A bagging machine, also known as a bagger, is used to automate the process of filling bags with specific quantities of products such as Urea, Organic fertilizers, grains, powders, or other bulk materials, etc.
Bagging machine is commonly used in industries like fertilizers, agriculture, food processing, chemicals Etc. Urea Bagging Machine is used to fill Urea in a required bag with fast speed and accuracy.
Bagging Machine all bagging function area controller and guided by Bagging Machine Controller. Before starting bagging this controller checks all required plant Inputs and if found ok then the bagging process will be started.
Working Principle of Urea Bagging Machine
A Urea Bagging Machine works on the principle of Gravity-Feeding. In Gravity fed method Urea is stored in a hopper at an elevated position.
Due to gravity, the urea flows downward from the hopper to a bagging machine and we did not need any other effort to navigate Urea in the bagging machine. This is a very economical and efficient way to bag Urea.
Load Cell assembly is provided in these hoppers to check the weight and level of stored Urea in these hoppers.
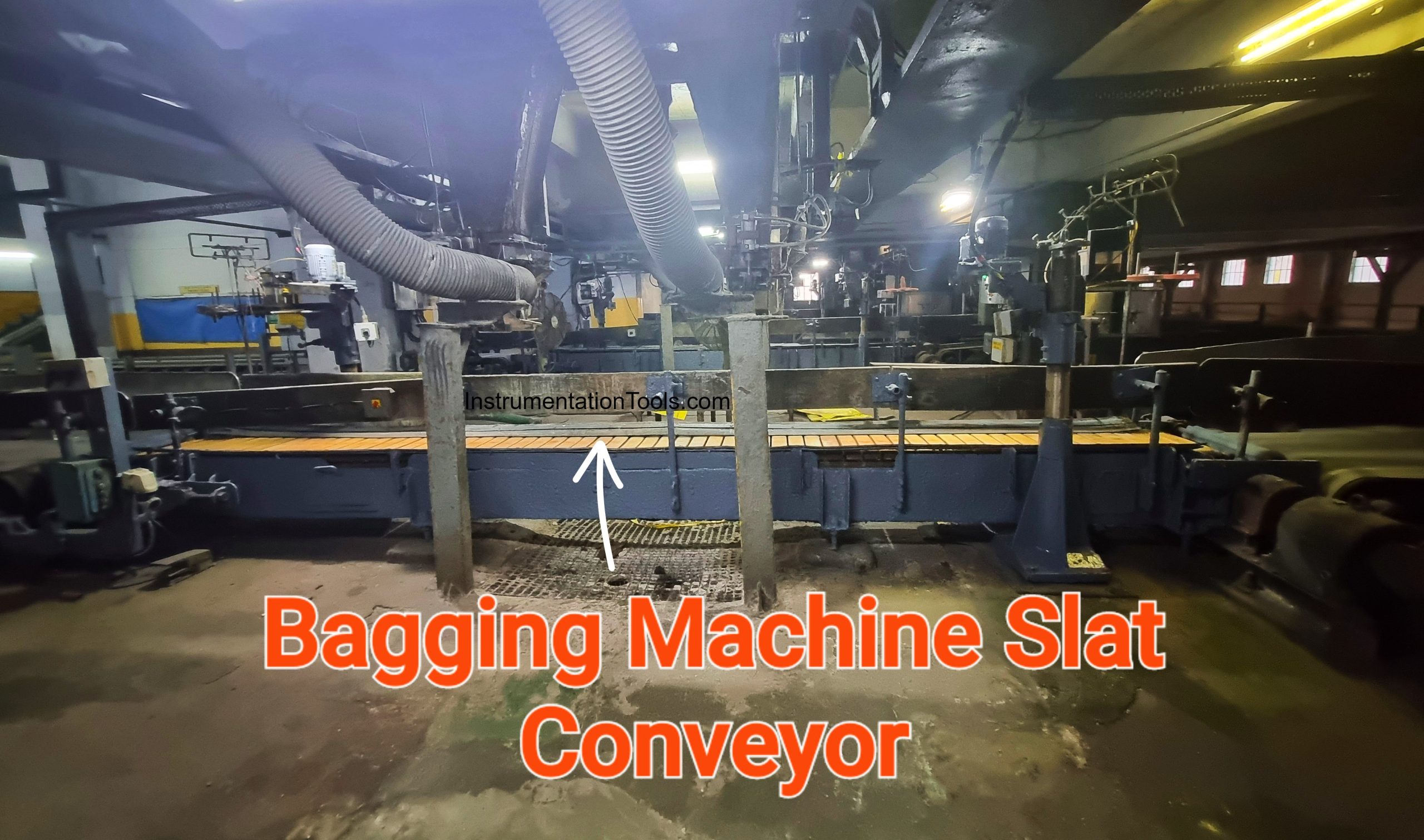
Advantages of using Gravity Feeding in Bagging
Simplified Mechanical System: Gravity-fed systems needed minimal mechanical components to form structure. Also, their operation and maintenance are easy in comparison to other systems.
Energy Efficient System: In this system, material moves from one place to another by gravity therefore we do not need an additional Electrical system like a Motor, Bulk conveyor system, etc.
Cost Effectiveness: Due to the simplified mechanical structure this system is very cost efficient.
Bagging Machine Components
The Urea Bagging Machine’s Important component name and brief description are explained as below.
Hopper – Hopper is a conical-shaped mechanical structure in which Urea is being stored for bagging.
Hopper Load cell – 4-Load cell assembly is provided on the bottom side of the hopper to measure the weight of Urea inside the Hopper.
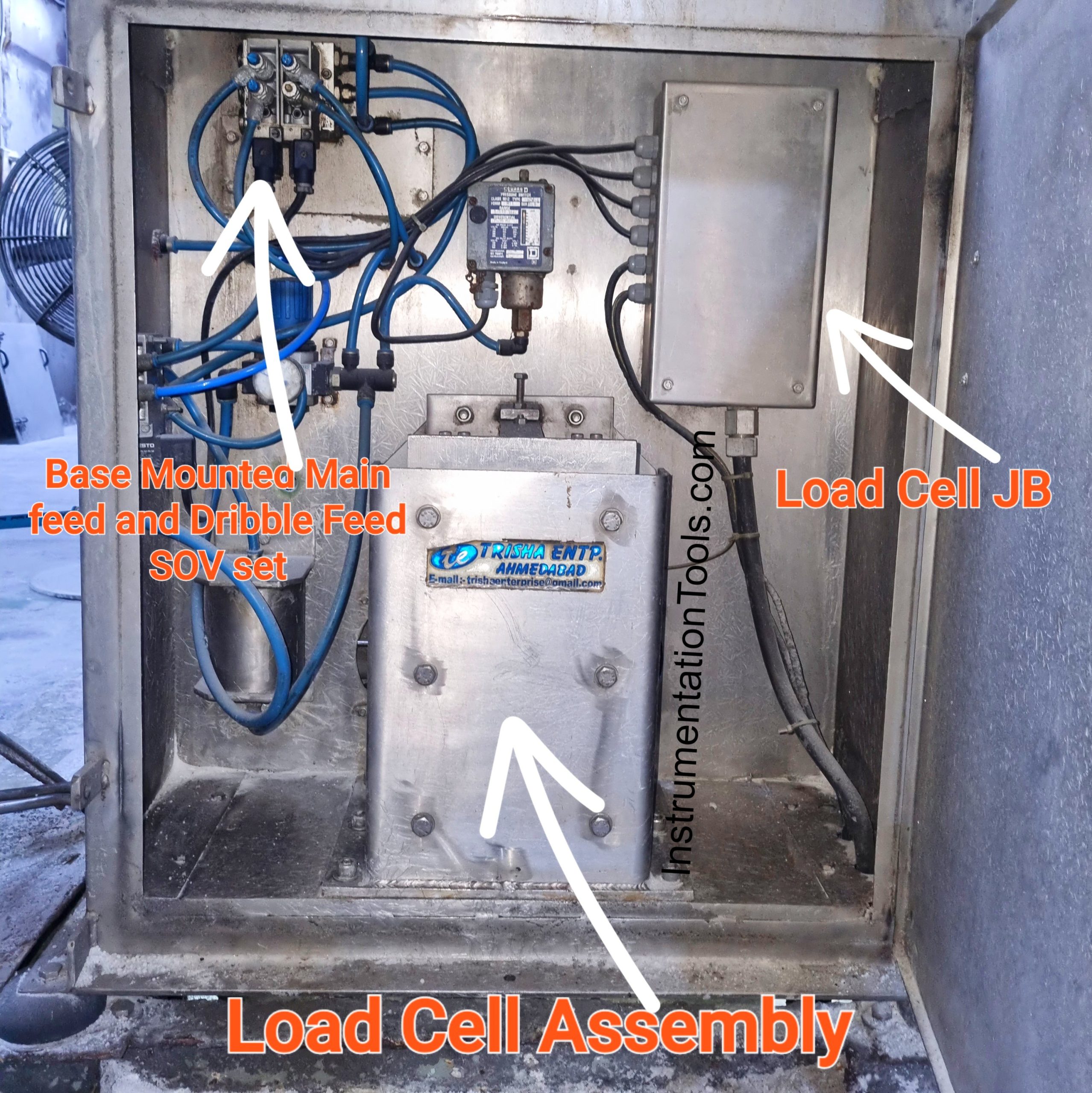
Mechanical Discharge Hopper – This Mechanical assembly is fitted just downward of the Main Hopper and at the end of this assembly a mechanical sliding gate is provided to control the flow of Urea, Mainly used to isolate the hopper during cleaning and dechocking of the Bagging Machine.
Bagging Machine SS/MS Body – Below Mechanical Discharge hopper Bagging Machine Main Body is connected cum fitted with a Mechanical discharge hopper. Inside the bagging machine body Feed gate assembly and Pandoor assembly is provided. Bagging Machine fitting is done with an anti-vibration pad to avoid soak vibration of the structure during the bagging process. Also at the upper side of the bagging machine body, a 3-inch pipe assembly (WDS System) is provided to suck the Urea dust & NH3-Ammonia present in the bagging material.
Urea Feed Gate assembly – This assembly is connected inside the Bagging machine body just below the Mechanical sliding gate. Feed gate assembly consists of two feeding gates i.e. Main Feed Gate (Coarse Feeding) and Dribble Feed Gate (Fine Feeding). Both these gates are controlled by a pneumatic power cylinder.
The main feed gate fulfills the filling of 70 -76  % of our required weight and the rest is filled by the Dribble feed gate. For example, if our target filling weight is 50 Kg then the Main Feed gate quantity will be between 35 to 38 Kg. and the rest Quantity will be filled by the Dribble feed Gate according to the main feed quantity setting. We cannot increase the range of the Main feed quantity by more than 76 % due to weight variation problems.
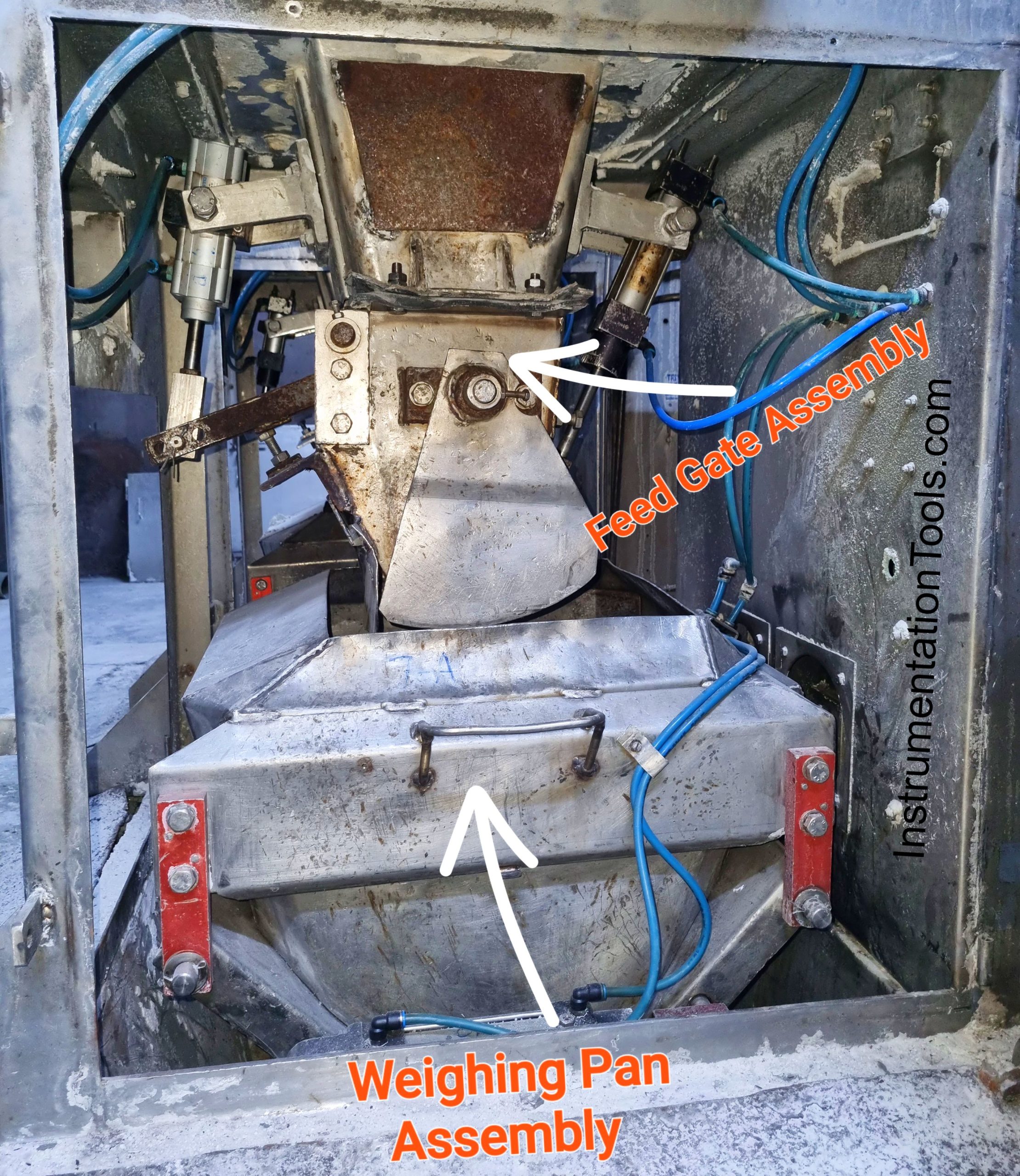
Urea Weighing Pan Assembly – This assembly is mounted just bottom of the Feed gate assembly consisting of two gates controlled by a Pneumatic Power Cylinder (2 Nos). This assembly also consists of a Load Cell assembly.
Discharge Chute – This assembly is fitted below the Pandoor assembly. This assembly is the link between the Pandoor and Bagging Machine Spout assembly. Required and measured Urea passed through this assembly and then got to Spout assembly and after that Material bagged into Urea Bag. During the weight variation problem bagging machine dechocking is done on this assembly i.e. Discharge Chute.
Urea Spout (Bag Holder ) assembly – This assembly is mounted on the bottom of the Discharge chute. This assembly consists of a Sensor assembly, and Two Gates i.e. Front spout gate, a rear spout gate, and a fixed jaw assembly. Both the Front spout gate and rear spout gate are controlled by a Pneumatic Power cylinder.
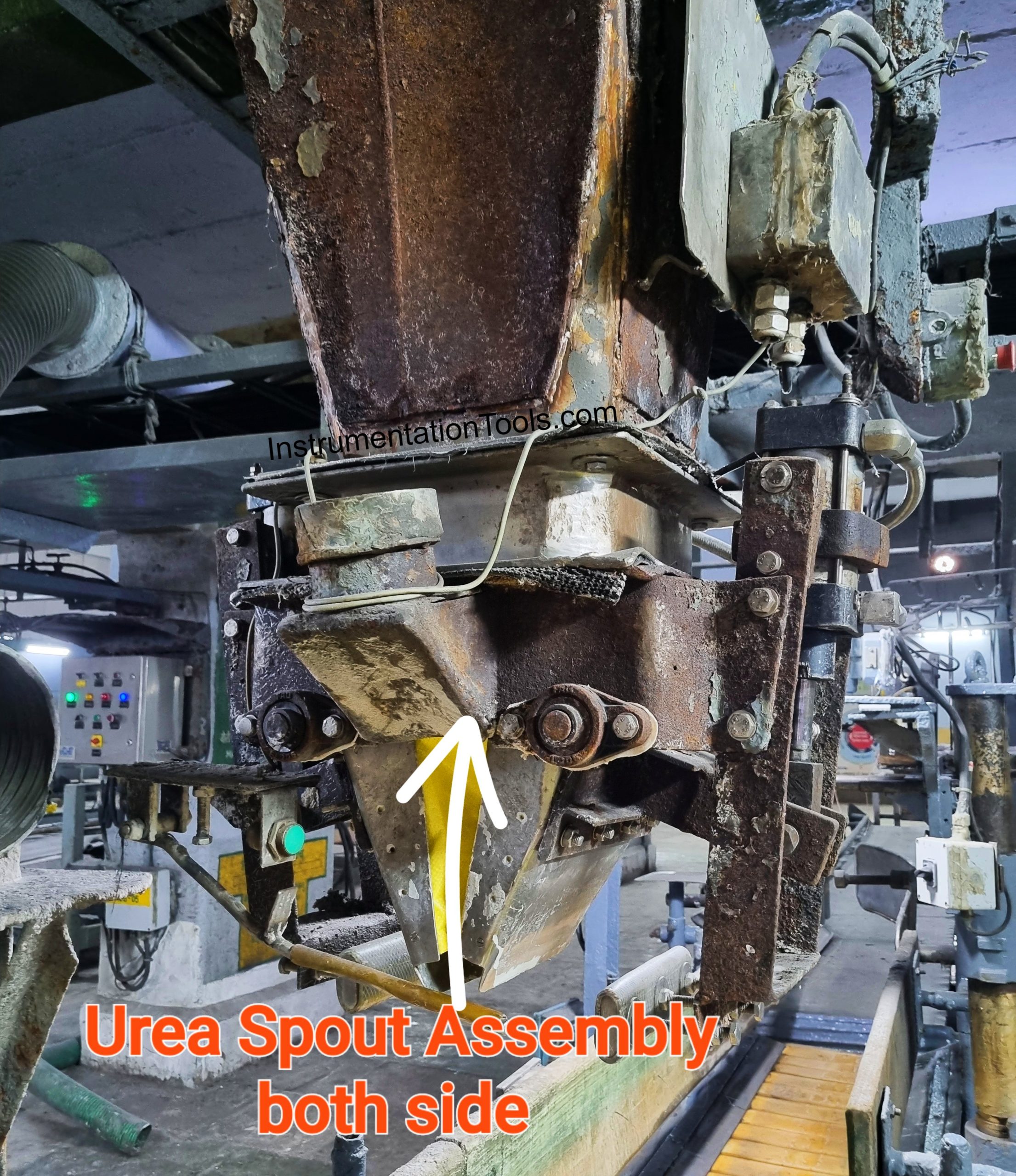
The operator places the Urea bag outer side of this bag holder assembly (During the bag placing process Sensor lever assembly is moved and sensor input is received by the Controller and material discharge command is initiated by the controller) and Urea is filled in Urea Bag and then filled Urea bag move to Stitch machine by slate conveyor and after that Urea bag placed on Wagon loader conveyor or Truck loader conveyor.
Bagging Machine Controller – The Bagging Machine Controller has the most important role because it controls, monitors, and regulates the entire bagging machine bagging process.
Slat Conveyor – It is a conveyor belt assembly placed just below the bagging machine on which the Urea Bag travels after Bag Filling. Also, this machine navigates Filled Urea bags to the Sewing machine and Belt conveyor System.
Bagging Machine Process
The urea is directed into the bagging machine via the Mechanical discharge Hopper, Feed gate assembly, Pandoor, and Discharge Chute.
In the bagging machine, the urea is accurately weighed and dispensed into Urea bags. The bags are then sealed to prevent spillage by using a Stitching Machine.
After Stitching (Sewing) bags, the Bags travel to their final loading point i.e. Wagon loading Point or Truck Loading point via Conveyor Belt.
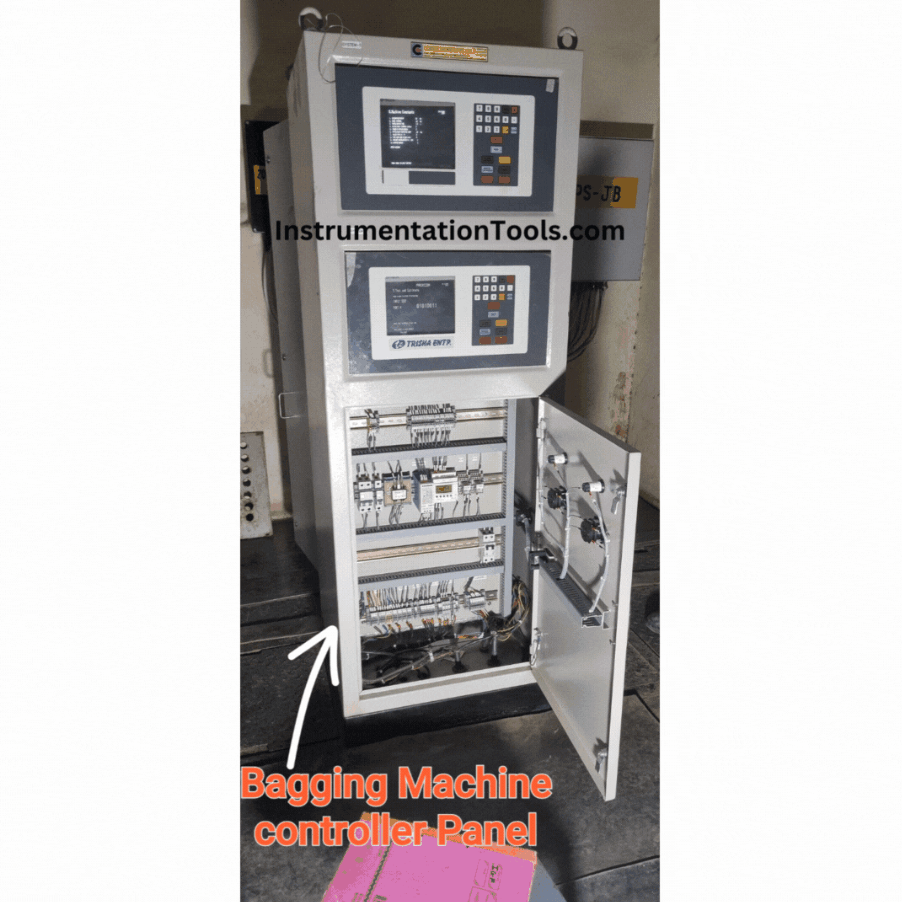
Advantages of Urea Bagging Machine
- Efficiency – The urea bagging machine is highly efficient for bagging of Urea and other materials with proper sealing by sewing. Bagging machine bagging speed and Sewing speed is too fast.
- Accuracy – The Bagging Machine’s speed is fast but it does not affect the accuracy of the bagging machine. The bagging machine bagged Urea with high speed and accuracy together.
- Automation of Process – By using a bagging machine we can increase the speed and accuracy of bagging, also we can minimize the labor or workers, and save a lot of time.
- Consistency – The bagging machine is a very consistent machine with the property of uniform weight bag filling capacity.
- Versatility – The Bagging Machine is suitable for various materials and bag types.
Conclusion
A bagging machine is essential for efficient Urea Bag packaging with High speed and high accuracy bagging ensuring that products reach consumers in a convenient and well-sealed form. Also Operability, maintainability of the bagging machine are simple. The bagging machine is cost efficient machine.