This article is about an introduction to Fluid power and Pneumatics, their Advantages & Disadvantages, and their Applications.
Introduction to Fluid Power
The basics of fluid power is to pressurize the fluids, these fluids may be gases or liquids. The fluids are incorporated into the system hardware that is used to generate, transmit and control power in a wide range of consumer and industrial applications. This is because fluid power is used to push, pull, regulate, or drive virtually all the machines of modern industry.
These fluid power systems are used in heavy industries for sensitive positioning for doing precision machine operations. Fluid power is called hydraulics when the fluid is liquid and it is called pneumatics when the fluid is gases. Hydraulic systems use liquids such as petroleum, synthetic oils, and water.
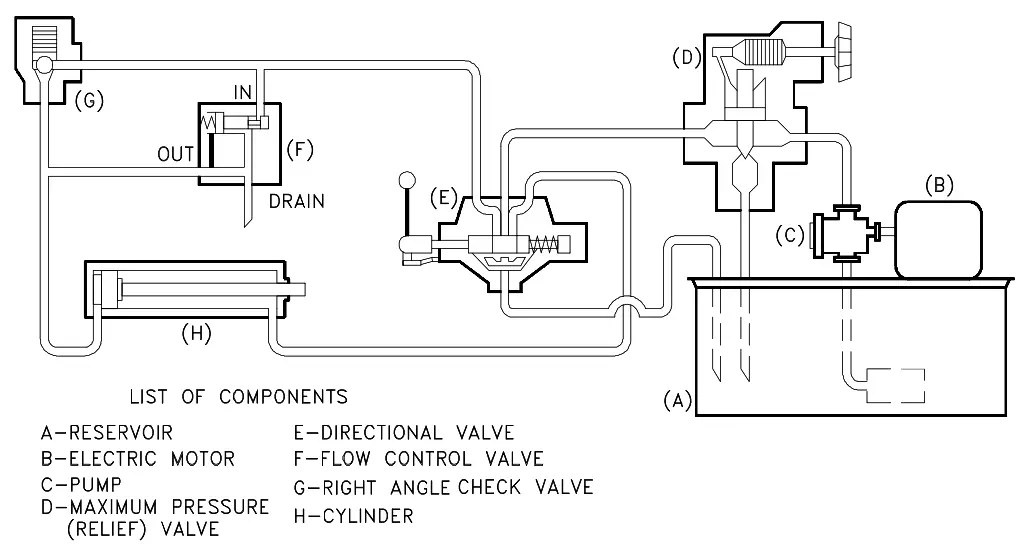
On the other pneumatic system uses air as the gas medium because air is very abundant and can be readily exhausted into the atmosphere after completing its assigned work. Fluid power is one of the three types of power transfer systems commonly used today. The other systems are mechanical and electrical. Each of the systems transfers power from a prime mover to an actuator that completes the work of the required system.
A fluid power system uses the prime mover to drive a pump that pressurizes a fluid which is then transferred through pipes and hoses to an actuator.
Advantages of Fluid Power
The following are some of the advantages of a fluid power system that is applicable to both Hydraulics and Pneumatics.
- It is easy to control the force and torque using fluid power.
- Infinitely variable speed control for both linear and rotary motion
- Overloading the system is possible without damaging the components
- It provides an easy way to control the speed of the machine and machine parts accurately.
- By fluid power system, we can easily stop the linear and rotary actuators with minimal shock to the system.
- Systems easily adapt to accommodate a range of machine sizes and design
- Fluid power systems were easily adapted to external control methods including mechanical, pneumatic, electric, and electronic systems
- The system can easily provide component lubrication.
Disadvantages of Fluid Power
The following are some of the disadvantages of fluid power system which is applicable to both Hydraulics and Pneumatics.
- Higher safety factors are required for high-pressure oil and compressed air or else it leads to serious damage to the system and surroundings.
- In case of bad or weak environmental system design component wear is highly possible
- Leakage of fluid and spills can cause a slippery & messy environment around the hydraulic environment.
- Fire hazards in hydraulic systems may be possible because of using combustible oils.
- Special handling and disposal procedures need to be followed for the hydraulic oil, it may cause damage to the surrounding environment.
- The high cost of compressing and conditioning is done on the air for the use of pneumatic systems.
- Reduced accuracy in actuator speed control in pneumatic systems caused by the compressibility of air.
- Noise level is high in pneumatics when the air is directly exhausted into the atmosphere from the components.
Applications of Fluid Power Systems
Some of the applications of fluid power systems are:
- Industrial- A fluid power system can provide motion control and power transmission to industrial machinery like material handling and assembly, equipment, controllers, and welding machines.
- Aerospace- It is also used in military and commercial aircraft in flight controls, motor controls, brakes, and more.
- Vehicular- Industries like agriculture, marine, and construction use fluid power in systems in vehicles like tractors, air brakes in trucks, cranes, etc.
Introduction to Pneumatics
Pneumatics is the word derived from the Greek which means “breathe”. Real practical Industrial application of pneumatics in production starts in the early 1950s.
The true and worldwide introduction of pneumatics, commenced only when the need for automation and rationalization of operational sequences to increases.
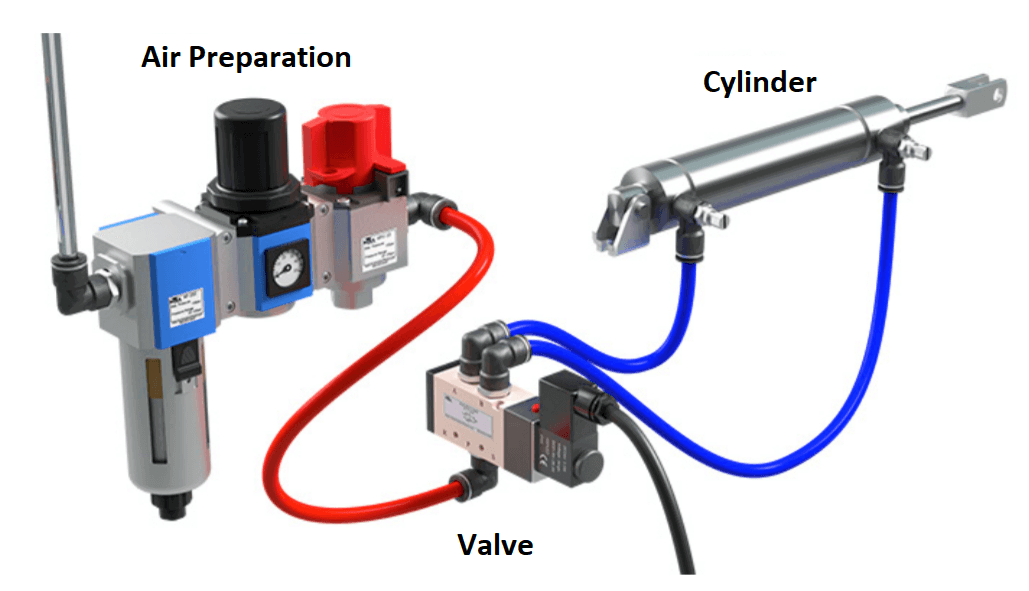
Today mostly all the automation process in the modern industry works with pneumatics. Pneumatics systems use pressurized gases to transmit and control power. Pneumatics systems typically use air (rather than other gases) as the fluid medium, because it is safe, low-cost, and readily available.
Advantages of Pneumatic Systems
- Availability: Air is available practically everywhere for compression
- Transport: Air medium is very easy to transport over long distances through pipelines. It is not necessary to return the compressed air to storage.
- Storage: A compressor need not be in continuous operation. Compressed air can be stored in and removed from a reservoir.
- Temperature: Compressed air is insensitive to temperature fluctuations. This ensures reliable operations even under extreme conditions of temperature.
- Explosion Proof: It offers no risk of explosion or fire, so it does not require protection against the explosion
- Cleanliness: Compressed air is clean since if it escapes through leaking pipes also it does not cause any damage.
- Simple components: Functioning components are in a very simple design.
- Speed: Compressed air is a fast working medium; cylinders have working speeds up to 2m/sec
- Overload Safe: Pneumatic operating components can be loaded to the point of stopping and they are therefore load safe.
Disadvantages of Pneumatic Systems
- Preparation: Compressed air requires good preparation. Dirt and condensate should not be present.
- Compressible: Due to compressibility it is not always possible to achieve uniform and constant piston speeds with compressed air.
- The force is available: Compressed air is economical only up to a certain force requirement. It requires more force to operate heavy-load objects.
- Cost: Compressed air is a relatively expensive means of conveying power. The high energy costs are partially compensated by inexpensive components and higher performance.
- Noise Level: The exhaust air is very loud. We need to fix the extra components like silencers to reduce the noise level.
Pneumatic Applications
Industrial Automation is the largest sector for pneumatics technology, which is widely used for manipulating products in manufacturing, processing, and packaging operations. Pneumatics are also applied in the food and medical processing equipment.
Pneumatics are also used in robot end effectors for picking and placing operations many times a day without deviating from the process flow. In many applications, pneumatics is used more for its ability to provide controlled pressing and squeezing operations than it is for fast and repetitive operations.
And also, pneumatics are used in chemical plants and refineries to actuate large valves. They are also used for lifting and moving workpieces and products.
Following is a list of common pneumatic applications:
- Packing
- Medical
- Factory Automation
- Material Handling
- Food & Beverage
- Medical & chemical refineries
- Robots Gripper
- Pick and Place operations
- Pressing & squeezing
Read Next:
- Instrument Air Design
- Pneumatic Piping Design
- Testing of Pneumatic Systems
- What is a Pneumatic Cylinder?
- Pneumatic Piping and Fittings