’ team set to join the stub TC wires to JB1 terminated extension lead wires thus:
- De-sheath TC1 Stub – TC flange map identifies the TCs – as learned while ‘graduating’
- Epoxy seal the de-sheathed stub end to prevent moisture ingress into the MgO insulation – reasons given above.
- Identify chromel wire using an AVO meter and slip a 2 mm dia x 2 mm long yellow sleeve over it, and same size red sleeve on the Alumel wire. An AVO meter identifies the chromel and Alumel wires as the catalyst temp > 100o C
- Inserted the TC 701A stub Chromel wire and EL701A 10-mm insulation bared yellow lead into a brass eyelet and plier crimped the joint tight.
- Likewise, join the stub’s negative Alumel wire to EL701A’s red wire.
- Similarly join stub TC 701B’s wires to EL 701Bs wires Thus, TCs 701A & B connect to the TCJB correct terminals
- After jointing all the TCs a ‘strong man’ applying his max capable force plier crimped all the eyelets to be sure of tight connections for good electrical contacts and accidental open outs
- The crew wrapped a PVC sheet over each stub and the joined 2 EL leads ends, twine wrapped and knotted for the joints’ weather and mechanical protection
- This way the crew recovered 22 out of 24 duplex TCs (44 out of 48 Nos. TCs)
- Crew could not de-sheath < 25 mm long too short 2 Nos. stubs
Other crews completed rest of the connections – see next problem -, the converter was ready for use in just 5 days, and the threatened high-cost catalyst loss and indefinite total plant outage threats disappeared.
The Indian Managing Director hailed this feat telling “Raghav, I repeat EPW’s (E.P. Wells former US GM) words after you recovered the burst pipe destroyed panel instrumentation, “you and your team have reconstructed truck crushed 22 out of 24 eggs”.
Temperature Readings Restoration Benefits
The Temp Readings Restoration Benefits are:
- The 15-years remaining life two million rupees – 1975 costs – high-cost catalyst served its full lifetime
- The indefinite total complex SD threat eliminated
- NH3 production and hence fertilizers production resumed in just 5-days
- The savings from the above run in to tens of millions of rupees
Epilogue
The author now the maintenance manager completed the below pre-SD arrangements to change the unacceptable activity convertor catalyst 15 years after this incident:
- Installed a bought-out water ring blower for catalyst evacuation near the convertor (fig 4), connected power, tried
- He got 20 tall x 20 mm wide V paths cut to a 300 mm long 2” pipe end
- Got it connected to a 50 m long fire hose end and the hose’s other end to the blower suction. This hose will suck the catalyst
- He got 20 m long fire hose connected to the blower discharge nozzle to deliver the sucked catalyst into an all-metal dumper. As the still in reduced state Iron catalyst will catch fire in the environs, choosing all metal dumper was necessary
- He evacuated a created 6 to 10 mm size 15 tons gravels heap to try out the system to be sure of catalyst unloading success.
- Two days before the convertor evacuation, he positioned one of the tech building air conditioning units and the plant largest compressor’s oil cooler near the convertor to deliver near 20o C 200 mm WC inert gas into the convertor. The catalyst unloading team’s leader felt despite holding the convertor under 10-20 mm WC inert gas pressure, air ingress can raise the catalyst temp > 40o C and discomfort the convertor inside evacuating crew. The 20o C inert gas feed will keep them comfortable.
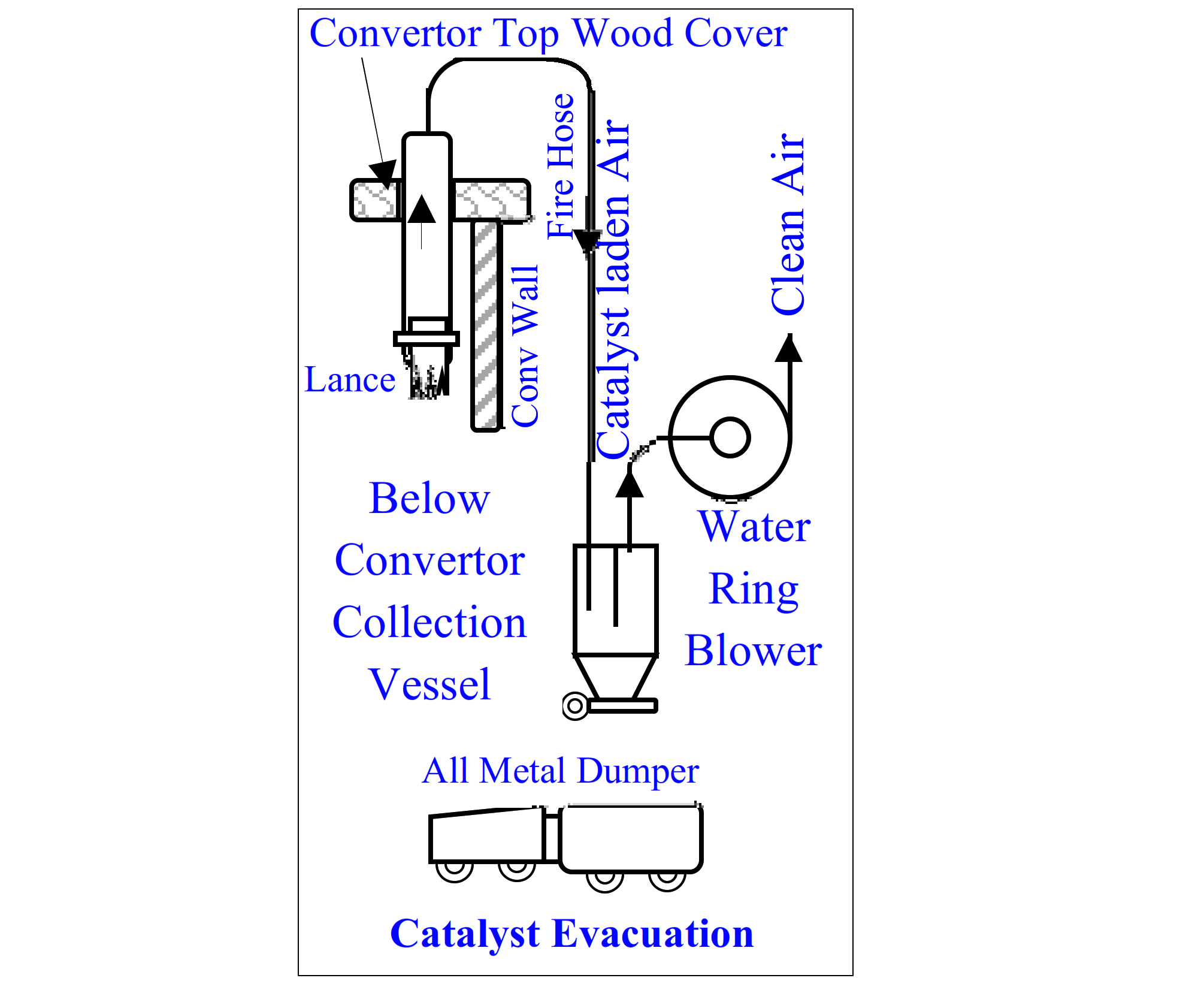
The US Team Evacuates the Convertor Spent Catalysts
Thanks to the well-done and tried out arrangements, the US firm’s technicians using life support systems entered the shutdown (SD) and cooled to 30o C and 10 mm WC inert gas pressured convertor and evacuated the 20 years old spent catalysts in 3-days, perhaps the first time in India.
Conventional methods would have taken 21 days and consumed 100 times more Inert Gas injected with controlled increasing air quantities to fully oxidize the catalyst and evacuate it manually. Problems like lumped up catalysts if any would have extended the evacuation times up to 50% even!
The instrument team put the spare MITCs and terminated them on the field junction box in one day after catalyst evacuation.
The operations and tech services crew loaded 25 tons got from Denmark, pre-reduced, but skin oxidized catalysts in 5 days. Pre-reduction eliminates 21-days reduction times after charging, enormous N2, H2 mixture quantities use and skin oxidation prevents fires during catalyst loading.
An assigned instrument technician ensured the catalyst loaders NOT DAMAGING the MITCs during the five loading days, as replacing damaged TCs is near impossible even catalyst partially loaded, and these must work fine during the new catalyst’s > 20 years expected lives.
Conclusion
This and the other case studies show how instrumentation ties so closely with the plants’ overall activities. Hence, instrument engineers must not only enhance instrumentation knowledge but also increase their overall plant knowledge.
This will not only enable solving many instrumentation problems as the case studies show, but will also ensure instrument engineers’ career growth to the plant’s top management positions.
Author: S. Raghava Chari
Do you face any similar issues? Share with us through the below comments section.
If you liked this article, then please subscribe to our YouTube Channel for Instrumentation, Electrical, PLC, and SCADA video tutorials.
You can also follow us on Facebook and Twitter to receive daily updates.
Read Next:
- Actuator Diaphragm Bursts
- Control Valves Leak Tightness
- Over-Capacity Control Valve
- Control Valve Gland Leaks
- Transmitter Pressure Correction