Tank Level Detection Switches are associated more with alarm initiation and executive response initiation. Unlike the monitoring systems, switches do not give continuous level measurement but are used to alert.
In this article, we are discussing about different types of level switches used for tank gauging applications.
Magnetic level switches, conductivity, and field-effect level switches, and microwave level switches are established level measurement switches. However, they are not appropriate for fuel storage applications and therefore outside of the scope of this article.
Tank Level Detection Switches
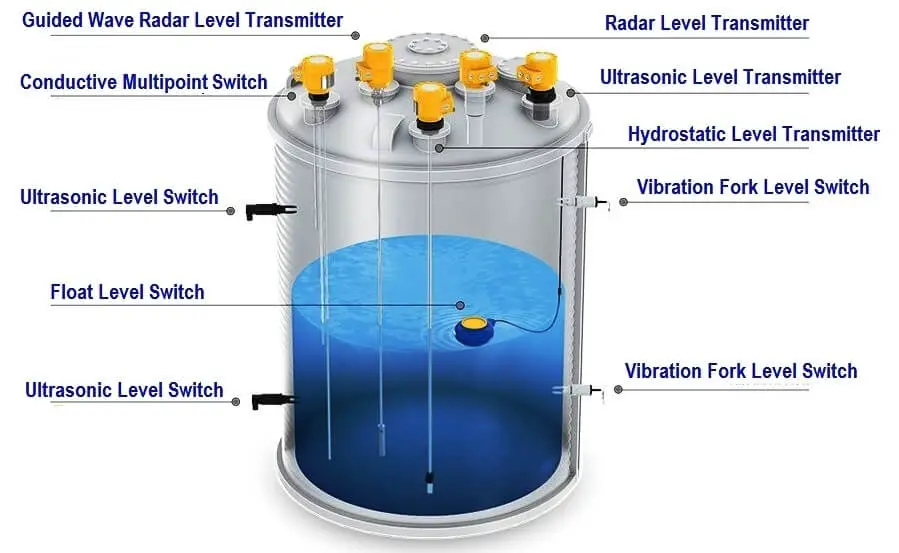
Image courtesy: gfps
Vibration Switch
This type of vibration level switch, also known as a ‘tuning fork switch’, uses piezo crystals that continually resonate at a known frequency in the open air. The rate at which these crystals resonate is affected when it is immersed in liquid.
The principle adopted for this type of switch in tank level overfill prevention is that the piezo crystal is harnessed to two metal prongs that come into contact with the stored gasoline in the tank as the tank level alters.
When the prongs, which are resonating due to the piezo crystal connection, come into contact with the gasoline, the frequency at which the prongs resonate changes. If the detected oscillation varies greatly from the crystal’s natural oscillation frequency, its resonant frequency (accounting for attenuation factors), it is implied that the crystal is exposed to an atmosphere other than air, namely gasoline, and the switch signal activates.
Displacer (Limit) Switch
Displacer switches work by using a spring-loaded weight, known as a displacer, which is held by its own weight on the surface of the liquid in the tank.
As the level of the liquid rises, a steel armature in which the displacer is attached rises into the mechanical switch mechanism. This armature passes a magnet that activates the switch. When the liquid level in the tank reduces, resulting in the displacers lowering, the switching action is reversed.
Mechanical (Limit) Switch
Mechanical switches use a form of lever (plungers and wobble sticks are also used) which moves according to the level of the liquid within the tank.
When the liquid reaches a certain level, the motion of the moving lever contacts the switch. When the level moves away from the activating level, the positioning of the lever causes the contacts of the switch to break apart.
Mechanical switches are continuously operational because they do not rely on any factors other than the level of liquid within the tank.
Optical Level Switch
A light source and detector are used to determine the presence of liquid in a storage tank. This non-intrusive method shines a light source onto the surface of the liquid. The reflection is then detected.
Examples of light sources are light-emitting diodes (LED) or lasers. This type of switch requires the detector lenses to be cleaned regularly, therefore these switches can have a significant inspection and maintenance overhead.
Magnetic Reed Switch
A magnetic reed switch allows or blocks electrical current flow by the magnetization of two metal strips ‘reeds’. The presence of a magnetic field, which is provided by a magnetic float within the tank, draws the two reeds together allowing current flow through the circuit.
When the magnetic float moves away from the reed switch, the magnetic field is removed and they separate. This separation occurs because the stiffness of the reeds forces them back apart. The reeds are normally housed in a glass hermetically sealed tube that attempts to protect them against corrosion due to moisture or aggressive materials.
Novel Tank Level Switching Method
The American Petroleum Institute (API) has presented a method of overfill detection for fuel storage tanks that uses instrumentation external to the tank. This method has been successfully implemented by a reputable fuel storage facility in America.
This system uses three pipes that run parallel to the outside of the fuel storage tank. Of these pipes, the center one is tapped into the bottom of the tank and always has liquid fuel present inside. This pipe is also vented to the atmosphere so that it can be assumed that the level in the pipe is the same as the level within the tank. The two outer side pipes are connected to the center pipe at high and/or high-high level alarm points.
These connections are piped connections between the center pipe and the outer pipes, which will allow liquid flow from the center pipe to the outer pipe when the fuel level reaches the alarm activation point, i.e. the connection pipe point. In the case where fuel overspills into the outer pipes, an alarm activates when the fuel begins to accumulate at the bottom of the pipe.
This method presents many advantages over currently adopted level switching methods because it is non-invasive to the tank, and alarm sensors are only exposed to fuel when an alarm event occurs. However, the center pipe that continually contains fuel must be protected from external damage because if this pipe were to fracture it could become a cause of loss of containment of tank contents.
Problems With Proof Testing HI-Hi Level Switches
A Control & Instrumentation inspector has stated that the most common type of hi-hi level switch used is the magnetic reed type. Proof testing without full knowledge of the switch mechanism has proved unsatisfactory.
One of the greatest shortcomings in the testing of hi-hi level switches is the lack of proper training of technicians or correct effective written procedures for proof tests.
Other problems encountered in proof testing hi-hi level switches can be aspects such as detaching of the float which the switch is connected to, ‘lockup’ where the float belonging to the switch becomes lodged within the stilling well, or even a physical failure of the switch due to wear or manufacture defect.
Read Next:
- Guided Wave Radar
- Importance of Level Measurement
- Capacitance Level Switch
- Float Level Sensor Principle
- Displacer Level Sensor
Dear All,
That very interesting about different type of instruments for monitoring of level.
I have been using a lot of pressure transmitter to measure level with diaphragm filled with silicon in cold or hot liquid and also non diaphragm type with a pig tail fill of water monitoring hot water tanks which are installed at the bottom side wall of the vessel.
Best Regards
What is the level switch that purges a tube with air ( nitrogen) and the resistance of the air is measured. ( air bubbles in the median in the tank)
Max Rudolph, the device you are talking about uses a pressure transmitter to measure the amount of force it takes to make the air to displace the liquid in a vertical tube placed in the liquid to be measured. It provides an output in Inches or mm of height of the liquid being measured. It is normally used on a system to give a fine measure of the final couple of % of a liquids height in a process container.
Bubbler system, or bubble tube level detection as it is commonly known.