Invasive devices have transducers that come into contact with the flowing fluid. They are also called ‘wetted’ transducers.
Non–invasive transducers do not come into contact with the fluid and are placed on the outside of the pipe. Intrusive devices protrude into the flow and distort the flow profile, as can be seen in the top two diagrams.
The distortion often leads to mis-measurement by introducing asymmetry to the velocity profile.
Different devices can be intrusive but non-invasive or even invasive but non-intrusive. For example, the ultrasonic meters are both non-intrusive and non-invasive.
The reason non-intrusive and especially non-invasive flow meters are so popular is because they do not protrude into the flow, do not come in contact with fluid, and do not generate any pressure losses.
The below table will give us clarity about Invasive and non-invasive and similarly Intrusive & non-intrusive.
Invasive Type
Sensor will be in contact with the process flow
Non-Invasive Type
Sensor will be mounted externally and there will be NO contact with process flow.
Intrusive Type
Sensor will be placed/mounted in the pipeline but either it can be in-contact or no-contact with the process flow.
Non-Intrusive Type
Sensor will be placed/mounted outside the pipeline but either it can be in-contact or no-contact with the process flow.
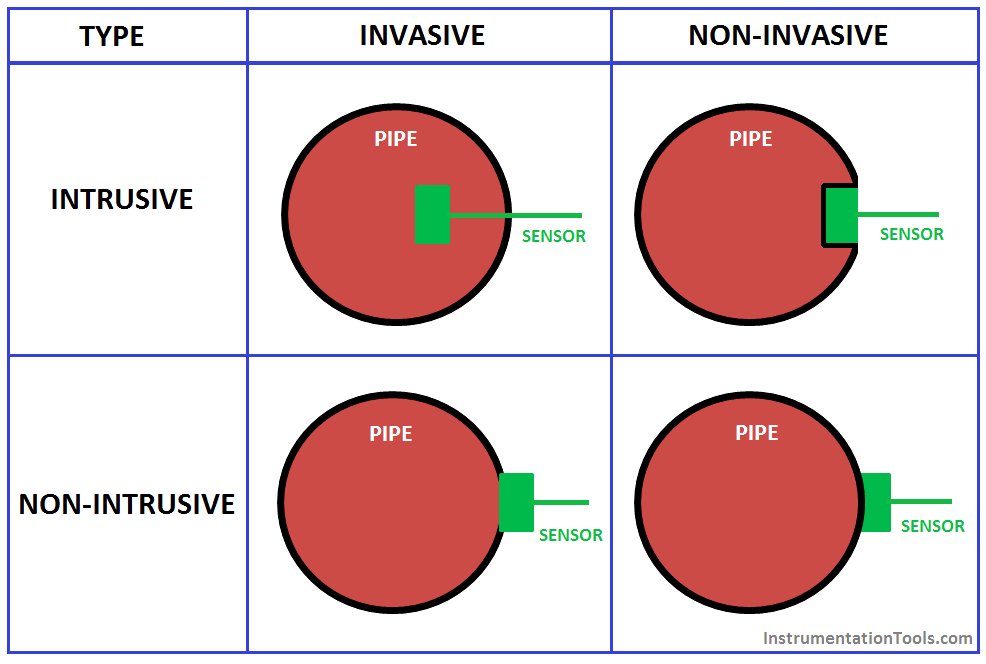
Non intrusive devices do not interfere with the flow profile. No pressure drop is observed meaning that these devices are more cost effective to operate. They are also non-invasive which means they do not come into contact with the fluid being measured.
This is very beneficial when measuring dangerous or corrosive fluids that could damage sensor heads. It also means the transducers can be used alongside heavily fouling fluids and not be affected. This extends the life of the transducers, again saving money.
There is no need to break into the pipeline to install these meters which means they can be installed without shutting down the process. This makes them ideal for use on a number of different lines for verification purposes as they are easily portable. There is no chance of leakage or contamination.
The turn down ratio is the range at which a meter can operate within its stated uncertainty levels. It is written as a ratio of the highest flow rate in its range compared to the lowest.
For a more traditional flow meter such as a differential pressure meter or a turbine meter, the turndown ratio is around 10:1. A non-invasive ultrasonic meter however can have a turndown ratio of up to 400:1.
There are no moving parts associated with ultrasonic meters and hence no wear and tear. A turbine meter may have to be maintained in order to achieve peak performance but this is not the case with non-invasive technology.
This low maintenance means it will continue to deliver a consistent reading for as long as transducers are working. And even if they fail then they can be easily replaced with new ones without shutting down the process.
Reference: tuvnel
If you liked this article, then please subscribe to our YouTube Channel for Instrumentation, Electrical, PLC, and SCADA video tutorials.
You can also follow us on Facebook and Twitter to receive daily updates.
Read Next:
- Inductive Proximity SwitchÂ
- Transit Time Flow meter
- Field Transmitter Principle
- Instrument documents
- Orifice Turndown ratio
simply outstanding
Pliz sir need your help I need interview questions and answers