In this article, we will study the basic steps required to follow before creating a CNC program.
When we store a CNC program in the machine, any time saved by bouncing the preparation of programming is lost easily.
Considering the required time in preparing in the proper way helps to ensure the accuracy of the CNC program and efficiency can be improved.
About CNC Turning Process
- If we want to make the machine tool perform production operations according to our requirements.
- Understanding CNC programming is necessary
- Programming a set of commands to communicate with the CNC machine.
- CNC program success is a direct result of preparation before creation.
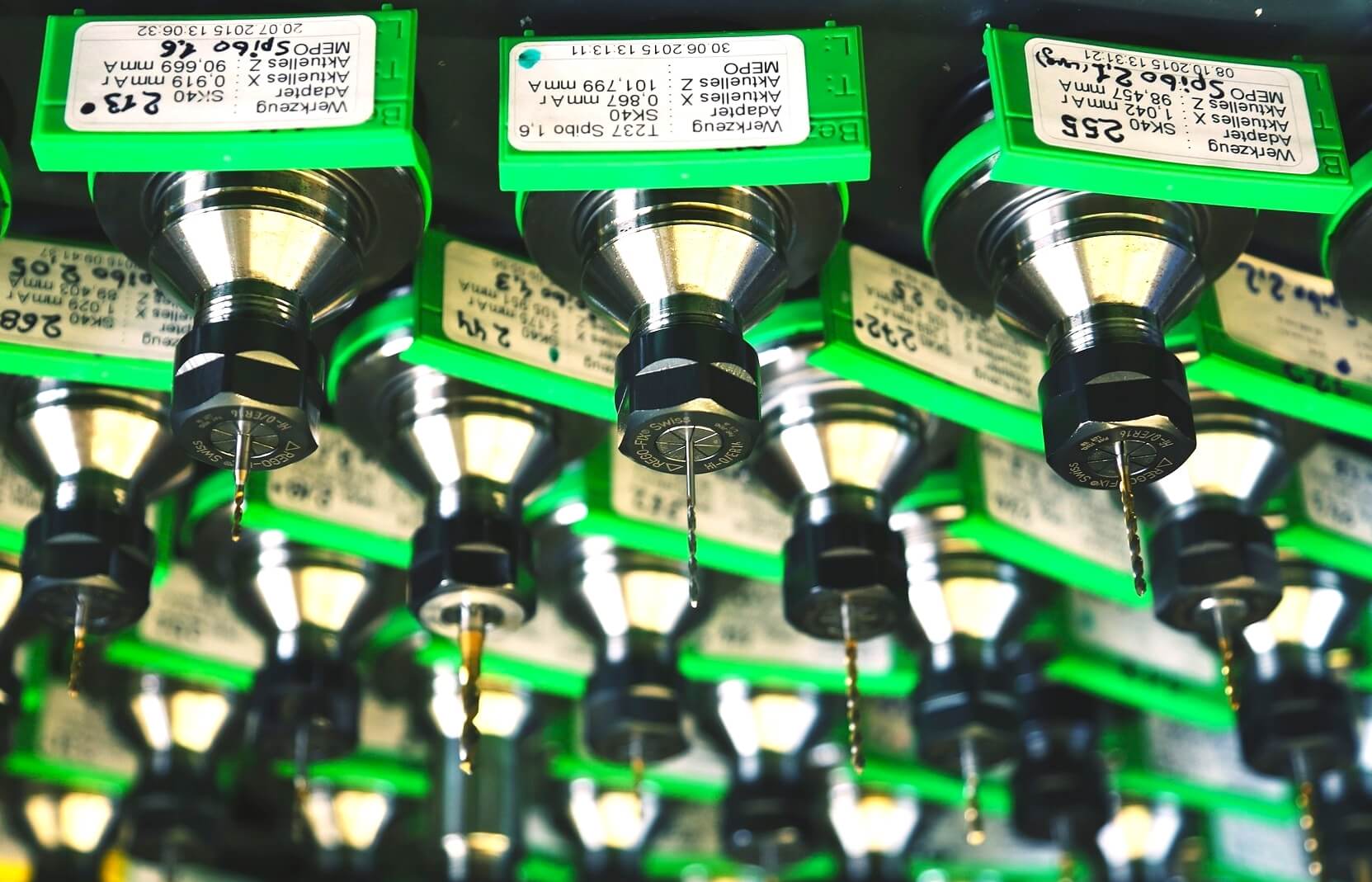
What are the steps to be followed before creating a CNC Program?
Before starting the CNC machine, the below shown complete six planning steps must be followed to generate a new program
1. Determining the required operation to be performed by the CNC machine
- The required machining operations for simple workpieces are determined very easily.
- But as the complexity increases, the difficulty of isolating all work should be made in a given operation.
- Usually, the company’s process routine doesn’t have general instructions, such as “Complete All Milling & Whole Machining“.
- It depends upon the programmer to find all surfaces to be machined.
- Complex graphics with multiple views distributed across multiple pages is not an easy task.
- Identifying machined surfaces by using colored pens and marking working copies of engineering drawings.
- The other way is creating a list of machined surfaces and cutting tools related to them.
- Both techniques can help you avoid missing anything when creating programs.
2. Determination of Process Sequence
- The sequence of processing operations is critical.
- A common thumb rule is too rough machining everything before completing any operations.
- If this rule is violated, an acceptable artifact cannot be produced consistently.
- Forgetting something in a complicated process is easy and quite common.
- The completed form is written in a version of the program, and everyone who sees it can know what exactly the program is doing.
- You can share with others or higher authorities if you doubt whether the process selected is feasible for confirmation.
- We can use it as a checklist during program development to avoid forgetting something.
It is recommended to use a series of action plan forms, the title of which can include:
- Step number
- Instructions
- Cutting tool name
- Tool station number
- Spindle speed
- Feed rate
- Notes or Questions for this step
3. Perform Mathematical Operations
- The required coordinates must be calculated during manual programming by the programmer.
- The idea is to avoid breaking when programming for calculations.
- The cutting conditions such as speed and feed will be calculated if a CAM system is used
- Speed and feed can also be recorded in the schedule as mentioned.
- The coordinates are recorded separately and written on the working copy of the engineering drawing.
4. Fixture Consideration
- A work-piece fixture affects the way you create CNC programs.
- For example the orientation of the fixture on the table, the clamps must be avoided, the positioning surface, and the jaw configuration for three jaw chucks.
- An acceptable CNC program can be created easily only by a clear understanding of how to fix the work-piece in the settings
5. Consider using Cutting Tools
- The cutting conditions are related directly to the cutting tool we are using but they should be recorded in the planning table.
- There may be problems of rigidity or clearance in cutting a tool. We must place the tool as short as possible if we know that the milling cutter performs a powerful roughing operation.
- Conversely, the drill bit must penetrate the casting to reach the point where the hole must be bored.
- During programming and providing installation instructions the points included in the schedule copy must highlight all special considerations.
- At some time we must come up with a component list to make a cutting tool.
- The whole cutting information will be included in the installation manual or documentation.
- Performing this operation before programming may expose a problem that affects the operation that the program must perform.
6. Document Writing
- If the CNC program is created to develop settings, production, and operation documents.
- Programmers and operators do the preparation work when they perform their work.
- You can include the G10 command in the program to retain or enter the program zero assignment into the fixture offset.
Summarize the above-instructed steps to use CNC machines to make components as required.
Though these preparation steps consume more time, skipping them can be rude and wasteful,
Especially, considering the machine downtime or time required to correct the problems should be addressed in the preparation phase.
We don’t have any reason to waste machine time, since there is no real preparation to initiate creating programs.