Conveyors are crucial elements of industrial production, facilitating the reliable and efficient movement of materials between different work areas. This is why taking care of your conveyor system is essential; otherwise, it can lead to costly and disruptive problems.
Common Conveyor Problems
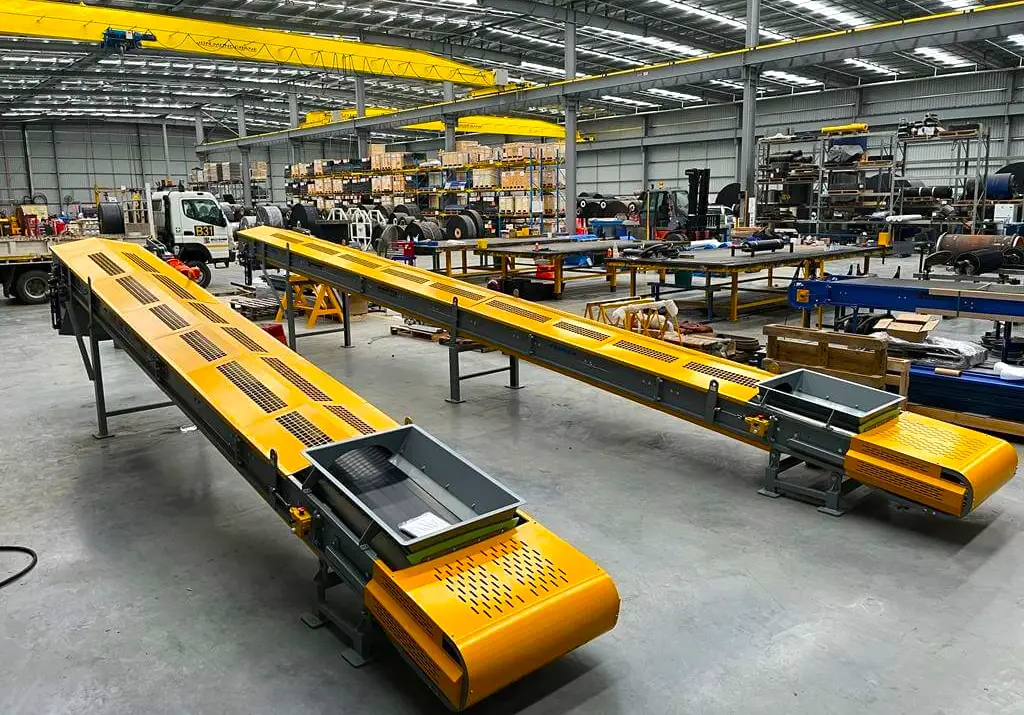
For instance, manufacturers and mining companies in Australia are regularly looking for various reliable parts for their conveyors, like modernized conveyor scrapers Sydney or replacement pulleys. So if you are working with conveyors, you should be aware of the common conveyor problems and how to prevent them.
This thorough guide examines the typical conveyor issues, their detection methods, and the steps to ensure your system operates seamlessly.
1. Poor Belt Tracking
A misaligned or damaged belt is a sign of poor belt tracking. This can cause damage to other components, such as conveyor rollers and sprockets, due to increased strain on the system. It can also lead to reduced efficiency, resulting in higher energy costs to power the conveyor.
Fortunately, poor belt tracking is easy to detect with visual indicators, such as an uneven flow of material or debris build-up on the conveyor belt. Regularly inspecting your conveyor for signs of damage or misalignment is the key to preventing this issue.
Start by adjusting the conveyor belt’s tensioning system and making sure it is properly aligned with the pulley. If needed, you can also re-align the pulley to ensure proper tracking. Finally, make sure all rollers are running smoothly and lubricate them if needed.
2. Excessive Wear on Components
Conveyor components can experience excessive wear due to continuous operation, environmental conditions, and the type of material being transported. This often leads to increased energy consumption and an increased risk of component failure.
To minimize this issue, you should regularly inspect all components and replace any worn or damaged ones. Additionally, you should be sure to lubricate all moving components as needed.
3. Build-Up of Debris & Contaminants
Accumulation of debris and impurities on the conveyor belt can diminish efficiency or trigger a system malfunction if not addressed swiftly. Occasionally, these particulates might be undetectable to the naked eye but still pose issues.
The best way to prevent this buildup is through proper maintenance and regular inspections of the conveyor system. It’s important to keep a close eye on all components and immediately address any wear or signs of deterioration.
Maintaining a tidy and properly serviced workspace surrounding the conveyor can proactively mitigate issues. This entails addressing spills and debris in the vicinity, as well as ensuring that all components are in optimal condition.
4. Belt Slippage
Another common issue with conveyors is that the belt may be slipping on the pulleys. Belt slippage can occur for various reasons, including misaligned or worn-out pulleys, improper tensioning, and incorrect weight distribution across the belt’s surface.
To avert potential issues, operators must routinely inspect components for wear and replace or repair them accordingly. Additionally, maintaining appropriate belt tension and even weight distribution is crucial. Adequate lubrication of moving parts also minimizes slippage.
Slippage may also be caused by incorrect operation or maintenance of the conveyor system. This can include failing to observe safety precautions, such as ensuring the area around the conveyor is clear and that all guards are in place. It is also important to regularly inspect the belt for fraying or cracking, as this could lead to slippage. Ensuring that personnel are properly trained on the conveyor system operation can also help reduce the risk.
5. Seized Rollers
Seized rollers are a common problem encountered in conveyor systems. This occurs when a roller becomes stuck and cannot rotate properly, resulting in decreased efficiency of the conveyor system. Generally, this is caused by dirt or some other foreign material preventing necessary rotation movement from occurring.
The best way to prevent seized rollers is to keep all moving parts clean and lubricated at all times. Regular inspection and maintenance of the conveyor system is key, as is ensuring that any foreign materials are removed immediately from the area. Moreover, if the rollers are constructed from steel, applying an anti-corrosive coating is crucial for ensuring their durability.
In severe cases where seized rollers occur frequently, replacing them with larger diameter or stainless steel rollers may be necessary. Doing so will prevent the problem from recurring in the future, ensuring a smooth working system and maximum efficiency.
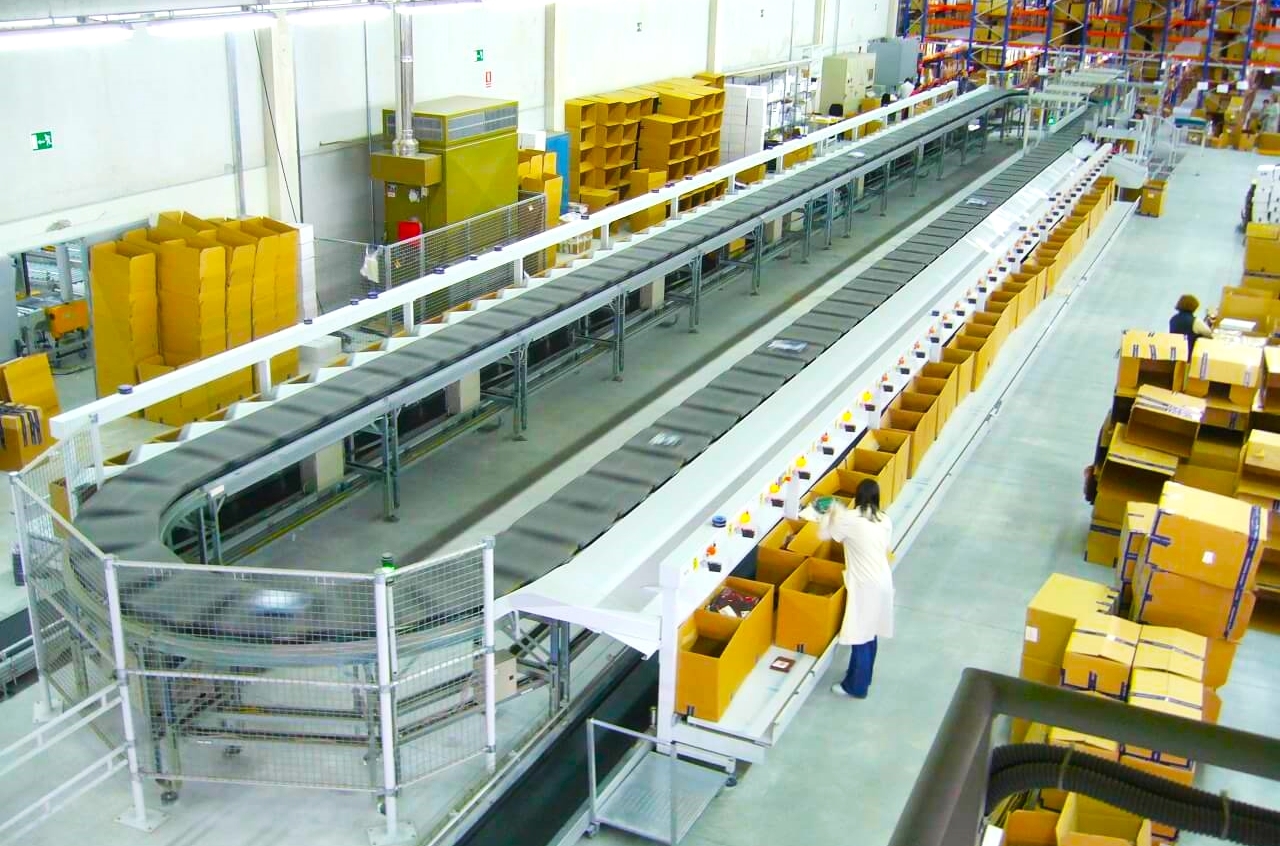
6. Improperly Installed or Worn Out Belting
Worn-out belting is another common conveyor problem that can cause disruption in production. If the belt is improperly installed or inadequately tensioned, it will suffer damage over time due to excessive wear and tear. In addition, belts that are too tight may lead to component breakage and premature failure of the system as a whole.
Preventing this issue requires regular inspections of the belt to ensure it is properly tensioned and installed. You should also replace worn-out belts with new ones as soon as possible. Doing this regularly will help keep your conveyor system running smoothly and efficiently for a long time.
7. Unstable or Incorrect Speed
Incorrect speed can result from belt speed, pulley speed, or motor-speed mismatches. Issues can arise when the conveyor starts up too quickly or stops abruptly, leading to jerky motion, which can increase stress on the belt and cause damage over time.
It’s important to ensure that all components of the conveyor system are properly matched and calibrated in order to prevent this type of problem.
Conclusion
Understanding these common conveyor issues and how to prevent them can help you maintain a safe and efficient conveyor system. Regular inspections, maintenance, and proper installation are essential to avoid costly repairs or unplanned downtime. This will ultimately save money in the long run by ensuring that your conveyor system functions properly and produces quality results. Investing in preventive measures now can save time and money down the road.
When it comes to conveyor systems, there is no one-size-fits-all solution. However, with careful consideration of your specific needs, you can find the best solution for your business.