PLC stands for Programmable Logic Controller.
Introduction to PLC
The programmable logic controller is also widely named as a dedicated Industrial computer widely used in the automation industry.
PLC capable of doing all monitor and control functions used to perform in the process control industry.
In comparison to the conventional relay circuit, PLC almost eliminated the heavy hardwiring problem when compared to relay circuits. In addition to the hardwiring problem, PLC is having more advantages over conventional relay-based systems.
Since we mentioned PLC as an Industrial Computer system, it is also having a CPU which is the brain of this advanced control system. But comparing with normal desktop computers, we have more features in PLC.
Since we are going to use this in industry, the controller is designed in such a way that it can able to withstand a higher operating temperature range where normal desktops cannot withstand, added to that PLCs are more immune to noise and resistant to vibration.
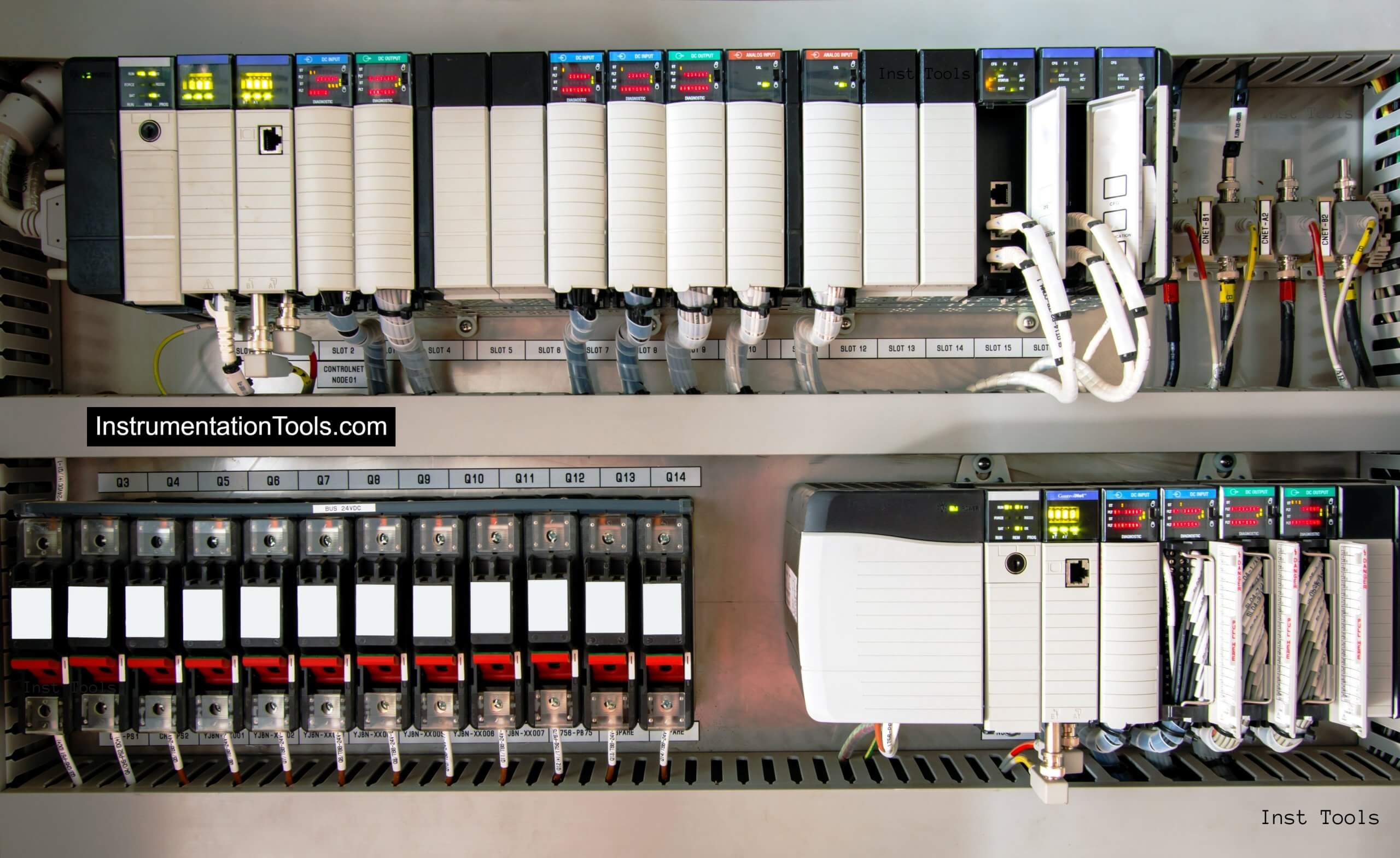
Let’s Split the words in PLC.
Programmable
The word “programmable” in PLC defines that we can able to change the logic with software programming.
Edit or delete the PLC program at any time to change the logic or functionality of a system using the programming.
Logic
The word “logic” is used to design the control loops, implementing required interlocks, and performing the desired functionality as per the required application.
Controller
As mentioned, it is the brain of the PLC. Usually, the controller meant to control the process. By using this part of the PLC only we are achieving the process control concepts in the automation industry.
What is PLC?
The below video tutorial will help you to understand the basic concepts of PLC.
Advantages of PLC
The advantages of PLC are as follows
- Better Reliability
- More Flexible
- Low Cost
- Easy Communication
- Faster Response Time
- Easy Troubleshooting
Better Reliability
When it comes to olden days industrial automation, we used a lot more connecting wires in panel wiring in the relay-based control systems.
This wiring is a tedious job When it comes to troubleshooting the circuit and related problems. It’s very difficult to find out the faulty wire, there is a quote that “Five hours to find it and Five minutes to fix it”. This is really true in relay-based control systems.
But in PLC, the wiring and troubleshooting are very less when compared to olden days relay-based control systems. Since PLC is using the CPU for programming, it’s really easy to upload and download the required logic and thus the reliability of PLCs is very much better than relay-based control systems.
More Flexible
In our college lab experiments, we used to connect the circuits in a breadboard. According to the type of lab, we will collect the circuit components and wire each component altogether to form the circuit on a breadboard.
Relay circuits are almost similar to breadboard circuits. If you want to design/change the logic (circuit) you have to rewire the whole circuit to form the newer one.
But in PLC we can do the logic changes inside a controller instead of changing the hardware/wiring. we have IO ports, just connecting input and output components and write a logic according to the application and download the program using PLC software.
If we have a requirement of changing the present PLC logic, just need to open the software and change the program, download it again to CPU. Hence It’s more flexible when compared to the relay-based control system.
Low Cost
In the olden days, we have relay-based logic systems and they are very expensive in long run. PLCs were designed to replace the relay-based systems.
PLC purchase is like a one-time investment and they save a lot of money when compared to relay-based systems with major impact during the troubleshooting, engineers manhours, and during installation & maintenance.
Easy Communication
PLCs are capable of making communication with other controllers, computers for data acquisition, SCADA, and Front end HMI software.
PLC can communicate with multiple controllers can connect to the hub to form a network to perform some monitor and control applications.
Faster Response Time
PLC is designed to handle real-time applications. Every logic will update the Input/output status in real-time. PLC reads the inputs, executes the desired operation, and writes the outputs accordingly.
In industry usually PLC connects with other controllers and front-end software for human interaction, in that case, also PLC responds faster since its scan time is very less (in milliseconds). While purchasing PLC we can able to check the scan time of PLC for the fastest response.
Easy Troubleshooting
Comparing to relay logic, PLC is very easy for troubleshooting. LED indications are there over the controller hardware to indicate the IO status.
Moreover, with the connected software, we can able to check the input or output status, and diagnostic information also available for identifying the faults in the system.
If you liked this article, then please subscribe to our YouTube Channel for PLC and SCADA video tutorials.
You can also follow us on Facebook and Twitter to receive daily updates.
Read Next:
- Motor ON and OFF Logic in PLC
- Coil Type Timers in Siemens PLC
- Pulse Timer Instruction in PLC
- Master Control Reset in PLC
- Bitwise Logical Instructions in PLC