Control valves are available in different types and shapes.
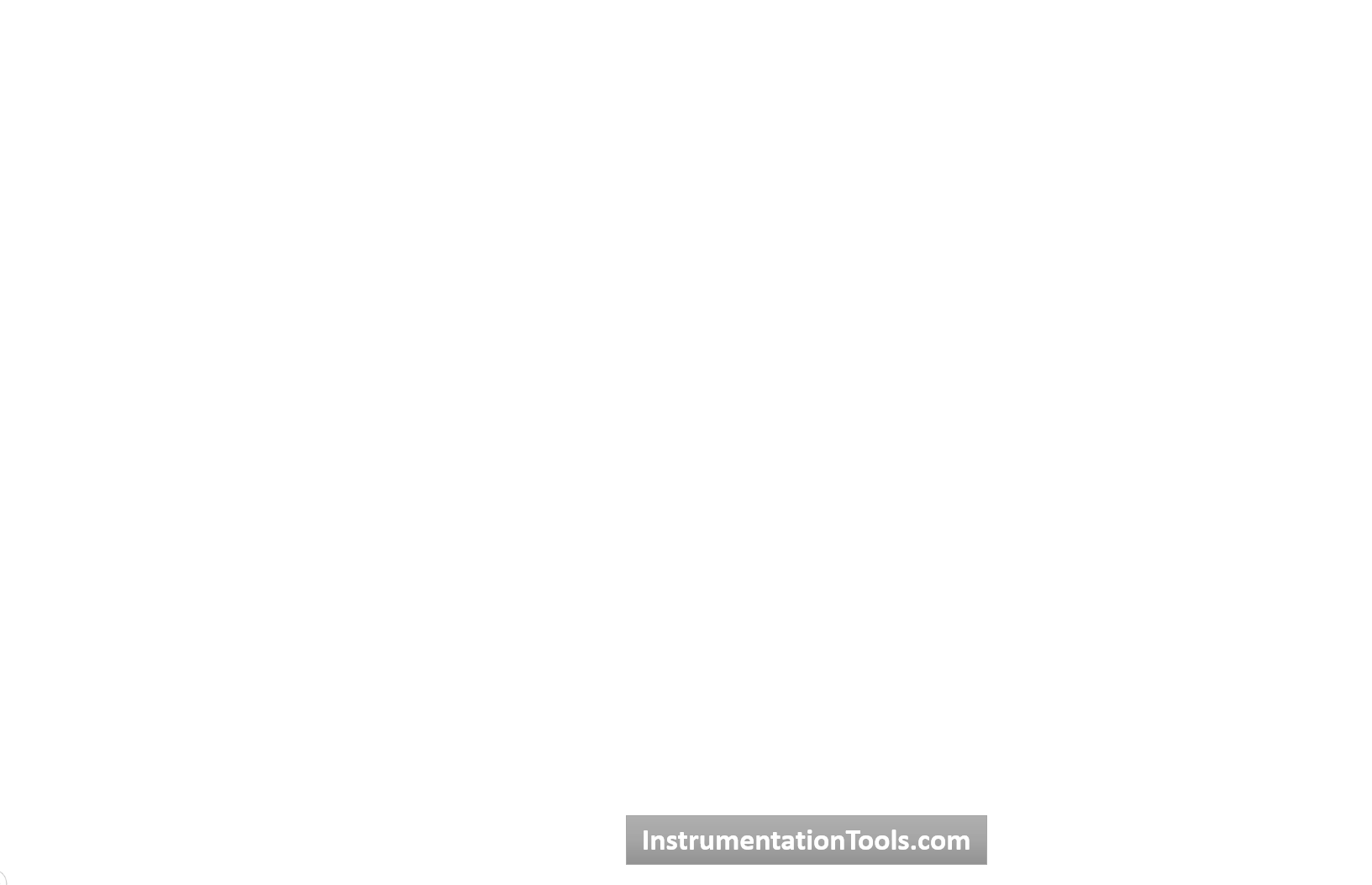
They can be classified in different ways; based on:
(a) action,
(b) number of plugs, and
(c) flow characteristics.
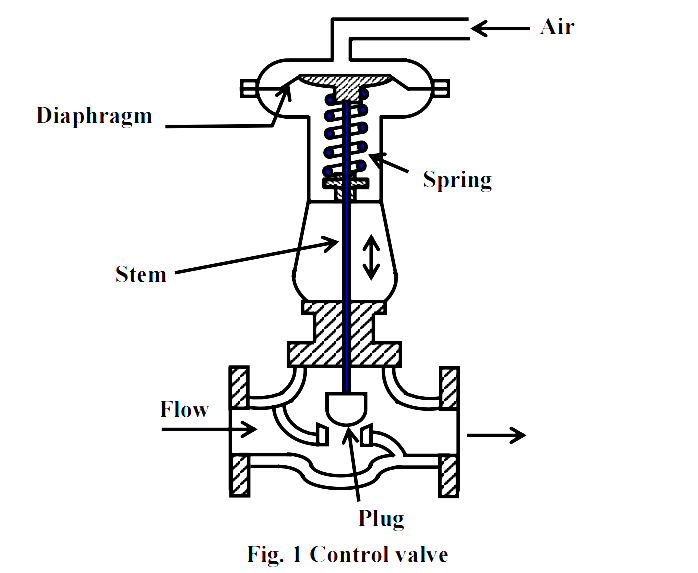
(a) Types of Control Valves based on Action:
Control valves operated through pneumatic actuators can be either
(i) air to open.
(ii) air to close.
They are designed such that if the air supply fails, the control valve will be either fully open, or fully closed, depending upon the safety requirement of the process.
For example, if the valve is used to control steam or fuel flow, the valve should be shut off completely in case of air failure. On the other hand, if the valve is handling cooling water to a reactor, the flow should be maximum in case of emergency.
The schematic arrangements of these two actions are shown in Fig. 2. Valve A are air to close type, indicating, if the air fails, the valve will be fully open. Opposite is the case for valve B.
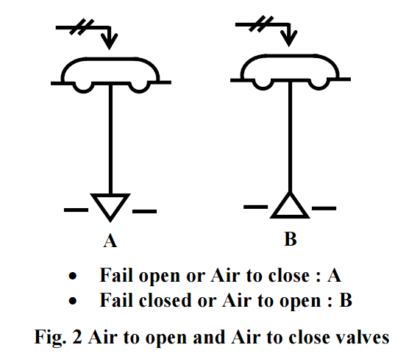
(b) Types of Control Valves based on Number of plugs:
Control valves can also be characterized in terms of the number of plugs present, as
(i) single-seated valve
(ii) double-seated valve
The difference in construction between a single seated and double-seated valve are illustrated in Fig. 3. Referring Fig.1 (and also Fig. 3(a)), only one plug is present in the control valve, so it is single seated valve.
The advantage of this type of valve is that, it can be fully closed and flow variation from 0 to 100% can be achieved. But looking at its construction, due to the pressure drop across the orifice a large upward force is present in the orifice area, and as a result, the force required to move the valve against this upward thrust is also large.
Thus this type of valves is more suitable for small flow rates. On the other hand, there are two plugs in a double-seated valve; flow moves upward in one orifice area, and downward in the other orifice.
The resultant upward or downward thrust is almost zero. As a result, the force required to move a double-seated valve is comparatively much less.
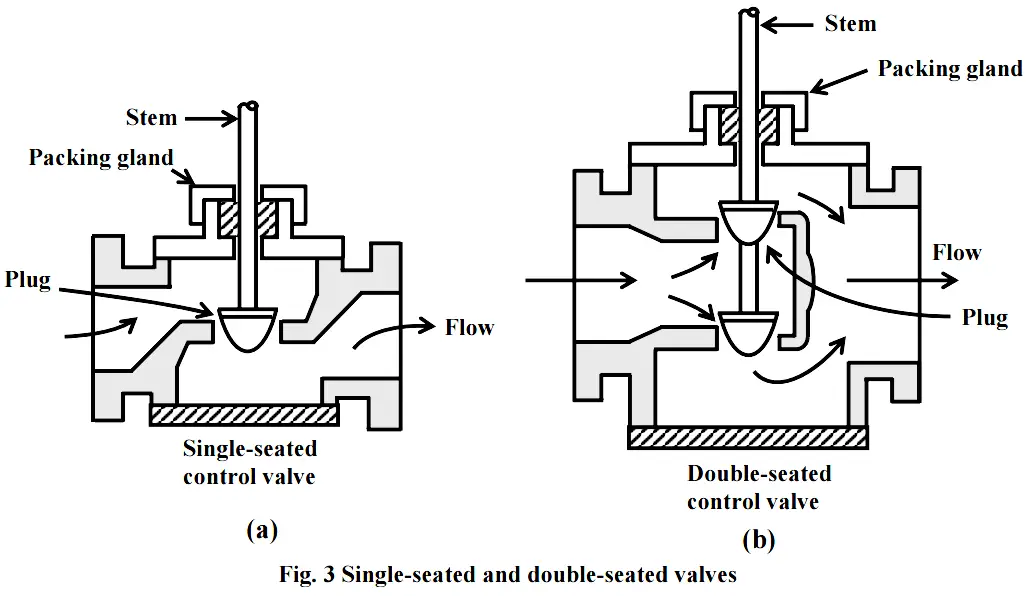
But the double-seated valve suffers from one disadvantage. The flow cannot be shut off completely, because of the differential temperature expansion of the stem and the valve seat.
If one plug is tightly closed, there is usually a small gap between the other plug and its seat. Thus, single-seated valves are recommended for when the valves are required to be shut off completely.
But there are many processes, where the valve used is not expected to operate near shut off position. For this condition, double-seated valves are recommended.
(c) Flow Characteristics:
It describes how the flow rate changes with the movement or lift of the stem. The shape of the plug primarily decides the flow characteristics. However, the design of the shape of a control valve and its shape.
The flow characteristic of a valve is normally defined in terms of
(i) Inherent or ideal characteristics and
(ii) Effective or installed characteristics.
An inherent characteristic is the ideal flow characteristics of a control valve and is decided by the shape and size of the plug.
On the other hand, when the valve is connected to a pipeline, its overall performance is decided by its effective characteristic.
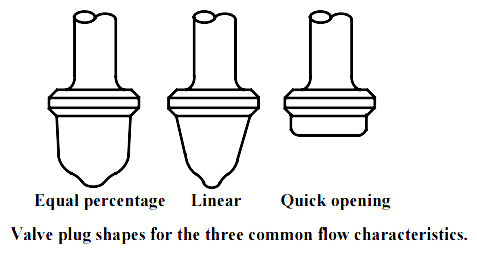
Click Here to read the full article on control valve characteristics.
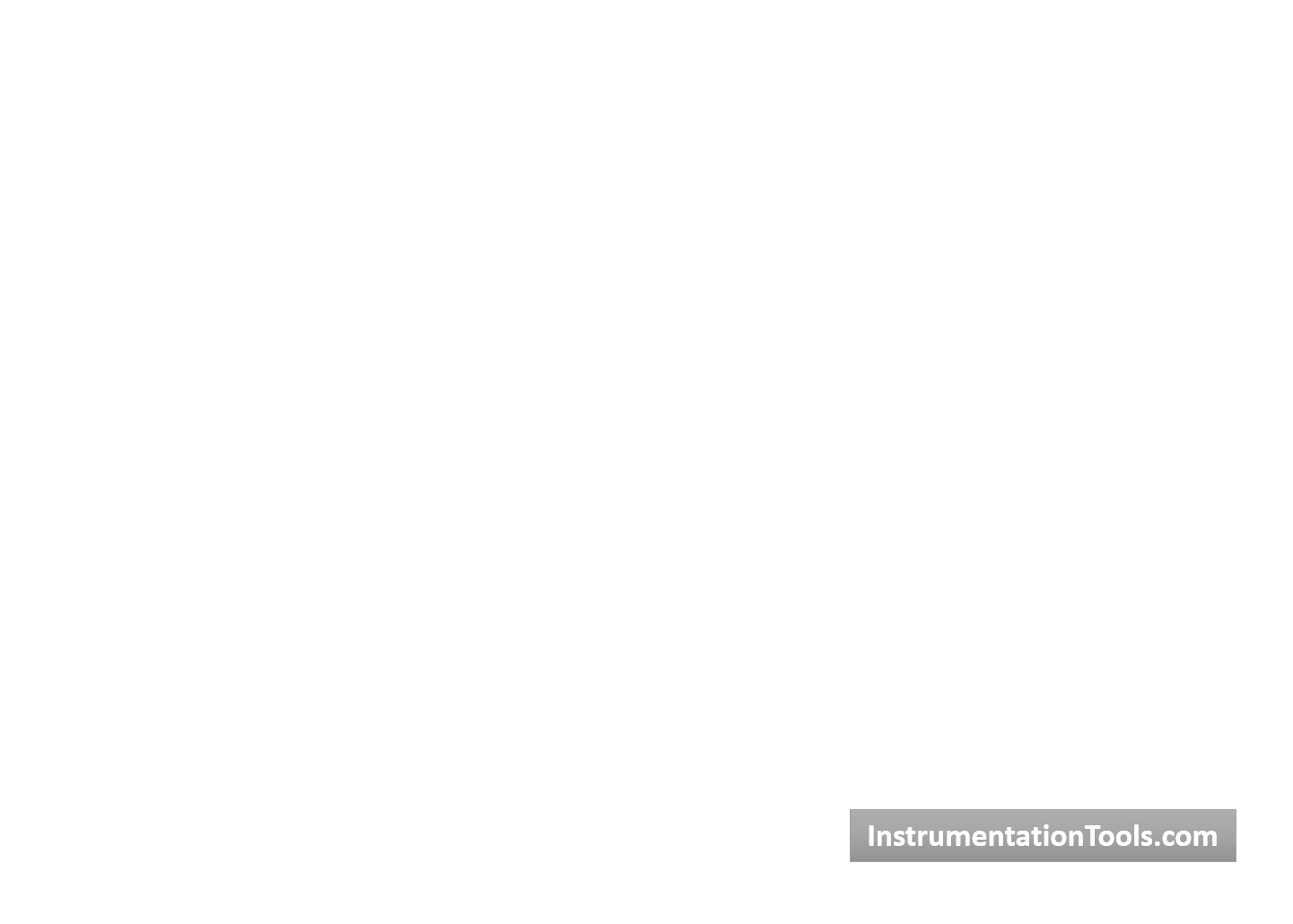
Classification of Control Valves

Read Next:
- Pneumatic Actuators Animation
- Valve Actuator Bench Set
- Pneumatic Directional Control Valves
- PID Controller Action
- Diaphragm Pneumatic Actuators
Dear sir,why we measure control valves cv
Hi.Could you add info about FLDO and FLDC valve actions?Thanks in advance
valuable information, thank you.