Safety Instrumented System (SIS) System testing is an important activity to follow the required Quality control achieved for the system.
SIS testing ensures that all planned, designed aspects of SIS are covered.
SIS System Testing
Below are the brief tests to be followed:
- Checking the system behaves as per Safety Requirement Specification (SRS)
- Diagnosing faults, errors, and unexpected behaviors
- Rectifying non-conformance (if any) with the design
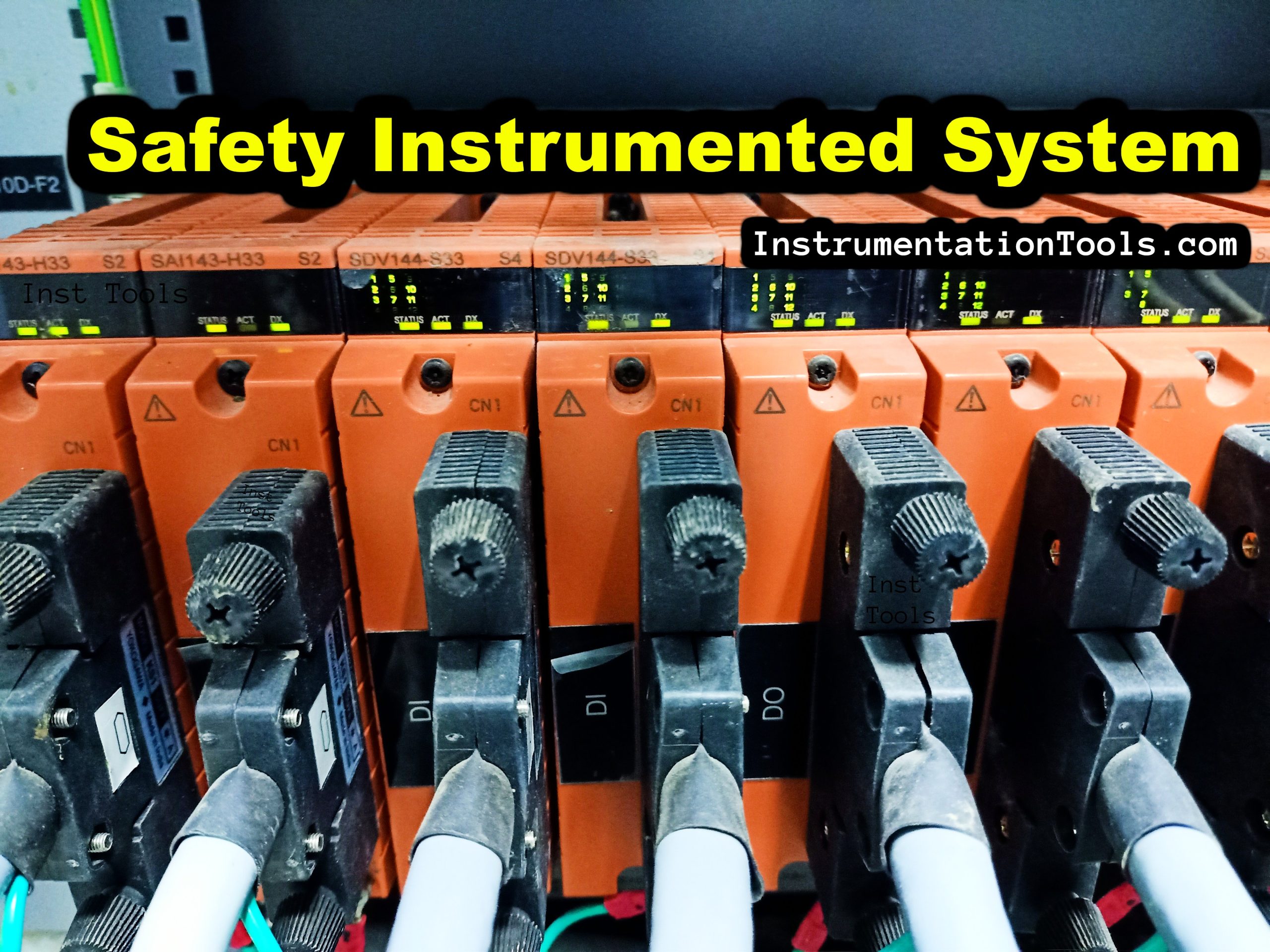
Need for Safety Instrumented System Testing
Testing a virtually error-free system doesn’t consume much time, the project can follow the schedule & avoid delays.
A robust testing plan can help to discover and rectify faults (if any) well before commissioning.
Non-conformance of the SIS system leads to complete re-work of hardware manufacturing, installation, testing, and commissioning.
Engineering efforts will be more and results in higher project expenditure.
Logic solver memory may be a challenge when the new program is created due to non-completion of testing and eventually ending up with major software logic change.
Methods to Improve SIS System Testing
- Various SIS tests (viz. Hardware test) need to be integrated with the overall plan.
- Development of accurate SRS that includes complete design, and test information.
- The project team needs to undergo various checks by different disciplines at the appropriate time as per Safety Requirement Specification (SRS).
- Need to implement strong change management for better SIS delivery and plant operation.
- Testing procedures to be made clear for Commissioning Startup, Operations, and Maintenance teams so that the schedule can be met without delays.
SIS System Testing Methodologies
Plan to be developed with clear scope & objectives for all test needs for SIS system testing.
Below are different tests that need to be performed.
- Hardware Acceptance
- Field device operation test
- Vendor shop QC tests.
- Factory Acceptance Test (FAT)
- Software template review test
- Software Factory Acceptance test / Software Acceptance test
- Code confirmation tests
- Different skid packages acceptance test
- Mechanical completion test at different stages to ensure the construction is done with the best standards.
- Site inspection, Power up tests
- System integrated function test
- Communication protocol test (to Confirm SIS communication with DCS or 3rd party system)
- System Integrated function test.
- Site Acceptance Test (SAT)
SIS System Testing Documentation
System testing procedure document to be prepared upfront before the start of the test.
All the above-mentioned test documents are to be signed off by the testing Engineer with a witness Engineer/Operator/Maintenance supervisor/Technician who is involved in these testing.
All individual testing procedures shall have Passed/Not passed/Comments if any.
Maintain final SRS, Cause & Effect Matrix, Logic narratives/drawings, wiring loop drawing for check ahead of tests.
Master test document to be maintained and any update/ changes per comments need to be signed off by respective personnel.
Fault Rectification & Punch List
With the above SIS, system testing keeps below records for tracking the punch list and closing out as there could be any fault found during the test.
A few punch list review tracking details are as follows.
- Safety functions that have been completed & all open points completed.
- System errors diagnosed and updated.
- Safety functions tested with different combinations (viz. if 2oo3 trip, check all combinations).
- Any software bug identified and corrected.
- Communication protocol tests with different systems/vendor packages through PLC, HMI, and OPC were verified & communications data flow was confirmed within the acceptable time limit.
Conclusion
Thus it is important to perform the SIS system testing in order to ensure that no faults exist in hardware, software application program, and communication with the other systems.
Completion of all such tests during the Design finalization & Engineering phase will assure the project’s successful completion per schedule.
If you liked this article, then please subscribe to our YouTube Channel for Electrical, Electronics, Instrumentation, PLC, and SCADA video tutorials.
You can also follow us on Facebook and Twitter to receive daily updates.
Read Next:
- What is HIPPS?
- SIS Solenoid Valves
- SIS Component Selection
- Automated Block Valves
- SIS Failures and Reliability