Hydraulic systems are mostly used in industries. Every device requires a force to move it. Just by powering it up, it cannot be moved mechanically. It can be oil, air, or electricity. Hydraulic systems use oil for motion.
Many heavy loads in an industry use hydraulic energy for their purpose. Be it any system, maintenance is a must for all. You cannot long run a system without maintenance. In this post, we will see the concept of maintenance of hydraulic systems.
What is a Hydraulic System?
A hydraulic system is a mechanical arrangement that uses specialized hydraulic fluid to move a load. This is done by pressurizing it and then moving it through outputs like actuators and valves.
According to Pascal’s law, when an enclosed fluid is pressurized in a certain calculated area, then it will convert this low input pressure into a very high pressure automatically due to its physical properties. These fluid properties are only available in special types of oils, which are thus used in hydraulic systems. The area where the oil is stored is generally large enough to accommodate a good quantity. So, this system is best used for heavy loads.
You will mostly find that heavy mechanical loads use this system for movement. If you use electrical or pneumatic systems in comparison, then you will require large-rated motors and compressors to achieve the performance. This demerit is eliminated in hydraulic systems because even a small push to the fluid will create a high push output for the load. This automatically reduces the cost of the system.
It is to be noted that each device that uses the oil like actuators or valves, has a return path for recirculating the oil back to the system. In this way, the process continues with the set quantity of oil. It is astonishing to see that a 100 kg force for example can create a 1000 kg force in return. So, hydraulic systems are best suited for heavy loads.
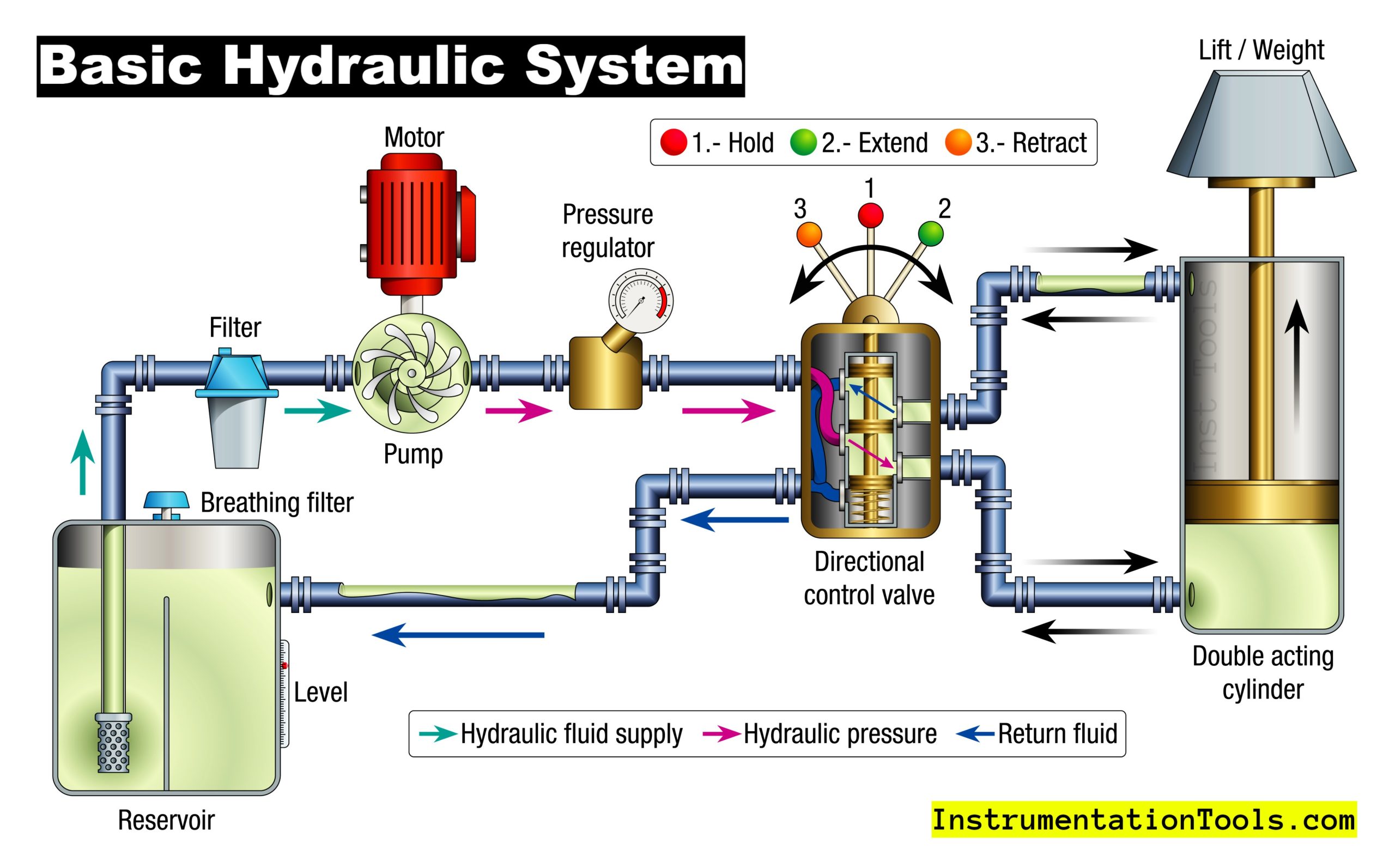
Why is hydraulic system maintenance important?
As the hydraulic system uses oil, one of the very main reasons for failure is oil leakage. Fluid leakage happens more easily than air leakage. Also, oil heats up easily after a prolonged use of time. With the increase in temperature, device failure chances too increase when not seen. The oil, similar to other types of media, must be free of particles, dirt, and any other types of contamination. Uncontaminated oil can damage the pumps or choke the filters inside.
As discussed earlier, cylinders and pistons are present inside the hydraulic system for moving the mechanical parts inside. Suppose a piston is moving in tandem with another piston; if one piston bends or misaligns, then the movement becomes rough and difficult to use. Prolonged operation will damage the whole mechanical arrangement in one day. People working around hydraulic systems must thus take care of themselves due to the risk involved in device failure or overheating, which can cause a blast.
This all brings us to the conclusion that timely maintenance of hydraulic systems is a must. Any lag in it can disrupt the whole operation of the plant. It can be difficult and deadly to imagine the failure of the system in between when it is moving a heavy load. So, maintenance of hydraulic systems is important and there are many operating and maintenance procedures that must be followed for a safe and long operation.
Hydraulic system maintenance checklist
Let us see what we can do to maintain the hydraulic system properly.
- Oil is not passed directly to the basin but through filters. Filters get choked easily after a period of time. So, regularly clean the filters or if required, change them if not washable.
- As the temperature rise is a major concern for failures, we can use oil cooling systems inside and temperature sensors to keep the heat under control. Timely actions must be taken for any alarm generated due to this.
- Pistons and cylinders when misaligned create an abrupt sound of movement. If found, check visually what is the issue and fix it. Do not wait for any loud sound to happen and damage the system.
- Like we change the engine oil of vehicles after a certain time, it is also necessary to empty the whole oil tank and fill it with new oil after a certain usage of time. This will lengthen the life of the machine.
- It is important to see that the lines that are connected to valves and actuators are not choked up or blocking the oil flow path. This can cause issues in the performance of the system.
- Hydraulic pumps are the main nerve of the system. As with any pump, if it is running dry, then it will damage its cavities. Similarly, care must be taken that the hydraulic pump does not run dry and the tank level is usually filled with the required amount of oil.
- Ensure that air does not get inside the system, as air filling can dilute the process and stop the whole system. This must be ensured by regular checking of holes, leakages, or inlets where there are chances of air intake.
- All the electrical wiring for pumps, valves, actuators, sensors, and other instruments must be regularly checked for any short-circuit, open wire or other electrical faults. Because this is the one which powers up the devices.
Read Next:
- What is a Pilot Valve?
- What is a Poppet Valve?
- Solenoid Manual Reset
- Digital Control Valves
- Valve Passing Problem