It is very important to understand the types of failures in the Safety Instrumented Systems (SIS) and methods to improve the reliability.
SIS Failure Types
There are two types of failures that are important to be considered in the design of SIS and to improve safety instrument & system performance:
- Random Failures
- Systematic Failures
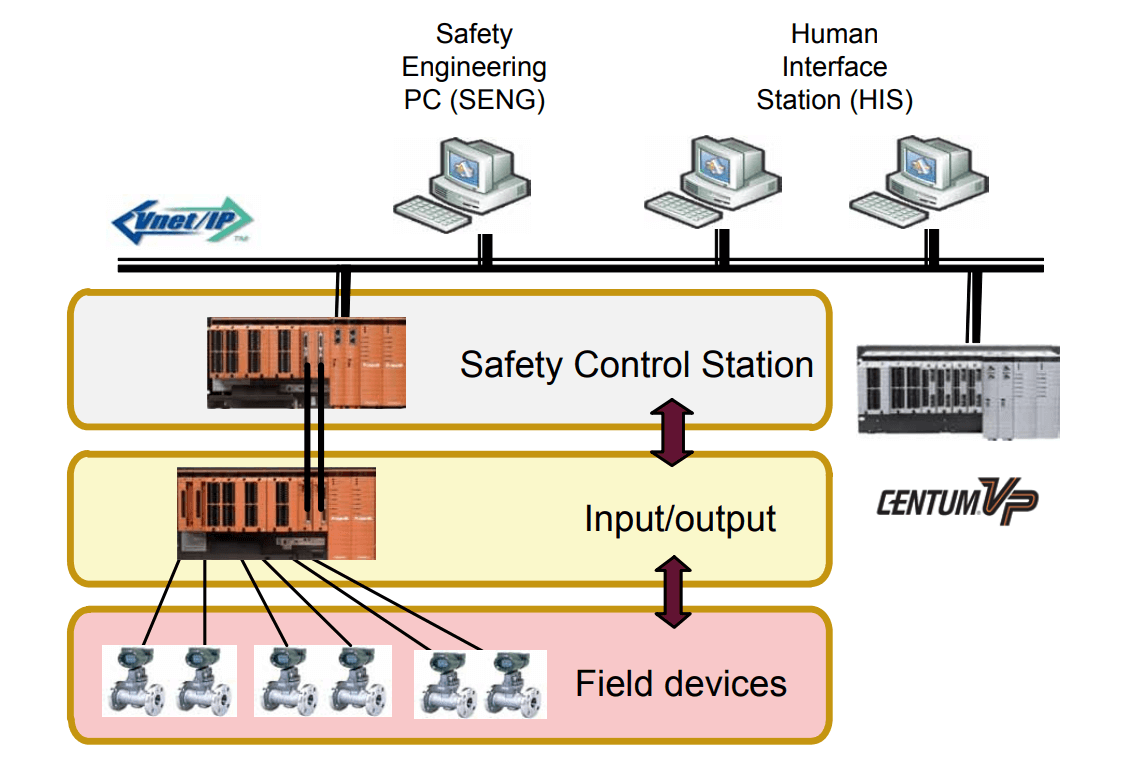
Random Failures
This is a type of failure occurring at a random time, which results from one or more degradation mechanisms (viz. Ageing of sensors, Damaged diaphragm, O rings leak, etc).
Random failures can be effectively predicted with statistics and are the basis for the probability of failure on demand-based calculations requirements for safety integrity level.
Methods to Overcome Random Failures
- Design SIS configuration as redundant (wherever possible)
- Diversify types of instruments to improve SIF performance
- Feedback failure data to Technology Centers for analysis
- Report the failure to Instrument manufacturers about the failure type, incident time, and any issues with the field devices.
- Utilize reliability models and tools where applicable
- Adjust the proof test interval to minimize any failure, or human errors and plan for instrument replacement after a useful life period.
- Follow the recommendations from International Safety certification agencies viz. TUV, Exida, etc.
Systematic Failures
A failure that happens in a deterministic (not in a random way) predictable fashion from a certain cause, can only be eliminated by a modification of the design or of the manufacturing process, operational procedures, documentation, or other relevant factors.
Examples of Systematic Failures
- Systematic failures are not age-related but due to mistakes/errors made in the supplier manufacturing process, design, installation, improper maintenance practices, or unpredicted process changes (flow, pressure)
- Lack of Quality Assurance testing & certification during manufacturing of instruments
- Mistakes in design Specifications, wrong actuator sizing, the wrong material selection including o rings, seals, etc.
- Poor initial installation, improper maintenance or calibration practices
- Configuration software mismatches viz. Range, Time constants
- Poor Management of Change procedures
- Some process Changes (verify technology and capability of the system)
Note: Systematic failures are not included in failure rate calculations
Methods to Overcome Systematic Failures
- Communicate to all applicable disciplines about any change in the process, flow, pressure & temperature variations if any.
- Document and share learning experiences with Maintenance & Engineering teams, Technology Centers so that necessary improvements can be made over the current construction, installation, maintenance, and training practices
Failure Data Analysis
Discrepancies between expected behavior and the actual behavior of the SIS should be analyzed and, where essential and necessary modifications to be made such that the designed safety is maintained.
This shall include monitoring the following:
- Actions are taken following demand on the system
- Failures of equipment forming part of the SIS established during routine testing or actual demand
- Reasons, Cause of the demands;
- Cause of false trips if any.
NOTE: It is recommended to analyze the discrepancies between expected behavior and actual behavior using Root Cause Analysis.
SIS Reliability
Reliability ensures that an SIS element is able to perform a required function over a stated period of time.
Reliability is defined on a yearly basis in % and is inversely related to false trip probability.
Reliability Benefits
- Reliability helps to verify and improve the reliability and availability of Safety Instrumented Systems
- It helps to identify and systematically eliminate any bad actors which call for repeat maintenance
- Reliability modeling helps to identify and reduce “no problem found” maintenance requests
- Reliability studies improve the cost performance of engineering and maintenance.
Reliability Tools
Reliability analysis is used to study the frequency that it will falsely trip the plant.
Ways to Improve Reliability
Evaluate & optimize the occurrence of false trips.
- Add Redundancy and diversity of SIS instruments
- Ensure instruments are protected against potential unrelated damage.
- Include Diagnostics or automatic testing.