Pneumatic temperature transmitter with the sensor. Principle, advantages, disadvantages, and applications.
Principle
A pneumatic temperature transmitter with a sensor of liquid fill or gas fill operates based on the force balance principle.
Thermal expansion of gas or liquid inside the capillary and bulb produces a 3-15 output signal proportional to the measured temperature.
It is functionally similar to a proportional controller.
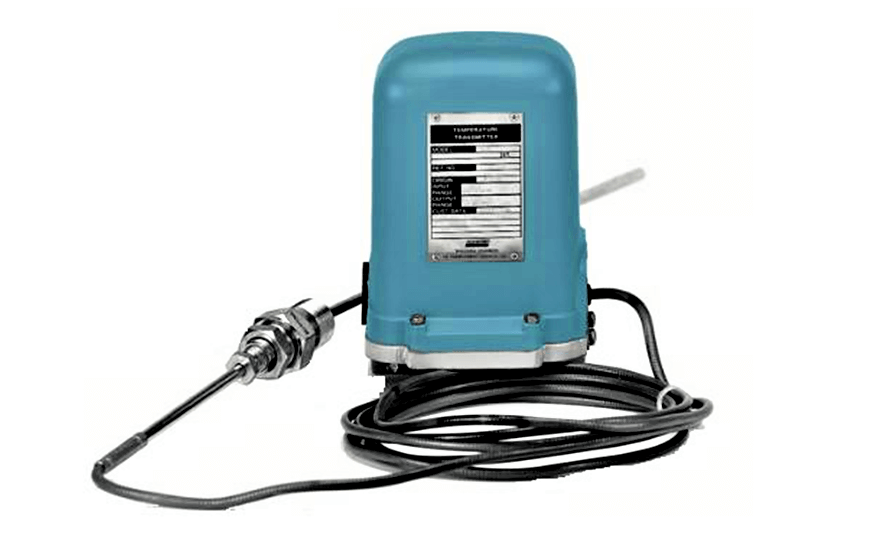
Transmitter Functioning
When the sensor of the temperature transmitter is subjected to an increase in temperature, the increased temperature expands the gas, vapor, mercury, or liquid contained in the sensor bulb and increases the moment of force, tending to rotate the flapper plate in a clockwise direction or right side as shown in the figure below.

The flapper plate now moves near the nozzle and the nozzle back pressure increases accordingly. The pressure is applied to the pneumatic relay unit, increasing its output, and the pressure consequently applied to the feedback bellows.
Thus the increasing the counterclockwise moment of the force due to the bellows unit is sufficient to restore the flapper plate to equilibrium.
The flapper plate is now placed into another position that is slightly closer (less than 0.001 inches) to the nozzle, and the output pressure has reached a new level linearly related to the measured temperature.
In the actual transmitter unit, two additional forces act on the flapper plate.
One of the force is applied by the zero elevation spring. Adjustment of this spring governs the constant force it adds to that supplied by the feedback bellows. This allows a given span of temperature measurement to be increased or decreased.
The other force is applied by the surrounding ambient temperature and barometric pressure compensating bellows.
This force does compensation for ambient temperature or atmospheric pressure variations acting on the gas-filled thermal system. Consequently, minimizing errors caused by these changes.
Advantages
- Do not require electrical power to operate.
- Intrinsically safe.
- Servicing and calibration are very easy as the transmitter consist of few parts. Â
Disadvantages
- Care should be taken while selecting a capillary bulb diameter with an immersion length, diameter, and size of a Thermowell.
- Capillary needs to be protected from mechanical damages.
- Capillary length should be as short as possible for good response.
- Less accuracy rate, slow response compared to electronic sensors/transmitters.
Applications
- Suitable for hazardous applications.
Read Next: