Maintenance engineers in industrial processes have many tasks. Regular maintenance, daily checks, and energy consumption monitoring are just a few samples of these tasks.
One of the most important tasks of a maintenance engineer is handling his spare parts inventory.
Spare parts are a critical element of any industrial process, without proper handling of spare parts inventory and management your process is bound to fail at some point in time.
Contents:
- What is a spare part?
- Classification of spare parts.
- What is a critical spare part?
- Points to classify whether a part is critical for you or not.
- Losses due to poor handling of spare parts.
- Tips to reduce spare parts costs.
- Conclusion.
What is a Spare Part?
A spare part is a part of your machine that has a probability of failing or becoming defective and needs to be changed to keep your machine running, like a sensor or a valve; it is also a part of your machine that is consumable or periodically changed like stretch rolls or slitting knives.
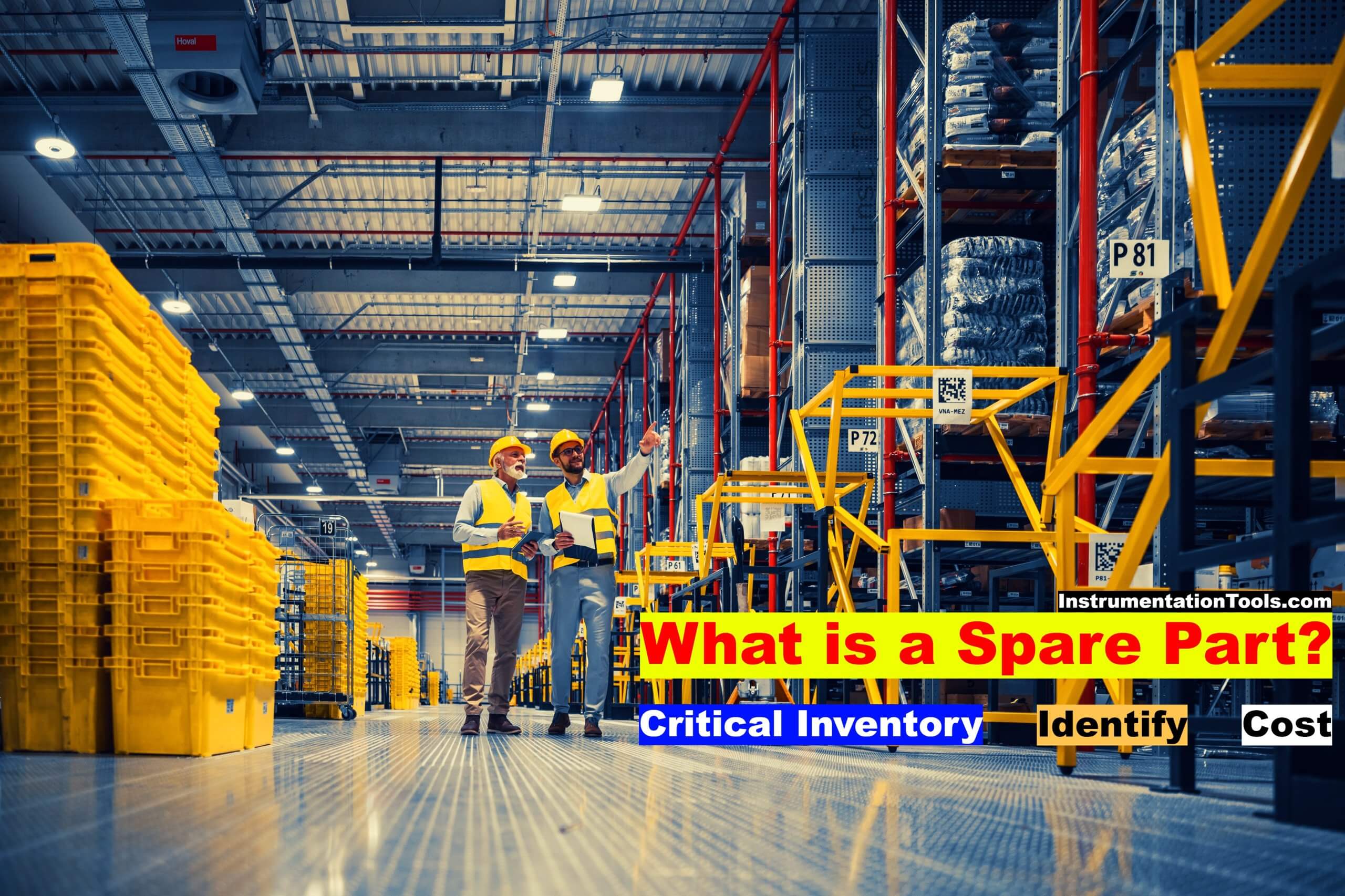
Spare parts are very important for your process because, without the proper handling and management of these parts, your process might be affected by them and even cause downtime for your production.
Classification of Spare Parts
Look, spare parts handling is a huge topic and a crucial element of any management task. But this article will only talk about spare parts from the maintenance engineer’s point of view.
As a maintenance engineer, you probably won’t be in charge of the spare parts warehouse, and that is not what this article is aiming for. But you will have the authority of what parts to order and what to not. And you will be responsible if there are any maintenance delays or failures or downtime increased because of a lack in a certain part.
Based on the maintenance engineer’s point of view, spare parts can be classified as follows:
- Consumable parts
- Non-consumable parts
Consumable Parts
Consumable spare parts that are periodically changed after a certain time, like filters, slitting knives, stretch rolls, and lubrication grease and oils.
Consumable Parts are changed based on certain timetables either because they are completely consumed like knives or stretch rolls, or because their specifications are no longer acceptable like lubrication, hydraulic, or heat transfer oils.
Non-Consumable Parts
Non-Consumable spare parts only changed when defects like sensors, valves, and bearings occurred.
Usually, when one of these parts is defective, your process will probably stop and cause downtime. So, most of these parts would be classified as critical spare parts and need to be available when needed.
What is a Critical Spare Part?
Look, any spare part can be a critical spare part; it depends on, what you are basing your classification upon. Your process manufacturer will usually provide you with a critical spare parts list that your supplier thinks is critical for the well-being and continuity of your process.
That doesn’t mean other parts can’t be critical for your process. It also doesn’t mean you have to buy all the suggested parts.
From the manufacturer’s view, the most critical spare parts will be parts that will cause your process to stop if defective or wearable parts that need to be checked and changed periodically, like Belts and chains.
From your point of view as a maintenance engineer, there are some other points you need to consider to classify a part as critical or not.
How to Identify Critical Spare Parts?
Points to classify whether a part is critical for you or not:
Can you run your machine without this part?
If this part will cause your process to stop, then it should be considered critical and you should have at least one piece of it, depending on how often you would need to replace it.
How frequently do you change this part?
if you frequently need to change this part, for example, lubrication oils or stretch tape rolls, then you should stock an amount equivalent to more than one complete change, because rebuying these parts also have cost, like transportation and changing prices.
Do you get this part locally, or do you have to export it?
If you get this part locally and can easily be provided, then it is less critical than if you have to buy it from abroad, in that case, you need to buy more than one piece, also considering the unit price and cost of customs and shipping.
Exportation duration, does it take long to arrive?
for some parts, you would wait for a long time, because the manufacturer makes it only when it is ordered from him, so you need to consider this arrival time in your planning.
Can you detect/expect this part failure’s pattern before it actually fails?
It would be helpful if you can detect a part’s failure behavior before it actually fails, that way you’ll have the time to take proper actions before this part can cause production to stop.
And yes, maybe you need to stop your process to actually change it, but at least you can perform this change at the nearest planned stop and maybe do some preparations for replacing this part so you can reduce changing time.
Will this part be obsolete soon? Will it not be supported anymore? Do you need to find a replacement?
Industrial processes are designed to run for many years, but that is not the case for some internal parts, like sensors and actuators.
Sometimes manufacturers of some sensor or other parts will decide that they will no longer support this part or manufacture any more of it. In that case, you need to have enough stock to keep your process running or you should try and find a replacement for this part.
Usually, the same manufacturer will provide this replacement, but you need to be aware of such cases, so as not to cause any trouble later.
Some More Points on Spare Parts
Other points that may be considered are as follows:
- Does this part have a lifetime? Does it have a shelf life?
- If this part fails, can you bypass it without affecting safety regulations for processes and personnel until you buy it?
- What is the cost of this part?
- What is the expected time to replace it?
All previous points should be considered by the maintenance engineer to wisely decide if a part is critical for your process or not. And to determine how many pieces of this part you need to have in stock.
Losses Due to Poor Handling of Spare Parts
As mentioned, poor spare part management will eventually cause your process more downtime than it should.
Losses if a part fails and you have this part in your stock:
- Production losses due to downtime.
- Cost of replacing this part.
- Cost of restarting your line again.
Losses if a part fails and you don’t have this part in your stock:
- Increased Production losses due to more downtime.
- The extra cost of buying this part is in a hurry, so you probably will pay more money for faster handling and delivery.
- Your purchasing department probably will work overtime to get this part as soon as possible. So overtime costs.
- Cost of replacing this part.
- Cost of restarting your line again.
It is worth mentioning, you need to know where each part of your inventory is located. Oftentimes, production downtime is increased because you can’t find the part you want; even though you know you have it in your warehouse. Simply because there is no proper handling and storing of parts inside the warehouse.
Again, as a maintenance engineer, you probably won’t be responsible for the warehouse handling, but as a best practice, you need to regularly make checks to your inventory to make sure each part is at its designated place. To avoid losing time searching for this part when in need.
Tips to Reduce Spare Parts Costs
- If you have different parts doing the same functions.
- Test your oils before changing.
- Consider buying a sharpening machine.
- Find the root cause of part failure.
If you have different parts doing the same functions:
If you have two of the same machine, let’s say a batch mixer that has a valve responsible for filling the batching tank, for some reason the two mixers have two different brands of valves, one valve is of TAMSON brand and the other is Danfoss.
Both valves are doing the same task and have the same electrical requirement. Why have stocks of both? Just one of them will be enough, get the idea? Whenever you have a similar case, you can choose one part which will be suitable for both machines and stock only this one.
And this is one way to reduce the spare parts that you have to buy.
Test your oils before changing:
If you have procedures for changing oils (hydraulic or lubrication) in your machine. You probably will be following the manufacturer changing time recommendation. Which is not always the right time based on your operating conditions.
Because usually, the manufacturer will consider some factors that might not be present in your case of usage, for example, ambient temp, operating speeds, running time, etc. all these factors will be chosen as the maximum possible value to be on the safe side.
That means, your operating conditions might be less harsh than the manufacturer’s specs, and you can use that in your favor.
One thing you can do is instead of changing the oil every 3 months as recommended, you can make an oil analysis test one or two weeks before changing time and take a decision based on the test results if the oil characteristics and performance can handle another 2 or 3 months, then you can delay the oil changing for another 3 months.
That way you will change the oil only 3 maybe 2 times in a year instead of 4. Saving the downtime for changing the oil and also the cost of the 2 times you buy the oil.
Consider buying a sharpening machine:
If your process has some slitting knives, for example, paper or non-woven industries. These knives will probably wear after some time and need to be changed, in some cases that can be very expensive if the number of knives is high or the changing period is very often.
In that case, you can consult with your knife supplier if you can sharpen your knives for reusing, and if yes, then maybe you can buy a sharpening tool for your knives and reuse them a couple of times before disposing of them completely.
Find the root cause of part failure:
When a part fails, and after you change this part and re-run your machine, you need to specify the reasons for the failures of this part. Eliminating the root cause will help prevent this problem from happening again and causing more downtime and more parts costs.
There are many ways to reduce spare parts costs, it depends on the process itself, and how much time you invest as a maintenance engineer in finding ways to reduce these costs.
Conclusion
Spare parts handling is a very important task of any maintenance engineer, poor handling of these spare parts will cause more process downtime and extra parts losses.
Proper handling of spare parts includes knowing which parts are critical for your process and how many pieces you should have in stock.